In Airline Applications Failure Of A Component
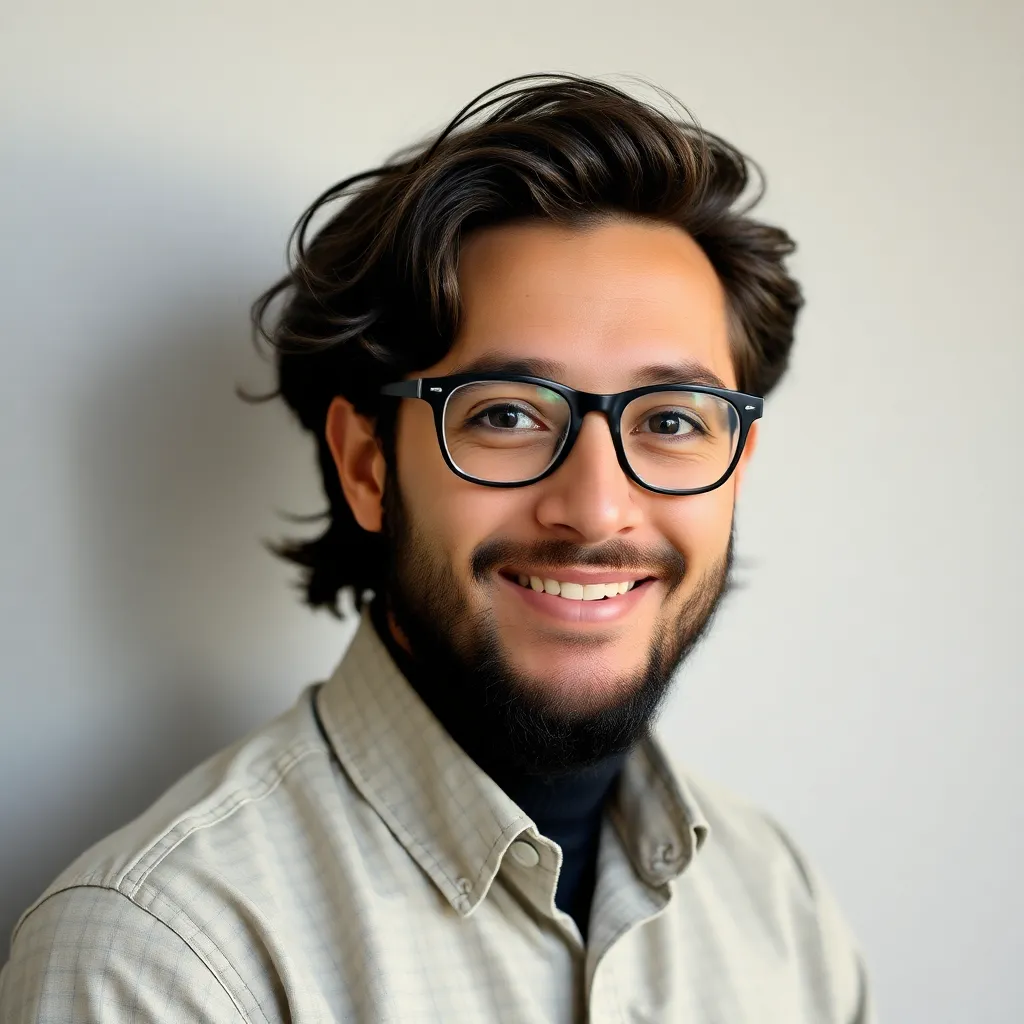
Breaking News Today
May 09, 2025 · 6 min read
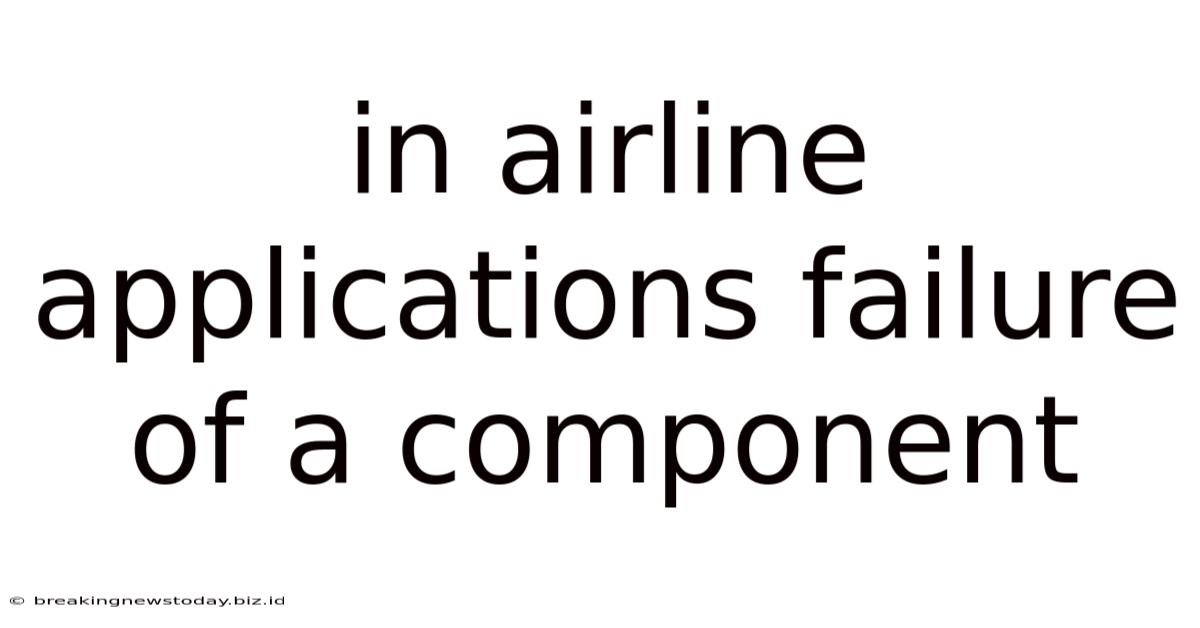
Table of Contents
In Airline Applications: The Failure of a Component – A Deep Dive into Causes, Consequences, and Mitigation
The aviation industry demands unparalleled reliability. A single component failure can have cascading effects, leading to delays, cancellations, diversions, and, in the worst-case scenario, catastrophic accidents. Understanding the causes, consequences, and mitigation strategies surrounding component failures in airline applications is crucial for ensuring passenger safety and operational efficiency. This comprehensive article delves into this critical area, exploring various aspects of component failure within the complex ecosystem of modern air travel.
Understanding the Landscape of Aircraft Component Failures
Aircraft are incredibly complex machines, comprising thousands of individual parts, each playing a vital role in the overall functionality and safety of the aircraft. These components range from small, seemingly insignificant fasteners to large, sophisticated engines and flight control systems. Failures can occur in any of these components, and the consequences can vary drastically depending on the criticality of the failed part and the operational context.
Categorizing Component Failures:
We can categorize component failures based on several factors:
-
Mechanism of Failure: This describes how the component failed. Examples include fatigue failure (due to repeated stress), corrosion (chemical degradation), wear and tear (due to friction or use), manufacturing defects (errors during production), and sudden catastrophic failure (unpredictable events).
-
Severity of Failure: This indicates the impact of the failure on aircraft safety and operation. Failures can range from minor inconveniences (e.g., a malfunctioning in-flight entertainment system) to critical failures that could jeopardize flight safety (e.g., engine failure, hydraulic system failure).
