Silicon Is Widely Used As A Semiconductor Because It
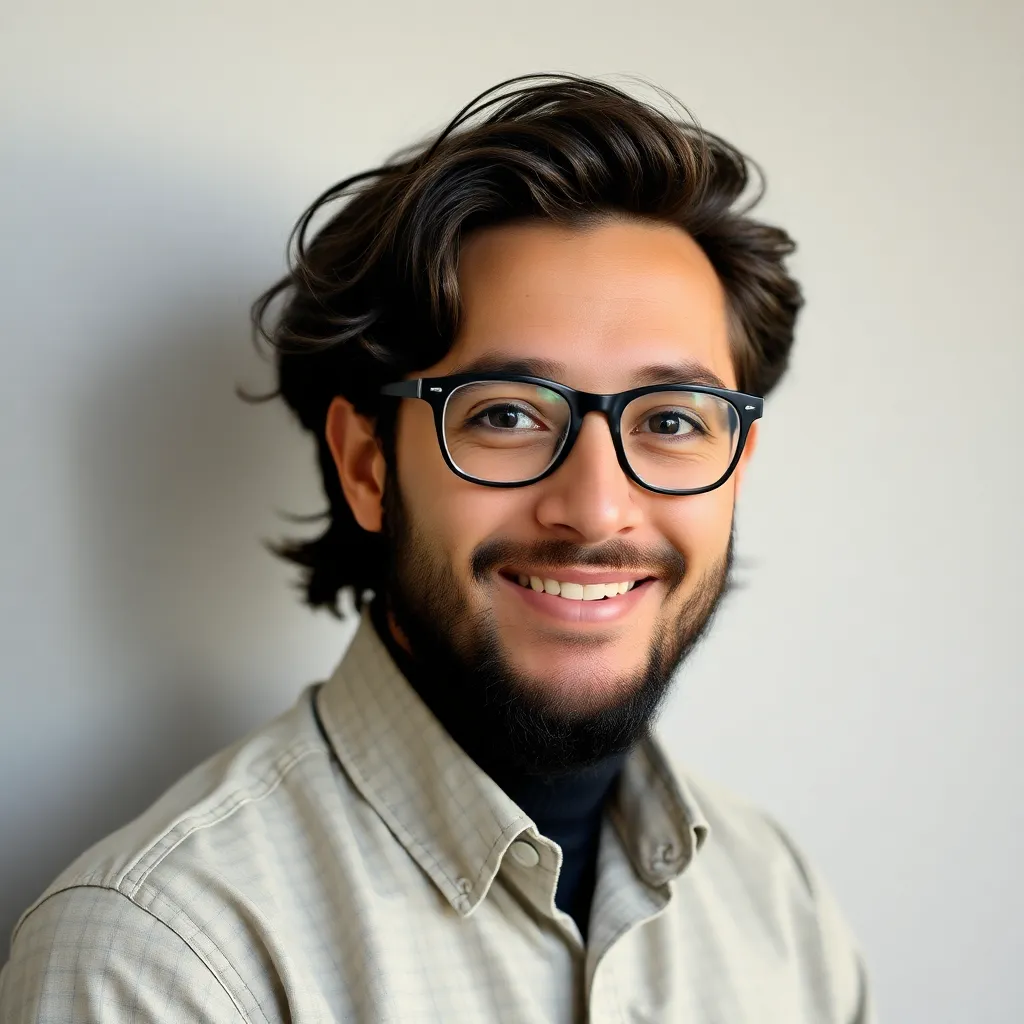
Breaking News Today
Apr 27, 2025 · 6 min read

Table of Contents
Silicon: The Unsung Hero of the Semiconductor World
Silicon's dominance in the semiconductor industry isn't accidental; it's a testament to its unique properties and the ingenious ways we've learned to harness them. While other materials exhibit semiconducting behavior, silicon reigns supreme due to a potent combination of factors that make it incredibly versatile, cost-effective, and readily scalable for mass production. Let's delve into the reasons why silicon is the undisputed champion of the semiconductor arena.
