All Refrigeration Compressors Are Designed To Pump
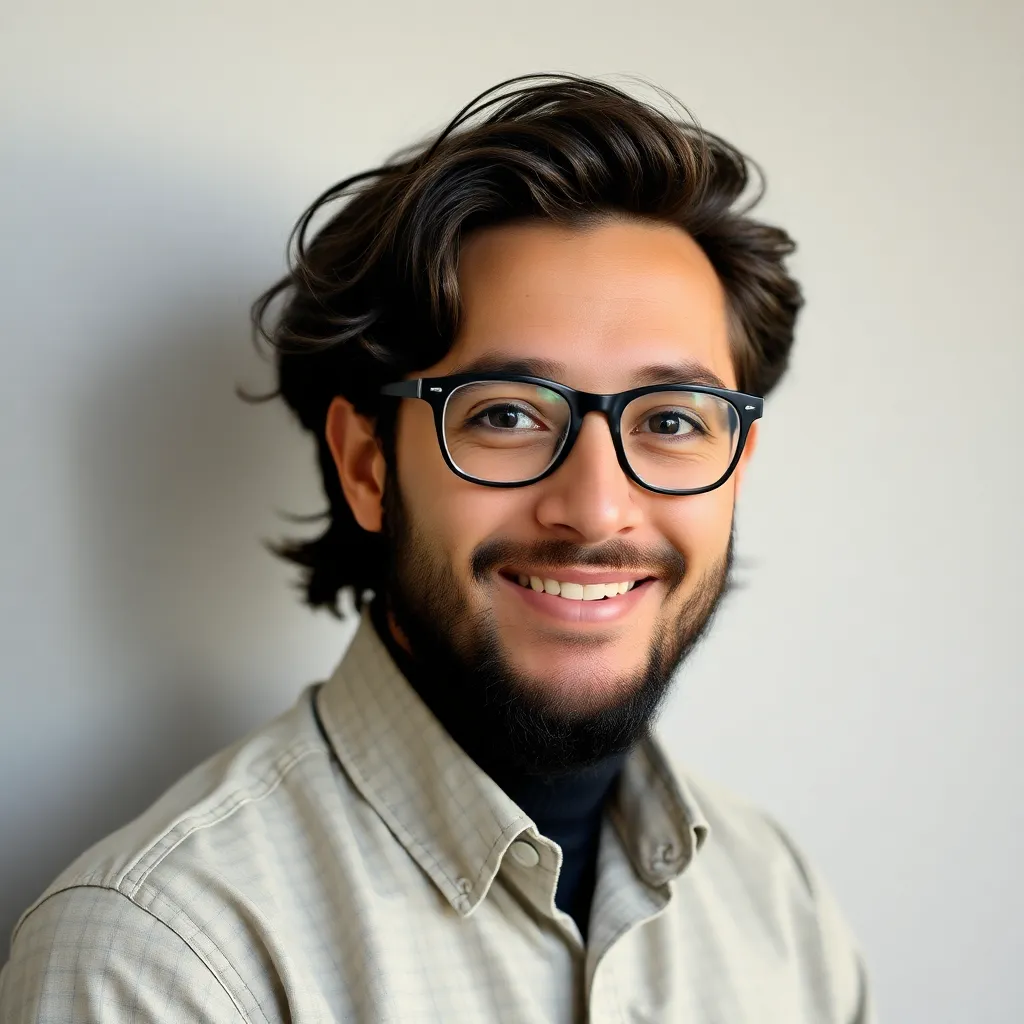
Breaking News Today
May 09, 2025 · 7 min read
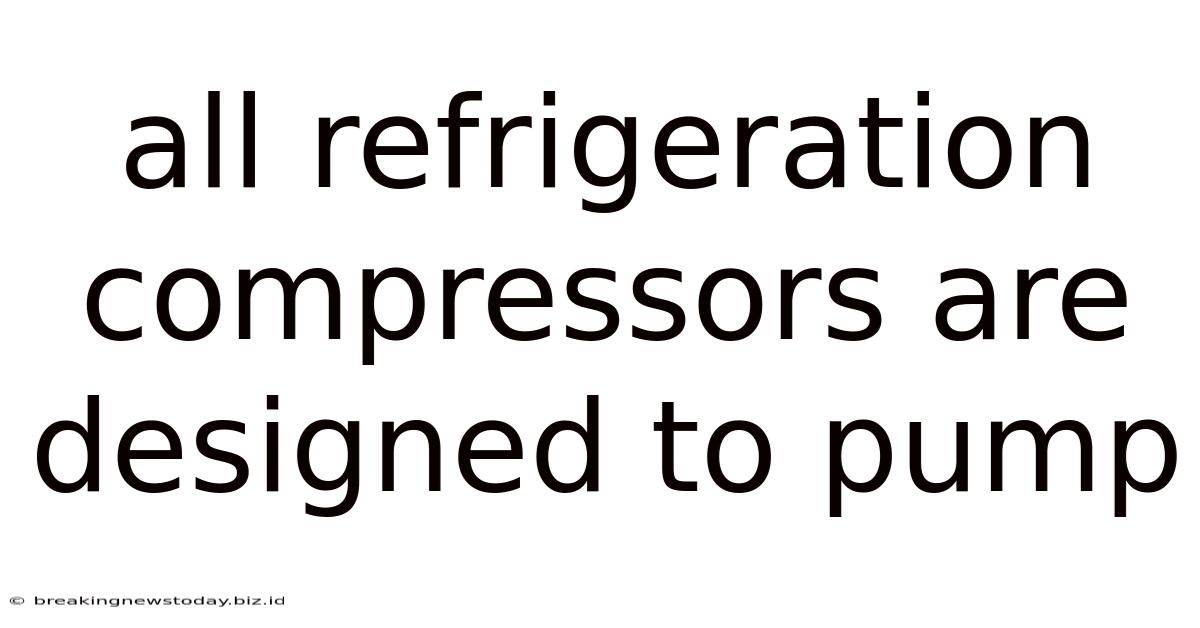
Table of Contents
All Refrigeration Compressors Are Designed to Pump: A Deep Dive into Compression Technology
Refrigeration, a cornerstone of modern life, relies heavily on the efficient and reliable operation of compressors. Understanding the fundamental role of these devices is crucial to appreciating the entire refrigeration cycle. This article will explore the intricacies of refrigeration compressors, focusing on their core function: pumping. We'll delve into the various types, operating principles, and key performance indicators, all while emphasizing their crucial role in the overall refrigeration process.
The Heart of the System: Understanding the Compressor's Pumping Action
At its core, a refrigeration compressor's function is to pump refrigerant through the refrigeration cycle. This seemingly simple action is multifaceted and incredibly important. The compressor doesn't just move refrigerant; it increases the refrigerant's pressure and temperature, preparing it for the crucial heat rejection phase in the condenser. This pressure increase is the key to efficient heat transfer and cooling. Think of it as the heart of the refrigeration system, tirelessly pumping life (in the form of cool air) into your refrigerator, air conditioner, or any other refrigeration application.
The Pumping Mechanism: A Closer Look
The exact method of pumping varies depending on the compressor type, but the underlying principle remains the same: increasing the refrigerant pressure. This pressure increase drives the refrigerant through the system, facilitating the heat transfer processes that lead to cooling.
-
Reciprocating Compressors: These compressors utilize a piston moving back and forth within a cylinder to compress the refrigerant. The piston's movement is controlled by a crankshaft and connecting rod, creating a cyclical pumping action.
-
Rotary Compressors: These use rotating components to compress the refrigerant. Scroll compressors, for example, use two spiral-shaped components, one fixed and one rotating, to trap and compress the refrigerant. Rotary vane compressors use rotating vanes to create pockets of refrigerant which are compressed as the vanes rotate.
