An Unfavorable Materials Quantity Variance Indicates That
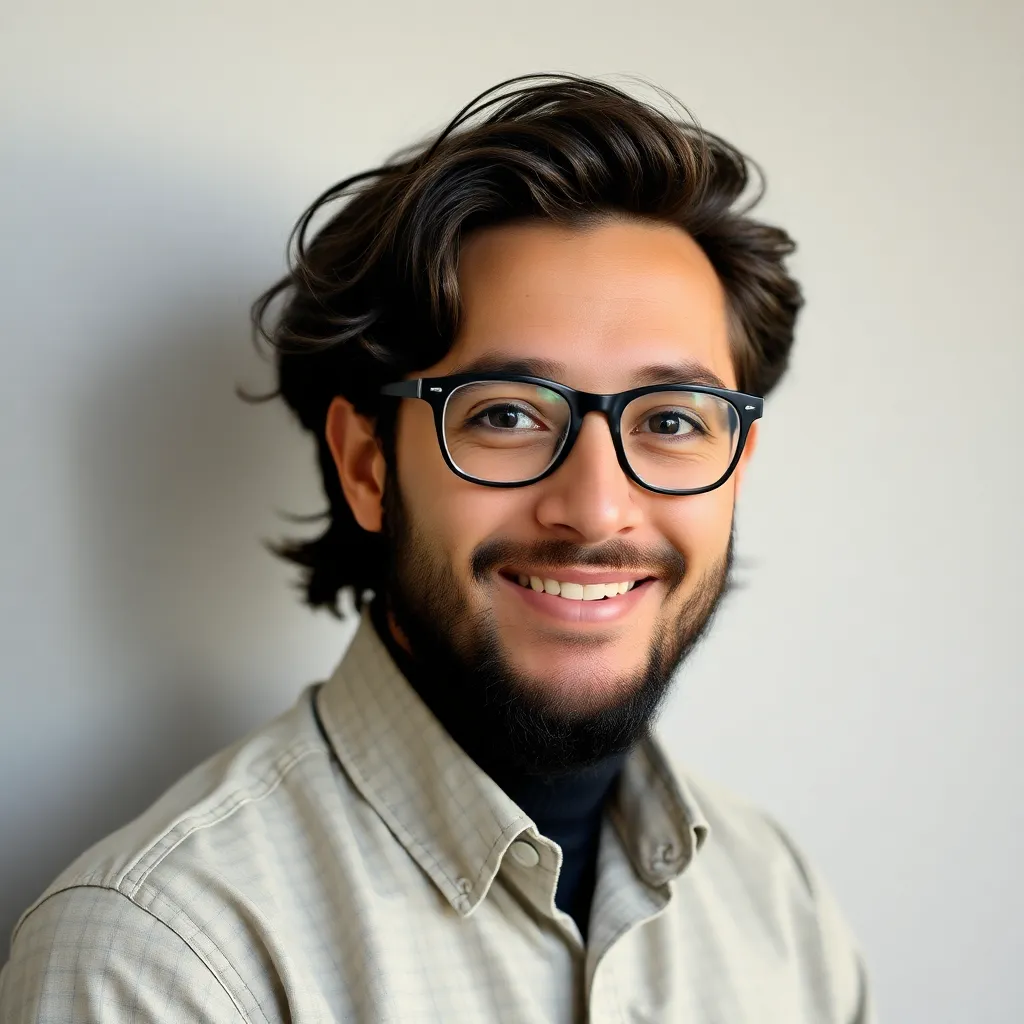
Breaking News Today
Apr 21, 2025 · 6 min read

Table of Contents
An Unfavorable Materials Quantity Variance Indicates That… Trouble Ahead?
An unfavorable materials quantity variance signifies that a company has used more raw materials than anticipated for a given level of production. This seemingly simple statement belies a complex issue that can significantly impact profitability and efficiency. Understanding the reasons behind this variance is crucial for effective cost management and operational improvement. This article delves deep into the meaning, causes, and corrective actions associated with an unfavorable materials quantity variance. We'll explore various scenarios, providing practical examples and actionable strategies to mitigate future occurrences.
Understanding Materials Quantity Variance
Before diving into unfavorable variances, let's establish a foundational understanding. A materials quantity variance measures the difference between the actual quantity of materials used in production and the standard quantity expected for the actual output achieved. The formula is:
(Actual Quantity Used – Standard Quantity Allowed) x Standard Price
A favorable variance indicates that less material was used than expected, resulting in cost savings. Conversely, an unfavorable variance indicates that more material was used, leading to increased costs. This excess cost directly impacts the company's bottom line, reducing profitability.
Common Causes of Unfavorable Materials Quantity Variance
Several factors can contribute to an unfavorable materials quantity variance. Identifying the root cause is paramount to developing effective solutions. These factors can be broadly categorized into:
1. Inefficient Production Processes
- Poorly maintained machinery: Malfunctioning equipment can lead to increased material waste due to spoilage, defects, or inefficient operations. Old, outdated machines often suffer from higher rates of material loss.
- Lack of employee training: Inadequate training on proper material handling, usage techniques, and operating procedures can result in significant material waste and increased consumption. Untrained workers may use more materials than necessary, leading to inefficiencies.
- Suboptimal production methods: Inefficient production processes, including poor workflow design or inadequate quality control checks, can contribute to material wastage. A poorly planned production flow can lead to delays, rework, and ultimately, more material consumption.