Abundant and Earth-Friendly: The Economic Advantage
One of the most compelling reasons for silicon's widespread adoption is its abundance. Silicon is the second most abundant element in the Earth's crust, after oxygen. This readily available resource translates directly into low production costs. Unlike some rarer elements used in specialized semiconductor applications, silicon's plentiful supply makes it economically viable to manufacture on a massive scale, fueling the global electronics industry. The environmental impact is also significantly reduced compared to mining rarer materials, making silicon a more sustainable choice.
The Cost-Effectiveness Factor
The cost-effectiveness of silicon extends beyond its abundance. The processing techniques used to purify and refine silicon into semiconductor-grade material are well-established and highly optimized. Decades of research and development have led to efficient and scalable manufacturing processes, further driving down the cost per unit. This affordability makes silicon-based electronics accessible to a global market, driving innovation and technological advancement across various sectors.
Exceptional Semiconducting Properties: The Technical Prowess
Beyond its economic advantages, silicon possesses crucial intrinsic properties that make it exceptionally suitable for semiconductor applications. Its inherent semiconducting nature allows for precise control over its electrical conductivity, a fundamental requirement for building transistors and integrated circuits.
Band Gap: The Key to Control
Silicon's band gap, the energy difference between its valence and conduction bands, is optimally situated for room-temperature operation. This means that at typical operating temperatures, silicon can effectively switch between conducting and non-conducting states, allowing for the creation of highly efficient transistors. A wider band gap might lead to higher power efficiency, but it would necessitate higher operating temperatures, making it less practical for many applications. A narrower band gap, on the other hand, would result in higher leakage currents, hindering performance and efficiency. Silicon's band gap strikes the perfect balance.
High Purity and Doping: Tailoring Conductivity
The ability to achieve extremely high purity levels in silicon is paramount. Impurities, even in minute quantities, can drastically alter silicon's conductivity. Sophisticated purification techniques, like the Czochralski process, allow for the production of silicon crystals with an incredibly low concentration of impurities. This high purity is crucial for controlling the silicon's electrical behavior.
The process of doping introduces controlled amounts of impurities (dopants) into the silicon crystal lattice. These dopants, typically elements like phosphorus (n-type) or boron (p-type), alter the conductivity of the silicon, creating regions with different charge carrier concentrations. This precise control over conductivity is fundamental to the operation of transistors and integrated circuits.
Excellent Thermal Conductivity: Managing Heat
The generation of heat is an inevitable byproduct of the operation of electronic devices. Silicon's relatively high thermal conductivity helps dissipate this heat effectively, preventing overheating and maintaining optimal performance. This thermal management is critical, especially in high-power applications where heat buildup can cause device failure. Advanced packaging techniques and heat sinks further enhance this thermal management capacity.
Scalability and Compatibility: The Manufacturing Miracle
The remarkable scalability of silicon manufacturing is a cornerstone of its success. The ability to produce silicon wafers with ever-increasing diameters has allowed for the relentless miniaturization of transistors, driving Moore's Law and fueling exponential increases in computing power. This miniaturization has been achieved through continuous advancements in photolithography and other fabrication techniques.
Photolithography: The Art of Miniaturization
Photolithography, a fundamental process in semiconductor manufacturing, relies on light to create intricate patterns on silicon wafers. Continuous improvements in this technique, including the transition from ultraviolet (UV) to extreme ultraviolet (EUV) lithography, have enabled the creation of incredibly small and densely packed transistors, pushing the boundaries of miniaturization. Each generation of lithography allows for a significant increase in the number of transistors that can be integrated onto a single chip.
