Production Order Processing Is An Example Of A
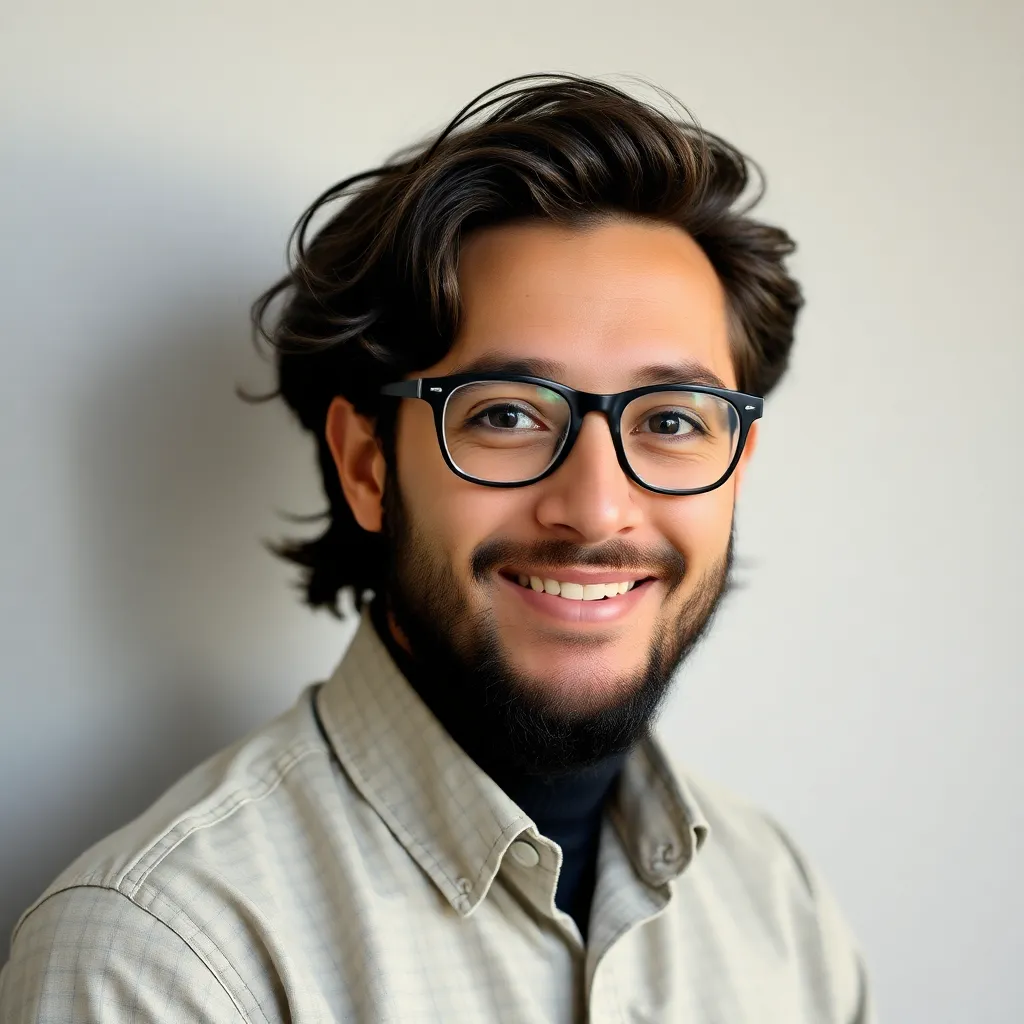
Breaking News Today
May 11, 2025 · 6 min read
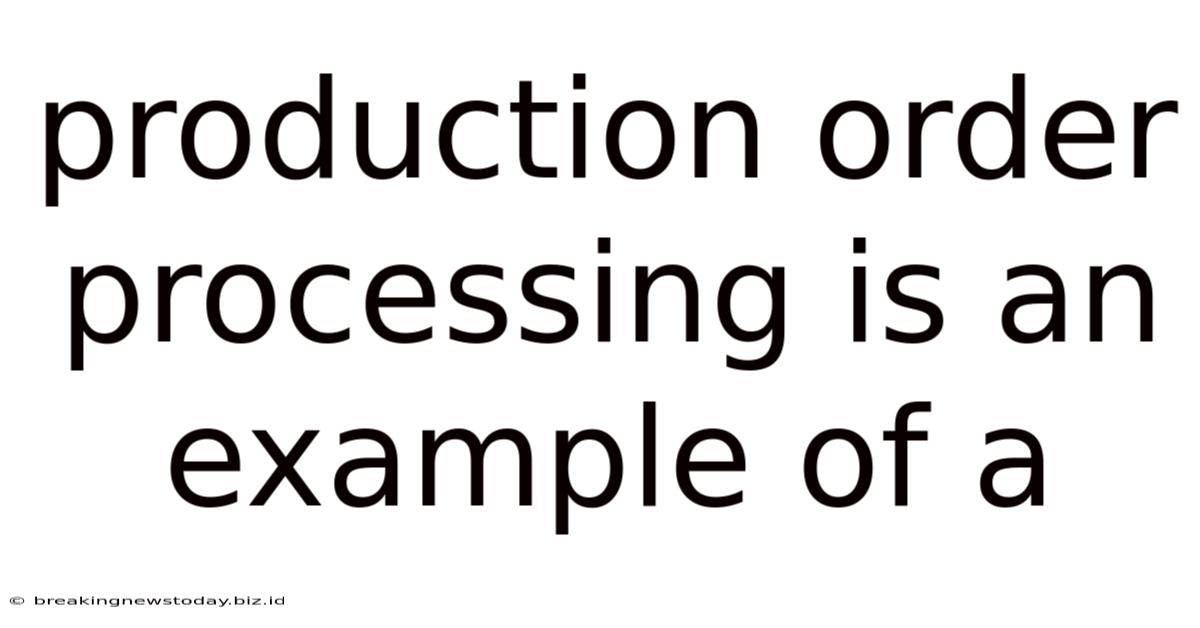
Table of Contents
Production Order Processing is an Example of a Manufacturing Execution System (MES)
Production order processing is a critical component of a larger system designed to optimize manufacturing operations. It's not a standalone process, but rather a vital function within a more comprehensive system. That system, most accurately, is a Manufacturing Execution System (MES). This article will delve deep into the role of production order processing within the MES framework, exploring its intricacies, benefits, and integration with other essential manufacturing processes.
Understanding Manufacturing Execution Systems (MES)
Before we dive into the specifics of production order processing, it's crucial to understand what an MES is and how it functions. An MES is a sophisticated software system that sits between the enterprise resource planning (ERP) system and the shop floor. It acts as a bridge, translating high-level business plans from the ERP into actionable instructions for manufacturing equipment and workers on the shop floor. Think of it as the central nervous system of a manufacturing operation, orchestrating all aspects of production.
Key functionalities of an MES include:
- Production Scheduling and Sequencing: Optimizing the production schedule based on available resources, due dates, and material availability.
- Production Order Management: Creating, releasing, tracking, and managing production orders throughout their lifecycle. This is where production order processing plays a critical role.
- Shop Floor Control: Monitoring and controlling manufacturing processes in real-time, providing alerts and feedback on performance.
- Quality Management: Tracking and managing quality data, ensuring adherence to quality standards.
- Material Management: Tracking the flow of materials through the production process, minimizing waste and maximizing efficiency.
- Labor Management: Tracking employee time and attendance, productivity, and skill sets.