-
Screw Compressors: These compressors use two intermeshing helical screws to compress the refrigerant. One screw rotates, while the other remains stationary, effectively trapping and compressing the refrigerant between the screw threads. These are particularly suited for large-scale refrigeration applications.
-
Centrifugal Compressors: These compressors use centrifugal force to increase the refrigerant's pressure. The refrigerant enters the compressor's impeller at the center, and the impeller's rotation throws the refrigerant outwards, increasing its pressure. Centrifugal compressors are commonly used in larger industrial refrigeration systems.
Regardless of the type, the pumping action is vital in establishing the pressure differential necessary for the refrigerant to absorb heat from the refrigerated space (evaporator) and then release it into the surroundings (condenser). This pressure differential drives the entire refrigeration cycle.
Beyond Pumping: Key Performance Indicators of Refrigeration Compressors
While pumping is the primary function, several other performance indicators are crucial for evaluating a compressor's efficiency and effectiveness. These indicators directly impact the overall performance and energy consumption of the refrigeration system.
1. Displacement: How Much Refrigerant Can Be Pumped?
Displacement refers to the volume of refrigerant a compressor can pump per unit of time. It's usually measured in cubic centimeters per minute (ccm) or cubic feet per minute (cfm). A higher displacement generally implies a greater cooling capacity, but this needs to be considered in context with other factors like efficiency. Understanding the system's cooling load is critical in selecting a compressor with the appropriate displacement.
2. Efficiency: How Much Energy Is Used to Pump?
Efficiency is paramount in modern refrigeration. Compressor efficiency is often expressed as a Coefficient of Performance (COP), which represents the ratio of cooling capacity to the power consumed. A higher COP indicates better efficiency, meaning more cooling output for less energy input. Factors affecting efficiency include the type of compressor, operating conditions, and refrigerant used. Choosing a highly efficient compressor can significantly reduce energy costs and environmental impact over the system's lifespan.
