Effective Controls Protect ______ From Workplace Hazards.
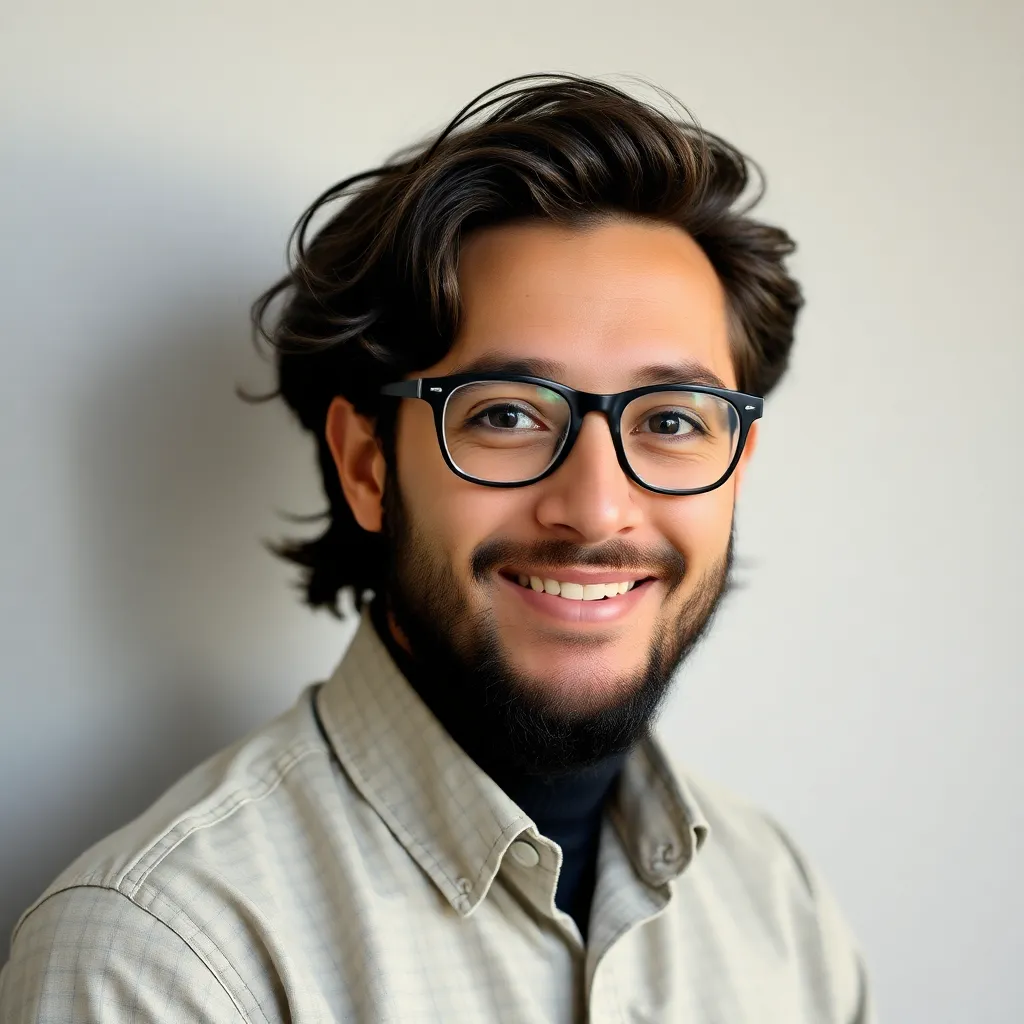
Breaking News Today
May 10, 2025 · 6 min read

Table of Contents
Effective Controls Protect Workers from Workplace Hazards
Workplace hazards are a significant concern for businesses of all sizes. From slips and falls to exposure to hazardous chemicals, the potential for injury or illness is ever-present. However, implementing effective controls can drastically reduce the risk of workplace accidents and protect your most valuable asset: your employees. This comprehensive guide explores various control measures, their implementation, and the crucial role they play in fostering a safe and productive work environment.
