Dc Injection Braking Is Often Used In Forklifts
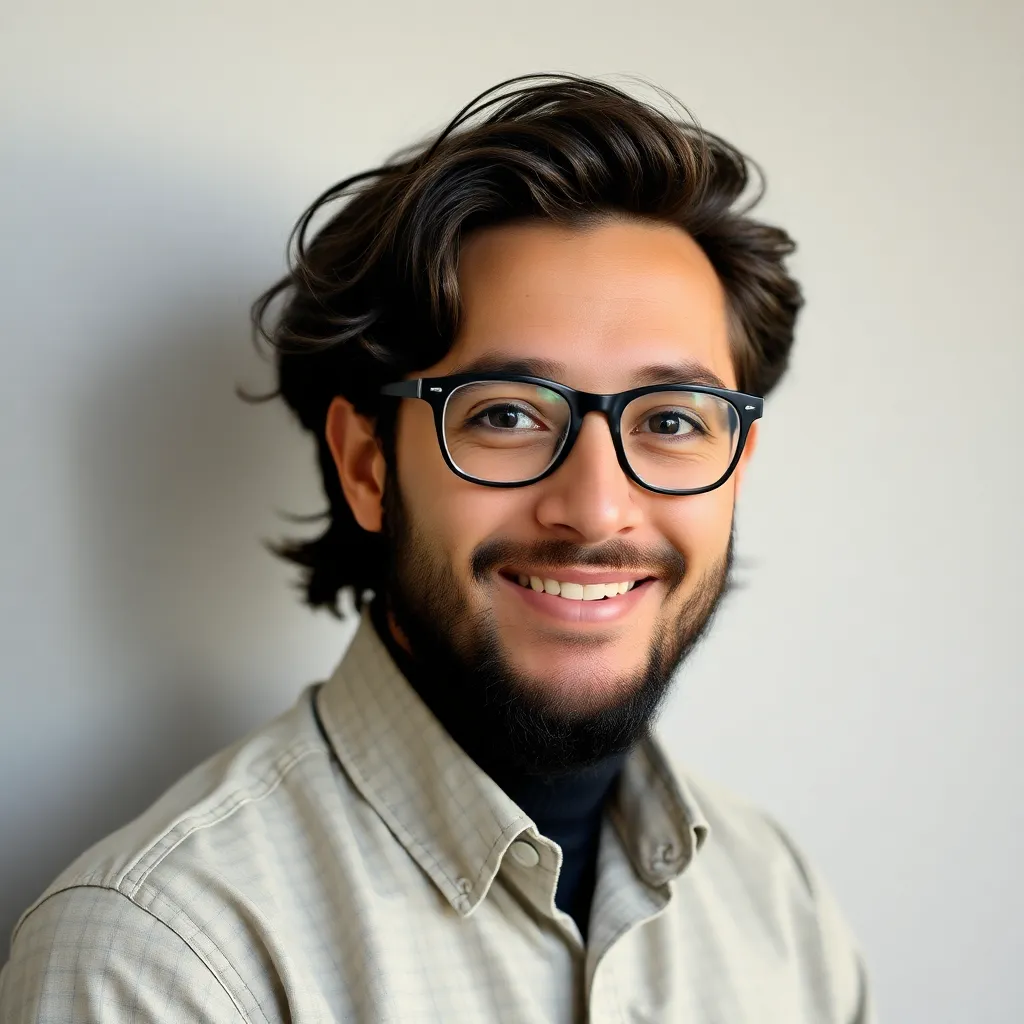
Breaking News Today
Apr 16, 2025 · 5 min read

Table of Contents
DC Injection Braking: A Deep Dive into its Application in Forklifts
DC injection braking is a crucial safety and efficiency feature frequently employed in modern forklifts. This braking system offers significant advantages over traditional braking methods, especially in the demanding environment of material handling. This article will delve deep into the mechanics, benefits, and considerations surrounding DC injection braking in forklifts.
Understanding DC Injection Braking
DC injection braking is a regenerative braking technique used to slow or stop a motor by injecting a direct current (DC) of opposite polarity into the motor windings. Instead of relying solely on friction-based braking, which can lead to wear and tear, DC injection braking utilizes the motor itself as a generator, converting kinetic energy into electrical energy. This electrical energy is then dissipated as heat through a resistor.
How it Works: A Step-by-Step Explanation
-
Motor Operation: During normal operation, the forklift motor receives DC power, converting it into mechanical energy to drive the wheels.
-
Braking Initiation: When the braking pedal is depressed or the braking system is activated (often through a control system), the polarity of the DC current supplied to the motor is reversed.
-
Regenerative Braking: This reversed polarity transforms the motor into a generator. The rotating motor now generates DC electricity as its rotational energy is converted.
-
Energy Dissipation: This generated electricity is then passed through a resistor network, effectively converting the electrical energy back into heat. This heat is then dissipated into the environment.
-
Deceleration: The conversion of kinetic energy into electrical energy, followed by heat dissipation, creates a braking force, slowing the forklift down.
