An Oil Furnace Heat Exchanger Is Built
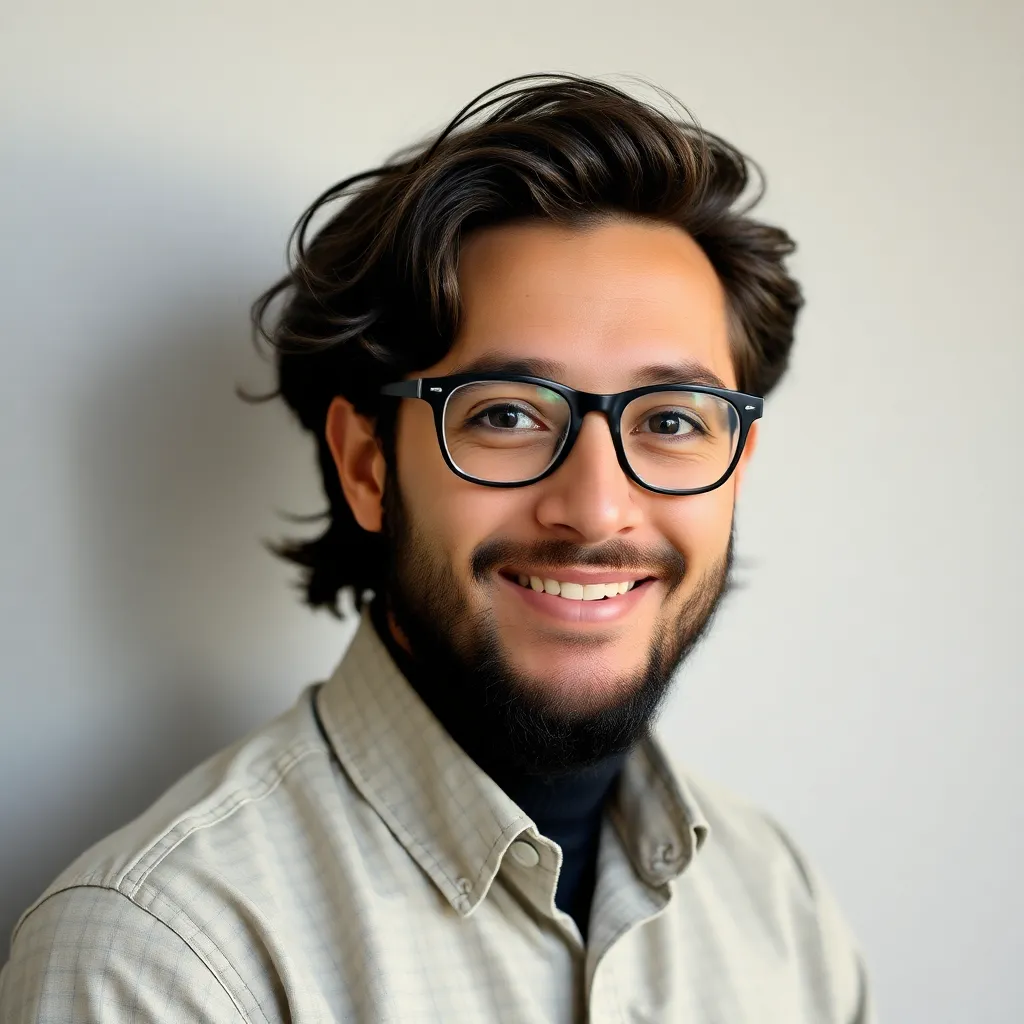
Breaking News Today
Apr 19, 2025 · 6 min read

Table of Contents
How an Oil Furnace Heat Exchanger is Built: A Deep Dive into Design and Manufacturing
An oil furnace heat exchanger is the heart of your heating system, responsible for transferring heat from the burning fuel to the air that warms your home. Understanding its construction is key to appreciating its function and troubleshooting potential problems. This comprehensive guide delves into the intricacies of oil furnace heat exchanger manufacturing, covering materials, design considerations, and quality control measures.
The Crucial Role of the Heat Exchanger
Before diving into the manufacturing process, let's emphasize the heat exchanger's critical role. It's where the combustion process's heat energy is converted into usable warmth for your home. Inefficient or damaged heat exchangers mean wasted energy and potential safety hazards. Understanding its construction allows for better maintenance and informed decisions regarding repairs or replacements.
Materials: The Foundation of Durability and Efficiency
The choice of materials for an oil furnace heat exchanger is paramount. They must withstand the extreme temperatures and corrosive environment created during combustion. Common materials include:
1. Aluminized Steel: A Popular Choice
Aluminized steel is a popular choice due to its cost-effectiveness and decent resistance to corrosion. A thin layer of aluminum is bonded to steel, enhancing its lifespan compared to bare steel. However, aluminized steel's lifespan is limited, especially in areas with corrosive elements in the air. The aluminum coating can eventually degrade, leading to rust and potential failure.
2. Stainless Steel: Premium Durability
Stainless steel offers superior corrosion resistance, extending the heat exchanger's lifespan significantly. Different grades of stainless steel provide varying levels of durability. Higher-grade stainless steel offers better resistance to high temperatures and corrosive byproducts of combustion. While more expensive upfront, the increased longevity often makes it a worthwhile investment in the long run.
3. Copper: Exceptional Heat Transfer
Copper boasts excellent heat transfer properties, ensuring efficient heat exchange between the combustion gases and the air. Its corrosion resistance is also superior to aluminized steel, though not always as high as some stainless steel grades. Copper heat exchangers are known for their durability and efficiency but typically command a higher price.