3. Pressure Ratio: How Much Pressure Does the Compressor Generate?
The pressure ratio, the ratio of the discharge pressure to the suction pressure, is a crucial parameter influencing the compressor's performance. A higher pressure ratio can lead to increased efficiency but may also place more stress on the compressor components. Optimal pressure ratios are crucial for efficient operation and depend on the specific refrigerant and application.
4. Reliability: How Long Can the Compressor Pump Consistently?
Reliability is crucial for any refrigeration system. Downtime can lead to significant losses, particularly in commercial settings. Compressor reliability is influenced by design, manufacturing quality, and proper maintenance. Investing in robust and reliable compressors is essential for minimizing downtime and maintaining consistent performance.
5. Noise Levels: How Quietly Can the Compressor Pump?
Noise levels are an important consideration, particularly in residential and commercial applications. Compressor noise can be minimized through advanced design techniques and vibration dampening. Noise reduction technologies are becoming increasingly important as consumers become more aware of the environmental impact of noise pollution.
The Role of Refrigerant in the Pumping Process
The refrigerant plays a vital role in the compressor's pumping action. The compressor compresses the refrigerant vapor, raising its pressure and temperature. The choice of refrigerant significantly impacts the compressor's performance and efficiency.
Modern refrigeration systems are increasingly moving towards environmentally friendly refrigerants with low global warming potentials (GWP) and ozone depletion potentials (ODP). These refrigerants can have slightly different thermodynamic properties, impacting the compressor's design and operating parameters. The selection of the appropriate refrigerant is a key part of system design optimization.
Types of Refrigerant Compressors: A Detailed Look
The diverse range of refrigeration applications necessitates a variety of compressor types. Each type possesses unique characteristics optimized for specific performance requirements.
1. Reciprocating Compressors: The Workhorse of Refrigeration
These are the most common type found in domestic refrigerators and smaller air conditioning units. Their relatively simple design and robust construction make them reliable and cost-effective. However, they can be prone to vibrations and noise, particularly at higher capacities. Recent advancements have led to quieter and more efficient reciprocating compressors, mitigating these drawbacks.
2. Rotary Compressors: Compact and Efficient Solutions
Rotary compressors, including scroll and vane types, are increasingly popular due to their compact size, high efficiency, and reduced noise and vibration compared to reciprocating compressors. They are often found in residential air conditioners, smaller commercial refrigeration units, and heat pump systems.
3. Screw Compressors: Powerhouses for Large-Scale Applications
Screw compressors are designed for high-capacity applications, like large industrial refrigeration systems, process cooling, and ice rinks. Their high displacement and robust design make them ideal for demanding environments. While efficient, their initial cost is generally higher than smaller compressors.
4. Centrifugal Compressors: High-Capacity and High-Efficiency Options
Centrifugal compressors are found in very large industrial applications such as ammonia refrigeration systems in food processing plants or large commercial buildings. They are known for their high capacity and efficiency at very large cooling loads but are more complex and require specialized maintenance.
Maintenance and Longevity of Refrigeration Compressors: Keeping the Pump Running Smoothly
Regular maintenance is crucial to ensure the longevity and efficient operation of a refrigeration compressor. Neglecting maintenance can lead to premature failure and costly repairs. Key maintenance practices include:
- Regular Inspection: Checking for leaks, unusual noises, and vibrations.
- Oil Changes: Maintaining the correct oil level and quality is essential for lubrication and cooling.
- Cleaning: Removing dirt and debris from the compressor and its surroundings.
- Professional Service: Regular servicing by qualified technicians ensures optimal performance and early detection of potential problems.
Ignoring these practices can lead to reduced efficiency, increased energy consumption, and ultimately, premature compressor failure.
Conclusion: The Unsung Hero of Cooling
Refrigeration compressors are the unsung heroes of modern cooling technology. Their primary function, the tireless pumping of refrigerant, is fundamental to the entire refrigeration cycle. Understanding the various types of compressors, their performance indicators, and the importance of maintenance is crucial for selecting and maintaining efficient and reliable refrigeration systems. From the smallest domestic refrigerator to the largest industrial chiller, the compressor’s pumping action remains the cornerstone of keeping things cool. The ongoing development of more efficient, environmentally friendly, and quieter compressors underscores the continuous evolution of this critical technology, ensuring that the cool air keeps on flowing.
Latest Posts
Latest Posts
-
Where Are You Allowed To Wash Your Hands Food Handlers
May 09, 2025
-
Which Shut Off Valves Should Be Open And Which Closed
May 09, 2025
-
When Would A Bias Most Likely Be Harmful
May 09, 2025
-
The Cor Is Responsible For Communications With The
May 09, 2025
-
What Are The Types Of Essential Records Army
May 09, 2025
Related Post
Thank you for visiting our website which covers about All Refrigeration Compressors Are Designed To Pump . We hope the information provided has been useful to you. Feel free to contact us if you have any questions or need further assistance. See you next time and don't miss to bookmark.