Category A Samples Can Be Mixed With Category B
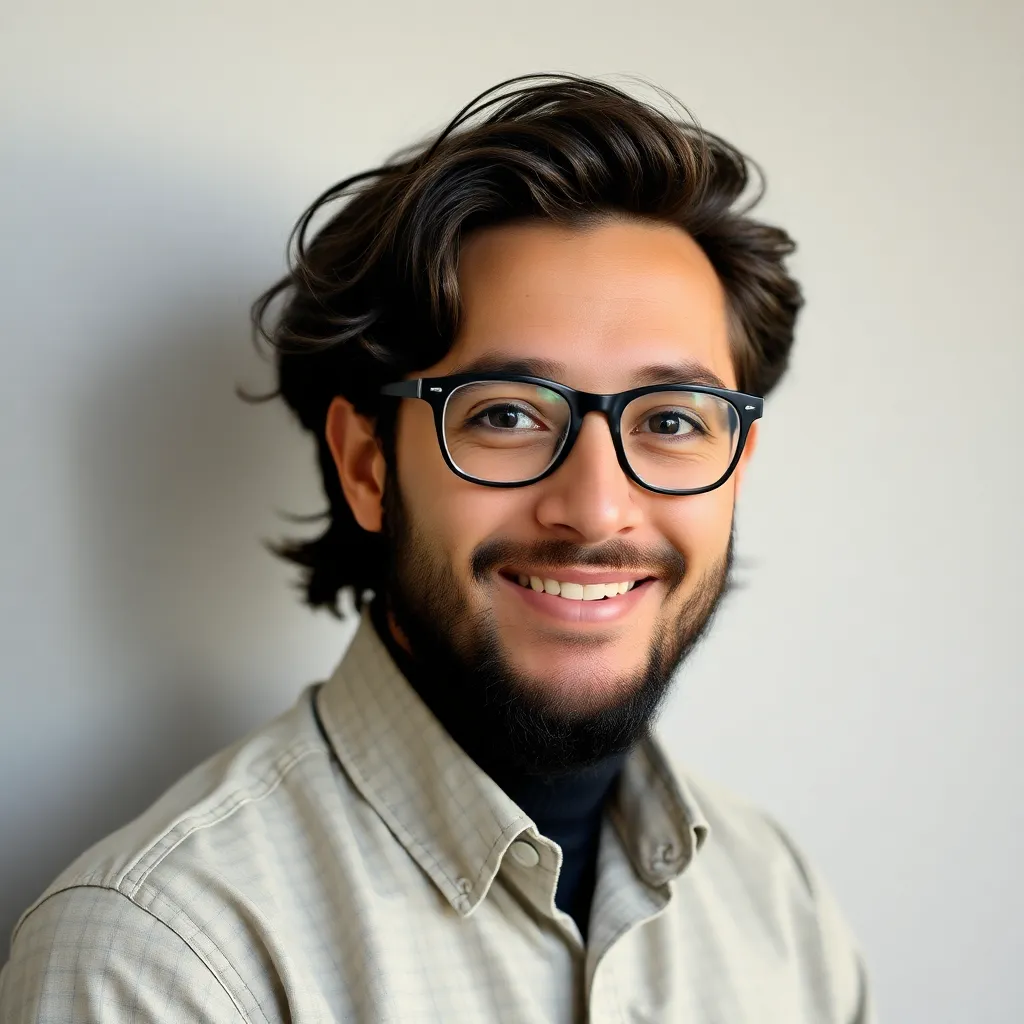
Breaking News Today
May 09, 2025 · 6 min read

Table of Contents
Can Category A Samples Be Mixed with Category B? A Comprehensive Guide
Mixing samples from different categories – a seemingly simple question – can have profound implications across numerous fields, from scientific research to industrial manufacturing and even culinary arts. This comprehensive guide delves deep into the considerations surrounding the mixing of Category A and Category B samples, exploring the potential benefits, risks, and best practices for various applications. We'll examine the underlying principles, emphasizing the importance of careful planning and adherence to established protocols.
Understanding the Context: Defining Categories A and B
Before we delve into the intricacies of mixing, it's crucial to clearly define what constitutes "Category A" and "Category B." The specific meaning of these categories is highly context-dependent. For instance:
In Scientific Research:
- Category A: Could represent control samples – those exhibiting known characteristics or undergoing a standard treatment. These samples serve as a baseline for comparison.
- Category B: Might encompass experimental samples – those exposed to different treatments or conditions, representing the variables being studied. Mixing these could confound results, obscuring the impact of the independent variables.
In Industrial Manufacturing:
- Category A: Could refer to high-quality, certified raw materials meeting stringent specifications.
- Category B: Might signify materials of lower quality, potentially containing impurities or exhibiting variations in composition. Mixing could compromise product quality and consistency.
In Food and Beverage:
- Category A: Could denote premium ingredients, carefully selected for flavor, aroma, and texture.
- Category B: Could represent less expensive or surplus ingredients. Mixing could alter the final product's taste, appearance, and shelf life.
The specific characteristics defining each category are dictated by the application and the intended outcome. Therefore, understanding the specific criteria for each category within your particular context is absolutely essential before considering any mixing.
Potential Benefits of Mixing Category A and Category B Samples
While the risks are often highlighted, certain situations justify mixing Category A and Category B samples. These benefits must always be weighed against the potential drawbacks.