- Data Acquisition and Analysis: Collecting and analyzing data from various sources to identify areas for improvement and optimization.
- Reporting and Analytics: Providing management with real-time visibility into production performance, allowing for data-driven decision-making.
Production Order Processing: The Heart of MES
Production order processing is the core function within an MES responsible for managing the entire lifecycle of a production order. It encompasses all the steps involved in creating, releasing, tracking, and completing a production order. This process is crucial for ensuring that the right materials are used, the correct steps are followed, and the finished goods meet quality standards.
Stages of Production Order Processing:
-
Order Creation and Planning: This initial stage involves creating a detailed production order based on customer demand, sales forecasts, or inventory levels. The order includes specifications such as product type, quantity, materials required, and due dates. Detailed planning involves resource allocation, scheduling, and potential bottleneck identification.
-
Material Requirements Planning (MRP): Integrated with the MES, the MRP system ensures that sufficient materials are available to meet the production order requirements. This may involve checking inventory levels, placing purchase orders for raw materials, and scheduling inbound deliveries. Efficient MRP minimizes material shortages and delays.
-
Order Release: Once all materials are confirmed available and the schedule is finalized, the production order is released to the shop floor. This triggers the initiation of the manufacturing process. This release often involves automated instructions sent directly to machines and work centers.
-
Work-in-Progress (WIP) Tracking: Throughout the manufacturing process, the MES tracks the progress of each production order. This allows for real-time visibility into the status of each order, pinpointing potential delays or bottlenecks. Detailed tracking enables precise monitoring of cycle times and overall production efficiency.
