Material Used To Make Gears That Can Tolerate High Loads
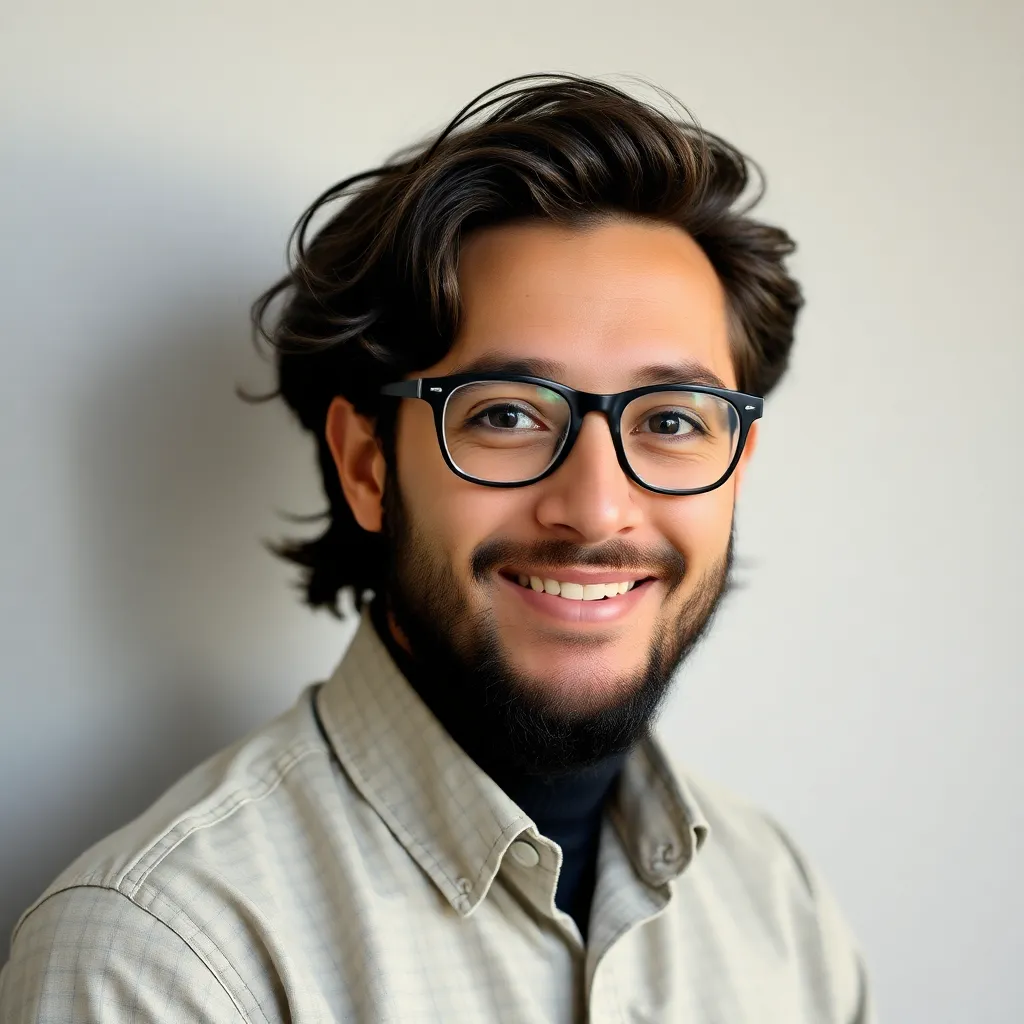
Breaking News Today
May 11, 2025 · 6 min read
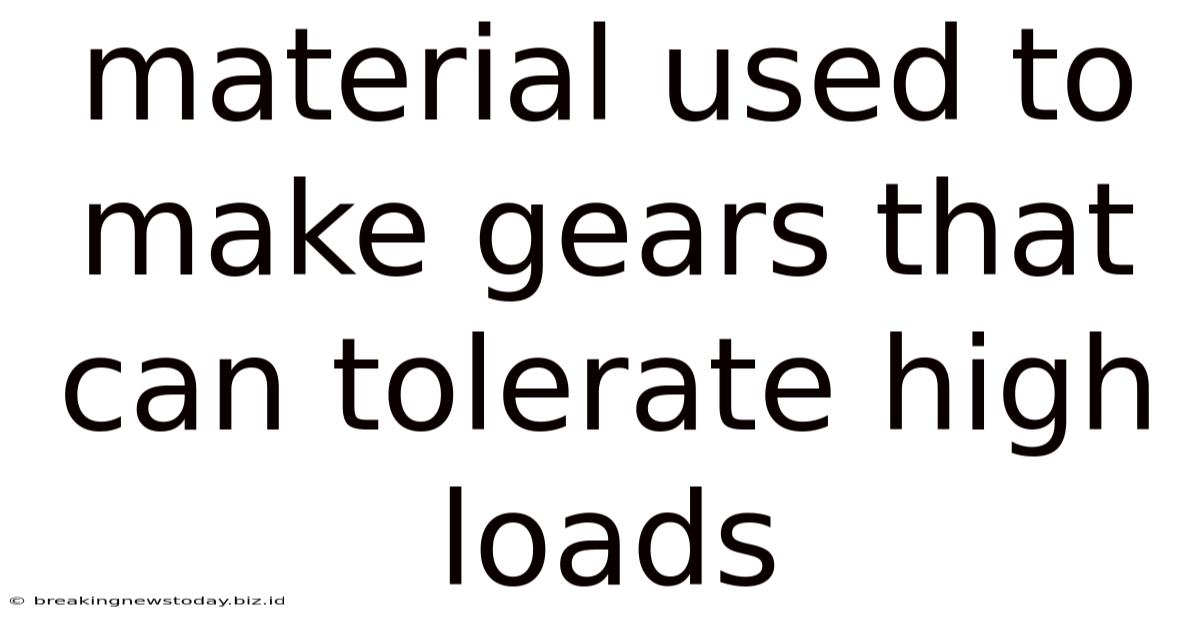
Table of Contents
Materials for High-Load Gear Applications: A Comprehensive Guide
Gears are fundamental components in countless mechanical systems, from automotive transmissions to industrial machinery. When dealing with high loads, the choice of material becomes paramount, directly impacting performance, longevity, and overall system reliability. This comprehensive guide explores the materials commonly used in high-load gear applications, delving into their properties, advantages, and limitations. Understanding these factors is crucial for engineers and designers tasked with creating robust and efficient machinery capable of withstanding demanding operational environments.
Understanding the Demands of High-Load Applications
High-load gear applications present significant challenges. These include:
High Contact Stresses: Gears experience intense pressure at the point of contact between teeth. This can lead to surface fatigue, pitting, and ultimately, gear failure.
Wear and Abrasion: Continuous contact and friction between gear teeth generate wear, particularly under high loads. This necessitates materials with high wear resistance.
Impact Loads: Sudden shocks and vibrations can significantly stress gears, potentially causing fracture or premature failure. Materials must exhibit good impact toughness.
High Temperatures: Friction generates heat, and high loads exacerbate this issue. Materials need to retain their strength and other critical properties at elevated temperatures.
Key Material Properties for High-Load Gears
Several key properties dictate a material's suitability for high-load gear applications:
