Incorrect Horizontal Angulation Of The Pid Results In
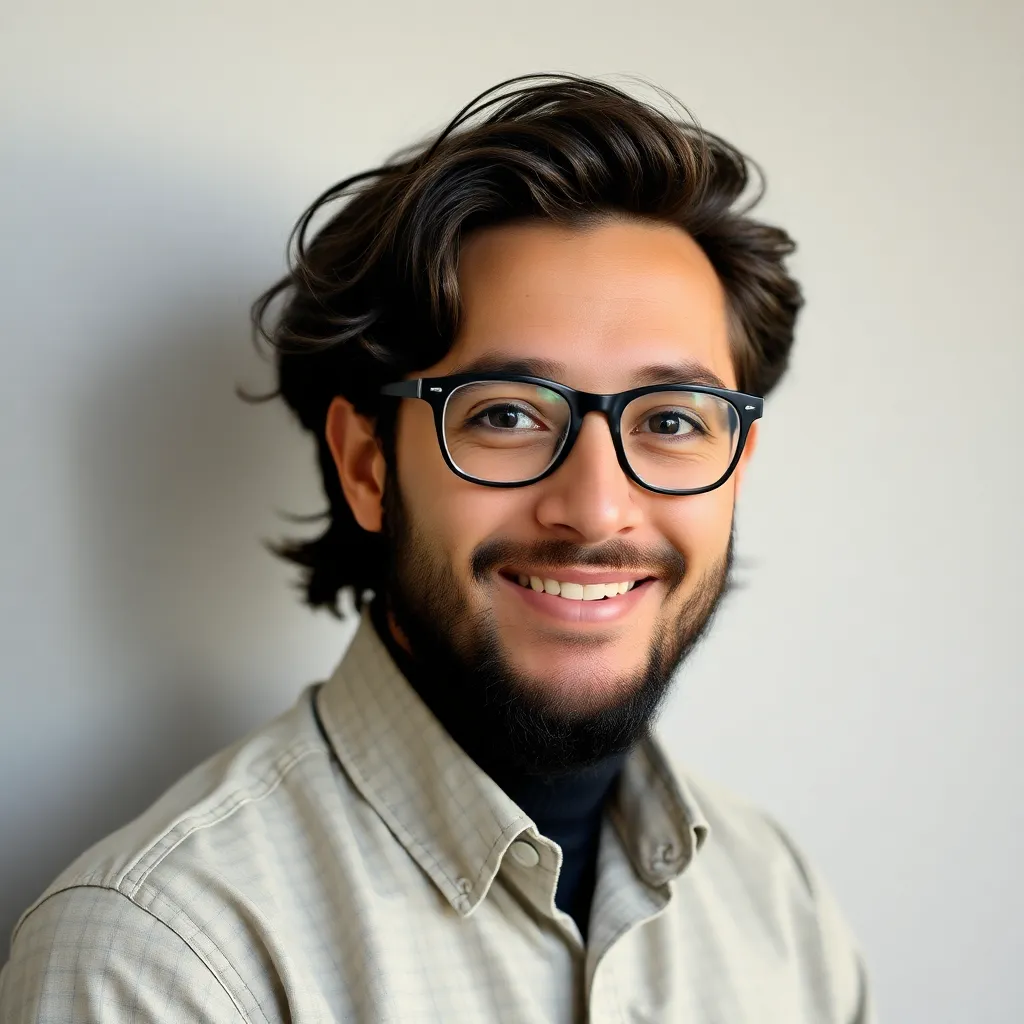
Breaking News Today
Apr 18, 2025 · 7 min read

Table of Contents
Incorrect Horizontal Angulation of the PID Results In: A Comprehensive Guide
The Proportional-Integral-Derivative (PID) controller is a ubiquitous feedback control system used across numerous industries, from industrial automation to aerospace engineering. Its effectiveness hinges on precise tuning, and one critical aspect is the correct horizontal angulation, often overlooked yet crucial for optimal performance. Incorrect horizontal angulation of the PID controller can lead to a cascade of problems, affecting stability, accuracy, and overall system efficiency. This article will delve deep into the consequences of incorrect horizontal angulation, exploring its impact on various aspects of PID control systems and offering insights into troubleshooting and corrective measures.
