Maintenance And Repairs Is An Operations Activity That Includes
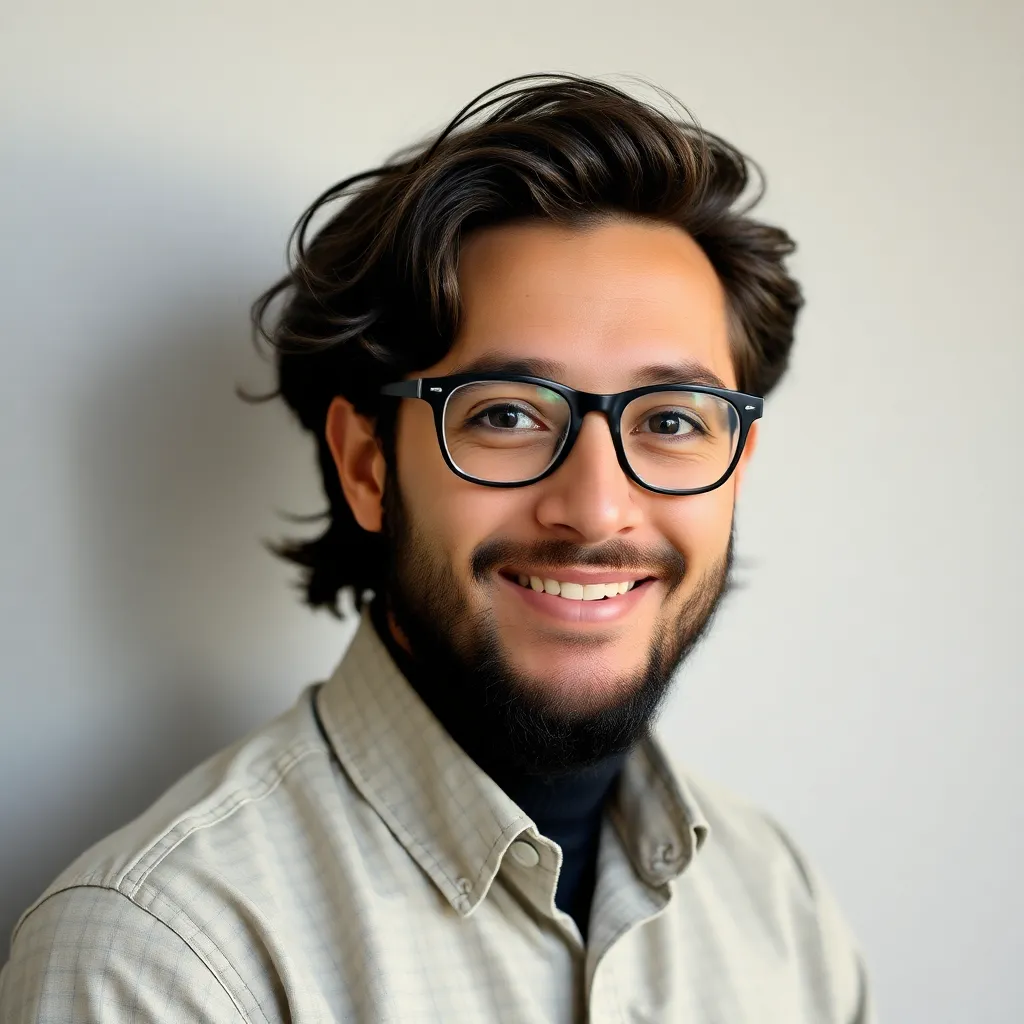
Breaking News Today
May 09, 2025 · 6 min read
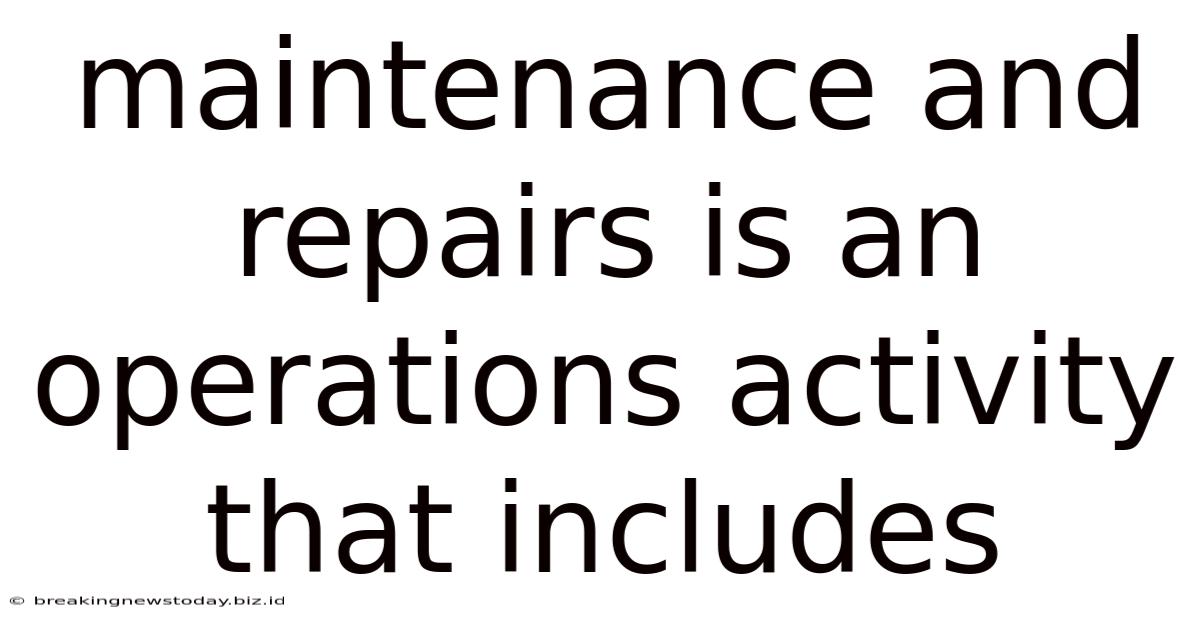
Table of Contents
Maintenance and Repairs: A Core Operations Activity
Maintenance and repairs are integral to the smooth functioning of any organization, regardless of size or industry. It's not merely a cost center; it's a strategic operational activity that directly impacts productivity, safety, profitability, and overall operational efficiency. This comprehensive guide delves into the multifaceted aspects of maintenance and repairs, exploring its significance, various types, planning strategies, and best practices for optimization.
The Importance of Maintenance and Repairs in Operations
Effective maintenance and repair programs are essential for several reasons:
1. Maximizing Equipment Lifespan and Performance
Regular maintenance significantly extends the lifespan of equipment and machinery. By addressing minor issues before they escalate into major problems, organizations can prevent costly breakdowns, reduce downtime, and ensure consistent operational performance. This proactive approach minimizes unexpected repairs and maximizes the return on investment (ROI) for capital equipment. Proactive maintenance is key to long-term cost savings.
2. Enhancing Safety and Reducing Risks
Neglecting maintenance can create hazardous working conditions, increasing the risk of accidents and injuries. Regular inspections, repairs, and preventative measures ensure that equipment operates safely and reliably, protecting both employees and assets. A strong safety culture, underpinned by robust maintenance practices, is crucial for mitigating workplace risks.
3. Improving Operational Efficiency and Productivity
Unplanned downtime due to equipment failures can severely disrupt operations, leading to production delays, lost revenue, and unmet customer demands. A well-planned maintenance program minimizes such disruptions, ensuring consistent productivity and meeting operational targets. This leads to increased operational efficiency and improved output.
4. Reducing Costs and Increasing Profitability
While maintenance involves costs, the long-term benefits far outweigh the expenses. Preventing major breakdowns, minimizing downtime, and extending equipment lifespan ultimately translate into significant cost savings. This cost-effectiveness directly contributes to improved profitability.
