Serviceability Is The Dimension Of Quality That Refers To _____.
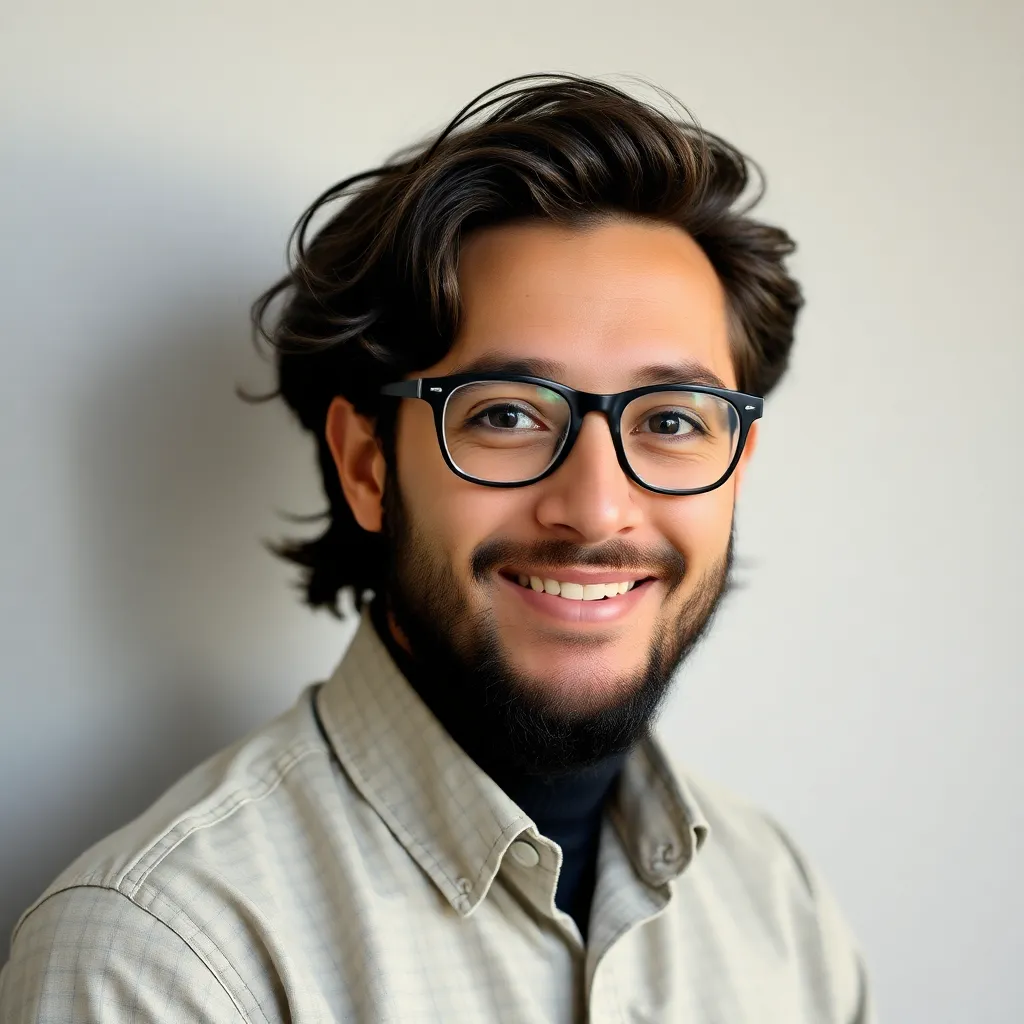
Breaking News Today
Mar 16, 2025 · 6 min read
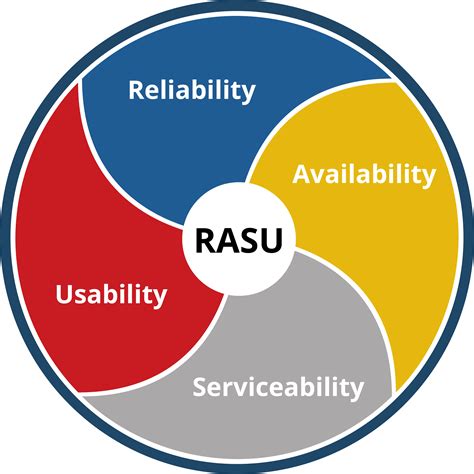
Table of Contents
Serviceability: The Unsung Hero of Product Quality
Serviceability is the dimension of quality that refers to the ease and cost of maintaining and repairing a product. It's often overlooked in the rush to focus on features and aesthetics, but it's a crucial factor influencing a product's overall success and a customer's perception of its value. This article delves deep into serviceability, exploring its various facets, its impact on customer satisfaction, and strategies for designing for better serviceability.
Understanding Serviceability: Beyond Just Repairs
While often equated solely with repair ease, serviceability encompasses a much broader spectrum. It's about the entire lifecycle of a product's maintenance, from preventative measures to troubleshooting and eventual disposal. Key aspects include:
1. Ease of Access: Getting to the Problem
The very first step in servicing a product is accessing the components that need attention. A poorly designed product might require extensive disassembly, potentially causing further damage in the process. High serviceability emphasizes easy access to key parts, minimizing the time and effort required for maintenance or repair. This could involve strategically placed access panels, modular designs, or the use of readily removable components.
2. Simplicity of Repair: Straightforward Fixes
Repair procedures should be intuitive and straightforward. This requires clear and concise documentation, readily available diagrams, and the use of standard, readily available tools. Complex repair processes often lead to increased downtime, higher repair costs, and potential for errors during repair. A well-designed, highly serviceable product will allow for repairs to be completed quickly and effectively, even by non-experts.