- Inadequate production planning: Poor planning can lead to material shortages that force the use of more expensive or less efficient substitutes, leading to an unfavorable variance. This can also cause production bottlenecks and require extra materials to compensate for delays.
- Obsolete technology: Using outdated technology might increase the quantity of raw materials needed due to inefficiencies and higher wastage.
2. Poor Quality of Raw Materials
- Inferior material quality: Using lower-quality raw materials might necessitate higher consumption to achieve the desired output. This is because inferior materials may be less consistent, requiring more material to compensate for defects or inconsistencies.
- Material defects: Receiving damaged or defective raw materials can lead to higher consumption as more material is needed to replace spoiled or unusable items. This can cause significant disruptions in the production process.
3. Ineffective Inventory Management
- Poor inventory control: Inadequate inventory management can result in material shortages, forcing the use of substitute materials or expedited orders, leading to an unfavorable variance. Lack of proper tracking and management can lead to material loss due to spoilage or obsolescence.
- Excess inventory: While not directly leading to higher material usage per unit, excessive inventory can mask inefficiencies, allowing them to persist without immediate detection. The higher carrying costs of excess inventory indirectly contribute to an unfavorable financial position.
4. External Factors
- Unforeseen circumstances: Unexpected events like power outages, natural disasters, or supplier disruptions can cause increased material consumption due to production delays or the need to use alternative materials. These events are often beyond the control of the company.
- Changes in product specifications: Modifications in product specifications can necessitate the use of different materials or techniques, potentially leading to a temporary increase in material usage while the production process adapts.
Analyzing and Interpreting the Unfavorable Variance
Simply identifying an unfavorable materials quantity variance isn't sufficient. A thorough investigation is crucial to pinpoint the exact cause. This involves:
- Gathering data: Collect comprehensive data on actual material usage, production output, and standard material allowances. Compare actual performance against planned performance.
- Investigating deviations: Analyze variances between actual and standard figures, examining individual production runs for patterns or anomalies.
- Identifying bottlenecks: Pinpoint areas within the production process where material wastage is most significant. Focus on areas with the highest deviation.
- Seeking employee feedback: Gather input from production workers regarding potential contributing factors. Frontline workers often have valuable insights into the root causes of such variances.
- Reviewing supplier performance: Assess whether the quality of supplied materials meets specifications. Poor-quality materials often require more material to compensate for defects.
Corrective Actions to Address Unfavorable Materials Quantity Variance
Once the root cause(s) have been identified, implementing corrective actions is vital to prevent future occurrences. These actions might include:
- Investing in new machinery: Upgrading outdated equipment can significantly reduce material waste and improve efficiency.
- Improving employee training: Providing comprehensive training on proper material handling, usage, and production techniques can reduce errors and wastage.
- Optimizing production processes: Implementing lean manufacturing principles or other process improvement methodologies can enhance efficiency and minimize waste.
- Implementing stricter quality control measures: Strengthening quality control checks at various stages of the production process can prevent defective materials from entering the production line.
- Improving inventory management: Implementing robust inventory control systems can prevent shortages and reduce the need for last-minute material acquisitions or substitutes.
- Negotiating better supplier agreements: Establishing stronger relationships with suppliers and negotiating better quality control terms can ensure the consistent supply of high-quality materials.
- Regular performance monitoring: Implementing regular monitoring and review of key performance indicators (KPIs) related to material usage can help identify potential problems early on.
- Using statistical process control (SPC): Implementing SPC techniques can aid in the identification of trends and patterns that may indicate underlying problems affecting material usage.
Beyond the Numbers: The Broader Implications
An unfavorable materials quantity variance is not simply an accounting problem; it reflects deeper operational inefficiencies. Ignoring it can lead to:
- Reduced profitability: Increased material costs directly impact profitability, potentially leading to reduced margins and lower overall returns.
- Increased waste: Excessive material consumption contributes to environmental concerns and increased disposal costs.
- Damaged reputation: Consistent product defects resulting from poor material usage can damage the company's reputation and customer trust.
- Lost competitiveness: Higher production costs can make a company less competitive in the market, especially if competitors have better material management practices.
Conclusion: Proactive Management is Key
An unfavorable materials quantity variance is a warning sign. It indicates underlying issues within the production process or supply chain that need immediate attention. By diligently investigating the root causes, implementing corrective actions, and maintaining regular monitoring, companies can not only reduce costs but also enhance operational efficiency, improve product quality, and strengthen their competitive position. Proactive management is crucial in preventing these variances from becoming a persistent drain on profitability and impacting the overall health of the business. Remember that continuous improvement is key – regularly reviewing processes and seeking opportunities for optimization is a vital component of effective cost control and operational excellence.
Latest Posts
Latest Posts
-
In What Direction Are Eyebrow Hairs Tweezed
Apr 21, 2025
-
What Types Of Information Can Be Found On An Epa
Apr 21, 2025
-
Identify The Statements That Describe The War On Poverty
Apr 21, 2025
-
Cuticle Remover Cream Contains Which Of The Following Ingredients
Apr 21, 2025
-
Why Is Social Media An Important Part Of Inbound Marketing
Apr 21, 2025
Related Post
Thank you for visiting our website which covers about An Unfavorable Materials Quantity Variance Indicates That . We hope the information provided has been useful to you. Feel free to contact us if you have any questions or need further assistance. See you next time and don't miss to bookmark.