Costs Assigned To Units Of Product Under Absorption Costing Include:
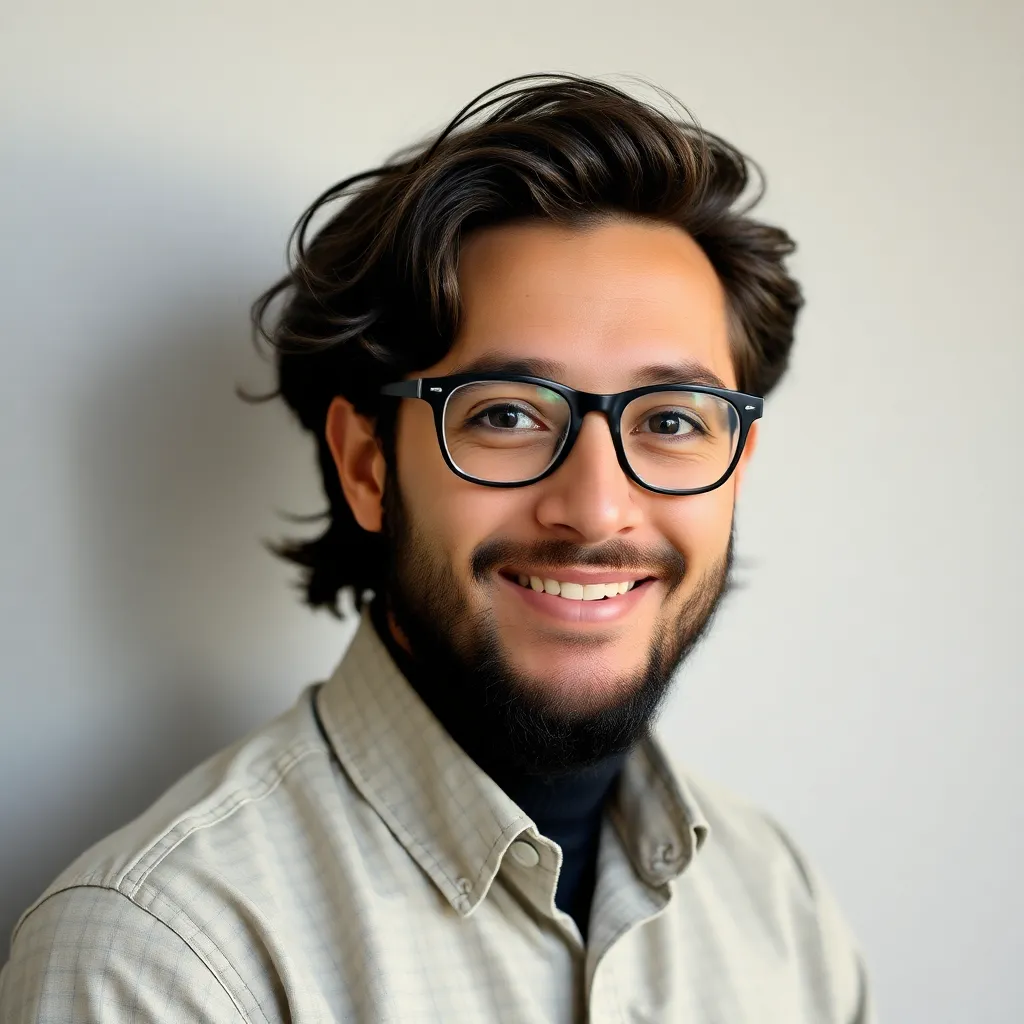
Breaking News Today
Apr 04, 2025 · 6 min read
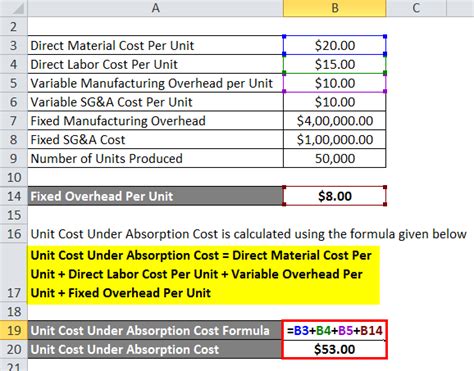
Table of Contents
Costs Assigned to Units of Product Under Absorption Costing
Absorption costing, also known as full costing, is a method of inventory costing where all manufacturing costs—both fixed and variable—are included in the cost of a product. This contrasts with variable costing, which only includes variable manufacturing costs. Understanding the costs assigned under absorption costing is crucial for accurate financial reporting, pricing decisions, and inventory valuation. This comprehensive guide will delve deep into the various costs included, their implications, and the differences from variable costing.
Key Costs Included in Absorption Costing
Absorption costing adheres to Generally Accepted Accounting Principles (GAAP) and requires that all manufacturing costs be capitalized as inventory. These costs are then expensed as the goods are sold. This comprehensive approach includes:
1. Direct Materials
These are the raw materials directly used in the production process and are easily traceable to the finished product. Examples include:
- Raw materials: The primary ingredients used to manufacture the product. For a bakery, this could be flour, sugar, and eggs. For a car manufacturer, it would be steel, rubber, and glass.
- Packaging materials: Materials directly used in packaging the finished product for sale. This could include boxes, labels, and plastic wrap.
Importance: Accurate tracking of direct materials is paramount for precise cost calculations. Any discrepancies or inefficiencies in material usage directly impact the final product cost. Effective inventory management and procurement strategies are vital to minimizing waste and ensuring consistent material costs.
