Safety Stock Exists For Which Of The Following Reasons
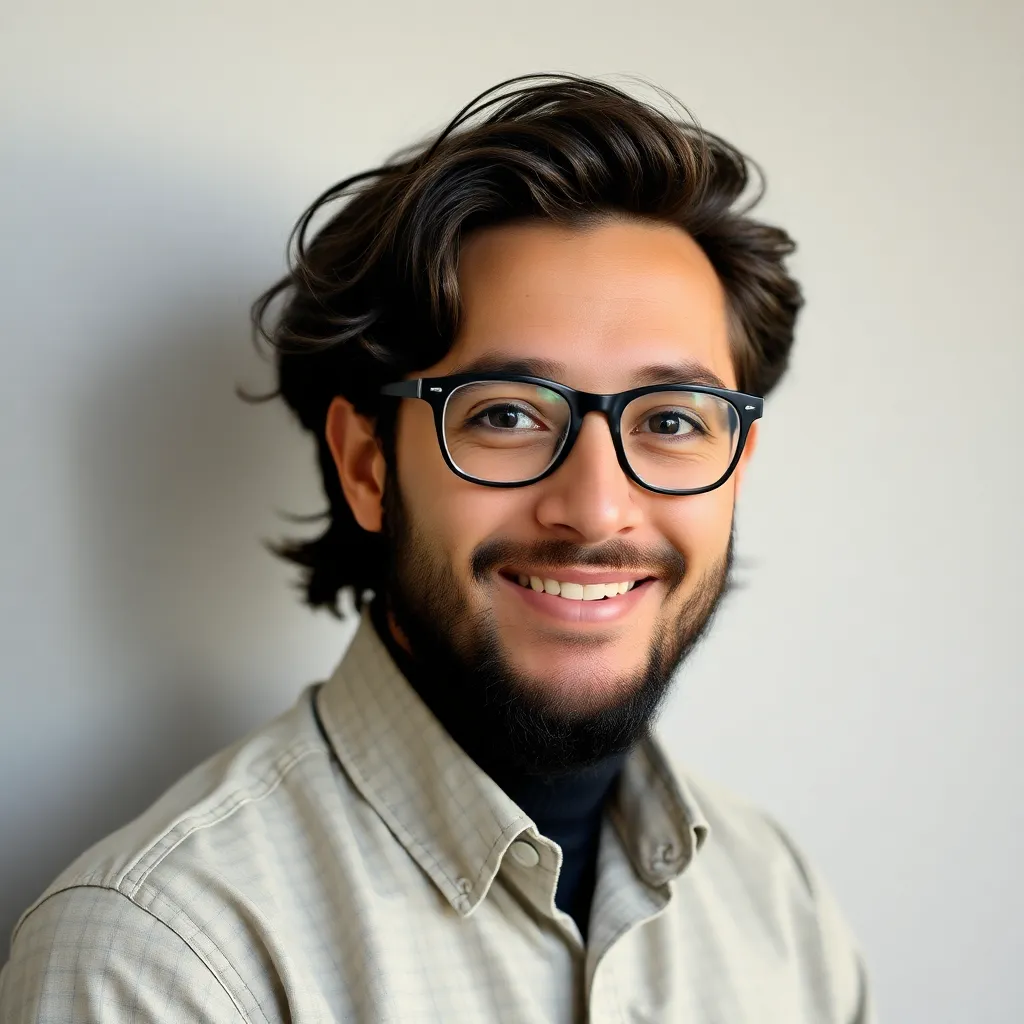
Breaking News Today
Apr 06, 2025 · 6 min read

Table of Contents
Safety Stock: Why It Exists and How to Optimize It
Safety stock, that extra buffer of inventory held beyond what's expected for immediate demand, is a crucial component of effective inventory management. While it might seem like an unnecessary expense, its existence is justified by several critical reasons, all aimed at mitigating risks and ensuring business continuity. Understanding these reasons is fundamental to optimizing safety stock levels and avoiding both stockouts and excessive holding costs.
The Primary Reasons for Holding Safety Stock
The need for safety stock stems from the inherent uncertainties within supply chains and demand forecasting. These uncertainties can manifest in various ways, each necessitating a safety net to protect against disruptions. Let's delve into the core reasons:
1. Demand Variability: The Unpredictable Nature of Customer Needs
This is arguably the most significant reason for holding safety stock. Even with sophisticated forecasting models, predicting customer demand with perfect accuracy is practically impossible. Demand fluctuates due to numerous factors:
- Seasonality: Certain products experience predictable peaks and troughs based on time of year, holidays, or weather patterns. Safety stock helps cover these surges in demand.
- Trends: Market trends can unexpectedly shift customer preferences, leading to unexpected spikes or dips in demand. A new competitor, a viral marketing campaign, or even a change in consumer behavior can significantly impact sales.
- Random Fluctuations: There's always an element of random variation in demand. These unpredictable fluctuations can be difficult to forecast and require a buffer to avoid stockouts.
- Promotional Activities: Sales promotions and marketing campaigns, while designed to boost sales, can also lead to unpredictable surges in demand, requiring extra inventory to meet the increased customer orders.
Example: A clothing retailer knows that winter coats will sell more in the fall and winter months. They use forecasting to estimate demand, but safety stock accounts for the possibility that actual demand might exceed their forecast due to unexpectedly cold weather or a successful marketing campaign.
