Metal Fasteners Used With Carbon Graphite Composite Structures
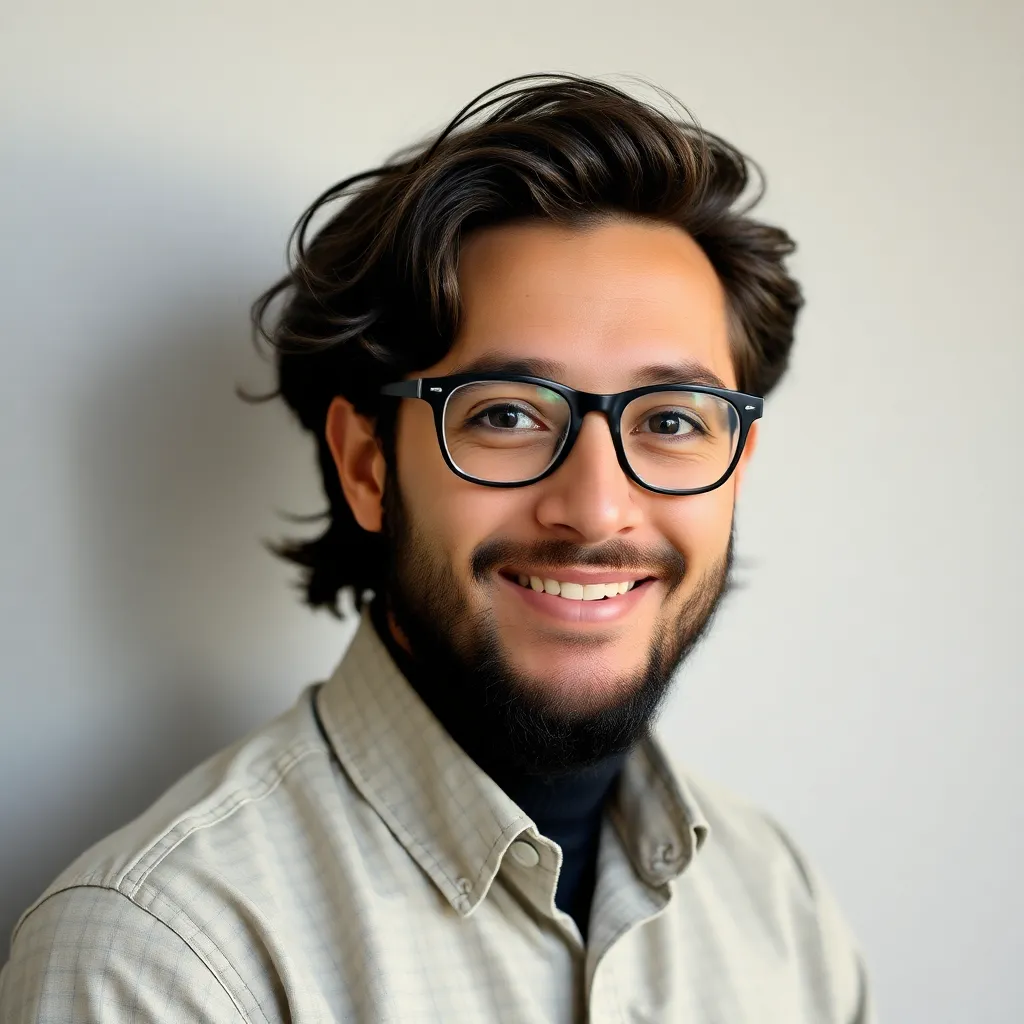
Breaking News Today
May 11, 2025 · 6 min read
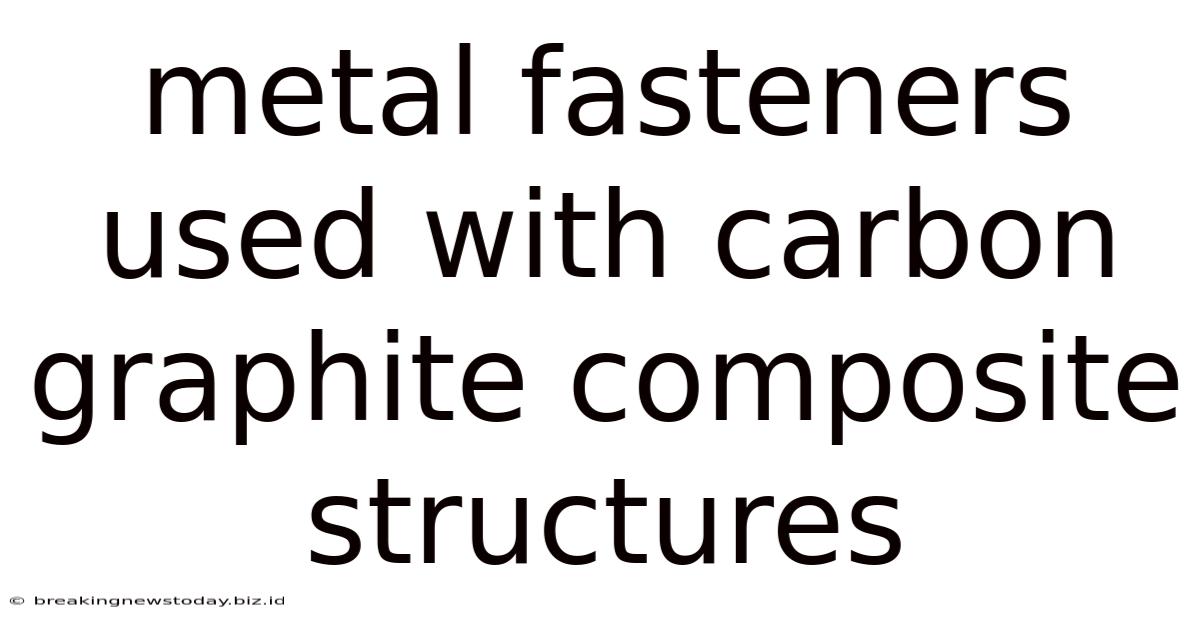
Table of Contents
Metal Fasteners Used with Carbon Graphite Composite Structures
Carbon graphite composites (CGCs) are increasingly prevalent in high-performance applications due to their exceptional strength-to-weight ratio, stiffness, and fatigue resistance. However, joining these materials presents unique challenges. Unlike metals, which can be easily welded or brazed, CGCS require specialized joining techniques to maintain structural integrity and avoid damage to the composite. Metal fasteners are frequently employed for joining CGCS, but their application demands careful consideration of several crucial factors to ensure reliable and durable joints. This article delves into the specifics of using metal fasteners with carbon graphite composite structures, exploring various fastener types, joint design considerations, and best practices for achieving optimal performance.
Understanding the Challenges of Fastening Carbon Graphite Composites
The inherent characteristics of CGCs pose significant challenges when it comes to fastening:
1. Anisotropy and Heterogeneity:
CGCs are anisotropic, meaning their mechanical properties vary depending on the direction of the applied load. The fibers within the composite are typically aligned in a specific direction to maximize strength along that axis. This anisotropy significantly affects the fastener’s behavior and the overall joint strength. Furthermore, the heterogeneous nature of the material – consisting of fibers and a matrix – introduces stress concentrations around the fastener hole, potentially leading to delamination or fiber breakage.
2. Low Shear Strength:
While CGCs exhibit high tensile strength along the fiber direction, their shear strength is considerably lower. This is particularly critical for bolted joints, where shear forces are often dominant. Careful consideration of the bolt diameter, material, and joint design is necessary to prevent shear failure of the composite.
