Storage And Handling Training Should Be Completed
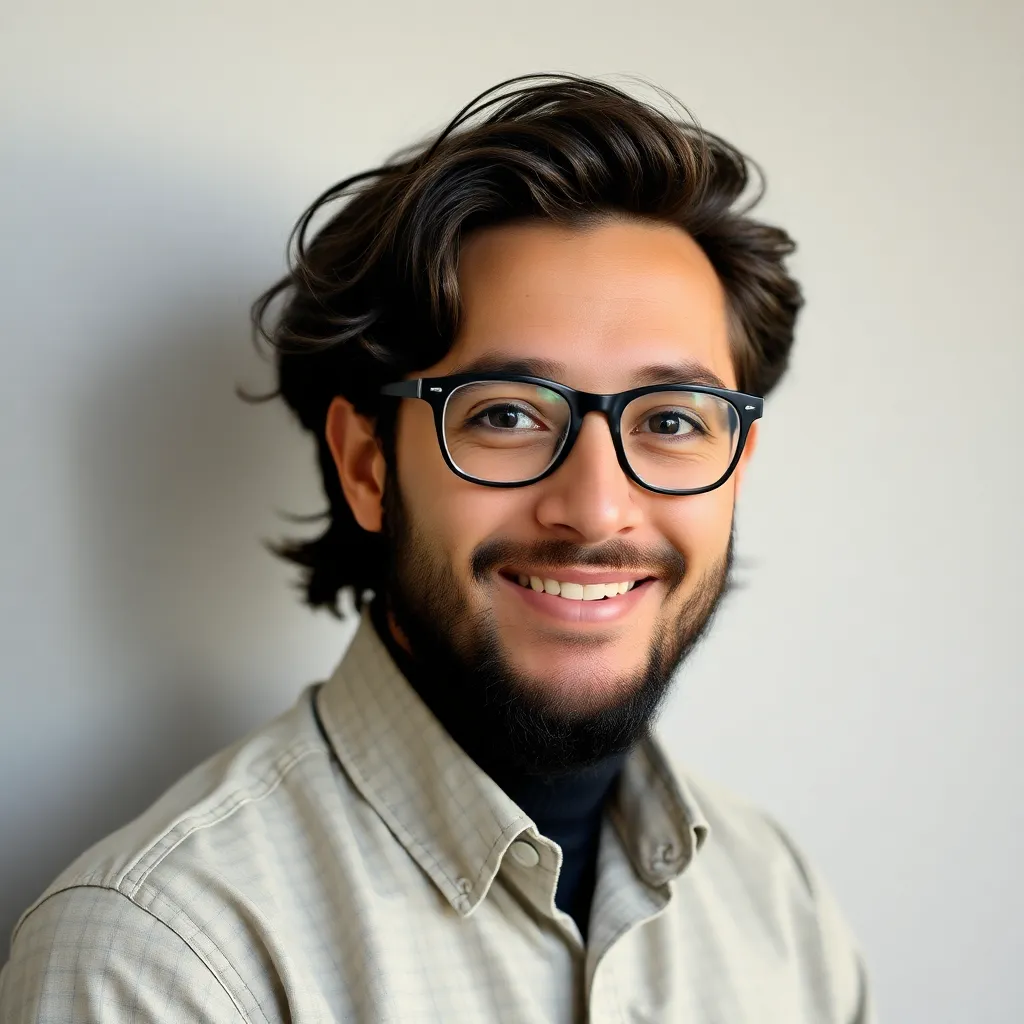
Breaking News Today
May 09, 2025 · 6 min read
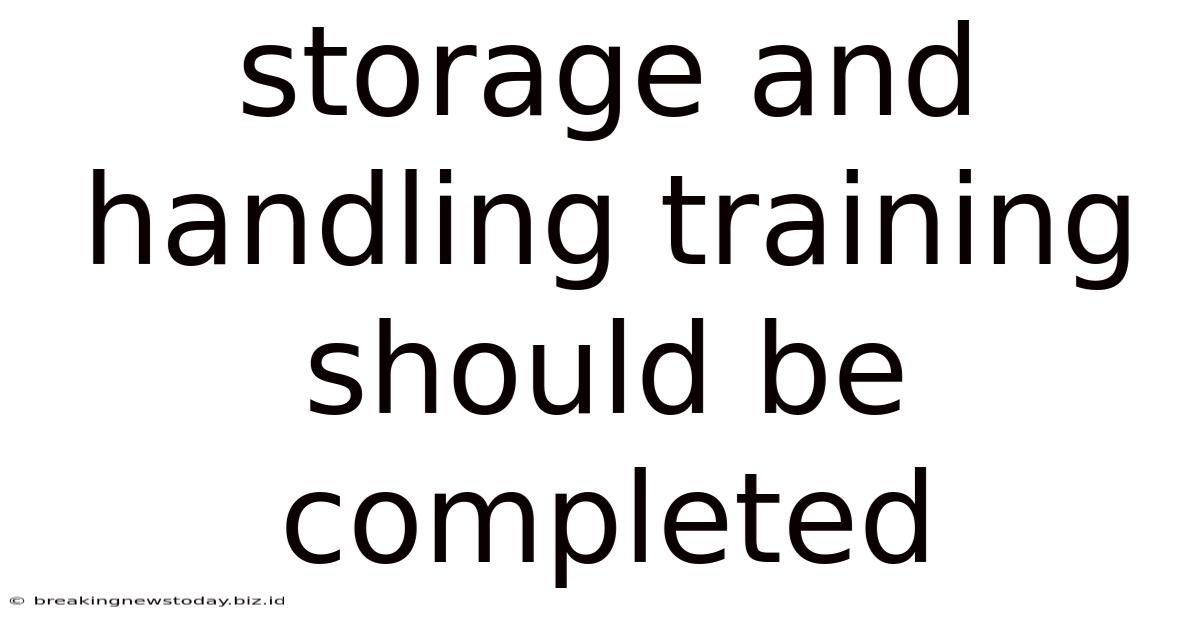
Table of Contents
Storage and Handling Training: Why It's Non-Negotiable for Your Business
Storage and handling of materials, goods, and equipment are critical aspects of any successful business operation, regardless of industry. Improper storage and handling can lead to a myriad of problems, including damaged goods, workplace injuries, lost productivity, and even legal liabilities. Therefore, comprehensive storage and handling training is not just a good idea – it's a non-negotiable requirement for maintaining a safe, efficient, and profitable business. This article delves deep into the importance, key components, and practical implementation of effective storage and handling training programs.
The High Cost of Inadequate Storage and Handling
Before diving into the details of training, let's highlight the significant consequences of neglecting proper storage and handling procedures. These costs extend far beyond simply replacing damaged goods:
1. Financial Losses:
- Damaged Goods: Improper stacking, inadequate protection from the elements, or poor material handling techniques can lead to significant product damage, resulting in direct financial losses due to waste and replacement costs. This is particularly relevant for businesses dealing with fragile or perishable goods.
- Reduced Efficiency: Inefficient storage systems and poor handling practices lead to wasted time searching for items, increased material handling times, and potential bottlenecks in the production or distribution process.
- Increased Insurance Premiums: A history of accidents or incidents related to poor storage and handling practices will almost certainly lead to higher insurance premiums, adding to your operational costs.
2. Safety and Health Hazards:
- Workplace Injuries: Improper lifting techniques, unsecured loads, and cluttered workspaces contribute significantly to workplace accidents, including strains, sprains, back injuries, and even more severe traumas. These injuries result in lost workdays, medical expenses, and potential legal ramifications.
