A P-chart Would Be Used To Monitor:
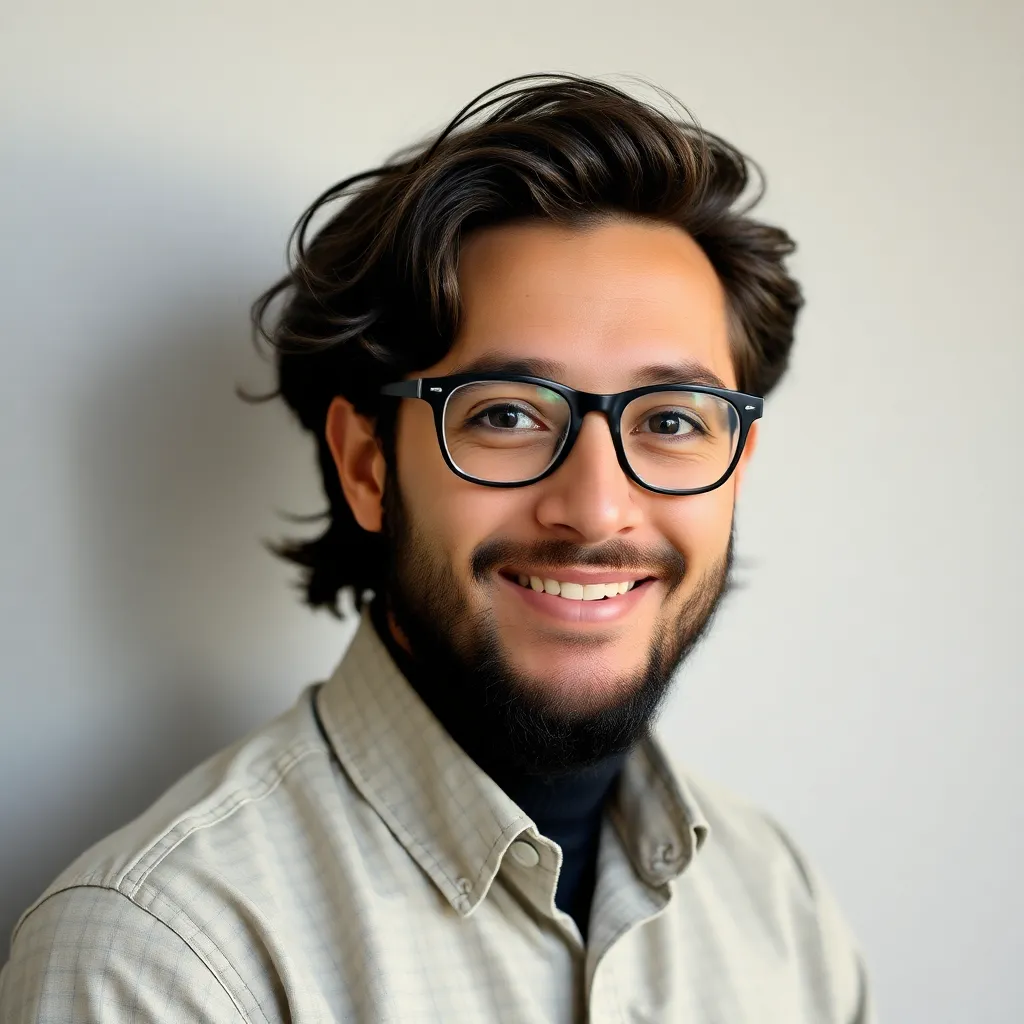
Breaking News Today
May 10, 2025 · 7 min read

Table of Contents
A P-Chart Would Be Used To Monitor: Process Stability and Proportion Nonconforming
A P-chart, or a p-chart for attributes, is a powerful statistical process control (SPC) tool used to monitor the proportion of nonconforming units in a sample. Unlike charts that track continuous data, the P-chart focuses on attributes – characteristics that are either present or absent, conforming or nonconforming. This makes it invaluable for a wide range of applications across various industries. Understanding when and how to use a P-chart is crucial for maintaining consistent product quality and identifying potential process improvements.
What Does a P-Chart Monitor?
At its core, a P-chart monitors the proportion of defective items in a sample. This "proportion" is expressed as a percentage or decimal. The chart tracks these proportions over time, allowing for the visualization of process stability and the detection of significant shifts or trends. This makes it particularly useful for:
- Identifying Out-of-Control Processes: A P-chart quickly highlights when the proportion of nonconforming units exceeds acceptable limits, indicating potential problems in the production process.
- Monitoring Process Capability: By analyzing the data presented on the P-chart, you can assess whether the process is capable of meeting predefined quality standards.
- Predicting Future Performance: Once a process is deemed stable, the P-chart can provide insights into its future performance, enabling proactive adjustments to prevent future quality issues.
- Improving Process Efficiency: By identifying and addressing the root causes of variations, businesses can streamline their operations and reduce waste.
Let's delve deeper into specific scenarios where a P-chart proves invaluable.
Key Applications of P-Charts: Where They Shine
The versatility of P-charts extends across diverse industries and processes. Here are some key areas where they are most effectively utilized:
1. Manufacturing and Production:
- Defect Rates: Monitoring the percentage of defective products in a production line. For instance, a manufacturer of electronic components might use a P-chart to track the proportion of faulty chips in each batch. This helps to identify if the soldering process, component quality, or other factors are contributing to higher defect rates.
- Quality Control Inspections: Analyzing the results of quality inspections where items are classified as either conforming or nonconforming. This could include checking for scratches, dents, or other imperfections in finished goods.
- Yield Analysis: Tracking the percentage of successful units produced compared to the total number of units processed. A consistently low yield indicates process inefficiencies that need attention.
