Employers Duty To Have Fall Protection Is When
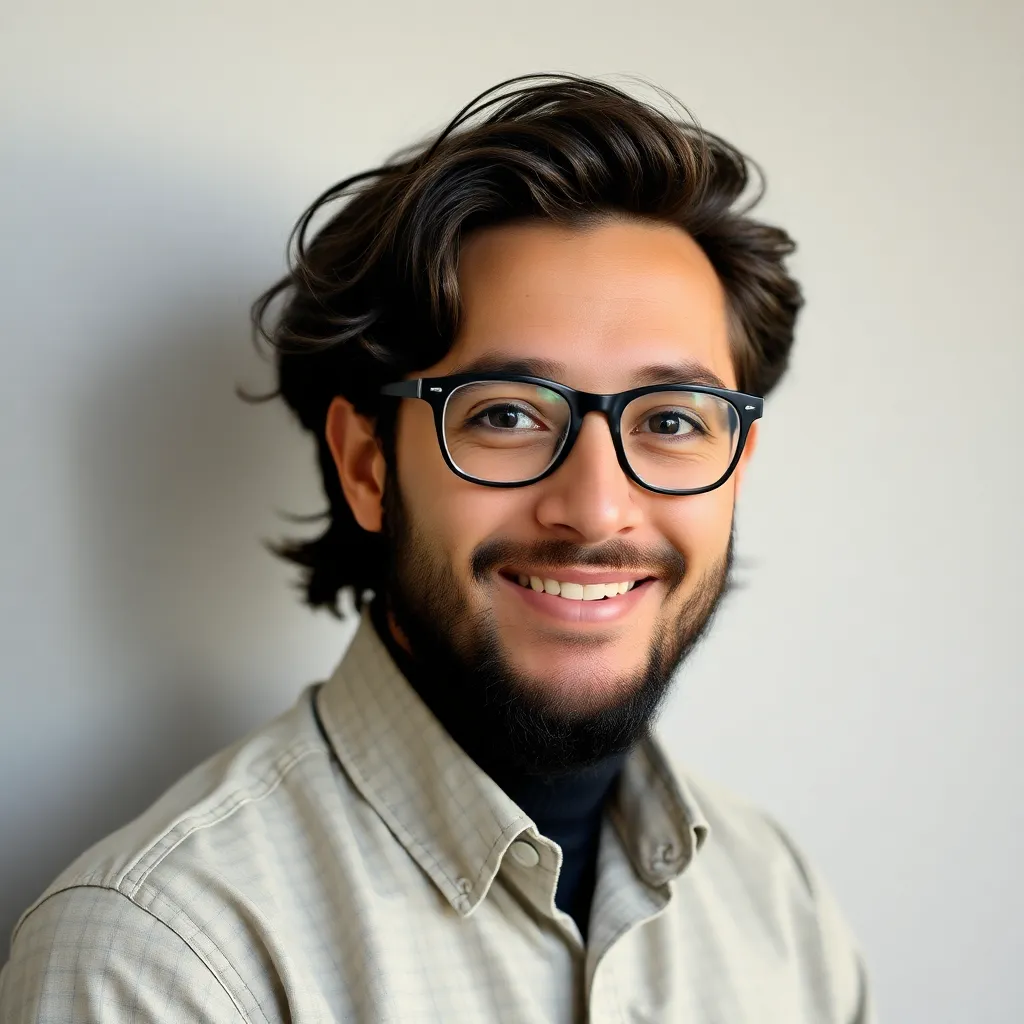
Breaking News Today
Apr 24, 2025 · 7 min read

Table of Contents
Employers' Duty to Provide Fall Protection: When, Where, and How
Falls are a leading cause of workplace fatalities and injuries, accounting for a significant portion of workplace accidents annually. This underscores the critical importance of fall protection in various industries. The question, "When is an employer obligated to provide fall protection?" isn't a simple one, as it depends on a complex interplay of factors, regulations, and risk assessments. This comprehensive guide delves into the intricacies of employer responsibilities regarding fall protection, examining the circumstances that necessitate its implementation, the specific regulations governing its use, and the best practices for ensuring worker safety.
