How Should Tubular Wire Wound Resistors Be Mounted And Why
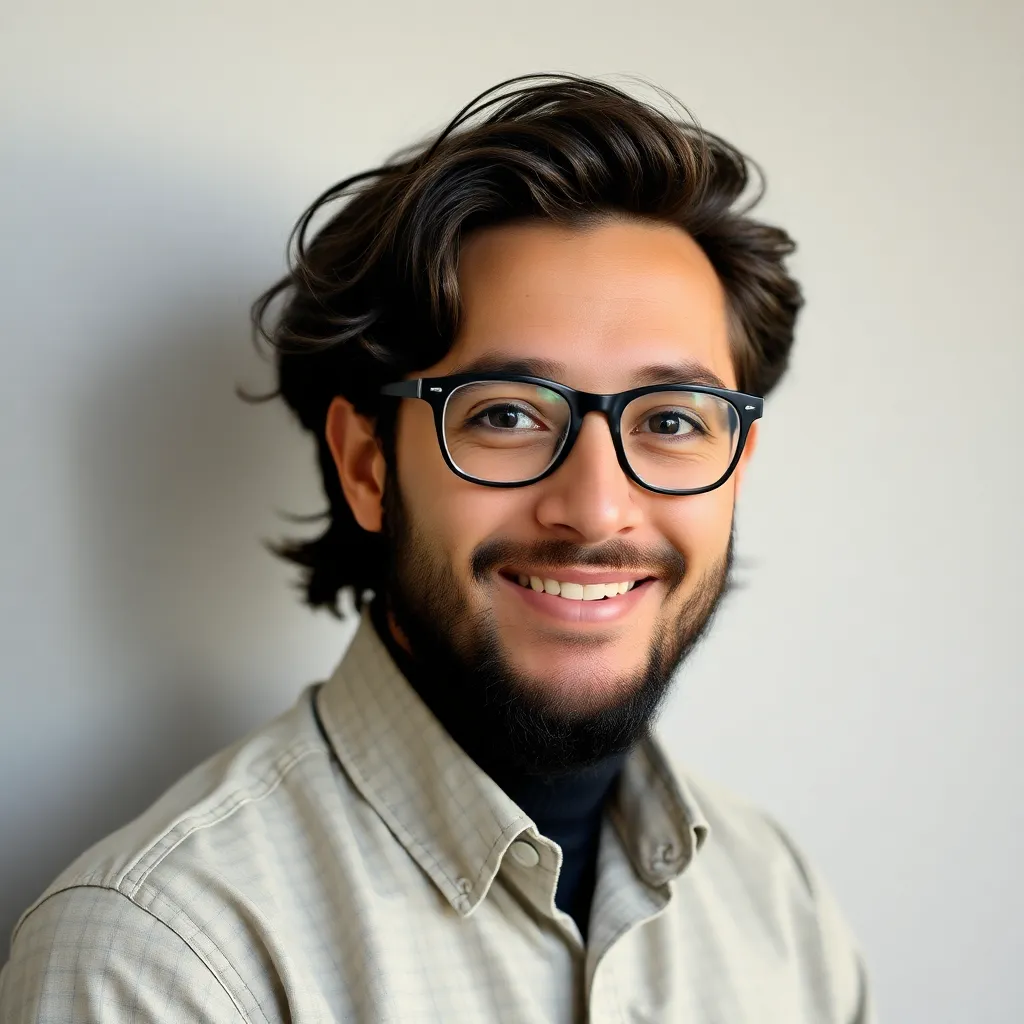
Breaking News Today
May 11, 2025 · 6 min read

Table of Contents
How Should Tubular Wire Wound Resistors Be Mounted and Why?
Tubular wire wound resistors, known for their high power handling capabilities and precision, require careful mounting to ensure optimal performance and longevity. Improper mounting can lead to overheating, failure, and even safety hazards. This comprehensive guide explores the best practices for mounting these resistors, explaining the underlying reasons behind each recommendation. Understanding these principles is crucial for engineers, hobbyists, and anyone working with high-power electronic circuits.
Understanding Tubular Wire Wound Resistors
Before delving into mounting techniques, let's briefly review the characteristics of tubular wire wound resistors. These resistors are constructed by winding a resistive wire around a ceramic core, often encased in a protective, often ceramic, outer shell. This construction contributes to their ability to dissipate significant amounts of heat, making them ideal for applications where high power dissipation is necessary. However, this same heat generation necessitates careful consideration during mounting.
Key Characteristics Affecting Mounting:
- Heat Dissipation: The primary concern when mounting these resistors is their heat dissipation capability. The resistor's ability to shed heat efficiently directly impacts its operating temperature and lifespan.
- Physical Size and Weight: Larger resistors dissipate heat more effectively but also demand more mounting space. The weight of the resistor needs to be considered to prevent stress on the mounting hardware.
- Lead Wire Material and Strength: The lead wires, usually made of nickel or similar material, can be fragile and must be handled carefully during the mounting process to avoid damage. Improper bending can lead to fractures and eventual failure.
- Operating Temperature Range: Exceeding the resistor's maximum operating temperature can severely shorten its lifespan and even cause catastrophic failure. The mounting method must ensure the resistor stays within its specified temperature range.
Mounting Techniques: Best Practices
Proper mounting of tubular wire wound resistors involves several key considerations. These methods aim to maximize heat dissipation, minimize stress on the component, and ensure reliable electrical connections.