2. Healthcare:
- Infection Rates: Hospitals utilize P-charts to monitor infection rates among patients. Tracking the proportion of patients contracting specific infections helps identify potential sources of contamination and implement preventative measures.
- Medication Errors: Pharmacies and hospitals can use P-charts to monitor the rate of medication errors. This enables them to identify areas where improvements in procedures or training are needed.
- Patient Satisfaction: While not directly a defect, patient satisfaction scores can be analyzed using a P-chart to track the proportion of patients reporting high satisfaction levels.
3. Service Industries:
- Customer Complaint Rates: Businesses can track the percentage of customers lodging complaints to pinpoint areas needing improvement in their service delivery.
- Order Fulfillment Accuracy: Analyzing the proportion of orders fulfilled accurately can reveal issues in the order processing and fulfillment systems.
- On-Time Delivery Rates: Monitoring the proportion of orders delivered on time helps identify logistical bottlenecks or scheduling inefficiencies.
4. Software Development:
- Bug Rates: Software development teams utilize P-charts to monitor the proportion of bugs identified in each software release. This enables them to assess the effectiveness of their testing and quality assurance processes.
- Defect Density: Tracking the number of defects per lines of code can highlight areas of the codebase prone to errors.
Constructing and Interpreting a P-Chart: A Step-by-Step Guide
Creating and interpreting a P-chart involves several key steps:
-
Data Collection: Gather data on the number of nonconforming units and the sample size for each subgroup. Ensure consistent sample sizes for accurate analysis. Larger sample sizes generally lead to more precise estimations.
-
Calculate the Proportion of Nonconforming Units (p): For each subgroup, divide the number of nonconforming units by the sample size.
-
Calculate the Average Proportion of Nonconforming Units (p̄): This is the average of the proportions calculated in step 2 across all subgroups. This provides a central tendency of your data.
-
Calculate the Standard Deviation of the Proportion (σp): The formula is: √[p̄(1-p̄)/n], where 'n' is the sample size.
-
Determine the Control Limits: The upper control limit (UCL) and lower control limit (LCL) are calculated as follows:
- UCL = p̄ + 3σp
- LCL = p̄ - 3σp
Note: If the LCL falls below zero, it's typically set to zero. This is because a proportion cannot be negative.
-
Plot the Data: Plot the proportion of nonconforming units for each subgroup on the chart, along with the center line (p̄) and the control limits (UCL and LCL).
-
Interpret the Chart: Points falling outside the control limits indicate potential process instability. Patterns such as trends or runs also suggest issues that require investigation.
Common Causes of Out-of-Control Signals
When a point falls outside the control limits or a pattern emerges, it's critical to investigate the root cause. Some common reasons include:
- Changes in Raw Materials: Variations in the quality of raw materials can lead to an increase in defective products.
- Equipment Malfunction: Faulty equipment can produce nonconforming units consistently.
- Process Adjustments: Changes in the production process, even seemingly minor ones, can have significant effects.
- Operator Error: Inconsistent or incorrect operator procedures can contribute to higher defect rates.
- Environmental Factors: Temperature fluctuations, humidity, or other environmental changes can impact the process.
Advantages and Limitations of P-Charts
Like any statistical tool, P-charts have advantages and limitations:
Advantages:
- Simplicity: Relatively easy to understand and implement.
- Visual Representation: Provides a clear visual representation of process stability over time.
- Early Detection of Problems: Allows for early detection of problems before they significantly impact quality.
- Wide Applicability: Applicable to a broad range of processes and industries.
Limitations:
- Requires Sufficient Data: A sufficient number of subgroups is necessary for accurate analysis.
- Assumes Constant Sample Size: Ideally, the sample size should remain constant across all subgroups. Variations can affect the accuracy of the control limits.
- Doesn't Identify Root Causes: While P-charts signal problems, they don't pinpoint the specific root causes. Further investigation is required.
- Sensitivity to Small Sample Sizes: With small sample sizes, the control limits can be wide, potentially masking subtle shifts in the process.
P-Chart vs. np-Chart: Understanding the Difference
The np-chart is closely related to the P-chart, but there's a crucial distinction:
-
P-chart: Tracks the proportion of nonconforming units in a sample. The sample size can vary between subgroups.
-
np-chart: Tracks the number of nonconforming units in a sample. The sample size must remain constant between subgroups.
Choosing between a P-chart and an np-chart depends on the consistency of your sample size. If the sample size varies, a P-chart is more appropriate. If the sample size is constant, an np-chart offers a simpler calculation.
Conclusion: Leveraging P-Charts for Continuous Improvement
The P-chart is a valuable tool for monitoring and improving process quality. By visually representing the proportion of nonconforming units over time, it allows for early detection of problems, enabling proactive interventions and preventing costly defects. Understanding its applications, construction, and interpretation is crucial for businesses striving for continuous improvement and delivering high-quality products or services. Remember to carefully consider the data, sample size, and potential limitations before implementing a P-chart to ensure accurate and meaningful results. The consistent application of this tool, coupled with root cause analysis, can significantly contribute to enhanced process efficiency and customer satisfaction.
Latest Posts
Latest Posts
-
Ar Answers For Harry Potter And The Goblet Of Fire
May 10, 2025
-
What Are Personnel Accountability Systems Designed To Do
May 10, 2025
-
Before You Have Work Done On Your Vehicle
May 10, 2025
-
Vocab Workshop Level C Unit 12 Answers
May 10, 2025
-
What Is The Percent Oxygen For A Fire To Burn
May 10, 2025
Related Post
Thank you for visiting our website which covers about A P-chart Would Be Used To Monitor: . We hope the information provided has been useful to you. Feel free to contact us if you have any questions or need further assistance. See you next time and don't miss to bookmark.