-
Quality Control and Inspection: At various stages, the MES facilitates quality control checks and inspections. Real-time data collection ensures that products meet the required quality standards, reducing the risk of defects and rework. This involves integration with quality management systems and automated inspection equipment.
-
Order Completion: Once the production order is completed, the MES records the completion time, quantities produced, and any associated costs. This data is crucial for cost accounting and performance analysis. The system may also automatically generate reports and notifications regarding completion.
-
Inventory Management and Updates: The MES updates inventory levels upon completion of the production order, reflecting the newly produced goods. This ensures accurate inventory records, facilitating efficient supply chain management.
Benefits of Efficient Production Order Processing within an MES
Implementing a robust production order processing system within an MES offers a myriad of benefits to manufacturers, including:
-
Improved Production Efficiency: Streamlined workflows, automated processes, and real-time monitoring significantly enhance overall production efficiency. Reducing downtime, minimizing waste, and optimizing resource utilization are key outcomes.
-
Reduced Production Costs: Optimized resource allocation, minimized waste, and improved quality reduce overall production costs. This leads to higher profit margins and increased competitiveness.
-
Enhanced Quality Control: Real-time monitoring and automated inspections help ensure consistent product quality, reducing defects and rework. This improves customer satisfaction and minimizes losses associated with quality issues.
-
Improved On-Time Delivery: Accurate scheduling, real-time tracking, and proactive identification of potential delays contribute to improved on-time delivery performance. Meeting deadlines strengthens customer relationships and enhances reputation.
-
Better Inventory Management: Accurate tracking of materials and finished goods optimizes inventory levels, minimizing storage costs and reducing the risk of stockouts or overstocking. This optimizes working capital.
-
Increased Transparency and Visibility: Real-time data and reporting provide complete transparency into the production process, enabling informed decision-making and proactive problem-solving. This facilitates better collaboration and communication across different departments.
-
Improved Data-Driven Decision Making: The MES collects vast amounts of data which, when analyzed, provides valuable insights into production performance. This allows for data-driven decisions for continuous improvement.
-
Enhanced Scalability and Flexibility: A well-designed MES can easily adapt to changing production needs and scale to accommodate growth. This adaptability is vital in dynamic market conditions.
Integrating Production Order Processing with Other MES Modules
Production order processing is not an isolated function within an MES; it interacts closely with other modules to create a cohesive and efficient system. These interactions are vital for seamless manufacturing operations.
-
Integration with ERP: The MES receives high-level production plans and data from the ERP system, translating them into executable instructions for the shop floor. This ensures alignment between business strategy and shop floor execution.
-
Integration with SCADA (Supervisory Control and Data Acquisition): The MES often integrates with SCADA systems to monitor and control manufacturing equipment in real-time. This enables automated data collection and direct control of production processes.
-
Integration with Quality Management Systems: The MES facilitates quality control and inspection throughout the production process, ensuring adherence to quality standards. This ensures efficient quality control checks.
-
Integration with Supply Chain Management Systems: The MES coordinates the flow of materials throughout the production process, ensuring timely delivery of raw materials and efficient management of finished goods inventory. This optimizes material flow.
-
Integration with Warehouse Management Systems (WMS): The MES interacts with WMS to track materials and products throughout the warehouse, ensuring efficient storage and retrieval. This improves warehouse operations.
Conclusion: Production Order Processing – A Cornerstone of Modern Manufacturing
Production order processing is undeniably a cornerstone of modern manufacturing, acting as a vital function within the broader context of a Manufacturing Execution System (MES). Its efficient implementation ensures improved efficiency, reduced costs, enhanced quality, and increased customer satisfaction. By leveraging the power of an integrated MES, manufacturers can streamline their operations, optimize their resources, and achieve a competitive advantage in today's dynamic marketplace. Investing in a robust and well-integrated MES, with its core functionality of effective production order processing, is a crucial step toward achieving operational excellence in manufacturing.
Latest Posts
Latest Posts
-
A Partial Bath Includes Washing A Residents
May 12, 2025
-
Which Of The Following Describes A Net Lease
May 12, 2025
-
Nurse Logic 2 0 Knowledge And Clinical Judgment
May 12, 2025
-
Panic Disorder Is Characterized By All Of The Following Except
May 12, 2025
-
Positive Individual Traits Can Be Taught A True B False
May 12, 2025
Related Post
Thank you for visiting our website which covers about Production Order Processing Is An Example Of A . We hope the information provided has been useful to you. Feel free to contact us if you have any questions or need further assistance. See you next time and don't miss to bookmark.