- High Tensile Strength: The ability to withstand significant pulling forces is essential for preventing gear tooth fracture.
- High Compressive Strength: Resistance to crushing forces is crucial for preventing gear tooth deformation under high loads.
- High Fatigue Strength: The ability to withstand repeated stress cycles without failure is paramount for longevity.
- High Hardness: Hardness ensures resistance to wear, abrasion, and surface damage.
- High Impact Toughness: The ability to absorb energy from impact loads without fracturing.
- Good Wear Resistance: Minimizes wear and tear, extending gear lifespan.
- High Elastic Modulus: A measure of stiffness, influencing the accuracy and precision of gear meshing.
- Good Thermal Conductivity: Helps dissipate heat generated by friction.
- Corrosion Resistance: Essential in harsh environments to protect against degradation.
Common Materials for High-Load Gears
Several materials stand out for their ability to withstand high-load conditions. Let's examine the most prominent ones:
1. Steel Alloys:
Steel remains the workhorse of high-load gear manufacturing. Various alloying elements modify its properties to suit specific applications.
- Carbon Steels: Offer a balance of strength and cost-effectiveness. However, they may not be suitable for extremely high loads or demanding environments. Higher carbon content increases hardness but reduces toughness.
- Alloy Steels: Incorporating elements like nickel, chromium, molybdenum, and vanadium significantly enhances strength, toughness, and wear resistance. These steels are often used in demanding applications. Examples include:
- Nickel-chromium-molybdenum steels (e.g., 4140, 8620): Excellent strength, toughness, and hardenability.
- High-speed steels (HSS): Exceptional wear resistance, often used in cutting tools and high-speed gears.