- Health Risks: Inadequate storage of hazardous materials can expose employees to harmful chemicals, leading to health problems and potential long-term health consequences. This can lead to significant compensation claims and reputational damage.
3. Legal and Compliance Issues:
- Non-Compliance with Regulations: Many industries are subject to strict regulations concerning the storage and handling of specific materials (e.g., hazardous materials, food products, pharmaceuticals). Failure to comply with these regulations can result in hefty fines, legal action, and even business closure.
- Liability for Accidents: If an accident or injury occurs due to inadequate storage and handling practices, the business could face significant legal liability, potentially leading to costly lawsuits and settlements.
The Essential Components of Effective Storage and Handling Training
A robust storage and handling training program must cover a variety of key areas to ensure comprehensive understanding and safe practices. Here's a breakdown of the essential components:
1. Understanding Hazards:
- Identifying Hazards: Trainees should be able to identify potential hazards associated with different materials and storage methods. This includes understanding the physical properties of materials (weight, size, fragility), potential chemical hazards, and ergonomic risks.
- Assessing Risks: Training should equip employees with the skills to assess the level of risk associated with different tasks and environments. This involves evaluating the likelihood and severity of potential hazards.
- Implementing Control Measures: Trainees must understand and be able to implement control measures to mitigate identified risks. This could include using appropriate personal protective equipment (PPE), implementing safe lifting techniques, and maintaining a clean and organized workspace.
2. Safe Material Handling Techniques:
- Proper Lifting Techniques: This is crucial for preventing back injuries and other musculoskeletal disorders. Training should cover proper body mechanics, lifting aids, and the importance of teamwork in handling heavy objects.
