Chapter 7: Advanced Composite Material - Faa
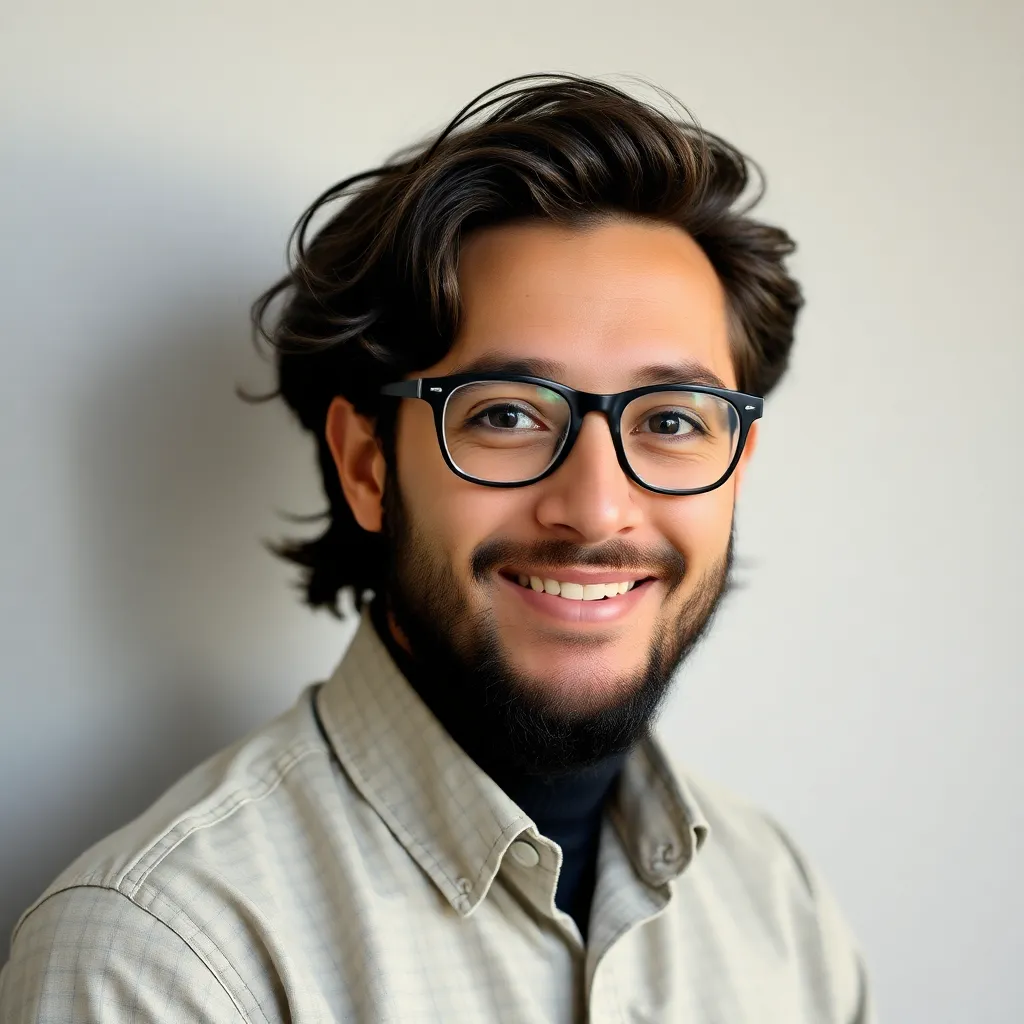
Breaking News Today
Mar 30, 2025 · 6 min read

Table of Contents
Chapter 7: Advanced Composite Materials - FAA Regulations and Considerations
The Federal Aviation Administration (FAA) plays a crucial role in regulating the use of advanced composite materials in aircraft design and manufacturing. This chapter delves into the complexities of FAA regulations surrounding composite materials, focusing on the challenges, approvals, and ongoing advancements that shape this vital area of aviation technology.
Understanding the FAA's Role in Composite Material Certification
The FAA's primary responsibility is ensuring the safety and airworthiness of all aircraft operating within its jurisdiction. This extends to the materials used in their construction. Given the unique properties and potential failure modes of advanced composite materials (compared to traditional metals like aluminum), the FAA has established stringent certification processes to ensure the safe and reliable integration of these materials into aircraft structures. This involves rigorous testing, analysis, and documentation throughout the entire lifecycle of a composite part or component, from design and manufacturing to in-service inspection and maintenance.
The Complexity of Composite Material Behavior
Unlike metals, composites exhibit complex, anisotropic behavior. This means their properties (strength, stiffness, fatigue resistance) vary depending on the direction of applied load. This complexity necessitates sophisticated analysis techniques and testing methodologies to accurately predict and manage the structural performance of composite components under various flight conditions. The FAA regulations reflect this complexity, requiring comprehensive material characterization, structural analysis, and testing protocols to demonstrate the airworthiness of composite structures.
FAA Certification Process for Composite Aircraft Parts
The FAA's certification process for composite aircraft parts is multifaceted and rigorous. It typically involves the following key stages:
1. Material Characterization and Qualification:
This initial stage focuses on thoroughly understanding the properties of the specific composite materials being used. This involves extensive testing to determine key parameters such as:
- Tensile strength: The ability of the material to withstand pulling forces.
- Compressive strength: The ability of the material to withstand squeezing forces.
- Shear strength: The ability of the material to withstand forces that cause layers to slide past each other.
- Flexural strength: The ability of the material to withstand bending forces.
- Fatigue strength: The ability of the material to withstand repeated loading cycles.