3. Susceptibility to Damage:
Drilling holes in CGCS can cause damage to the surrounding fibers, reducing the material's strength and stiffness. The hole size, the drilling process, and the subsequent preparation of the hole are crucial factors in minimizing damage and ensuring joint integrity.
4. Environmental Degradation:
CGCs can be susceptible to environmental degradation, particularly moisture absorption and thermal cycling. The fastener and the joint design must be selected to withstand these environmental factors and prevent premature failure.
Types of Metal Fasteners Used with Carbon Graphite Composites
Several types of metal fasteners are suitable for joining CGCS, each with its advantages and limitations:
1. Bolts:
Bolts are the most common type of fastener used with CGCS, offering high clamping force and reliable performance. However, they require pre-drilled holes, potentially introducing damage. High-strength steel or titanium bolts are frequently used due to their high strength-to-weight ratio and corrosion resistance. The choice of bolt material depends on the application's specific requirements and environmental conditions.
2. Screws:
Screws, like bolts, are suitable for joining CGCS but often require the use of specialized washers or inserts to distribute the load and prevent damage to the composite. Self-tapping screws can be used in some cases, eliminating the need for pre-drilling, but they can induce more stress concentrations. Material selection is crucial, with stainless steel and titanium being popular choices.
3. Rivets:
Rivets offer a permanent fastening solution, suitable for applications where disassembly is not required. However, they typically require specialized tooling and careful design to ensure proper joint strength. Aluminum and titanium rivets are commonly used due to their lightweight and high strength properties.