Understanding Workplace Hazards and Risk Assessment
Before delving into control measures, it's essential to understand the nature of workplace hazards. These hazards can be categorized into several groups:
1. Physical Hazards:
- Noise: Prolonged exposure to loud noises can lead to hearing loss.
- Vibration: Hand-arm vibration syndrome (HAVS) and whole-body vibration can cause significant health problems.
- Temperature extremes: Exposure to extreme heat or cold can cause heat stroke, hypothermia, or other health issues.
- Radiation: Exposure to ionizing or non-ionizing radiation poses serious health risks.
- Ergonomic hazards: Poor posture, repetitive movements, and awkward working positions can lead to musculoskeletal disorders (MSDs).
- Lighting: Inadequate lighting can cause eye strain and accidents.
2. Chemical Hazards:
- Toxic substances: Exposure to toxic chemicals can cause various health problems, including poisoning, respiratory issues, and cancer.
- Irritants: Substances that irritate the skin, eyes, or respiratory system.
- Carcinogens: Substances known to cause cancer.
- Flammable and explosive substances: Pose a significant fire and explosion risk.
3. Biological Hazards:
- Bacteria, viruses, and fungi: Exposure can lead to infections and diseases.
- Bloodborne pathogens: Such as HIV and Hepatitis B and C, pose a significant risk to healthcare workers and others.
- Parasites: Can cause various illnesses.
4. Psychosocial Hazards:
- Stress: Excessive workload, bullying, harassment, and lack of control can lead to stress-related illnesses.
- Violence: Workplace violence can range from verbal abuse to physical assault.
- Burnout: A state of emotional, physical, and mental exhaustion.
5. Ergonomic Hazards:
These hazards relate to the design of the workplace and the tasks performed. Poor workstation design, repetitive movements, and awkward postures contribute to musculoskeletal disorders (MSDs) like carpal tunnel syndrome and back pain.
Conducting a Thorough Risk Assessment:
A comprehensive risk assessment is the foundation of any effective workplace safety program. This involves:
- Identifying hazards: Systematically identifying all potential hazards in the workplace.
- Assessing risks: Determining the likelihood and severity of harm from each hazard.
- Evaluating existing controls: Assessing the effectiveness of current safety measures.
- Implementing control measures: Putting in place appropriate control measures to eliminate or reduce risks.
- Monitoring and reviewing: Regularly monitoring the effectiveness of control measures and reviewing the risk assessment as needed.
Hierarchy of Controls: Prioritizing Safety Measures
The hierarchy of controls outlines a prioritized approach to managing workplace hazards. The most effective controls aim to eliminate the hazard entirely, while less effective controls reduce the risk. The hierarchy is:
-
Elimination: Removing the hazard completely. This is the most effective control method. For example, replacing a hazardous chemical with a safer alternative.
-
Substitution: Replacing a hazardous substance or process with a less hazardous one. For example, using a less toxic cleaning agent.
-
Engineering controls: Modifying the workplace or equipment to reduce exposure to hazards. Examples include installing ventilation systems, using guarding on machinery, or providing ergonomic workstations.
-
Administrative controls: Implementing procedures and policies to manage hazards. Examples include training programs, safe work procedures, and work permits.
-
Personal Protective Equipment (PPE): Providing employees with PPE to protect them from hazards. This is the least effective control measure and should be used only as a last resort when other controls are not feasible. Examples include safety glasses, gloves, respirators, and hearing protection.
Implementing Effective Control Measures: A Detailed Look
Let's examine each control measure in more detail:
1. Elimination: The Gold Standard
Eliminating the hazard is always the preferred approach. This might involve:
- Replacing hazardous materials: Switching to safer alternatives.
- Automating processes: Reducing manual handling and exposure to hazards.
- Redesigning work processes: Eliminating tasks that expose workers to risks.
2. Substitution: A Safer Alternative
Substitution involves replacing a hazardous substance or process with a less hazardous one. Examples include:
- Replacing solvents with water-based cleaners.
