Match The Step In The Control Process With Its Description.
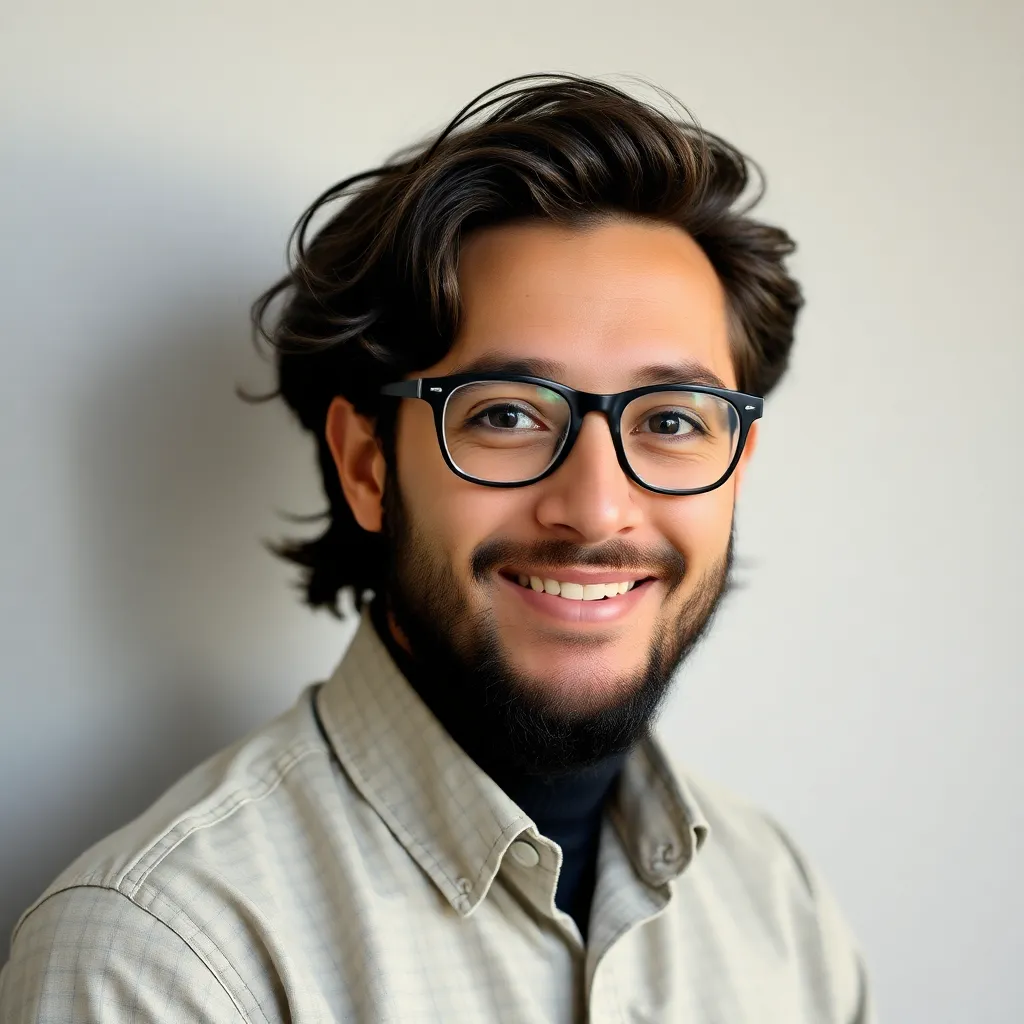
Breaking News Today
Apr 27, 2025 · 6 min read

Table of Contents
Match the Step in the Control Process with Its Description: A Comprehensive Guide
Controlling is a crucial management function that ensures activities are performed according to plans and objectives. It's a continuous process involving several steps, each vital for effective organizational performance. This comprehensive guide will delve into each step of the control process, providing detailed descriptions and practical examples to help you master this essential management skill.
The Four Key Steps in the Control Process
The control process typically involves four interconnected steps:
- Establishing Standards: Setting clear benchmarks for performance.
- Measuring Performance: Assessing actual results against established standards.
- Comparing Performance to Standards: Identifying deviations or variances between actual and expected performance.
- Taking Corrective Action: Implementing measures to address performance gaps and ensure future alignment with standards.
Let's explore each step in detail:
1. Establishing Standards: Setting the Benchmarks for Success
This initial step lays the foundation for the entire control process. Establishing standards involves defining clear, measurable, achievable, relevant, and time-bound (SMART) goals and criteria against which performance will be evaluated. These standards should be:
Characteristics of Effective Standards:
- Specific: Standards should be unambiguous and leave no room for misinterpretation. Instead of a vague goal like "improve customer service," a specific standard might be "reduce customer complaint resolution time by 15% within the next quarter."
- Measurable: Standards must be quantifiable, allowing for objective assessment. This could involve numerical targets, percentages, or other quantifiable metrics.
- Achievable: Standards should be realistic and attainable, considering available resources and constraints. Unrealistic expectations can demotivate employees and lead to failure.
- Relevant: Standards must align with organizational goals and contribute to overall strategic objectives. Irrelevant standards waste resources and distract from crucial priorities.
- Time-Bound: Standards should have a clear timeframe for accomplishment. This creates urgency and allows for timely evaluation and adjustments.
Examples of Standards Across Different Functions:
- Production: Number of units produced per hour, defect rate, materials waste percentage.
- Marketing: Brand awareness, market share, customer acquisition cost.
- Finance: Return on investment (ROI), profitability margins, cash flow.
- Human Resources: Employee turnover rate, employee satisfaction scores, training completion rates.
- Quality Control: Number of defects per batch, customer satisfaction ratings, adherence to industry standards.