Understanding PID Control and Horizontal Angulation
Before discussing the repercussions of incorrect angulation, let's establish a clear understanding of what PID control entails and how horizontal angulation plays a role.
A PID controller operates by continuously measuring the difference (error) between the desired setpoint and the actual process variable. It then calculates an output signal based on three fundamental control actions:
- Proportional (P): This action is proportional to the current error. A larger error results in a larger corrective action.
- Integral (I): This action accounts for accumulated error over time. It eliminates steady-state errors but can contribute to oscillations if not properly tuned.
- Derivative (D): This action anticipates future errors based on the rate of change of the error. It helps dampen oscillations and improve response speed.
Horizontal Angulation, in the context of PID control, refers to the orientation or alignment of the control loop's response relative to the horizontal axis. A properly tuned PID controller will exhibit a horizontal angulation that reflects a smooth, stable, and efficient response to changes in the setpoint or disturbances. An incorrect angulation suggests a misalignment that indicates tuning problems.
While the term "horizontal angulation" isn't standard terminology in PID control literature, it serves as a useful conceptual framework to understand the overall behavior of the system's response and to identify when something is fundamentally wrong with the tuning. It refers to the overall shape of the response curve on a graph plotting the process variable against time. A properly tuned system will exhibit a response curve that approaches the setpoint smoothly and remains stable. Deviations from this ideal often manifest as incorrect angulation.
Consequences of Incorrect Horizontal Angulation
An incorrect horizontal angulation in a PID system signifies a significant deviation from optimal performance. The ramifications can manifest in various ways, significantly impacting the system's effectiveness and stability. Let's explore some common consequences:
1. Oscillations and Instability
One of the most prevalent consequences of improperly tuned PID controllers, often stemming from incorrect horizontal angulation, is oscillations. These oscillations can range from minor fluctuations to large, sustained swings around the setpoint. The system might fail to settle at the desired value, constantly overshooting and undershooting.
-
Cause: An overly aggressive proportional gain (Kp) or a poorly tuned derivative gain (Kd) can lead to these oscillations. This translates to a response curve that exhibits a zig-zag pattern rather than a smooth approach to the setpoint – an incorrect horizontal angulation.
-
Impact: Oscillations can damage equipment, reduce product quality, and create unsafe operating conditions.
2. Slow Response Time
An incorrectly angled response curve often indicates a sluggish or slow response to changes in the setpoint or disturbances. The system takes an excessively long time to reach the desired value, compromising its overall responsiveness.
-
Cause: A low proportional gain (Kp) or an excessively high integral gain (Ki) can result in slow response times. The system reacts weakly to errors, leading to a prolonged settling time and an incorrectly angled response.
-
Impact: Slow response times reduce efficiency and can affect productivity and throughput.
3. Steady-State Error
Steady-state error refers to the persistent difference between the actual value and the setpoint after the system has settled. Incorrect horizontal angulation can be a symptom of this error.
-
Cause: An insufficient integral gain (Ki) is the primary reason for steady-state error. Without adequate integral action, the controller fails to compensate for accumulated errors, resulting in the system settling at a value different from the setpoint. The response curve will never fully align horizontally.
-
Impact: Steady-state error can be unacceptable in many applications, especially where precise control is required.
4. Over- or Undershoot
Excessive overshoot or undershoot indicates that the system is either overly aggressive or too passive in its response. Incorrect horizontal angulation reflects this over- or under-correction.
-
Cause: An excessively high proportional gain (Kp) coupled with an inadequate derivative gain (Kd) can cause significant overshoot. Conversely, low gains can lead to sluggish response and insufficient correction, resulting in undershoot.
-
Impact: Overshoot can lead to system instability, damage to equipment, or product defects. Undershoot leads to inefficiency and prolonged settling times.