2. Lead Time Variability: The Unpredictable Time to Replenishment
Lead time – the time between placing an order with a supplier and receiving the goods – is another major source of uncertainty. Unexpected delays can stem from:
- Supplier Issues: Supplier production problems, transportation delays, or quality control issues can all significantly extend lead times. A supplier experiencing a fire or strike will inevitably impact delivery times.
- Transportation Delays: Unexpected traffic congestion, weather events, port congestion, or even driver shortages can all disrupt the timely delivery of goods. International shipping is particularly susceptible to such delays.
- Customs and Regulatory Issues: International shipments can face unexpected delays due to customs inspections, regulatory changes, or documentation issues.
- Logistics Problems: Inefficiencies within the company's own logistics network can also contribute to lead time variability. This could involve issues with warehousing, order processing, or internal transportation.
Example: A manufacturer relies on a specific component from an overseas supplier. They account for the typical lead time in their planning, but safety stock mitigates the risk of production delays should a shipment be delayed due to a storm or port congestion.
3. Supply Chain Disruptions: The Unexpected and Unforeseeable
Beyond lead time variability, unforeseen events can completely disrupt the supply chain:
- Natural Disasters: Earthquakes, floods, hurricanes, and other natural disasters can severely impact the ability to source materials or transport goods.
- Political Instability: Political unrest, trade wars, or changes in government regulations can disrupt supply chains, particularly those that rely on international trade.
- Pandemics: Global health crises, like the COVID-19 pandemic, have demonstrated the fragility of supply chains and the need for robust safety stock strategies.
- Supplier Bankruptcy: A supplier facing financial difficulties can suddenly cease operations, leaving companies without a critical source of materials.
Example: A company that relies on a single supplier for a crucial raw material might hold a substantial amount of safety stock to protect against supplier bankruptcy or a natural disaster affecting the supplier's facility.
4. Obsolescence and Perishability: The Time-Sensitive Nature of Some Goods
Certain products have limited shelf lives due to obsolescence or perishability:
- Technological Products: Rapid technological advancements can quickly render products obsolete, making it difficult to sell older inventory.
- Fashion Items: Seasonal trends and changing fashion tastes mean that clothing and accessories can quickly become outdated.
- Food and Perishable Goods: Food products, pharmaceuticals, and other perishable items have limited shelf lives and require careful management to avoid spoilage and waste.
Example: A retailer selling electronics needs to consider the rate of obsolescence for their products. Safety stock in this case might be lower due to the risk of unsold items becoming obsolete and worthless.
Optimizing Safety Stock Levels: Finding the Sweet Spot
While the reasons above clearly highlight the importance of safety stock, holding excessive inventory is costly. The goal is to find the optimal safety stock level that balances the risk of stockouts with the cost of holding extra inventory. Several factors influence this optimization:
- Service Level: This represents the desired probability of meeting customer demand. A higher service level requires more safety stock but reduces the risk of stockouts.
- Demand Variability: Higher demand variability necessitates higher safety stock levels to account for unpredictable fluctuations.
- Lead Time Variability: Greater uncertainty in lead times also requires larger safety stock levels to protect against delays.
- Holding Costs: The cost of storing and insuring inventory, including warehouse space, insurance, and potential obsolescence, influences the acceptable level of safety stock.
- Stockout Costs: The cost associated with not meeting customer demand, including lost sales, customer dissatisfaction, and potential damage to brand reputation, is crucial in determining the appropriate safety stock level.
Strategies for Optimization:
- Accurate Forecasting: Employ sophisticated forecasting techniques, incorporating historical data, seasonality, trends, and market insights to improve demand prediction accuracy.
- Improved Supply Chain Visibility: Enhance communication and collaboration with suppliers to improve lead time predictability and anticipate potential disruptions.
- Supplier Diversification: Reduce reliance on single suppliers to mitigate the risk of supply chain disruptions.
- Efficient Inventory Management Systems: Utilize technology such as Enterprise Resource Planning (ERP) systems to track inventory levels, manage orders, and optimize stock replenishment.
- Regular Inventory Reviews: Conduct periodic reviews of safety stock levels to adjust them based on actual demand, lead times, and market conditions.
- ABC Analysis: Categorize inventory items based on their value and demand. Higher-value items typically require more careful management and higher safety stock levels.
Conclusion: A Balancing Act Between Risk and Cost
Safety stock is not merely a precautionary measure; it's a strategic tool for mitigating risks inherent in the supply chain and ensuring business continuity. While carrying extra inventory incurs holding costs, the costs of stockouts—lost sales, dissatisfied customers, and damaged reputation—can be far more substantial. The key is to find the optimal balance, leveraging advanced forecasting techniques, robust supply chain management practices, and effective inventory control systems to minimize costs while maintaining an appropriate safety net. Understanding the underlying reasons for holding safety stock is the first step towards optimizing inventory levels and achieving a truly efficient and resilient supply chain.
Latest Posts
Latest Posts
-
What Is The Best Tool For Guaranteeing Return Business
Apr 08, 2025
-
Mr Goodman Is Exhibiting Signs And Symptoms Of Which Condition
Apr 08, 2025
-
Are Identified As Ports 49152 Through 65535
Apr 08, 2025
-
Non Occupational Disability Coverage Is Designed For
Apr 08, 2025
-
Shows Brain Activity By Tracking Glucose Absorption
Apr 08, 2025
Related Post
Thank you for visiting our website which covers about Safety Stock Exists For Which Of The Following Reasons . We hope the information provided has been useful to you. Feel free to contact us if you have any questions or need further assistance. See you next time and don't miss to bookmark.