-
Stopping: The braking force continues until the forklift comes to a complete stop, or until the braking input is released.
Advantages of DC Injection Braking in Forklifts
DC injection braking offers a plethora of benefits compared to traditional braking systems, making it a preferred choice for forklift manufacturers and operators alike.
1. Reduced Wear and Tear on Mechanical Components
Unlike friction-based braking systems that rely on brake pads and rotors, DC injection braking significantly minimizes wear and tear on these components. This translates to:
- Extended Lifespan: Brake pads and rotors last considerably longer, reducing maintenance costs and downtime.
- Reduced Maintenance: Less frequent brake pad and rotor replacements mean less labor and expense.
- Improved Reliability: The system is less prone to failure due to the reduced mechanical wear.
2. Enhanced Safety
DC injection braking contributes to improved forklift safety in several ways:
- Improved Braking Response: The system provides quick and effective braking, reducing stopping distances.
- Reduced Fade: Unlike friction brakes which can experience fade under prolonged or heavy use, DC injection braking maintains consistent braking performance.
- Emergency Braking Capabilities: Many systems incorporate emergency braking features that automatically activate DC injection braking in the event of a malfunction or other critical situation.
3. Increased Efficiency
The regenerative nature of DC injection braking contributes to enhanced efficiency:
- Energy Recovery: A portion of the kinetic energy is recovered and converted into electrical energy, although this energy is dissipated as heat, it is still more efficient than simple frictional dissipation.
- Reduced Energy Consumption: This can lead to slightly lower overall energy consumption, improving operational costs.
4. Enhanced Control and Maneuverability
DC injection braking often provides improved control, especially at lower speeds:
- Precise Control: The system allows for smoother and more precise control during low-speed maneuvers.
- Improved Maneuverability: This makes the forklift easier to handle in tight spaces and reduces the risk of accidents.
Comparing DC Injection Braking with Other Braking Systems
Let's compare DC injection braking with other commonly used braking systems in forklifts:
DC Injection Braking vs. Friction Braking
Feature | DC Injection Braking | Friction Braking |
---|---|---|
Wear & Tear | Minimal | Significant |
Maintenance | Reduced | High |
Braking Response | Quick and effective | Can be slower, dependent on conditions |
Fade | Minimal | Prone to fade under prolonged use |
Efficiency | More energy efficient (partially regenerative) | Less energy efficient |
Cost | Higher initial investment | Lower initial investment |
DC Injection Braking vs. Regenerative Braking (Other Types)
While DC injection braking is a form of regenerative braking, other regenerative systems might exist. The core difference often lies in how the regenerated energy is handled. Some systems might store the energy in batteries, increasing overall efficiency further. However, DC injection braking's simplicity and reliability often make it the preferred choice in many forklift applications.
Considerations for Implementing DC Injection Braking
While DC injection braking offers numerous benefits, certain considerations are vital during implementation and operation:
1. Initial Investment Cost
The initial cost of implementing DC injection braking is typically higher compared to traditional friction-based systems. However, the long-term cost savings due to reduced maintenance and extended lifespan often outweigh the initial investment.
2. System Complexity
DC injection braking involves a more complex system compared to simple friction braking. This requires specialized expertise for installation, maintenance, and repair.
3. Heat Dissipation
The resistor network used to dissipate the generated heat needs to be adequately designed to prevent overheating. Poor heat dissipation can lead to system failure.
4. Compatibility
Ensure the DC injection braking system is compatible with the forklift's motor and other electrical components. Improper integration can lead to malfunctions and safety hazards.
Conclusion: The Future of Forklift Braking
DC injection braking is progressively becoming the standard in modern forklift design. Its combination of enhanced safety, reduced maintenance, and improved efficiency makes it a compelling choice for material handling applications. While the initial investment might be higher, the long-term benefits far outweigh the costs, leading to safer, more efficient, and cost-effective forklift operation. As technology continues to advance, we can expect further refinements and improvements to this vital braking technology, ensuring even greater safety and productivity in the demanding world of forklift operations. Continuous research and development will likely focus on optimizing heat dissipation, improving energy recovery efficiency, and enhancing system integration for seamless and reliable performance. The future of forklift braking points clearly towards more sophisticated and efficient regenerative braking solutions like DC injection braking.
Latest Posts
Latest Posts
-
Gathering Information Helps Someone Consider To Solve A Problem
Apr 19, 2025
-
Which Food Contains The Least Healthful Type Of Fat
Apr 19, 2025
-
When You Drive At Night You Can Reduce
Apr 19, 2025
-
What Is The Color Of An An Steel Flared Tube Fitting
Apr 19, 2025
-
During Which Type Of Counseling Does The Senior
Apr 19, 2025
Related Post
Thank you for visiting our website which covers about Dc Injection Braking Is Often Used In Forklifts . We hope the information provided has been useful to you. Feel free to contact us if you have any questions or need further assistance. See you next time and don't miss to bookmark.