5. System Instability and Failure
In extreme cases, incorrect horizontal angulation can lead to complete system instability and failure. This is characterized by uncontrolled oscillations, runaway conditions, and the inability to maintain control.
-
Cause: Incorrectly tuned PID parameters, particularly an overly aggressive proportional gain and a poorly tuned derivative gain, can easily cause instability. The system's response spirals out of control, represented by a wildly inaccurate horizontal angulation.
-
Impact: System instability can cause equipment damage, safety hazards, and production losses.
Troubleshooting and Corrective Measures
Identifying and correcting incorrect horizontal angulation involves a systematic approach to PID tuning. Here are some strategies:
-
Visual Inspection: Observe the system's response to setpoint changes and disturbances. Plot the process variable against time to analyze the response curve. Deviations from a smooth, horizontal approach to the setpoint indicate an incorrectly angled response.
-
Manual Tuning Methods: Utilize Ziegler-Nichols methods or other manual tuning techniques to systematically adjust the P, I, and D gains. These methods provide a structured approach to finding optimal PID parameters. Observe the system's response after each adjustment, and fine-tune the gains based on the observed horizontal angulation.
-
Auto-tuning Features: Many modern PID controllers offer auto-tuning features. These features employ algorithms to automatically determine optimal PID parameters based on the system's behavior. While convenient, it’s crucial to understand the underlying principles and verify the results.
-
Simulation and Modeling: Use simulation tools to model the system's behavior and test different PID parameters before implementing them in the real system. This approach allows experimentation without risking damage to the real equipment. Simulation provides valuable insights into the relationship between PID parameters and horizontal angulation.
-
Process Understanding: Deep understanding of the controlled process is fundamental. Factors like process dynamics, delays, and non-linearities significantly impact PID performance. Consider these factors while tuning.
-
Iterative Approach: PID tuning is an iterative process. It requires repeated adjustments, careful observation, and fine-tuning to achieve optimal performance. Document each adjustment and its impact on the horizontal angulation of the response.
Advanced Considerations
Beyond the basic methods, several advanced techniques can further refine PID control and improve horizontal angulation:
-
Adaptive Control: Adaptive control algorithms automatically adjust PID parameters in response to changes in the process dynamics. This helps maintain optimal performance even under varying conditions.
-
Fuzzy Logic Control: Fuzzy logic controllers incorporate linguistic rules to handle uncertainties and non-linearities in the process. They can be combined with PID controllers to improve robustness and accuracy.
-
Neural Network Control: Neural networks can learn optimal PID parameters from data, making them suitable for complex processes with uncertain dynamics.
-
Model Predictive Control (MPC): MPC algorithms predict the future behavior of the system and optimize control actions to minimize errors. MPC offers advanced capabilities for complex processes and often outperforms traditional PID controllers in terms of stability and efficiency.
Conclusion
Incorrect horizontal angulation in a PID controller signals a fundamental issue within the control loop. Understanding the causes and consequences of incorrect angulation is critical for maintaining system stability, accuracy, and efficiency. By employing a combination of manual tuning, advanced tuning methods, and thorough process understanding, engineers can achieve precise PID control, leading to optimized system performance and a correctly angled response curve—a crucial aspect often overlooked but pivotal for successful automation. A correctly tuned system will exhibit a smooth, stable, and efficient response curve, reflecting an accurate and predictable horizontal angulation in its control performance. Remember, the pursuit of a properly angled response curve represents a commitment to optimal control system performance.
Latest Posts
Latest Posts
-
Group Life Policies In Florida Are Required To Contain
Apr 19, 2025
-
Each Of The Faces Of A Fair Six Sided
Apr 19, 2025
-
To Calculate The Empirical Formula Start By
Apr 19, 2025
-
Mr Xi Will Soon Turn Age 65
Apr 19, 2025
-
The United States And East Asia Quick Check
Apr 19, 2025
Related Post
Thank you for visiting our website which covers about Incorrect Horizontal Angulation Of The Pid Results In . We hope the information provided has been useful to you. Feel free to contact us if you have any questions or need further assistance. See you next time and don't miss to bookmark.