Crucial Consideration: The standards set should be communicated effectively to all relevant stakeholders. This ensures everyone is working towards the same goals and understands the expectations. Transparency fosters accountability and engagement.
2. Measuring Performance: Gathering Accurate and Timely Data
Once standards are established, the next step involves systematically measuring actual performance against those standards. Accurate and timely data collection is crucial for effective control. This stage often involves:
Methods for Measuring Performance:
- Quantitative Data: Numerical data like sales figures, production output, or financial metrics. These provide objective measures of performance.
- Qualitative Data: Non-numerical data gathered through surveys, interviews, observations, or focus groups. This helps assess subjective aspects like employee morale or customer satisfaction.
- Performance Reports: Regularly generated reports that summarize key performance indicators (KPIs) and provide a snapshot of current performance levels.
- Technology-Based Monitoring: Utilizing software and systems to track performance in real-time, providing immediate insights and alerts. This can involve CRM systems, project management software, or manufacturing automation systems.
- Direct Observation: Observing employees or processes firsthand to assess performance. This can provide valuable qualitative insights, especially when assessing complex or nuanced aspects of performance.
Ensuring Accuracy and Timeliness:
- Use Reliable Data Sources: Ensure the data used for measurement is from credible and verifiable sources. Inaccurate data will lead to flawed conclusions and ineffective corrective actions.
- Establish Clear Measurement Procedures: Develop well-defined procedures for data collection and recording to ensure consistency and minimize errors.
- Utilize Technology: Leverage technology to automate data collection and analysis, improving accuracy and efficiency.
- Regular Monitoring: Conduct regular performance monitoring to identify deviations early on, before they become significant problems.
Important Note: The methods used for measuring performance should align with the specific standards established in the first step. The choice of measurement techniques will depend on the nature of the activity and the available resources.
3. Comparing Performance to Standards: Identifying Deviations
This step involves analyzing the collected data and comparing actual performance to the pre-established standards. The objective is to identify any variances or deviations—differences between actual and expected results. This comparison should reveal:
Types of Deviations:
- Favorable Deviations: Performance exceeding expectations. While positive, these still require analysis to understand the reasons for the success and to replicate it in other areas.
- Unfavorable Deviations: Performance falling short of expectations. These require immediate attention to identify causes and implement corrective actions.
Techniques for Comparing Performance:
- Variance Analysis: A quantitative technique that compares budgeted or planned figures to actual results, identifying the magnitude and direction of the differences.
- Benchmarking: Comparing performance against industry best practices or competitors to identify areas for improvement.
- Performance Dashboards: Visual representations of key performance indicators, allowing for a quick overview of overall performance and highlighting deviations.
- Trend Analysis: Analyzing performance data over time to identify patterns and trends, helping predict future performance and anticipate potential problems.
Critical Insight: Simply identifying deviations is not enough; understanding why the deviations occurred is equally crucial. This often involves investigating the root causes, considering various factors such as resource constraints, process inefficiencies, or external factors.
4. Taking Corrective Action: Addressing Performance Gaps
The final step in the control process involves taking appropriate action to address any identified performance gaps. Corrective actions can range from minor adjustments to significant organizational changes, depending on the severity and nature of the deviation. Effective corrective actions should:
Types of Corrective Actions:
- Immediate Corrective Action: Addressing the immediate problem to prevent further deviation. This might involve adjusting processes, providing additional resources, or temporarily reallocating personnel.
- Basic Corrective Action: Addressing the root cause of the deviation to prevent recurrence. This might involve process improvements, employee training, or changes to organizational structure.
- Preventative Action: Proactive steps to prevent future deviations. This might involve implementing new systems, developing improved procedures, or enhancing employee skills.
Implementing Effective Corrective Actions:
- Identify Root Causes: Thoroughly investigate the causes of the deviation to ensure that corrective actions address the underlying problem, not just the symptoms.
- Develop Specific Actions: Create a clear plan outlining the specific actions to be taken, assigning responsibility, and setting deadlines.
- Monitor Effectiveness: Track the effectiveness of corrective actions to ensure they are achieving the desired results. Regular monitoring allows for adjustments as needed.
- Communicate Changes: Clearly communicate corrective actions to all relevant stakeholders, ensuring everyone is aware of the changes and their implications.
- Document Processes: Maintain detailed records of corrective actions taken, including the rationale, implementation details, and results. This information can be valuable for future decision-making and continuous improvement.
Important Note: The success of corrective actions depends on timely implementation and effective communication. Delaying action or failing to communicate effectively can exacerbate the problem and undermine the effectiveness of the control process.
Conclusion: Mastering the Control Process for Organizational Success
The control process is a dynamic and iterative cycle. Effective control is not simply about reacting to problems; it's about proactively monitoring performance, identifying deviations early on, and implementing appropriate corrective actions to ensure activities align with organizational goals. By diligently following these four steps and employing the strategies outlined above, organizations can significantly enhance efficiency, productivity, and overall success. Mastering the control process is paramount to achieving sustainable growth and maintaining a competitive edge in today’s dynamic business environment. Continuous monitoring, adaptation, and improvement are key components of a successful control system. Regular review and updates to established standards are also crucial to reflect changing business needs and market dynamics.
Latest Posts
Latest Posts
-
Based On This Model Households Earn Income When
Apr 27, 2025
-
When Graphing Your Data It Is Important To
Apr 27, 2025
-
A And Are Network Infrastructure Devices
Apr 27, 2025
-
The Interosseous Membrane Is Located Between The
Apr 27, 2025
-
What Does The Poem Include That The Artwork Does Not
Apr 27, 2025
Related Post
Thank you for visiting our website which covers about Match The Step In The Control Process With Its Description. . We hope the information provided has been useful to you. Feel free to contact us if you have any questions or need further assistance. See you next time and don't miss to bookmark.