3. Availability of Parts: Keeping it Running
The availability of replacement parts is crucial for maintaining a product's serviceability. Products with readily available parts, whether from the manufacturer or authorized third-party suppliers, ensure that repairs can be carried out promptly. Long lead times for parts can lead to significant downtime and increased operational costs. Therefore, strategic planning for parts management is essential in ensuring long-term serviceability.
4. Diagnostics and Troubleshooting: Finding the Fault
Easy diagnosis and troubleshooting are crucial aspects of serviceability. This involves providing clear diagnostic indicators, readily accessible troubleshooting guides, and perhaps even built-in diagnostic tools. A product with poor diagnosability forces technicians to spend significant time identifying the problem, increasing the overall cost and duration of the repair. Effective diagnostic features can significantly improve efficiency and reduce repair time.
5. Cost-Effectiveness: Balancing Value and Repair
Serviceability should be considered throughout the product's lifecycle, from design to disposal. High serviceability aims to minimize the total cost of ownership by reducing repair time, part replacement costs, and downtime. While some initial investment in design for serviceability might be needed, the long-term cost savings often outweigh the initial investment.
The Impact of Serviceability on Customer Satisfaction
Serviceability significantly impacts customer satisfaction. A product that is easy to maintain and repair instills confidence and reduces frustration. Customers value products that are reliable and can be quickly restored to operational condition when problems occur.
- Reduced Downtime: Easy repairs minimize downtime, keeping customers productive and happy.
- Lower Repair Costs: Simple repairs translate into lower repair bills, adding to customer satisfaction.
- Increased Product Lifetime: Serviceable products tend to last longer, offering greater value to the customer.
- Improved Customer Loyalty: Positive experiences with serviceability lead to increased customer loyalty and positive word-of-mouth.
- Enhanced Brand Reputation: A reputation for producing serviceable products enhances brand credibility and trustworthiness.
Designing for Serviceability: Proactive Strategies
Designing for serviceability isn't an afterthought; it's an integral part of the entire product development process. Several key strategies can enhance a product's serviceability:
1. Modular Design: Easy Component Replacement
Modular designs make it easier to identify and replace faulty components without requiring complete disassembly of the product. This significantly simplifies repairs and reduces repair time. The use of standardized modules also improves the availability of replacement parts.
2. Standardized Components: Commonality for Ease
Using standardized, readily available components minimizes the need for specialized tools and parts. This reduces repair costs and speeds up the repair process. Open-source hardware can be particularly beneficial in this regard.
3. Clear and Accessible Documentation: Guiding Repair
Comprehensive and easily accessible documentation, including diagrams, instructions, and troubleshooting guides, simplifies the repair process for both technicians and end-users. Well-structured documentation improves repair efficiency and reduces errors. Multimedia tutorials can enhance understanding.
4. Diagnostic Features: Pinpointing the Problem
Built-in diagnostic features, such as self-diagnostic tests and error codes, can significantly speed up troubleshooting. These features allow technicians to quickly identify the root cause of the problem, reducing repair time and costs. Remote diagnostics are becoming increasingly common.
5. Robust Materials and Construction: Durable Design
Using robust and durable materials in the product's construction extends its lifespan and reduces the likelihood of failures. This reduces the need for frequent repairs and improves the overall serviceability of the product. Careful consideration of material selection is paramount.
6. Environmental Considerations: Sustainable Disposal
Serviceability extends to the end-of-life stage of a product. Designing for easy disassembly and recycling minimizes environmental impact and allows for the recovery of valuable materials. Sustainable design practices are increasingly important in today's environmentally conscious market.
Serviceability in Different Industries
Serviceability considerations vary across industries, reflecting the specific requirements and constraints of each sector.
1. Electronics: Modular Designs and Easy Access
In the electronics industry, serviceability often centers around modular designs, accessible components, and readily available replacement parts. The increasing complexity of electronics necessitates careful consideration of serviceability to minimize repair costs and downtime.
2. Automotive: Diagnoses and Specialized Tools
The automotive industry relies on advanced diagnostics and specialized tools for repair. Serviceability in this sector focuses on efficient diagnostics, access to critical components, and the availability of specialized parts.
3. Medical Devices: Sterility and Safety
Medical device serviceability prioritizes sterility, safety, and regulatory compliance. Repairs must adhere to strict protocols to ensure the continued safe operation of the devices.
4. Industrial Machinery: Robustness and Accessibility
Industrial machinery demands high robustness and easy access for maintenance and repair. Serviceability in this sector focuses on minimizing downtime and ensuring the safety of maintenance personnel.
Conclusion: Serviceability – A Key Differentiator
Serviceability is a critical dimension of quality that often determines a product's long-term success and customer satisfaction. By proactively designing for serviceability, manufacturers can reduce repair costs, improve customer loyalty, and enhance their brand reputation. It's not simply about fixing things; it's about building trust, ensuring product longevity, and minimizing the total cost of ownership. Ignoring serviceability is a missed opportunity to deliver superior value and build a strong competitive advantage in today's market. In the long run, prioritizing serviceability is a strategic investment that yields significant returns. Embrace it as a key differentiator and watch your products—and your business—thrive.
Latest Posts
Latest Posts
-
In Which Situation Would It Be Legal To Deliver Alcohol
May 09, 2025
-
What Is The Ability To Do Work
May 09, 2025
-
A Food Borne Parasite Found In Under Cooked Pork Is
May 09, 2025
-
Blends Digital Elements With The Physical World Around You
May 09, 2025
-
Are You Smarter Than A Kindergartener Quiz
May 09, 2025
Related Post
Thank you for visiting our website which covers about Serviceability Is The Dimension Of Quality That Refers To _____. . We hope the information provided has been useful to you. Feel free to contact us if you have any questions or need further assistance. See you next time and don't miss to bookmark.