Effective Capacity Is Always Blank______ Design Capacity.
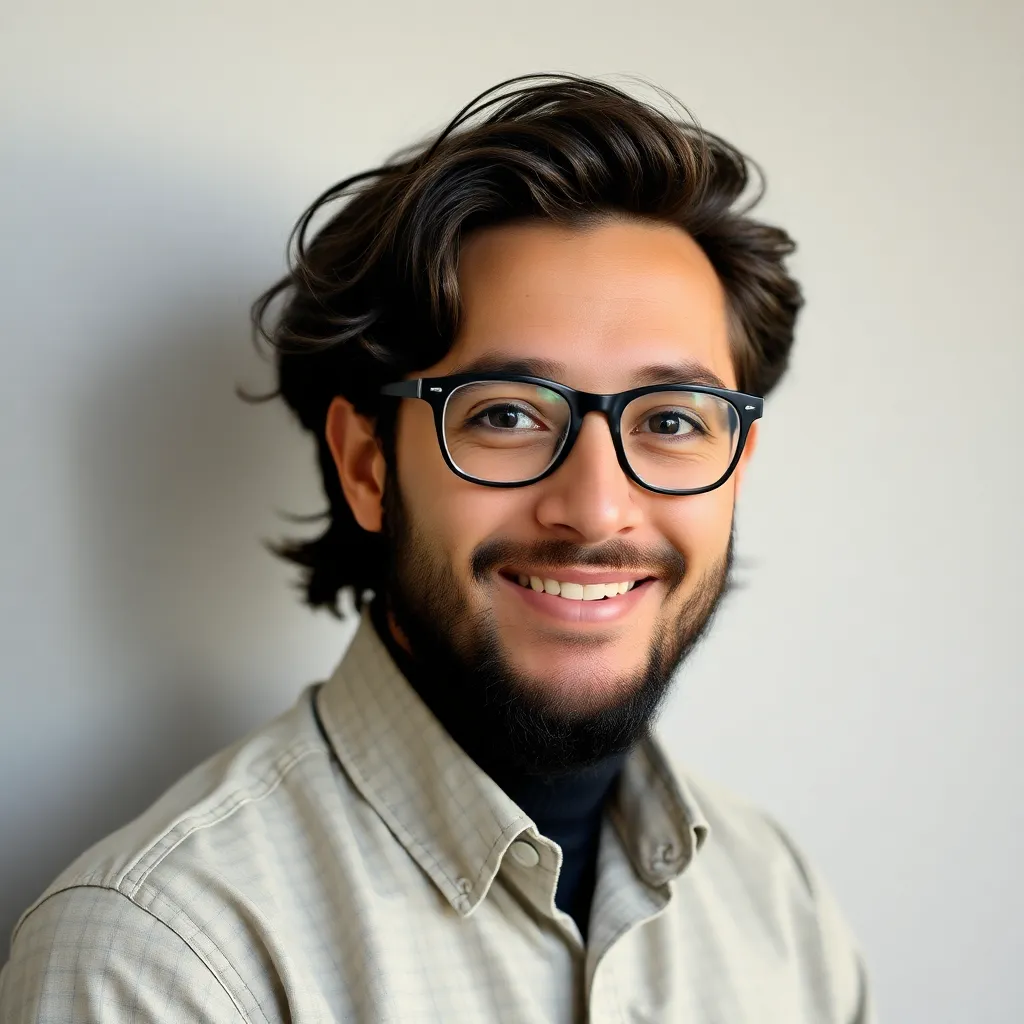
Breaking News Today
Apr 09, 2025 · 6 min read

Table of Contents
Effective Capacity is Always Less Than Design Capacity: Understanding the Gap and Optimizing Performance
Effective capacity, the actual output a system can achieve given its real-world constraints, is always less than design capacity, the theoretical maximum output based on ideal conditions. This fundamental difference stems from a multitude of factors that impact production efficiency and ultimately, a company's bottom line. Understanding this gap, its causes, and the strategies to bridge it is crucial for optimizing operational performance and achieving business goals.
