For Safety's Sake Industrial Screwdriver Blades Are Made Of
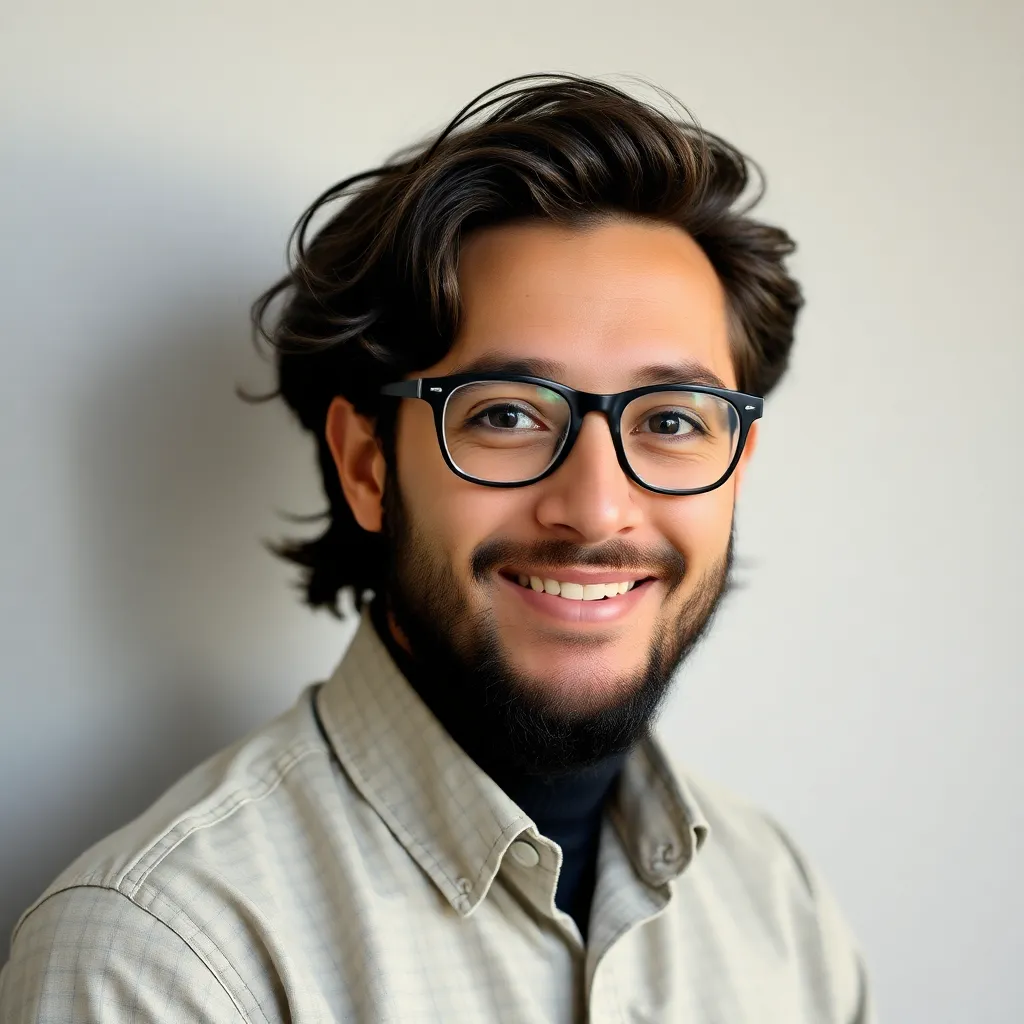
Breaking News Today
Mar 27, 2025 · 5 min read

Table of Contents
For Safety's Sake: The Materials Science Behind Industrial Screwdriver Blades
Industrial screwdrivers face significantly harsher conditions than their household counterparts. They're subjected to higher torque, repeated use, potentially corrosive environments, and the risk of accidental damage. Therefore, the materials used in their construction are critical to ensuring both the tool's longevity and, most importantly, the safety of the user. Let's delve into the science behind the materials chosen for industrial screwdriver blades and explore why they're selected for maximum safety and performance.
The Crucial Role of Material Properties
The selection of a material for industrial screwdriver blades isn't arbitrary. It's a careful balancing act, prioritizing several key properties:
1. High Tensile Strength: Withstanding the Pressure
Tensile strength refers to a material's ability to resist being pulled apart. Industrial screwdrivers often handle significant torque, especially when dealing with stubborn screws or large-scale assembly. A high tensile strength ensures the blade won't snap or fracture under pressure, preventing injuries from flying debris. Materials like high-carbon steel and certain alloy steels excel in this area.
2. High Yield Strength: Preventing Deformation
Yield strength indicates the point at which a material begins to deform permanently. A high yield strength is crucial to prevent the blade from bending or warping during use. This maintains the accuracy of the screwdriver's fit within the screw head, avoiding cam-out (the slipping of the blade) and potential damage to both the screw and the workpiece.