Understanding the Employer's Duty
The fundamental principle underpinning an employer's responsibility for fall protection is the duty of care. Employers have a legal and moral obligation to provide a safe working environment for their employees, free from foreseeable hazards. This duty extends to proactively identifying and mitigating risks, including the risk of falls from heights. Failure to fulfill this duty can result in severe legal consequences, including fines, lawsuits, and even criminal charges.
The extent of an employer's duty is not static; it's dynamic and adapts based on the specific work environment, the nature of the task, and the potential for falls. Simply put, the higher the risk of a fall, the more stringent the employer's obligation to provide adequate fall protection.
When Fall Protection is Mandated: The Role of OSHA and Similar Regulations
In the United States, the Occupational Safety and Health Administration (OSHA) plays a crucial role in establishing and enforcing fall protection standards. OSHA's regulations aren't merely suggestions; they are legally binding requirements that employers must adhere to. These regulations are designed to minimize fall-related injuries and deaths. Similar regulatory bodies exist in other countries, each with its own specific guidelines and standards.
OSHA's 29 CFR 1926 Subpart M, "Fall Protection," outlines detailed requirements for fall protection in construction and other related industries. Key aspects include:
-
Fall Protection Plan: Employers must develop and implement a comprehensive fall protection plan tailored to the specific project or worksite. This plan should identify potential fall hazards, assess the risks, and detail the specific fall protection measures to be implemented. This plan needs to be regularly reviewed and updated.
-
Guardrails: Guardrails are a primary fall protection method. OSHA specifies the required height, strength, and spacing of guardrails to effectively prevent falls.
-
Safety Net Systems: In situations where guardrails are impractical or infeasible, safety net systems can be used. These systems must meet specific requirements regarding strength, installation, and inspection.
-
Personal Fall Arrest Systems (PFAS): PFAS, including harnesses, lanyards, and shock-absorbing lanyards, are critical for protecting workers from falls. Employers must ensure that PFAS are properly selected, inspected, and used according to manufacturer's instructions. Training is also paramount here.
-
Training: Employers are legally obligated to provide comprehensive fall protection training to all employees who work at heights. This training should cover hazard recognition, proper use of fall protection equipment, and emergency procedures. This training must be documented.
Determining the Need for Fall Protection: Risk Assessment is Key
The most crucial step in determining when fall protection is necessary is conducting a thorough risk assessment. This assessment should identify all potential fall hazards at the worksite, evaluate the likelihood of falls, and determine the severity of potential injuries.
Factors to consider during a risk assessment include:
-
Height: The higher the working height, the greater the risk of a fatal or serious injury from a fall. Even seemingly small heights can pose significant risks.
-
Surface Conditions: Uneven or slippery surfaces increase the likelihood of slips, trips, and falls.
-
Weather Conditions: Rain, snow, or ice can significantly increase the risk of falls.
-
Task Complexity: Complex or demanding tasks can distract workers and increase the risk of accidents.
-
Employee Experience and Training: Workers with limited experience or inadequate training are at a higher risk of falls.
-
Type of Work: Different work tasks present varying degrees of fall risk. For instance, roofing work inherently carries a higher risk than general office work.
Hierarchy of Fall Protection Controls
Once a risk assessment has identified potential fall hazards, employers should implement controls based on a hierarchy of controls, prioritizing the most effective and safest options:
-
Elimination: The most effective way to prevent falls is to eliminate the hazard altogether. This might involve redesigning the work process or using alternative methods that don't require working at heights.
-
Substitution: If elimination isn't feasible, substituting the hazardous task or equipment with a safer alternative is the next best option. This might involve using a scissor lift instead of a ladder.
