Four Critical Questions To Consider When Shutting Down Equipment
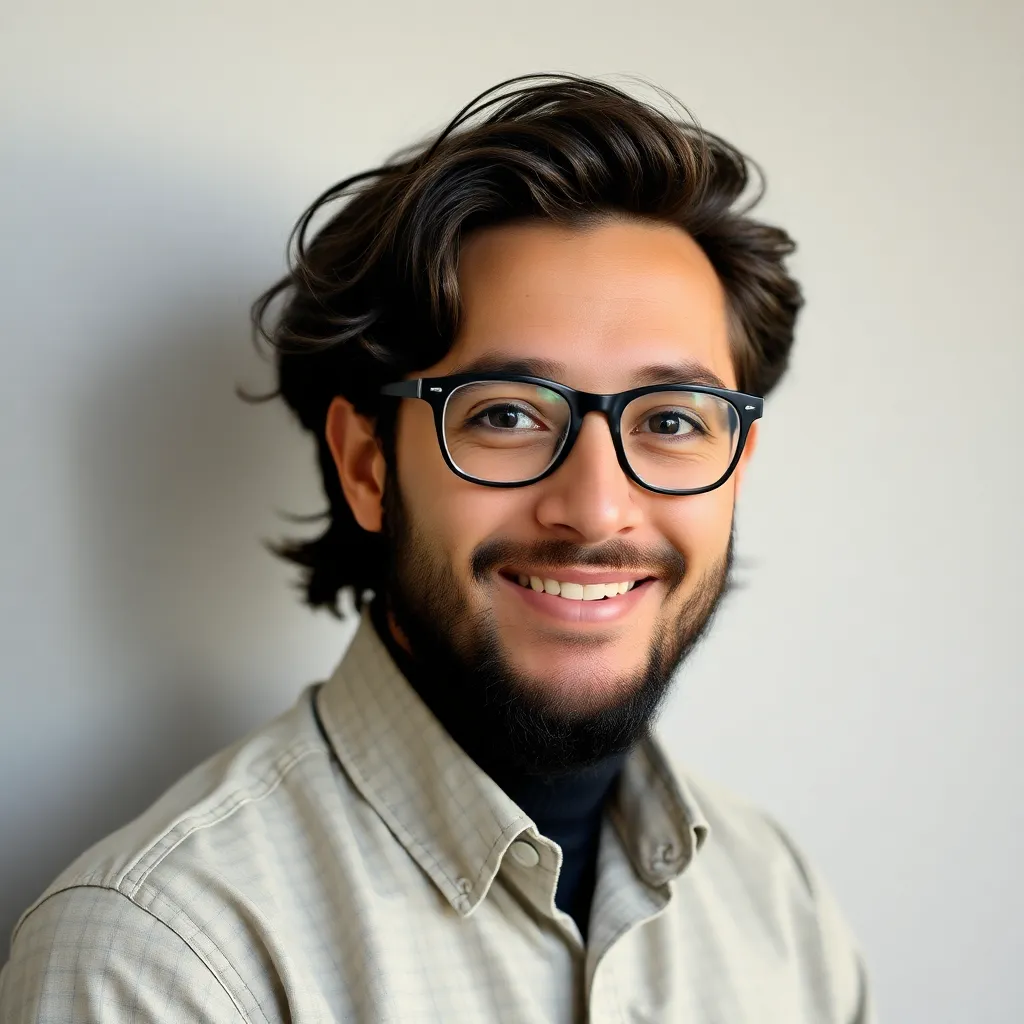
Breaking News Today
Apr 06, 2025 · 6 min read

Table of Contents
Four Critical Questions to Consider When Shutting Down Equipment
Shutting down equipment might seem straightforward, a simple flick of a switch or a press of a button. However, for many pieces of equipment, especially industrial machinery, complex systems, and critical infrastructure, a hasty shutdown can lead to costly repairs, safety hazards, data loss, and even environmental damage. Therefore, a structured and methodical approach is paramount. Before you even think about powering down, four critical questions must be considered:
1. What are the safety implications of shutting down this equipment?
This is arguably the most crucial question. Ignoring safety protocols can result in serious injury or even death. The answer will vary wildly depending on the type of equipment. Consider these factors:
Identifying Potential Hazards
-
Stored Energy: Many machines retain energy even after being switched off. This could be in the form of:
- Mechanical energy: Compressed springs, hydraulic pressure, rotating parts with inertia. Unexpected release of this energy can cause serious harm.
- Electrical energy: Capacitors can store a lethal charge even after disconnection from the power supply.
- Thermal energy: Overheated components, such as motors or furnaces, can cause burns.
-
Hazardous Materials: Some equipment uses or produces hazardous materials like chemicals, flammable liquids, or radioactive substances. Shutting down improperly could lead to spills, leaks, or uncontrolled reactions. Proper procedures must be followed to ensure safe containment and disposal.
-
Entrapment Hazards: Moving parts, confined spaces, and other elements might pose risks during the shutdown process. Ensure that all personnel are clear of dangerous areas before commencing shutdown.
-
Environmental Concerns: Certain processes generate emissions or waste. Sudden shutdown might lead to uncontrolled releases into the environment. A planned shutdown allows for mitigation strategies.
Developing Safe Shutdown Procedures
Safety protocols should be clearly defined and documented. They should include:
-
Lockout/Tagout (LOTO) Procedures: This essential safety procedure ensures that energy sources are isolated and equipment cannot be accidentally restarted during maintenance or shutdown. Every step should be documented and verified.
-
Emergency Shutdown Procedures: Define clear steps to be taken in case of unexpected events during shutdown. This includes identifying emergency stops, contacting relevant personnel, and evacuating the area if necessary.