Compatibility with Other Materials: Building Complex Systems
Silicon's compatibility with other materials is another key factor. It readily forms stable interfaces with various insulators and metals, crucial for creating complex integrated circuits. This compatibility enables the integration of diverse components – transistors, capacitors, resistors, and interconnects – into a single silicon chip, allowing for the creation of sophisticated electronic systems on a microscopic scale.
Silicon's Limitations and the Search for Alternatives
Despite its widespread success, silicon does have limitations. Its relatively low electron mobility compared to some other materials restricts its performance in high-frequency applications. Moreover, as transistors continue to shrink, quantum mechanical effects become more pronounced, potentially limiting further miniaturization based on silicon technology.
These limitations have spurred significant research into alternative semiconductor materials like gallium nitride (GaN) and silicon carbide (SiC) for specific applications requiring higher electron mobility or higher operating temperatures. However, the cost and complexity of manufacturing these alternative materials currently pose challenges to their widespread adoption.
The Continued Reign of Silicon: A Look Ahead
While alternative materials are emerging, silicon's position as the dominant semiconductor material remains firmly entrenched. Continuous advancements in silicon processing technologies, including novel doping techniques and improved thermal management strategies, continue to extend its performance capabilities. The immense infrastructure built around silicon manufacturing, coupled with its cost-effectiveness and well-established fabrication processes, makes it unlikely to be displaced entirely in the foreseeable future.
Instead of complete replacement, a more likely scenario is a co-existence, with silicon continuing to dominate in many applications while alternative materials find niches in specific high-performance or specialized areas. The future of electronics likely involves a synergistic approach, leveraging the strengths of both silicon and emerging materials to develop ever-more powerful and efficient devices.
Beyond Transistors: Silicon's Diverse Applications
Silicon's applications extend far beyond transistors. Its versatile properties find use in various technologies, highlighting its ubiquitous nature in modern life:
Solar Cells: Harnessing Solar Energy
Silicon's ability to absorb sunlight and convert it into electricity makes it the dominant material in photovoltaic solar cells. The high abundance and cost-effectiveness of silicon make solar power generation more accessible, contributing significantly to sustainable energy solutions.
Sensors: Sensing the World Around Us
Silicon's sensitivity to various physical and chemical stimuli makes it ideal for creating sensors. Silicon-based sensors are used extensively in various applications, from pressure and temperature sensors to gas detectors and accelerometers found in smartphones and other electronic devices.
MEMS (Microelectromechanical Systems): Microscopic Machines
Silicon's mechanical properties, combined with its ability to be precisely etched and shaped, make it a perfect material for creating microelectromechanical systems (MEMS). MEMS devices are microscopic machines with a wide range of applications, including accelerometers, gyroscopes, and microfluidic devices.
Conclusion: Silicon's Enduring Legacy
Silicon's dominance in the semiconductor industry is a result of a unique combination of factors. Its abundance, cost-effectiveness, exceptional semiconducting properties, scalability, and compatibility with other materials have propelled it to the forefront of electronics. While alternative materials are emerging to address specific limitations, silicon's enduring legacy is assured, as it continues to shape the technological landscape for the foreseeable future. The ongoing advancements in silicon technology, coupled with its established infrastructure and widespread adoption, ensure its continued relevance and contribution to innovation for generations to come. The unsung hero of the digital age, silicon, continues to power our world.
Latest Posts
Latest Posts
-
Which Is The Most Restrictive Type Of Healthcare Plan
Apr 27, 2025
-
Indicate Whether The Given Transfusion Is Compatible Or Not Compatible
Apr 27, 2025
-
If Your Drivers License Suspended You May Drive Only
Apr 27, 2025
-
In The Anthropological Study Of Religion A Revitalization Ritual Is
Apr 27, 2025
-
Lord Of The Flies Ch 1 Summary
Apr 27, 2025
Related Post
Thank you for visiting our website which covers about Silicon Is Widely Used As A Semiconductor Because It . We hope the information provided has been useful to you. Feel free to contact us if you have any questions or need further assistance. See you next time and don't miss to bookmark.