5. Maintaining Regulatory Compliance
Many industries are subject to strict regulations regarding equipment maintenance and safety. Organizations must adhere to these regulations to avoid penalties, legal issues, and reputational damage. A robust maintenance program ensures compliance and demonstrates a commitment to regulatory standards.
Types of Maintenance and Repairs
Maintenance and repair activities can be categorized into several types:
1. Preventative Maintenance (PM)
This proactive approach focuses on preventing equipment failures before they occur. It involves regular inspections, lubrication, cleaning, and adjustments to ensure equipment operates optimally. Preventative maintenance is scheduled at regular intervals and helps extend equipment lifespan, improve efficiency, and reduce downtime.
2. Corrective Maintenance (CM)
This reactive approach addresses equipment failures after they have occurred. It involves repairing or replacing damaged components to restore equipment functionality. While necessary, corrective maintenance is often more expensive and disruptive than preventative maintenance, highlighting the importance of proactive maintenance strategies.
3. Predictive Maintenance (PdM)
This advanced approach uses data analysis and monitoring technologies to predict potential equipment failures. By analyzing sensor data, vibration patterns, and other indicators, organizations can identify problems before they manifest as breakdowns. Predictive maintenance allows for timely interventions, minimizing downtime and optimizing resource allocation.
4. Breakdown Maintenance (BM)
This reactive approach involves repairing equipment only after it has completely failed. It's the least efficient and most costly type of maintenance. It leads to significant downtime, production losses, and potential safety hazards. Breakdown maintenance should be avoided as much as possible through implementing other maintenance strategies.
5. Condition-Based Maintenance (CBM)
This approach combines elements of predictive and preventative maintenance. It involves monitoring the condition of equipment and performing maintenance only when necessary based on the actual condition of the asset. CBM helps optimize maintenance schedules, reduce unnecessary interventions, and maximize equipment lifespan.