Cost Reduction:
In industrial settings or large-scale production, mixing lower-cost Category B materials with Category A materials can significantly reduce production expenses, especially if the impact on the final product is minimal or acceptable within pre-defined tolerances. This approach requires thorough testing and quality control measures to ensure the final product meets minimum standards.
Enhanced Properties:
In some cases, combining Category A and Category B samples can lead to novel or enhanced properties. This is particularly relevant in materials science, where blending components with different characteristics might result in improved strength, durability, or other desirable traits. However, this requires a deep understanding of material behavior and precise control over the mixing process.
Resource Optimization:
Mixing could help utilize surplus or otherwise unusable Category B materials, preventing waste and promoting sustainability. This is especially important in industries dealing with valuable or sensitive resources. However, strict quality control must be maintained to prevent contamination or degradation of the final product.
Potential Risks and Drawbacks of Mixing Category A and Category B Samples
The potential downsides of combining disparate categories often outweigh the advantages. Ignoring these risks can lead to serious consequences.
Contamination and Degradation:
Introducing Category B samples might contaminate Category A samples, rendering them unsuitable for their intended purpose. This is particularly true in scientific research, where contamination can lead to inaccurate or misleading results. Similarly, mixing incompatible materials in manufacturing can result in chemical reactions, degradation of the product's quality, or even safety hazards.
Inconsistent Results:
The lack of homogeneity when mixing samples from different categories can lead to inconsistent results. This is a significant concern in experiments or processes where precision and repeatability are critical. Variations in the composition of the mixed samples could confound analysis and prevent drawing reliable conclusions.
Compromised Product Quality:
In manufacturing or food production, mixing Category A and Category B samples might compromise the final product's quality, appearance, taste, or performance. This can result in product recalls, financial losses, and damage to brand reputation.
Safety Hazards:
Mixing incompatible materials can create hazardous conditions. Chemical reactions, explosions, or the release of toxic substances are all potential risks, highlighting the importance of thorough safety assessments before any mixing process begins.
Best Practices for Mixing Category A and Category B Samples
When the potential benefits outweigh the risks, a carefully planned and controlled mixing process is paramount.
Thorough Testing and Analysis:
Before mixing, rigorous testing and analysis of both Category A and Category B samples are vital to determine compatibility, assess potential risks, and establish appropriate mixing ratios. This could involve chemical analysis, physical testing, and microbial testing, depending on the specific application.
Controlled Mixing Environment:
The mixing process should be conducted in a controlled environment to minimize the risk of contamination and ensure uniformity. This might necessitate the use of specialized equipment, clean rooms, or other controlled settings.
Strict Quality Control:
Throughout the mixing process and after, strict quality control measures are critical to ensure that the mixed samples meet the required specifications. This could involve regular testing, inspection, and documentation of the entire process.
Detailed Documentation:
Maintaining detailed records of the mixing process, including the quantities of each category of samples, mixing procedures, and test results, is crucial for traceability and ensuring accountability. This documentation facilitates troubleshooting, quality assurance, and compliance with relevant regulations.
Adherence to Regulations and Standards:
When dealing with regulated industries, it's crucial to adhere to all relevant regulations and standards to ensure compliance and prevent potential legal or safety issues. This could involve following specific guidelines for handling materials, conducting tests, and documenting the process.
Case Studies: Real-World Examples
Illustrative examples will solidify the concepts discussed above.
Example 1: Pharmaceutical Research: Mixing a control group (Category A) of cells untreated with a new drug with an experimental group (Category B) treated with the drug is generally avoided. Combining them would contaminate the control, making it impossible to determine the drug's effect accurately.
Example 2: Food Production: A premium chocolate manufacturer (Category A chocolate) might mix a small percentage of slightly less-refined chocolate (Category B) to reduce costs. This requires meticulous testing to ensure that the final product meets quality and taste standards. Extensive sensory analysis and quality control checks would be crucial.
Example 3: Materials Science: Researchers might blend a high-strength polymer (Category A) with a more flexible elastomer (Category B) to create a composite material with improved flexibility and impact resistance. This would necessitate precise control over the mixing ratios and thorough analysis of the resulting material's mechanical properties.
Conclusion: A Cautious Approach is Key
The decision to mix Category A and Category B samples should never be taken lightly. A comprehensive risk assessment, thorough testing, rigorous quality control, and adherence to best practices are paramount. The potential benefits must always be carefully weighed against the potential drawbacks, ensuring that the ultimate outcome aligns with the intended objectives and doesn't compromise safety, quality, or the reliability of results. Prioritizing a cautious and well-planned approach is the key to successful and responsible mixing of samples from different categories.
Latest Posts
Latest Posts
-
Does A Quizlet User Know If I Combine Quizzes
May 09, 2025
-
The Reinstatement Provision In A Health Insurance Policy Is
May 09, 2025
-
According To Freud Much Of Our Behavior Is Motivated By
May 09, 2025
-
What Is True About Product Recalls In The 21st Century
May 09, 2025
-
Which Of The Following Statements About Crossing Over Is True
May 09, 2025
Related Post
Thank you for visiting our website which covers about Category A Samples Can Be Mixed With Category B . We hope the information provided has been useful to you. Feel free to contact us if you have any questions or need further assistance. See you next time and don't miss to bookmark.