- Manual Handling Equipment: Trainees should be familiar with the safe operation and limitations of various manual handling equipment, such as hand trucks, pallet jacks, and dollies.
- Mechanical Handling Equipment: For businesses using forklifts, cranes, or other mechanical handling equipment, training should cover safe operation, pre-operational checks, and emergency procedures.
3. Storage Methods and Best Practices:
- Storage Layout and Design: Understanding how to optimize storage space, organize materials efficiently, and ensure appropriate segregation of incompatible materials is vital.
- Stacking and Securing Loads: Proper stacking techniques are crucial to prevent collapses and damage. Training should cover safe stacking practices, load stability, and the use of appropriate supports and bracing.
- Inventory Management: Effective inventory management systems can improve efficiency and reduce the risk of damage or loss. Training should cover inventory control procedures, stock rotation, and first-in, first-out (FIFO) methods.
- Storage of Hazardous Materials: Specific training is required for the storage of hazardous materials, covering safety data sheets (SDS), appropriate containers, labeling requirements, and emergency procedures.
4. Workplace Safety and Housekeeping:
- Maintaining a Clean and Organized Workspace: A cluttered workspace increases the risk of accidents and injuries. Training should emphasize the importance of regular housekeeping, proper waste disposal, and the efficient organization of materials.
- Emergency Procedures: Employees should be trained on emergency procedures, including evacuation plans, fire safety procedures, and how to respond to spills or accidents involving hazardous materials.
- Personal Protective Equipment (PPE): Training should cover the correct selection, use, and maintenance of appropriate PPE, such as safety shoes, gloves, eye protection, and hearing protection.
5. Documentation and Record Keeping:
- Incident Reporting: Employees should understand the importance of promptly reporting any incidents or near misses related to storage and handling.
- Maintenance Records: For mechanical handling equipment, appropriate maintenance records must be kept, and employees should be trained to perform basic checks and report any maintenance needs.
Implementing Effective Storage and Handling Training
The success of your storage and handling training program depends on careful planning and implementation. Here’s a practical approach:
1. Needs Assessment:
Before designing the training, conduct a thorough needs assessment to identify specific knowledge gaps and training needs within your workforce. This assessment should consider the types of materials handled, the equipment used, and the existing safety procedures.
2. Develop a Training Plan:
Based on your needs assessment, develop a comprehensive training plan outlining the specific topics to be covered, the training methods to be used, and the assessment criteria. The plan should specify learning objectives, the duration of the training, and the resources required.
3. Choose Appropriate Training Methods:
Utilize a variety of training methods to ensure effective knowledge transfer and skills development. This could include classroom instruction, hands-on training, simulations, videos, and online modules. Hands-on practice is crucial for skills development.
4. Provide Regular Refreshers and Updates:
Storage and handling procedures may change due to new regulations, technological advancements, or changes in materials handled. Provide regular refresher training to ensure employees remain up-to-date on best practices and safety procedures.
5. Assess and Evaluate Training Effectiveness:
Implement a robust assessment process to evaluate the effectiveness of the training program. This could involve written tests, practical assessments, observations, and feedback sessions. Use the assessment results to identify areas for improvement in the training program.
6. Ongoing Monitoring and Improvement:
Continuously monitor workplace practices to ensure compliance with training and identify areas needing further attention. Regular audits and safety inspections are essential components of a successful program. Encourage feedback from employees and use it to improve your procedures.
Conclusion: Investing in a Safer and More Efficient Future
Investing in comprehensive storage and handling training is an investment in the safety and efficiency of your business. By implementing a robust training program covering all the essential components outlined above, you can significantly reduce the risk of accidents, improve productivity, minimize financial losses, and ensure compliance with all relevant regulations. Don't wait for an incident to occur; proactively invest in your employees' safety and the long-term success of your business through effective storage and handling training. The benefits far outweigh the costs. A safer workplace is a more productive and profitable workplace. Remember, a well-trained workforce is a valuable asset.
Latest Posts
Latest Posts
-
If You Find Yourself In A Skid
May 10, 2025
-
Most Of The Heat Produced In The Body Is Through
May 10, 2025
-
Which Of The Following Is Not True Of Proteins
May 10, 2025
-
An Allergic Reaction Is A Form Of Hyposensitivity
May 10, 2025
-
Examples Of Vector Graphics Include Select All That Apply
May 10, 2025
Related Post
Thank you for visiting our website which covers about Storage And Handling Training Should Be Completed . We hope the information provided has been useful to you. Feel free to contact us if you have any questions or need further assistance. See you next time and don't miss to bookmark.