A Beam Has A Maximum Strength Of 3000 Psi
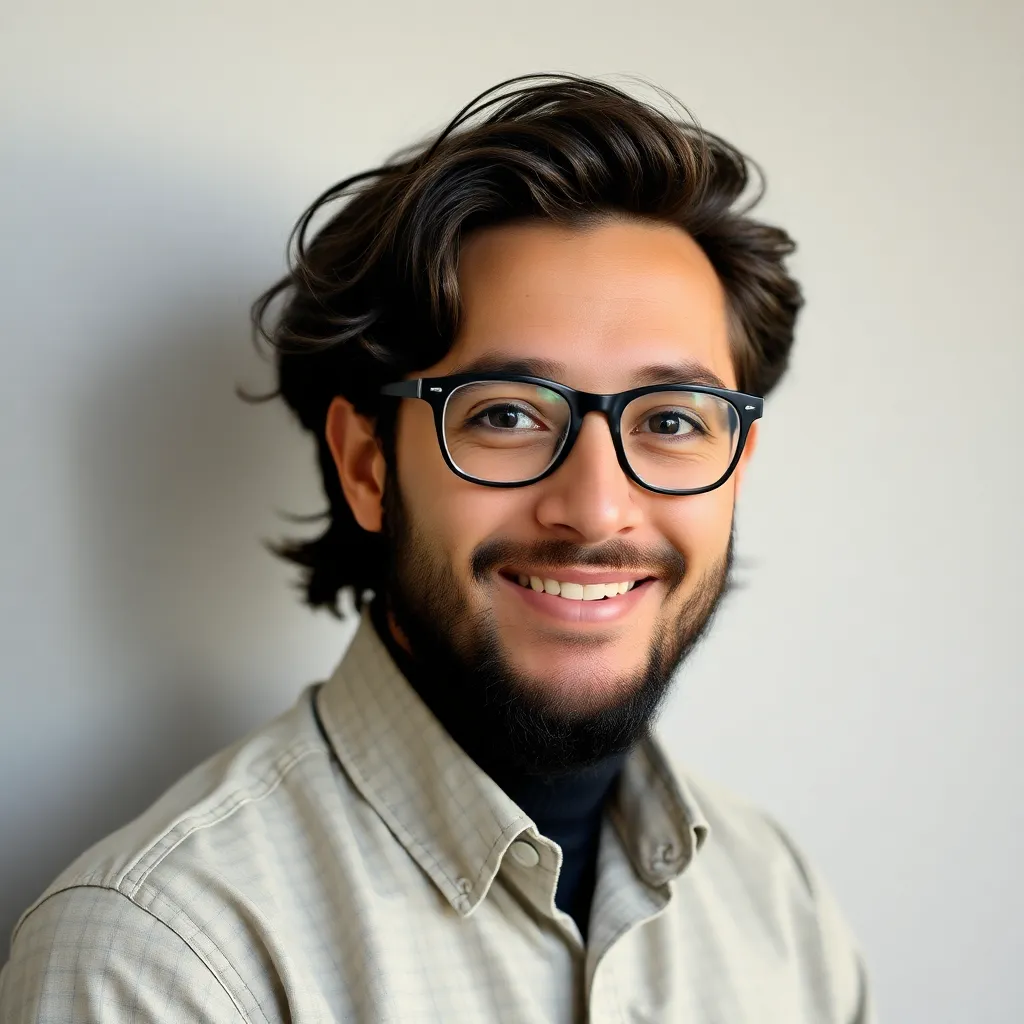
Breaking News Today
Apr 23, 2025 · 6 min read

Table of Contents
A Beam's Maximum Strength: Understanding 3000 psi and its Implications
Understanding the maximum strength of a structural beam is crucial for engineers and architects involved in designing safe and reliable structures. A beam with a maximum strength of 3000 psi (pounds per square inch) presents a specific set of design considerations and limitations. This article will delve into the meaning of this strength rating, its implications for design, factors influencing beam strength, common beam materials, and best practices for ensuring structural integrity.
Deciphering 3000 psi: What Does it Mean?
The 3000 psi figure represents the maximum compressive or tensile stress a beam material can withstand before yielding or fracturing. This is often referred to as the yield strength or ultimate tensile strength, depending on the specific test method used. It's a critical parameter in determining the load-bearing capacity of the beam. In simpler terms, it's the point where the material begins to deform permanently (yielding) or breaks (fracturing) under stress. Exceeding this limit can lead to structural failure, potentially resulting in catastrophic consequences.
Important Note: The 3000 psi value is a material property. The actual strength of a specific beam depends not only on the material's properties but also its dimensions (length, width, height), shape, and the way the load is applied. A longer, thinner beam made from the same material will have a lower load-carrying capacity than a shorter, thicker one, even if both have the same material strength of 3000 psi.
Stress vs. Strain: A Fundamental Concept
Before we proceed, it's essential to understand the difference between stress and strain.
- Stress: Stress is the force applied to a material per unit area (measured in psi or MPa). Think of it as the intensity of the force acting on the material.
- Strain: Strain is the deformation of a material in response to stress. It's the change in length or shape divided by the original length or shape.
The relationship between stress and strain is described by a stress-strain curve, which is unique to each material. The 3000 psi value usually corresponds to a point on this curve, indicating the stress level at which permanent deformation begins (yielding) or failure occurs (ultimate tensile strength).
Factors Affecting Beam Strength
Several factors beyond the inherent material strength (3000 psi in this case) significantly influence a beam's overall load-bearing capacity.