- Impact resistance: The material's ability to absorb energy from impacts.
- Creep resistance: The material's ability to resist deformation under sustained stress.
- Environmental resistance: The material's ability to withstand exposure to various environmental conditions such as temperature, humidity, and ultraviolet radiation.
The FAA requires extensive data demonstrating the consistency and reliability of these material properties.
2. Design and Analysis:
Once the material properties are established, the design and structural analysis of the composite part must demonstrate its ability to meet the required safety margins under all anticipated flight conditions. Sophisticated finite element analysis (FEA) techniques are commonly employed to model the behavior of the composite structure under various loading scenarios. The analysis must account for the anisotropic nature of the composite material, as well as any potential flaws or imperfections.
The FAA reviews the design and analysis process meticulously, requiring detailed documentation of the methodologies used and the results obtained.
3. Manufacturing Process Qualification:
The manufacturing process itself must be rigorously controlled and qualified to ensure consistency in the quality and properties of the finished composite part. The FAA demands a thorough understanding of how the manufacturing process affects the final product's structural integrity. This includes detailed process specifications, quality control measures, and non-destructive testing procedures.
4. Testing and Qualification:
Once the part is manufactured, it undergoes a series of rigorous tests to verify that it meets the design requirements and safety standards. These tests may include:
- Static testing: Applying static loads to the part to determine its strength and stiffness.
- Fatigue testing: Applying cyclic loads to the part to determine its fatigue life.
- Impact testing: Simulating impacts to assess the part's damage tolerance.
- Environmental testing: Exposing the part to various environmental conditions to assess its durability.
The results of these tests must demonstrate that the part meets the required safety margins and complies with the FAA's regulations.
5. Continued Airworthiness:
Even after certification, the FAA requires ongoing monitoring and maintenance of composite aircraft parts. This includes regular inspections to detect potential damage and degradation, as well as procedures for repairing or replacing damaged components. The FAA provides guidelines for these procedures to ensure continued airworthiness throughout the aircraft's operational life.
Challenges in Composite Material Certification
Despite the significant advantages of composite materials, their certification presents several challenges:
- Complexity of Material Behavior: The anisotropic nature of composites makes accurate modeling and analysis challenging.
- Damage Tolerance: Detecting and assessing damage in composite structures is more difficult than in metallic structures. This necessitates development of advanced non-destructive inspection (NDI) techniques.
- Durability and Degradation: Long-term durability and resistance to environmental degradation are key concerns. The FAA requires extensive testing and analysis to demonstrate the long-term reliability of composite structures.
- Manufacturing Variability: Maintaining consistent quality and properties throughout the manufacturing process is critical. The FAA mandates rigorous quality control measures.
- Repair and Maintenance: Repairing damaged composite structures can be complex and expensive. The FAA requires clear guidelines for the repair and maintenance of composite components.
- Life Prediction: Accurately predicting the service life of composite components is crucial for ensuring safe operation. Advancements in modeling and testing techniques are constantly being developed to improve life prediction capabilities.
Ongoing Advancements in Composite Material Certification
The FAA is continually working to improve its certification process for composite materials, keeping pace with advancements in material science, manufacturing technologies, and analysis techniques. This includes:
- Development of advanced analytical tools: Improving the accuracy and efficiency of FEA and other analytical methods.
- Advanced Non-Destructive Inspection (NDI) techniques: Developing more sensitive and reliable methods for detecting damage in composite structures.
- Improved material characterization techniques: Developing more accurate and efficient methods for characterizing the properties of composite materials.
- Life prediction models: Developing more accurate models to predict the service life of composite structures.
- Collaboration with industry: Working closely with industry to develop and implement improved certification procedures.
The Future of Composite Materials in Aviation
Advanced composite materials are set to play an increasingly significant role in future aircraft design. Their high strength-to-weight ratio, excellent fatigue resistance, and design flexibility offer significant advantages in terms of fuel efficiency, reduced emissions, and improved performance. However, continued collaboration between the FAA and the aviation industry is crucial to address the challenges associated with their certification and ensure the safe and reliable integration of composite materials into aircraft structures. This includes continued investment in research and development of advanced materials, manufacturing processes, analysis techniques, and inspection methods.
Conclusion
The FAA's rigorous certification process for advanced composite materials plays a critical role in ensuring the safety and airworthiness of aircraft. While the complexities of composite behavior present unique challenges, the advancements in materials science, analysis techniques, and non-destructive inspection methods are paving the way for wider adoption of these materials in aviation. The ongoing collaboration between the FAA and the aviation industry is essential to maintain a balance between promoting innovation and ensuring the highest levels of safety in the air. The future of flight increasingly hinges on the successful integration and continued certification of these lightweight, high-performance materials. Understanding the intricacies of the FAA's regulatory framework and the ongoing innovations within the field is key for anyone involved in the design, manufacture, or maintenance of composite aircraft structures.
Latest Posts
Latest Posts
-
Self Worth Accomplishment And Confidence Represent The
Apr 01, 2025
-
A Food Establishment That Serves Raw Oysters
Apr 01, 2025
-
Atls Test Questions And Answers 10th Edition
Apr 01, 2025
-
Label The Map Of Costa Rica Based On Panorama
Apr 01, 2025
-
When Using A Visual Signal To Support Your Recovery Efforts
Apr 01, 2025
Related Post
Thank you for visiting our website which covers about Chapter 7: Advanced Composite Material - Faa . We hope the information provided has been useful to you. Feel free to contact us if you have any questions or need further assistance. See you next time and don't miss to bookmark.