Planning and Implementing Effective Maintenance Programs
Developing and implementing a successful maintenance program requires a structured approach:
1. Conducting Thorough Equipment Assessments
A detailed assessment of all equipment, including its criticality, age, condition, and maintenance history, is essential for developing a tailored maintenance plan. This involves identifying critical components, potential failure points, and maintenance requirements for each piece of equipment. This data-driven approach informs maintenance scheduling and resource allocation.
2. Developing a Comprehensive Maintenance Schedule
Based on the equipment assessment, a comprehensive schedule outlining preventative maintenance tasks, inspection intervals, and spare parts requirements should be developed. This schedule should be tailored to the specific needs of each piece of equipment and consider factors such as operating hours, environmental conditions, and usage patterns. A well-defined schedule ensures timely maintenance and minimizes disruptions.
3. Establishing a Robust Inventory Management System
Efficient inventory management is crucial for ensuring that necessary spare parts and consumables are readily available when needed. This involves tracking inventory levels, managing stock replenishment, and minimizing waste. A streamlined inventory system reduces downtime and prevents delays in repairs.
4. Training and Empowering Maintenance Personnel
Well-trained maintenance personnel are essential for effective maintenance and repair operations. Providing comprehensive training on equipment operation, maintenance procedures, and safety protocols is critical. Empowering the maintenance team increases their efficiency and effectiveness.
5. Utilizing Maintenance Management Software (MMS)
MMS streamlines maintenance processes, allowing for efficient scheduling, tracking, and reporting of maintenance activities. It centralizes information, improves communication, and provides valuable data for optimizing maintenance strategies. MMS significantly improves the efficiency and effectiveness of maintenance operations.
6. Establishing Key Performance Indicators (KPIs)
KPIs provide measurable targets for assessing the effectiveness of the maintenance program. Examples include mean time between failures (MTBF), mean time to repair (MTTR), maintenance costs, and downtime. Regularly monitoring and analyzing KPIs allows for identifying areas for improvement and optimizing the program. Data-driven improvements are essential for continuous improvement.
Optimizing Maintenance and Repair Operations
Several strategies can be employed to optimize maintenance and repair operations:
1. Implementing Root Cause Analysis (RCA)
RCA helps to identify the underlying causes of equipment failures, preventing recurrence. By investigating the root cause of each failure, organizations can implement corrective actions to prevent similar incidents in the future. RCA reduces the frequency of failures and improves reliability.
2. Utilizing Total Productive Maintenance (TPM)
TPM is a holistic approach to maintenance that involves the entire organization in improving equipment reliability and productivity. It emphasizes proactive maintenance, employee involvement, and continuous improvement. TPM fosters a culture of preventative maintenance and optimizes equipment performance.
3. Leveraging Technology and Automation
Advanced technologies such as sensors, data analytics, and automation can significantly improve maintenance efficiency and effectiveness. These technologies allow for predictive maintenance, remote monitoring, and automated fault detection. Technology enhances maintenance accuracy and minimizes human error.
4. Outsourcing Maintenance Services
In some cases, outsourcing maintenance services can be a cost-effective solution, especially for specialized equipment or when internal resources are limited. Outsourcing allows organizations to access specialized expertise and resources while focusing on their core competencies. Strategic outsourcing optimizes resource allocation and improves maintenance quality.
5. Continuous Improvement and Monitoring
Regularly reviewing and updating the maintenance program based on performance data and feedback is crucial for continuous improvement. This involves analyzing KPIs, identifying areas for improvement, and implementing changes to optimize the program. Continuous improvement is vital for maintaining efficiency and effectiveness.
Conclusion
Maintenance and repairs are not simply operational costs; they are strategic investments that directly impact an organization's productivity, profitability, safety, and overall success. By implementing a well-planned, proactive maintenance program and leveraging best practices, organizations can significantly improve operational efficiency, reduce downtime, extend equipment lifespan, and enhance safety. The integration of technology, data analysis, and continuous improvement efforts is key to maximizing the effectiveness of maintenance and repair operations in today's competitive landscape. A proactive, data-driven approach to maintenance translates to a more robust, efficient, and profitable organization.
Latest Posts
Latest Posts
-
Does A Quizlet User Know If I Combine Quizzes
May 09, 2025
-
The Reinstatement Provision In A Health Insurance Policy Is
May 09, 2025
-
According To Freud Much Of Our Behavior Is Motivated By
May 09, 2025
-
What Is True About Product Recalls In The 21st Century
May 09, 2025
-
Which Of The Following Statements About Crossing Over Is True
May 09, 2025
Related Post
Thank you for visiting our website which covers about Maintenance And Repairs Is An Operations Activity That Includes . We hope the information provided has been useful to you. Feel free to contact us if you have any questions or need further assistance. See you next time and don't miss to bookmark.