1. Material Properties:
Beyond the yield strength, other material properties like elastic modulus (Young's modulus), Poisson's ratio, and ductility play a crucial role. The elastic modulus indicates the material's stiffness, determining how much it deforms under a given load. Poisson's ratio describes the material's tendency to deform in one direction when stressed in another. Ductility measures a material's ability to deform plastically before fracturing.
2. Beam Geometry:
The shape and dimensions of the beam are paramount. A rectangular beam, I-beam, or T-beam will each behave differently under load. The cross-sectional area, moment of inertia, and section modulus are crucial geometric properties that determine the beam's resistance to bending and shear stresses. Larger cross-sections generally translate to higher strength.
3. Loading Conditions:
The type, magnitude, and location of the load significantly affect the beam's performance. A concentrated load at the center of a beam will produce higher stresses than a uniformly distributed load over the entire length. The support conditions (simply supported, fixed, cantilever) also influence the stress distribution within the beam.
4. Manufacturing Defects and Damage:
Imperfections during manufacturing, such as internal voids or cracks, can significantly weaken the beam and reduce its load-carrying capacity. Any existing damage, such as corrosion or impact damage, will further compromise the beam's integrity.
Common Beam Materials with 3000 psi Strength (or thereabouts)
While achieving precisely 3000 psi in a specific beam might require custom material blends or specific treatment processes, several common materials fall within a similar strength range. It's important to consult material datasheets for exact values, as these can vary depending on the specific alloy or treatment.
- Certain Grades of Steel: Certain lower-strength steel grades can exhibit yield strengths in the vicinity of 3000 psi. These are often used in less demanding applications.
- Some Aluminum Alloys: Specific aluminum alloys can achieve comparable tensile strengths, although their lightweight nature might necessitate larger cross-sections to achieve equivalent load-bearing capacity to steel.
- Concrete (with Reinforcement): While concrete itself has a lower compressive strength, reinforced concrete beams, incorporating steel rebar for tensile strength, can achieve effective strengths comparable to 3000 psi in certain configurations.
- Wood (depending on species and treatment): Certain types of wood, particularly when treated for increased durability and strength, can exhibit comparable tensile strength in specific orientations of the grain.
Design Considerations for Beams with 3000 psi Strength
Designing structures using beams with a 3000 psi strength requires careful attention to detail and adherence to relevant engineering codes and standards.
1. Load Calculations:
Accurately estimating all loads (dead loads, live loads, environmental loads) is critical. Using appropriate safety factors is essential to account for uncertainties and potential variations in material properties and loading conditions.
2. Stress Analysis:
A thorough stress analysis must be performed to determine the stress distribution within the beam under different loading scenarios. This often involves using finite element analysis (FEA) software for complex geometries and loading conditions.
3. Deflection Analysis:
Excessive deflection (bending) can compromise the structural integrity and serviceability of a beam. Deflection limits are specified in design codes and must be checked during the design process.
4. Buckling Considerations:
Slender beams are susceptible to buckling under compressive loads. Buckling checks are essential, particularly for columns and beams subjected to significant axial compression.
5. Fatigue Analysis:
If the beam is subjected to cyclic loading (repeated stress reversals), a fatigue analysis must be performed to ensure that the beam can withstand the expected number of load cycles without failure.
6. Material Selection:
The choice of material should be based on its strength, stiffness, durability, cost, and availability. Consider the environment, anticipated loads, and other relevant factors when selecting a material.
7. Detailing and Construction:
Proper detailing of connections and supports is essential to ensure the beam's effective load transfer. Careful construction practices are vital to avoid damage or defects that can compromise the beam's strength.
Safety and Best Practices
Ensuring structural safety is paramount. Here are some key best practices:
- Adhere to building codes and standards: Always follow relevant building codes and standards in your region. These codes incorporate safety factors and best practices to ensure structural integrity.
- Use qualified engineers: Employ experienced structural engineers to design and oversee the construction of any structure where beam strength is a critical factor.
- Regular inspection and maintenance: Regular inspections can help detect potential problems early on. Timely maintenance can prevent minor issues from escalating into significant safety hazards.
- Proper load management: Avoid overloading beams beyond their design capacity. Keep track of loads and ensure that they remain within the allowable limits.
- Consider environmental factors: Account for environmental factors such as temperature variations, humidity, and exposure to corrosive elements, which can affect the long-term strength of the beam.
Conclusion
A beam with a maximum strength of 3000 psi represents a specific material characteristic with implications for structural design. Understanding the interplay of material properties, beam geometry, loading conditions, and construction practices is crucial for ensuring the safety and reliability of structures using beams of this strength. Always prioritize adherence to engineering standards, diligent design practices, and robust construction to mitigate risks and ensure structural integrity. Remember, the 3000 psi value is just one component in a complex design process; achieving structural safety requires a comprehensive and holistic approach.
Latest Posts
Latest Posts
-
Best Suited For Areas Subject To Friction
Apr 23, 2025
-
The Great Gatsby Book Quotes And Page Numbers
Apr 23, 2025
-
Antibodies Received From Maternal Fetal Transmission Are An Example Of
Apr 23, 2025
-
6 Hour Defensive Driving Course Test Answers
Apr 23, 2025
-
Post Tax Dollar Contributions Are Found In
Apr 23, 2025
Related Post
Thank you for visiting our website which covers about A Beam Has A Maximum Strength Of 3000 Psi . We hope the information provided has been useful to you. Feel free to contact us if you have any questions or need further assistance. See you next time and don't miss to bookmark.