-
Component Type: The type of component plays a crucial role in determining the potential consequences of failure. Engine failures, for instance, are far more critical than failures in the cabin lighting system. Other critical systems include flight control systems, landing gear, and braking systems.
-
Operational Context: The conditions under which the failure occurs (e.g., during takeoff, cruise flight, landing) significantly influence the severity of the consequences. A landing gear failure during landing is far more critical than during cruise.
Common Causes of Component Failure in Airline Applications
Numerous factors contribute to component failures in aircraft. Understanding these causes is essential for developing effective preventative measures.
1. Material Degradation:
-
Fatigue: Repeated stress cycles can lead to microscopic cracks that propagate over time, eventually causing component failure. This is a particularly significant concern for highly stressed components like airframe structures, engine parts, and landing gear. Regular inspections and non-destructive testing are crucial for detecting fatigue cracks before they lead to failure.
-
Corrosion: Exposure to environmental factors like moisture, salt spray, and chemicals can cause corrosion, weakening the component's structural integrity. Corrosion protection methods, such as coatings and anti-corrosion treatments, are vital in mitigating this risk. Regular inspections and maintenance are crucial for early detection.
-
Creep: This is a slow, time-dependent deformation of materials under constant stress at high temperatures. It is a significant concern for engine components operating at elevated temperatures.
2. Manufacturing Defects:
Defects introduced during the manufacturing process can significantly reduce the component's lifespan and increase the risk of failure. These defects can range from subtle imperfections in material properties to more significant errors in assembly or design. Rigorous quality control procedures are crucial for detecting and eliminating manufacturing defects.