4. Pins:
Pins, particularly interference-fit pins, can be used for joining CGCS, particularly in applications requiring high shear strength. The interference fit creates a strong joint without the need for pre-drilled holes, but careful control of the pin diameter and material is crucial to avoid damaging the composite.
Joint Design Considerations
The design of the joint is paramount to achieving optimal performance when fastening CGCS. Key considerations include:
1. Hole Size and Preparation:
The hole diameter should be carefully selected to minimize damage to the surrounding fibers. Undersized holes can lead to excessive stress concentrations, while oversized holes can weaken the joint. Precise hole drilling techniques, such as laser drilling, are often preferred to reduce damage. Deburring the hole is essential to prevent stress risers and improve the fastener’s seating.
2. Washers and Inserts:
Washers are crucial in distributing the load and preventing damage to the composite around the fastener. Large-diameter washers significantly reduce the stress concentration. Composite inserts, sometimes made of the same material as the composite structure or a high-strength material, can be embedded into the composite during manufacturing to provide a stronger, more reliable attachment point. These inserts create a reinforced zone around the fastener hole.
3. Bolt Torque and Clamping Force:
Proper bolt torque is critical to ensure sufficient clamping force without over-tightening and damaging the composite. Over-tightening can crush the composite, leading to delamination. The recommended torque should be determined based on the bolt material, size, and composite properties. Torque wrenches are essential to ensure accurate tightening.
4. Adhesive Bonding:
In many instances, adhesive bonding is used in conjunction with mechanical fasteners to improve joint performance. Adhesives can fill gaps, distribute stress, and enhance the load transfer between the fastener and the composite. Structural adhesives with high strength and durability are commonly selected. The adhesive selection depends on the environmental conditions and the specific requirements of the application.
5. Finite Element Analysis (FEA):
FEA is an invaluable tool for optimizing joint design. By simulating the stress distribution and predicting potential failure modes, FEA can help engineers make informed design decisions to minimize risks and enhance reliability. This method allows for virtual testing and refinement before physical prototyping.
Best Practices for Fastening Carbon Graphite Composites
Adhering to best practices is crucial for the successful and reliable fastening of carbon graphite composite structures.
-
Material Selection: Carefully select the fastener material based on the application’s requirements, considering factors such as strength, weight, corrosion resistance, and thermal properties.
-
Surface Preparation: Ensure proper surface preparation of both the composite and the metal fastener before assembly. Cleaning the surfaces removes contaminants and promotes better adhesion.
-
Proper Drilling Techniques: Utilize accurate and controlled drilling techniques to minimize damage to the composite material. Consider using specialized drills and techniques like laser drilling.
-
Careful Installation: Ensure proper installation of the fasteners, following the manufacturer's guidelines for torque and clamping force.
-
Non-Destructive Testing (NDT): Consider using NDT techniques, such as ultrasonic inspection, to detect any potential defects or flaws in the joints after assembly.
-
Quality Control: Implement rigorous quality control procedures at each stage of the manufacturing process to ensure the reliability and durability of the fastened joints.
Conclusion
Fastening carbon graphite composite structures requires careful consideration of numerous factors. The choice of fastener type, joint design, and installation procedures are critical to achieving optimal performance and ensuring joint reliability. By understanding the inherent challenges of fastening CGCS and adhering to best practices, engineers can design and manufacture high-performance structures that exploit the superior material properties of these advanced composites. Continuous advancements in materials science and joining techniques will further enhance the capabilities and reliability of these critical connections. Ongoing research into novel fastener designs, improved adhesives, and advanced joining techniques is continuously pushing the boundaries of high-performance composite structures. The future of composite structures relies heavily on the development of robust and efficient joining solutions.
Latest Posts
Latest Posts
-
Medical Assisting Administrative And Clinical Procedures 7th Edition
May 12, 2025
-
Condensation Of Chromosomes Continues Throughout Which Phase Of Mitosis
May 12, 2025
-
Why Does The Compressor On A Leaking System Become Overheated
May 12, 2025
-
Which Of These Changes Will Result In Increased Blood Pressure
May 12, 2025
-
New York State Life Insurance Exam Questions
May 12, 2025
Related Post
Thank you for visiting our website which covers about Metal Fasteners Used With Carbon Graphite Composite Structures . We hope the information provided has been useful to you. Feel free to contact us if you have any questions or need further assistance. See you next time and don't miss to bookmark.