1. Utilizing Adequate Mounting Space and Airflow:
Why it matters: Sufficient spacing is paramount for effective heat dissipation. Crowding resistors restricts airflow, leading to higher operating temperatures and potential overheating.
How to do it: Allow ample clearance around the resistor, ensuring at least twice the diameter of the resistor on all sides. Consider the use of heat sinks for high-power applications to further enhance heat transfer to the surrounding environment. Ensure good airflow around the heat sink and resistor by using fans or positioning the components in well-ventilated areas of the circuit board.
2. Using Suitable Mounting Hardware:
Why it matters: The chosen mounting method significantly impacts heat dissipation and stress on the resistor.
How to do it: Avoid clamping the resistor directly, as this can introduce stress and impede heat transfer. Instead, use techniques like stand-offs or insulated mounting brackets that provide support without restricting airflow. For heavier resistors, consider using stronger mounting hardware to prevent the resistor from sagging or falling.
3. Secure Lead Wire Connections:
Why it matters: Loose connections can lead to increased resistance, overheating at the connection point, and eventual failure.
How to do it: Use appropriate soldering techniques to ensure strong, reliable connections. Avoid excessive heat during soldering to prevent damage to the resistor or its lead wires. Consider using heat sinks on the lead wires during soldering to prevent heat damage. Crimping or other specialized mechanical terminations may be necessary for particularly high current applications.
4. Applying Thermal Compound (Where Appropriate):
Why it matters: Thermal compounds improve heat transfer between the resistor and a heat sink. This is especially critical in high-power applications.
How to do it: Apply a thin, even layer of thermal compound between the resistor and the heat sink, ensuring complete contact between the two surfaces. Avoid using excessive amounts of thermal compound, as this can hinder heat transfer. Consider using thermal pads for easier application and better heat transfer.
5. Orientation for Optimal Heat Dissipation:
Why it matters: Resistors should be oriented to maximize convective heat transfer.
How to do it: Position the resistor so that the maximum surface area is exposed to air. Avoid placing resistors in enclosed areas or on surfaces that impede airflow.
6. Considering the Resistor's Wattage Rating:
Why it matters: The wattage rating of the resistor indicates its maximum power dissipation capability.
How to do it: Always select a resistor with a wattage rating that comfortably exceeds the expected power dissipation in the circuit. Overloading a resistor will inevitably lead to overheating and failure. Selecting a resistor with a higher power rating allows for better heat dissipation margins and longer life. This may require different mounting techniques due to the larger size and heat output.
7. Avoiding Stress on the Resistor Body:
Why it matters: Excessive stress on the resistor body can cause cracks in the ceramic core, compromising its structural integrity and leading to failure.
How to do it: Avoid bending or twisting the resistor during mounting. Use gentle pressure when fastening the mounting hardware. Always support the resistor's weight properly.
Choosing the Right Mounting Method: Case Studies
The optimal mounting method depends heavily on the specific application and the resistor's characteristics. Let's consider a few examples to illustrate this point.
Case Study 1: High-Power Amplifier
In a high-power audio amplifier, large wire wound resistors are often used to handle significant power dissipation. Here, a heat sink is absolutely essential. The resistor should be mounted securely to the heat sink using thermal compound, and the heat sink itself should be adequately ventilated. The larger size of the resistor and the higher power output would necessitate robust mounting hardware and potentially the use of additional cooling such as fans.
Case Study 2: Low-Power Control Circuit
In a low-power control circuit, the power dissipation is minimal. A simple surface mount or through-hole mounting method might suffice. While airflow is still beneficial, the requirement for extensive heat sinking or other complex mounting techniques may be unnecessary. Nevertheless, proper soldering techniques are still paramount to maintain a reliable connection.
Case Study 3: High-Frequency Application
High-frequency applications can introduce additional considerations. The lead lengths should be kept as short as possible to minimize parasitic inductance and capacitance. This might influence mounting choices, potentially favouring surface-mount components or specialized techniques to minimize lead length and maintain signal integrity.
Troubleshooting Common Mounting Issues
Improper mounting can lead to a variety of problems. Recognizing and addressing these issues is crucial for ensuring reliable circuit operation.
- Overheating: If the resistor feels excessively hot, it's a clear sign of overheating. This could be due to insufficient mounting space, inadequate airflow, insufficient wattage rating, or poor heat dissipation.
- Loose Connections: Intermittent operation or increased resistance usually indicates loose connections. Resoldering or replacing the connections is typically necessary.
- Physical Damage: Cracks or other physical damage to the resistor indicate stress during mounting. Replace the damaged resistor and review the mounting technique to prevent recurrence.
Conclusion: The Importance of Proper Mounting
Proper mounting of tubular wire wound resistors is crucial for ensuring reliable circuit operation and maximizing the lifespan of these components. By following the guidelines outlined in this guide and carefully considering the specific requirements of each application, you can avoid common mounting issues and maintain the integrity of your electronic designs. Remember, investing time in proper mounting techniques translates to enhanced circuit reliability, longer component life, and ultimately, a more robust and efficient system. The seemingly small detail of resistor mounting can significantly influence the overall success and reliability of the entire project.
Latest Posts
Related Post
Thank you for visiting our website which covers about How Should Tubular Wire Wound Resistors Be Mounted And Why . We hope the information provided has been useful to you. Feel free to contact us if you have any questions or need further assistance. See you next time and don't miss to bookmark.