Understanding Design Capacity and Effective Capacity
Before delving into the reasons for this disparity, let's define our key terms:
Design Capacity: This represents the maximum output a system or process can achieve under ideal conditions. It's a theoretical limit, assuming perfect efficiency, no downtime, and readily available resources. Think of it as the manufacturer's stated potential, often found in brochures or specifications.
Effective Capacity: This is the actual output a system achieves considering real-world constraints. These constraints can range from machine breakdowns and employee absenteeism to material shortages and unforeseen bottlenecks. Effective capacity is the realistic output, reflecting the true capabilities of the system under typical operating conditions.
The difference between these two capacities highlights the inherent limitations and inefficiencies present in any real-world operation. The gap isn't necessarily a sign of failure, but rather an indicator of areas needing improvement and optimization.
Why Effective Capacity is Always Less Than Design Capacity: The Key Factors
The gap between design and effective capacity arises from numerous factors, which can be broadly categorized as:
1. Operational Inefficiencies:
-
Machine Breakdowns and Maintenance: Unexpected equipment failures or scheduled maintenance inevitably lead to downtime, reducing the time available for actual production. Even with robust maintenance schedules, unexpected issues arise, affecting effective capacity. This is particularly impactful in manufacturing environments with complex machinery.
-
Material Shortages and Supply Chain Issues: Delays in receiving raw materials or components can bring production to a halt. Supply chain disruptions, whether due to unforeseen events or logistical challenges, directly reduce effective capacity. This underscores the importance of robust supply chain management and contingency planning.
-
Quality Control Issues: Defects in the production process can lead to wasted materials, rework, and scrap, significantly impacting the actual output. Strong quality control measures, including proactive inspections and process improvements, are essential to minimizing this impact.
-
Bottlenecks in the Production Process: A bottleneck occurs when one stage of the production process operates slower than others, restricting the overall output. Identifying and addressing bottlenecks is crucial for improving effective capacity and overall throughput.
-
Employee Absenteeism and Turnover: Employee absence due to illness, vacation, or other reasons can reduce workforce availability and hence, production output. High employee turnover also impacts efficiency due to the time and resources needed for training new personnel.
2. Policy and Management Factors:
-
Planned Downtime: While unavoidable, scheduled maintenance, cleaning, and safety inspections contribute to the gap between design and effective capacity. Careful planning and scheduling of these activities are crucial to minimizing their impact.
-
Safety Regulations and Compliance: Adhering to safety regulations and industry standards often requires additional time and resources, reducing the time available for production. These regulations, while crucial, indirectly limit effective capacity.
-
Production Scheduling and Planning: Inefficient scheduling can lead to resource underutilization or conflicts, directly impacting the final output. Effective scheduling practices are critical to optimizing resource allocation and maximizing effective capacity.
-
Product Mix and Customization: Producing a diverse range of products or customizing orders often increases complexity and reduces the efficiency of specialized processes, directly impacting the achievable output. Balancing the needs of customization with operational efficiency is crucial.
3. External Factors:
-
Economic Downturns and Market Demand: Fluctuations in market demand can significantly influence production levels. Reduced demand necessitates lower production, resulting in underutilization of design capacity.
-
Natural Disasters and Unexpected Events: Unforeseen events such as natural disasters or pandemics can severely disrupt operations, leading to significant reductions in effective capacity. Business continuity plans are essential to mitigate the impact of such events.
-
Government Regulations and Policies: Changes in government regulations or policies can impact production processes, often imposing additional restrictions and increasing complexity, leading to a lower effective capacity.
-
Competition and Market Dynamics: Competitive pressures might force companies to operate at a lower capacity to remain price-competitive, further widening the gap between design and effective capacity.