2. Direct Labor
This encompasses the wages and benefits paid to workers directly involved in the manufacturing process. This includes:
- Wages: The hourly or salary payments made to assembly line workers, machine operators, and other production personnel.
- Benefits: Employer contributions to employee benefits such as health insurance, retirement plans, and paid time off. These are often expressed as a percentage of wages.
Importance: Direct labor costs can fluctuate based on factors like employee productivity, overtime hours, and wage rates. Efficient workforce management, training, and automation can help control direct labor costs and improve overall productivity.
3. Variable Manufacturing Overhead
These are indirect costs that change proportionally with the level of production. They include:
- Indirect materials: These are materials used in the production process but are not directly traceable to the finished product, such as lubricants, cleaning supplies, and small tools.
- Indirect labor: This includes the wages and benefits paid to support staff involved in production, such as maintenance personnel, supervisors, and quality control inspectors.
- Utilities: Costs associated with electricity, water, and gas used in the manufacturing facility. These costs typically increase as production volume increases.
Importance: Accurate allocation of variable manufacturing overhead requires careful tracking of production activity and cost drivers. Effective cost accounting systems are essential to capture and assign these costs appropriately.
4. Fixed Manufacturing Overhead
These are indirect costs that remain constant regardless of the production volume. They include:
- Depreciation: The allocation of the cost of manufacturing equipment and facilities over their useful lives.
- Rent: The cost of renting the manufacturing facility.
- Property taxes: Taxes paid on the manufacturing facility.
- Insurance: Insurance premiums for the manufacturing facility and equipment.
- Salaries of factory supervisors and managers: Fixed salaries paid to personnel overseeing production operations.
Importance: While fixed manufacturing overhead doesn't change with production volume, it's crucial to accurately allocate these costs to the units produced to determine the true cost of each product. The allocation method used can significantly impact the final cost per unit. Common methods include machine hours, direct labor hours, or a predetermined overhead rate.
How Costs are Assigned: Allocation Methods
Assigning fixed manufacturing overhead to units produced requires careful consideration. Several methods are available, each with its own advantages and disadvantages:
-
Direct Labor Hours: This method allocates overhead based on the number of direct labor hours used in production. Simpler to implement, but may not accurately reflect overhead consumption if production processes vary significantly in labor intensity.
-
Machine Hours: This method allocates overhead based on the machine hours used in production. More suitable for automated production environments where machinery is the primary cost driver.
-
Predetermined Overhead Rate: This involves calculating a predetermined rate based on budgeted overhead costs and a chosen cost driver (e.g., direct labor hours, machine hours). This method provides a more stable cost estimate, but requires careful budgeting and forecasting.
-
Activity-Based Costing (ABC): A more sophisticated approach that allocates overhead based on specific activities that consume resources. This offers a more accurate cost assignment, especially in complex manufacturing processes with multiple activities.
Absorption Costing vs. Variable Costing: Key Differences
While absorption costing includes all manufacturing costs, variable costing only includes variable manufacturing costs. This difference has significant implications for financial reporting and decision-making:
Feature | Absorption Costing | Variable Costing |
---|---|---|
Fixed MOH | Included in product cost | Treated as a period expense |
Inventory Valuation | Higher due to inclusion of fixed MOH | Lower as fixed MOH is not included |
Net Income | Can vary with changes in inventory levels | Remains consistent regardless of inventory |
GAAP Compliance | Compliant | Not compliant for external financial reporting |
Decision Making | Less useful for short-term decisions | More useful for short-term decisions |
Implications for Financial Reporting and Decision-Making
The choice between absorption and variable costing has significant implications:
-
Inventory Valuation: Absorption costing results in a higher inventory valuation because it includes fixed manufacturing overhead. This impacts the balance sheet and can affect financial ratios.
-
Net Income: Absorption costing net income can fluctuate based on changes in inventory levels. If production exceeds sales, a portion of fixed manufacturing overhead remains in inventory, resulting in higher net income. Conversely, if sales exceed production, net income decreases as the fixed overhead is released from inventory. Variable costing net income is less affected by inventory fluctuations.
-
Pricing Decisions: Absorption costing provides a complete picture of product costs, which can inform pricing strategies. However, it may not be as helpful for short-term pricing decisions.
-
Performance Evaluation: Variable costing separates fixed and variable costs, making it easier to evaluate the efficiency of operations and identify areas for cost reduction.
Conclusion
Absorption costing, with its inclusion of all manufacturing costs, is a crucial method for financial reporting under GAAP. Understanding the various components of cost assignment – direct materials, direct labor, variable and fixed manufacturing overhead – is essential for accurate product costing. While providing a complete cost picture suitable for external reporting, its complexities and dependence on inventory levels can make it less suitable for short-term operational decisions. A thorough understanding of both absorption and variable costing allows businesses to make informed decisions based on the specific context and goals. The choice of costing method depends on the reporting requirements, the nature of the business, and the type of decisions being made.
Latest Posts
Latest Posts
-
What Is The Goal In Treating Dehydrated Skin
Apr 04, 2025
-
In How Many States Is Booth Rental Allowed
Apr 04, 2025
-
Which One Of These Best Defines An Annuity Due
Apr 04, 2025
-
The Mcintosh Mx1375 Reference Entertainment System Includes A Subwoofer
Apr 04, 2025
-
Walking On The Hot Sand On A Beach
Apr 04, 2025
Related Post
Thank you for visiting our website which covers about Costs Assigned To Units Of Product Under Absorption Costing Include: . We hope the information provided has been useful to you. Feel free to contact us if you have any questions or need further assistance. See you next time and don't miss to bookmark.