-
Engineering Controls: Engineering controls are physical modifications to the work environment that reduce the risk of falls. Examples include installing guardrails, safety nets, or providing secure work platforms.
-
Administrative Controls: Administrative controls involve changing the way work is performed to minimize the risk of falls. This could include establishing work procedures, implementing safety rules, and providing additional supervision.
-
Personal Protective Equipment (PPE): PPE, such as fall arrest systems, should be the last line of defense, used only when other controls are not feasible or insufficient.
Specific Examples of When Fall Protection is Required
While a comprehensive risk assessment is paramount, there are certain scenarios where the need for fall protection is virtually guaranteed by OSHA and similar regulations:
-
Working at heights of 6 feet or more: This is a general guideline, and the specific threshold might vary depending on the work environment and the type of task. However, in many situations, any elevation above 6 feet mandates fall protection.
-
Roofing work: Roofing is inherently dangerous due to the height and the nature of the work. Fall protection is mandatory for almost all roofing activities.
-
Construction work: Numerous construction activities require working at heights, including erecting scaffolding, installing windows, and working on high-rise buildings. Fall protection is essential in all these situations.
-
Working on scaffolds: Scaffolds, even if relatively low to the ground, must be equipped with appropriate fall protection measures, typically guardrails and toe boards.
-
Working near open-sided floors or platforms: Any work near open-sided floors or platforms necessitates adequate fall protection to prevent workers from falling.
-
Working on ladders: While ladders might seem straightforward, certain ladder heights and tasks demand additional fall protection, especially when working above a certain height.
-
Working in excavations: Workers in excavations are at risk of falling into the excavation itself. Proper shoring and other fall protection measures are crucial in this context.
Beyond the Legal Requirements: Proactive Fall Protection
While legal compliance is essential, a truly effective fall protection program goes beyond simply meeting the minimum regulatory requirements. A proactive approach emphasizes a safety culture that prioritizes the prevention of falls before they occur. This includes:
-
Regular inspections: Regular inspections of fall protection equipment, work areas, and fall protection systems are critical. Damaged or worn-out equipment must be immediately replaced.
-
Employee training and communication: Ongoing training and communication are crucial to ensure that employees understand the risks of falls and know how to use fall protection equipment correctly.
-
Emergency response planning: Having a comprehensive emergency response plan in place, including rescue procedures, is crucial in case of a fall.
-
Leading indicators: Monitoring leading indicators, such as near misses and unsafe acts, can help identify potential fall hazards before they result in accidents.
Conclusion: A Culture of Safety
Employers' duty to provide fall protection is not simply a legal obligation; it's a fundamental responsibility rooted in a commitment to worker safety and well-being. By conducting thorough risk assessments, implementing appropriate fall protection measures based on the hierarchy of controls, and fostering a robust safety culture, employers can significantly reduce the risk of falls and create a safer work environment for their employees. Remember that proactive measures, continuous training, and regular inspections are key to ensuring a workplace free from fall-related incidents. The cost of neglecting fall protection far outweighs the investment in implementing robust safety measures. Prioritizing fall protection is not just a legal requirement; it's a moral imperative.
Latest Posts
Latest Posts
-
How Do The Moral Dilemmas Of Volumnius And Strato Compare
Apr 24, 2025
-
Transfer Of Greco Islamic Knowledge To Western Europe
Apr 24, 2025
-
Business Owners Generally Paid Low Wages In Factories Because
Apr 24, 2025
-
These Organize Commonly Used Commands Into Sets Of Related Activities
Apr 24, 2025
-
Which Of These Statements Regarding The Annuitant Is Correct
Apr 24, 2025
Related Post
Thank you for visiting our website which covers about Employers Duty To Have Fall Protection Is When . We hope the information provided has been useful to you. Feel free to contact us if you have any questions or need further assistance. See you next time and don't miss to bookmark.