3. Impact Resistance: Surviving Accidental Drops and Impacts
Industrial environments can be unforgiving. Screwdrivers might be dropped, struck, or subjected to unexpected impacts. Impact resistance is vital to prevent chipping, cracking, or breakage of the blade. Certain alloy steels, along with carefully heat-treated high-carbon steels, are engineered for enhanced impact resistance.
4. Hardness: Resistance to Wear and Tear
Hardness is a measure of a material's resistance to scratching, abrasion, and indentation. Repeated use on hard screws, especially in repetitive assembly lines, can lead to wear and tear on the blade's tip. A hard blade maintains its sharpness and precision for a longer time, improving efficiency and reducing the risk of slipping. This is usually achieved through heat treatment processes.
5. Fatigue Resistance: Withstanding Repeated Stress
Industrial screwdrivers often experience fatigue, a gradual weakening of the material due to repeated stress cycles. A high fatigue resistance is essential to prevent sudden failure after prolonged use. The microstructure of the material, controlled by heat treatment and alloying, significantly influences fatigue resistance.
6. Corrosion Resistance: Maintaining Integrity in Harsh Environments
Some industrial settings involve corrosive substances like chemicals or moisture. Corrosion resistance is crucial to ensure the blade remains functional and safe, preventing weakening or degradation of the material. Stainless steels, often containing chromium and nickel, are popular choices for their excellent corrosion resistance.
Common Materials Used in Industrial Screwdriver Blades
Several materials are frequently used in the manufacturing of industrial screwdriver blades, each offering a specific combination of the properties discussed above.
1. High-Carbon Steel: A Workhorse Material
High-carbon steel is a widely used material due to its excellent balance of strength, hardness, and toughness. The higher carbon content increases hardness and tensile strength, making it suitable for high-torque applications. However, its corrosion resistance is relatively low, limiting its use in corrosive environments. Heat treatment plays a crucial role in tailoring the final properties of high-carbon steel blades.
2. Alloy Steels: Tailoring Properties for Specific Needs
Alloy steels contain additional elements like chromium, molybdenum, vanadium, or manganese to enhance specific properties. These additions can improve hardness, toughness, impact resistance, and corrosion resistance, making them suitable for a wide range of industrial applications. Specific alloy compositions are chosen based on the intended use of the screwdriver and the environment it will operate in. For example, chromium additions enhance corrosion resistance, while vanadium and molybdenum improve strength and toughness.
3. Stainless Steel: The Corrosion-Resistant Champion
Stainless steels, primarily those containing chromium and nickel, offer superior corrosion resistance. Their ability to withstand corrosive environments makes them the preferred choice for industrial applications involving chemicals, moisture, or outdoor exposure. However, stainless steels might not possess the same level of hardness and tensile strength as high-carbon or some alloy steels. Different grades of stainless steel (e.g., 304, 316) offer varied combinations of properties.
The Importance of Heat Treatment
The properties of the screwdriver blade material are further enhanced by heat treatment processes. These processes involve carefully controlled heating and cooling cycles to alter the material's microstructure, leading to increased hardness, strength, and other desirable properties. Common heat treatments include:
- Annealing: Reduces internal stresses and increases ductility (ability to deform without breaking).
- Hardening: Increases hardness and strength through rapid cooling from high temperatures.
- Tempering: Reduces brittleness and improves toughness after hardening.
Beyond the Blade: The Entire Screwdriver Design
While the blade material is paramount, the overall design of the industrial screwdriver also contributes significantly to safety:
- Ergonomic Handles: Comfortable, slip-resistant handles reduce the risk of hand fatigue and accidental drops.
- Reinforced Shanks: Strong shanks connect the blade to the handle, preventing bending or breakage under stress.
- Safety Features: Some industrial screwdrivers incorporate features like magnetic tips, which improve grip on the screw and reduce the chance of cam-out, thereby enhancing safety.
Conclusion: A Multifaceted Approach to Safety
The safety of industrial screwdrivers is a result of a carefully considered combination of material science, manufacturing processes, and design engineering. The choice of blade material – whether high-carbon steel, alloy steel, or stainless steel – is a crucial aspect, with each material offering a unique set of properties tailored to specific needs. Heat treatments further refine these properties, enhancing strength, hardness, and durability. Finally, a well-designed screwdriver, including ergonomic handles and robust construction, contributes significantly to ensuring the tool's safe and efficient operation. Understanding the science behind these materials and processes highlights the commitment to worker safety embedded in the design and manufacturing of industrial screwdrivers. The focus isn't simply on functionality; it's on preventing accidents and protecting those who use these tools every day.
Latest Posts
Latest Posts
-
Which Statement Is True Regarding Primary Dysmenorrhea Select All
Mar 30, 2025
-
The Massage Therapy Center Maintains A Database
Mar 30, 2025
-
The Government Engages In An Industrial Policy
Mar 30, 2025
-
Discuss The Interdependence Of The Components Of Wellness
Mar 30, 2025
-
Which Statement Is Not True About Receipts
Mar 30, 2025
Related Post
Thank you for visiting our website which covers about For Safety's Sake Industrial Screwdriver Blades Are Made Of . We hope the information provided has been useful to you. Feel free to contact us if you have any questions or need further assistance. See you next time and don't miss to bookmark.