Design Considerations: Optimizing Heat Transfer and Efficiency
The design of the heat exchanger directly impacts its efficiency and lifespan. Key design considerations include:
1. Surface Area: Maximizing Heat Exchange
A larger surface area allows for more efficient heat transfer. Manufacturers achieve this through various designs, including:
-
Finned Tubes: These feature numerous fins extending from the tubes, significantly increasing the surface area exposed to the airflow. The fins are carefully designed to optimize air circulation and heat transfer.
-
Plate Design: Plate heat exchangers, while less common in oil furnaces, offer a high surface area-to-volume ratio. They are known for efficient heat transfer but require precise manufacturing and are often more complex than finned tube designs.
2. Gas Flow Path: Ensuring Complete Combustion
The design of the gas flow path is crucial for ensuring complete combustion. A well-designed path allows the hot gases to fully interact with the heat exchanger, maximizing heat transfer. Inefficient gas flow paths can lead to incomplete combustion, wasted energy, and increased emissions.
3. Airflow Management: Balanced Heat Distribution
The design must facilitate even airflow across the heat exchanger's surface to prevent hot spots and ensure uniform heating. Manufacturers often incorporate baffles or other design elements to manage airflow and optimize heat distribution.
Manufacturing Process: Precision and Quality Control
The manufacturing process involves several key stages:
1. Material Selection and Preparation: Establishing a Solid Foundation
The process begins with the careful selection and preparation of the chosen material. This may involve cutting, shaping, and cleaning the metal sheets or tubes to ensure precision and cleanliness.
2. Tube Bending and Forming: Creating the Heat Transfer Core
Precise bending of tubes is crucial to create the intricate network of passages for the hot gases. Automated bending machines ensure accuracy and consistency. The formed tubes are then carefully inspected for any defects.
3. Fin Attachment: Amplifying Heat Transfer Area
For finned-tube heat exchangers, the fins are attached to the tubes using various methods, including expansion, brazing, or welding. The attachment method must ensure strong bonding and even heat transfer across the entire surface.
4. Assembly and Welding: Building the Complete Structure
The various components of the heat exchanger are carefully assembled and welded together. This process requires precision and expertise to ensure the structural integrity and leak-proof operation of the heat exchanger. Advanced welding techniques, like laser welding, are often used to ensure high-quality welds.
5. Leak Testing: Ensuring Safety and Reliability
Rigorous leak testing is crucial to detect any imperfections in welds or joints that could lead to gas leaks. Pressure testing under controlled conditions is a common method used to identify leaks.
6. Quality Control and Inspection: Maintaining High Standards
Throughout the manufacturing process, stringent quality control measures are implemented to ensure that each heat exchanger meets the required specifications. This includes regular inspections and tests at each stage to detect and correct any flaws or deviations from the design. This stage also involves ensuring the heat exchanger meets safety standards.
Common Heat Exchanger Designs in Oil Furnaces
Oil furnaces often utilize one of two primary heat exchanger designs:
1. Aluminized Steel Tubular Heat Exchanger
This is the most common type found in budget-friendly oil furnaces. It consists of multiple tubes arranged in a parallel configuration. Hot gases from combustion pass through these tubes, transferring heat to the surrounding air. The relatively low cost and ease of manufacture make it a popular choice, but its shorter lifespan compared to other materials is a trade-off.
2. Stainless Steel or Copper Tubular Heat Exchanger
High-efficiency oil furnaces frequently use stainless steel or copper tubular heat exchangers. These materials offer enhanced durability and efficiency compared to aluminized steel. The higher initial cost is offset by longer lifespan and improved performance. The design is similar to aluminized steel versions but benefits from superior material properties.
Understanding Heat Exchanger Lifespan and Failure
Even with robust construction, heat exchangers eventually wear down. Several factors affect their lifespan:
- Material Quality: Higher-grade materials naturally last longer.
- Corrosion: Exposure to corrosive elements in combustion byproducts or the surrounding air accelerates degradation.
- Overheating: Excessive temperatures can damage the heat exchanger over time.
- Sediment Buildup: Accumulation of soot and dust restricts airflow and reduces efficiency, increasing stress on the exchanger.
Common signs of heat exchanger failure include:
- Reduced Heating Efficiency: Noticeably weaker heat output.
- Unusual Noises: Popping, crackling, or whistling sounds during operation.
- Gas Leaks: A strong smell of gas or a visible gas leak. (Call a professional immediately if you suspect a gas leak.)
- Cracks or Holes: Visible damage to the heat exchanger, requiring professional inspection and replacement.
Conclusion: A Complex System for Essential Comfort
The construction of an oil furnace heat exchanger is a sophisticated process requiring precise manufacturing and high-quality materials. Understanding this process allows for a greater appreciation of the component's importance in delivering reliable and safe home heating. While various designs and materials exist, the ultimate goal remains consistent: efficient, safe, and long-lasting heat transfer for your home's comfort. Regular maintenance and professional inspections are crucial to extend the life of your heat exchanger and avoid costly repairs or replacements.
Latest Posts
Latest Posts
-
Decibel Is A Measurement Of The Amount Of Pollution
Apr 19, 2025
-
The Sailor 2025 Program And The Implementation
Apr 19, 2025
-
Term Insurance Has Which Of The Following Characteristics
Apr 19, 2025
-
Staff Members Must Be Trained Specifically To Use Restraint
Apr 19, 2025
-
A Very Large Refrigerant Leak Can Cause
Apr 19, 2025
Related Post
Thank you for visiting our website which covers about An Oil Furnace Heat Exchanger Is Built . We hope the information provided has been useful to you. Feel free to contact us if you have any questions or need further assistance. See you next time and don't miss to bookmark.