Bridging the Gap: Strategies for Optimizing Effective Capacity
Improving the ratio of effective capacity to design capacity is a continuous improvement process requiring strategic interventions. Here are some key strategies:
1. Process Optimization:
-
Lean Manufacturing Principles: Implementing lean methodologies helps to eliminate waste in all forms (muda), including overproduction, waiting, transportation, inventory, motion, over-processing, and defects. This results in a smoother, more efficient production flow.
-
Six Sigma Methodology: Six Sigma focuses on reducing variation and defects in processes to achieve near-perfect quality. This minimizes rework, waste, and downtime, improving effective capacity.
-
Value Stream Mapping: Visualizing the entire production process helps identify bottlenecks and areas for improvement, guiding efficient resource allocation and process redesign.
-
Automation and Technological Advancements: Automating repetitive tasks and incorporating advanced technologies can significantly improve efficiency, reduce human error, and increase throughput, ultimately increasing effective capacity.
2. Capacity Planning and Management:
-
Accurate Forecasting and Demand Planning: Predicting future demand allows for optimized resource allocation and production scheduling, minimizing idle time and maximizing utilization.
-
Capacity Cushion: Maintaining a planned buffer capacity allows for handling unexpected fluctuations in demand or unforeseen issues, ensuring consistent production levels.
-
Flexible Manufacturing Systems: Adaptable systems allow for quicker response to changes in demand or product mix, reducing the impact of fluctuations and maximizing effective capacity.
3. Workforce Management:
-
Employee Training and Development: Investing in employee skills and training enhances efficiency, reduces errors, and minimizes downtime, positively impacting effective capacity.
-
Effective Scheduling and Shift Management: Optimizing employee scheduling ensures sufficient workforce availability and minimizes disruptions caused by absenteeism.
-
Employee Engagement and Motivation: A motivated and engaged workforce is more productive and efficient, contributing to increased effective capacity.
4. Supply Chain Optimization:
-
Strategic Sourcing and Supplier Relationships: Establishing strong relationships with reliable suppliers ensures timely delivery of materials, minimizing disruptions and maximizing production.
-
Inventory Management: Efficient inventory management balances the need for readily available materials with the cost of storage and minimizes the risk of shortages.
-
Risk Management and Contingency Planning: Developing plans to mitigate potential supply chain disruptions ensures business continuity and reduces the impact on effective capacity.
5. Technology and Data Analytics:
-
Real-time Monitoring and Data Analytics: Tracking key performance indicators (KPIs) in real-time provides insights into operational efficiency and allows for prompt identification and resolution of problems.
-
Predictive Maintenance: Utilizing data analysis to predict potential equipment failures allows for proactive maintenance, minimizing downtime and maximizing effective capacity.
-
Advanced Planning and Scheduling Software: Specialized software can optimize production schedules, resource allocation, and supply chain management, improving overall efficiency.
By systematically addressing the factors that contribute to the gap between design and effective capacity and implementing the strategies outlined above, organizations can significantly improve their operational performance, increase their overall output, and ultimately, boost their profitability. The key is to adopt a proactive approach to identifying and mitigating potential constraints, constantly striving for optimization and continuous improvement. Remember, the pursuit of bridging this gap is an ongoing journey, not a destination.
Latest Posts
Latest Posts
-
A Patient Presents After A 25 Foot Fall
Apr 17, 2025
-
Which Characteristic Is Most Likely To Indicate A Binge Eating Disorder
Apr 17, 2025
-
By 1900 Germanys Steel Production Exceeded All Other Countries Except
Apr 17, 2025
-
Match Each Economist To His Economic Belief
Apr 17, 2025
-
Jobs And Careers That Require Degrees Or Certificates Generally
Apr 17, 2025
Related Post
Thank you for visiting our website which covers about Effective Capacity Is Always Blank______ Design Capacity. . We hope the information provided has been useful to you. Feel free to contact us if you have any questions or need further assistance. See you next time and don't miss to bookmark.