-
Personal Protective Equipment (PPE): Identify the appropriate PPE necessary for the safe execution of the shutdown process, including gloves, eye protection, and hearing protection.
Example: Shutting down a large industrial press requires a meticulous LOTO procedure, ensuring the hydraulic system is depressurized, and all moving parts are brought to a complete standstill before anyone approaches the equipment. Failure to do so could result in serious injury.
2. What are the operational implications of shutting down this equipment?
Beyond safety, consider the impact of the shutdown on your operations. This often involves evaluating downstream effects and potential disruptions.
Assessing Downstream Impacts
-
Production Downtime: How long will the shutdown take? What is the cost of production downtime? Are there alternative systems or processes that can be employed to minimize disruption?
-
Product Loss or Damage: Will the shutdown lead to spoilage of materials or products in process? Are there procedures to salvage or protect these assets?
-
Service Interruptions: Does the equipment provide a critical service to customers or internal departments? How will the shutdown affect their operations?
-
Data Loss: If the equipment handles data, what measures are in place to prevent loss or corruption during shutdown? This may include backups, data migration, or system flushing procedures.
Planning for a Smooth Transition
Minimizing disruption often involves careful planning and coordination:
-
Scheduled Maintenance: If possible, schedule the shutdown during periods of low demand or during planned maintenance windows.
-
Phased Shutdown: Break down the shutdown process into smaller, manageable stages to allow for monitoring and adjustments.
-
Communication: Communicate clearly with relevant personnel about the shutdown plan, including timelines, potential impacts, and contingency plans.
-
Post-Shutdown Procedures: Define clear procedures for restarting the equipment and verifying its proper functionality after shutdown.
Example: Shutting down a data center requires careful planning to minimize downtime. This may involve a staged shutdown of servers, ensuring data backups are complete, and having a dedicated team monitoring the process.
3. What are the environmental considerations related to equipment shutdown?
Environmental regulations and sustainability are increasingly important factors. Consider the potential impact of your shutdown on the environment.
Minimizing Environmental Impact
-
Waste Generation: Does the shutdown generate any waste? How will this waste be handled and disposed of? Compliance with environmental regulations is crucial.
-
Emissions: Does the equipment release emissions into the air or water? Are there procedures to minimize emissions during shutdown?
-
Energy Consumption: Even during shutdown, some equipment might continue to consume energy. Identify ways to reduce energy usage.
-
Spill Prevention: If the equipment handles liquids, are there precautions to prevent accidental spills during the shutdown process?
Implementing Environmentally Sound Practices
-
Waste Minimization: Implement strategies to reduce waste generation, such as recycling and proper disposal methods.
-
Emission Control: Utilize appropriate emission control technologies to limit environmental impact.
-
Energy Efficiency: Optimize energy consumption during shutdown through efficient shutdown procedures and equipment design.
-
Compliance Monitoring: Ensure compliance with all relevant environmental regulations and permits.
Example: Shutting down a chemical plant requires careful consideration of potential chemical spills and air emissions. Emergency response plans and environmental monitoring must be in place.
4. What is the cost-effectiveness of this shutdown procedure?
While safety is paramount, it's vital to also evaluate the cost-effectiveness of the chosen shutdown procedure. A poorly planned shutdown can result in significant financial losses.
Analyzing Costs
-
Downtime Costs: Calculate the cost of lost production or service during the shutdown period.
-
Maintenance Costs: Consider the cost of repairs, replacement parts, and labor required during the shutdown.
-
Disposal Costs: Factor in the cost of disposing of any waste generated during the shutdown.
-
Environmental Remediation Costs: Account for the potential costs of addressing any environmental damage.
Optimizing Cost-Effectiveness
-
Preventive Maintenance: Regular preventive maintenance can help reduce the frequency and duration of shutdowns, saving money in the long run.
-
Efficient Shutdown Procedures: Well-defined and efficient procedures minimize downtime and reduce the risk of errors.
-
Proper Training: Investing in training for personnel ensures that shutdowns are performed correctly, reducing the risk of accidents and costly repairs.
-
Technology Integration: Utilizing advanced technologies such as predictive maintenance systems can help optimize shutdown schedules and minimize downtime.
Example: A poorly executed shutdown of a manufacturing line might result in significant downtime, damage to equipment, and wasted materials, far exceeding the cost of implementing a more structured and thorough shutdown procedure.
Conclusion:
Shutting down equipment is more than just turning off a switch. By systematically considering these four critical questions – safety, operational implications, environmental concerns, and cost-effectiveness – you can develop a shutdown procedure that minimizes risk, maximizes efficiency, and protects your bottom line. A proactive and well-planned approach ensures a smooth and safe transition, protecting personnel, the environment, and your organization's financial stability. Remember, thorough documentation and regular reviews of your shutdown procedures are crucial to maintaining safety and efficiency. This will ensure that your procedures remain current and effective in protecting your equipment and personnel.
Latest Posts
Latest Posts
-
Venezuelans Started Buying Items Immediately Because Of Their Fear Of
Apr 08, 2025
-
Which Nims Management Characteristic Involves Using Standardized Names
Apr 08, 2025
-
How Can A Server Determine If A Guest Is 21
Apr 08, 2025
-
Which Of The Following Examples Illustrates Allyship
Apr 08, 2025
-
Select All True Statements About Whisk Fern Sporophytes
Apr 08, 2025
Related Post
Thank you for visiting our website which covers about Four Critical Questions To Consider When Shutting Down Equipment . We hope the information provided has been useful to you. Feel free to contact us if you have any questions or need further assistance. See you next time and don't miss to bookmark.