- Case-Hardened Steels: These steels undergo a surface hardening process (e.g., carburizing, nitriding) to create a hard wear-resistant surface while retaining a tough core. This combination optimizes both wear resistance and impact toughness.
2. Cast Iron:
Cast iron offers excellent compressive strength and good damping capacity. Its relative ease of casting makes it cost-effective for large gears. However, its tensile strength is lower compared to steel, limiting its use in high-tension applications. Different types of cast iron offer varying properties:
- Gray Cast Iron: Economical, readily machinable, and exhibits good damping capacity. However, its tensile strength and fatigue strength are lower than steel.
- Ductile Iron (Nodular Iron): Superior strength and toughness compared to gray cast iron, making it suitable for more demanding applications.
3. Non-Ferrous Metals:
While less common than steel and cast iron, certain non-ferrous metals find niche applications in high-load gears, particularly when corrosion resistance or specific material properties are prioritized:
- Bronze: Excellent wear resistance, especially in applications involving lubrication difficulties. However, its strength is lower than steel.
- Brass: Good machinability and corrosion resistance, but generally not suitable for extreme high-load situations.
- Aluminum Alloys: Lightweight and corrosion-resistant, but generally not suitable for very high-load applications due to lower strength compared to steel.
4. Ceramics:
Advanced ceramic materials offer exceptional hardness, wear resistance, and high-temperature capabilities. However, their brittle nature and potential for fracture under impact limit their use in high-load applications, typically restricted to specific components or situations:
- Silicon Nitride: Exceptional hardness and wear resistance. Its high cost and potential for fracture restrict its widespread adoption.
- Aluminum Oxide: Good hardness and wear resistance, but also relatively brittle.
5. Composites:
Composite materials, combining different materials like fibers reinforced in a matrix, offer potential advantages in specific applications. However, their use in high-load gears is still under development:
- Fiber-reinforced polymers: High strength-to-weight ratios, but generally not suitable for extreme high loads and high temperatures.
Gear Design Considerations for High Loads
Material selection is only one piece of the puzzle. Optimizing gear design is critical for maximizing the lifespan and performance of high-load gears:
- Proper Gear Ratio: Selecting the appropriate gear ratio minimizes stress on the gears.
- Tooth Profile: The geometry of the gear teeth impacts load distribution and wear resistance. Modified tooth profiles, such as those with increased contact ratio, can improve performance.
- Surface Treatments: Surface treatments such as nitriding, carburizing, or shot peening can enhance surface hardness, wear resistance, and fatigue strength.
- Lubrication: Appropriate lubrication is vital for reducing friction, wear, and heat generation. High-quality lubricants, specialized for high-load conditions, are essential.
- Manufacturing Processes: Precise manufacturing techniques are crucial for ensuring accurate gear geometry and minimizing defects that can initiate failure.
Material Selection Process for High-Load Gears
Choosing the right material involves a careful consideration of several factors:
- Load Characteristics: Determine the magnitude, type (static, dynamic, impact), and direction of the loads.
- Operating Environment: Consider temperature, humidity, corrosive substances, and lubrication conditions.
- Required Lifespan: Specify the desired operating time before replacement or maintenance.
- Cost Constraints: Balancing material cost with performance requirements is crucial.
- Manufacturing Capabilities: Evaluate the feasibility and cost of manufacturing gears from chosen materials.
Conclusion
Selecting materials for high-load gear applications demands careful consideration of numerous factors. While steel alloys remain the most prevalent choice, the specific alloy and surface treatments must be tailored to the specific application's demands. Other materials, like cast iron, ceramics, and composites, offer potential advantages in specific niche applications. A thorough understanding of material properties, gear design principles, and the overall operating conditions is essential for ensuring the reliability and longevity of high-load gear systems. Optimization requires a holistic approach, encompassing material selection, gear design, manufacturing processes, and appropriate lubrication strategies. This synergistic approach maximizes performance, reduces downtime, and contributes to the overall success of the mechanical system.
Latest Posts
Latest Posts
-
Which Of These Changes Will Result In Increased Blood Pressure
May 12, 2025
-
New York State Life Insurance Exam Questions
May 12, 2025
-
Which Program Did Lovaas Develop Based On Discrete Trial Intervention
May 12, 2025
-
The Color Purple Book Quotes With Page Numbers
May 12, 2025
-
When Did The Term Stress Enter Scientific Literature
May 12, 2025
Related Post
Thank you for visiting our website which covers about Material Used To Make Gears That Can Tolerate High Loads . We hope the information provided has been useful to you. Feel free to contact us if you have any questions or need further assistance. See you next time and don't miss to bookmark.