3. Design Flaws:
Design flaws can manifest as weaknesses in the component's structure or functionality. These flaws can only be identified through thorough analysis and testing during the design and development phase. Continuous monitoring and feedback after deployment are crucial for identifying and addressing unforeseen issues.
4. Operational Factors:
-
Improper Maintenance: Inadequate or incorrect maintenance can accelerate component degradation and increase the likelihood of failure. Following strict maintenance procedures and using certified technicians is paramount.
-
Environmental Conditions: Extreme temperatures, humidity, and other environmental factors can negatively impact component performance and lifespan. Operating aircraft in harsh environments necessitates careful consideration of potential environmental effects.
-
Pilot Error: While less frequent, pilot error can sometimes contribute to component failure, particularly through mishandling of aircraft systems or exceeding operational limits.
5. External Factors:
-
Bird Strikes: Collisions with birds can cause significant damage to critical aircraft components, including engines and windshields.
-
Hail and Ice: Exposure to hail and ice during flight can damage airframe structures and affect aerodynamic performance.
-
Lightning Strikes: Lightning strikes can cause damage to electrical systems and other sensitive components.
Consequences of Component Failure
The consequences of component failure in airline applications can range from minor inconveniences to catastrophic accidents.
1. Operational Disruptions:
Component failures frequently lead to delays, cancellations, and diversions. These disruptions cause significant financial losses for airlines and inconvenience to passengers. The severity of the disruption depends on the criticality of the failed component and the location of the aircraft.
2. Safety Risks:
Critical component failures can pose significant safety risks, potentially leading to accidents and fatalities. The failure of critical systems, like flight control systems or engines, can have catastrophic consequences. Redundancy and fail-safe mechanisms are crucial for mitigating these risks.
3. Economic Impact:
The economic consequences of component failures can be substantial. This includes direct costs associated with repairs, replacements, and investigation, as well as indirect costs due to operational disruptions, lost revenue, and legal liabilities.
4. Reputation Damage:
Component failures can damage an airline's reputation, leading to decreased passenger confidence and potential loss of market share.
Mitigation Strategies:
Preventing component failures is a continuous process that involves multiple layers of defense.
1. Design and Manufacturing:
-
Robust Design: Components should be designed with sufficient safety margins to withstand expected stresses and environmental conditions. This involves meticulous analysis, simulation, and rigorous testing.
-
Material Selection: Selecting materials with high strength, durability, and resistance to corrosion and fatigue is paramount.
-
Quality Control: Rigorous quality control procedures during manufacturing are crucial for detecting and eliminating defects.
2. Maintenance and Inspection:
-
Preventative Maintenance: Regular inspections and maintenance are crucial for detecting potential problems before they lead to failures. This includes visual inspections, non-destructive testing, and performance monitoring.
-
Predictive Maintenance: Advanced technologies like sensors and data analytics can be used to predict potential failures and schedule maintenance proactively.
-
Component Replacement: Implementing a schedule for replacing components at predetermined intervals, based on their expected lifespan, can prevent failures.
3. Operational Procedures:
-
Pilot Training: Pilots should receive comprehensive training on how to handle various component failures and emergencies.
-
Flight Operations Monitoring: Continuous monitoring of flight parameters and operational data can help identify potential problems and prevent accidents.
4. Redundancy and Fail-Safe Mechanisms:
-
Redundant Systems: Critically important systems are often designed with redundancy, allowing the aircraft to continue operating safely even if one component fails.
-
Fail-Safe Mechanisms: Mechanisms are built into the system to prevent catastrophic failure even if a component malfunctions. This ensures that the failure is contained and does not propagate to other systems.
Conclusion:
Component failures in airline applications are a complex issue with significant safety and economic implications. A multi-layered approach involving robust design, rigorous maintenance, advanced technologies, and comprehensive operational procedures is necessary to mitigate the risk of failures and ensure the continued safety and efficiency of air travel. Continuous research, development, and technological advancements are crucial in improving the reliability and safety of aircraft components. The commitment to safety remains paramount throughout the lifecycle of every component, from design to disposal, ensuring the safe and reliable transportation of millions of passengers worldwide.
Latest Posts
Latest Posts
-
Just In Time Delivery Ap Human Geography
May 09, 2025
-
What Is The Ultimate Source Of Energy
May 09, 2025
-
If An Appellate Court Affirms A Case It Means
May 09, 2025
-
When Command Is Transferred The Process Should Include An
May 09, 2025
-
In Ems What Does Mental Status Refer To
May 09, 2025
Related Post
Thank you for visiting our website which covers about In Airline Applications Failure Of A Component . We hope the information provided has been useful to you. Feel free to contact us if you have any questions or need further assistance. See you next time and don't miss to bookmark.