- Using less toxic pesticides.
- Substituting manual lifting with mechanical aids.
3. Engineering Controls: Modifying the Workplace
Engineering controls physically alter the workplace or equipment to reduce exposure to hazards. These are often permanent solutions and highly effective. Examples include:
- Ventilation systems: Removing airborne contaminants.
- Machine guarding: Preventing contact with moving parts.
- Emergency shut-off switches: Quickly stopping machinery in emergencies.
- Ergonomic workstations: Designed to reduce strain and fatigue.
- Improved lighting: Reducing eye strain and accidents.
- Containment systems: Preventing the spread of hazardous materials.
4. Administrative Controls: Procedures and Policies
Administrative controls involve implementing procedures and policies to manage hazards. These are crucial for managing risks that cannot be eliminated or substituted. Examples include:
- Safety training programs: Educating employees on hazards and safety procedures.
- Safe work procedures: Detailed instructions for performing tasks safely.
- Work permits: Authorizing hazardous work after assessing risks.
- Regular inspections: Identifying potential hazards and ensuring compliance with safety procedures.
- Emergency response plans: Procedures for handling emergencies and accidents.
- Regular maintenance programs: Ensuring equipment is functioning properly.
- Communication strategies: Keeping employees informed about safety issues and changes.
5. Personal Protective Equipment (PPE): The Last Line of Defense
PPE should be used only as a last resort when other controls are not feasible. It's crucial to remember that PPE protects the individual, not the hazard itself. Proper selection, training, and maintenance of PPE are vital. Examples include:
- Safety glasses: Protecting eyes from flying debris.
- Hearing protection: Reducing noise exposure.
- Respirators: Protecting the respiratory system from airborne contaminants.
- Gloves: Protecting hands from chemicals and other hazards.
- Safety shoes: Protecting feet from falling objects and crushing hazards.
- High-visibility clothing: Increasing visibility in low-light conditions.
Maintaining and Reviewing Controls: Ongoing Commitment to Safety
Implementing controls is only the first step. Regular maintenance, monitoring, and review are crucial to ensure their continued effectiveness. This involves:
- Regular inspections: Identifying potential hazards and ensuring controls are functioning properly.
- Employee feedback: Gathering input from employees about potential hazards and the effectiveness of controls.
- Incident investigations: Thoroughly investigating accidents to identify root causes and prevent recurrence.
- Regular training: Keeping employees updated on safety procedures and changes.
- Reviewing the risk assessment: Updating the assessment to reflect changes in the workplace or processes.
Legal and Ethical Responsibilities: Protecting Your Workforce
Employers have a legal and ethical responsibility to provide a safe and healthy workplace for their employees. Failure to implement effective controls can lead to:
- Accidents and injuries: Resulting in lost productivity, increased healthcare costs, and potential lawsuits.
- Fines and penalties: From regulatory bodies for non-compliance with safety regulations.
- Damage to reputation: Negative publicity can damage a company's image and brand.
By prioritizing the implementation and maintenance of effective controls, businesses can significantly reduce workplace hazards, protect their employees, and foster a culture of safety and wellbeing. Investing in a robust safety program isn't just a legal requirement; it's a sound business practice that benefits both employees and the bottom line. A safe workplace is a productive workplace.
Latest Posts
Latest Posts
-
Domain 5 Lesson 1 Fill In The Blanks
May 10, 2025
-
California State Board Of Cosmetology Practice Test
May 10, 2025
-
An Abnormal Discharge From The Pharynx Is Known As
May 10, 2025
-
The Theory Of Constraints Defines Inventory As
May 10, 2025
-
The Term Behavioral Crisis Is Best Defined As
May 10, 2025
Related Post
Thank you for visiting our website which covers about Effective Controls Protect ______ From Workplace Hazards. . We hope the information provided has been useful to you. Feel free to contact us if you have any questions or need further assistance. See you next time and don't miss to bookmark.