The Amount Of Inspection Needed Depends On __________ And __________.
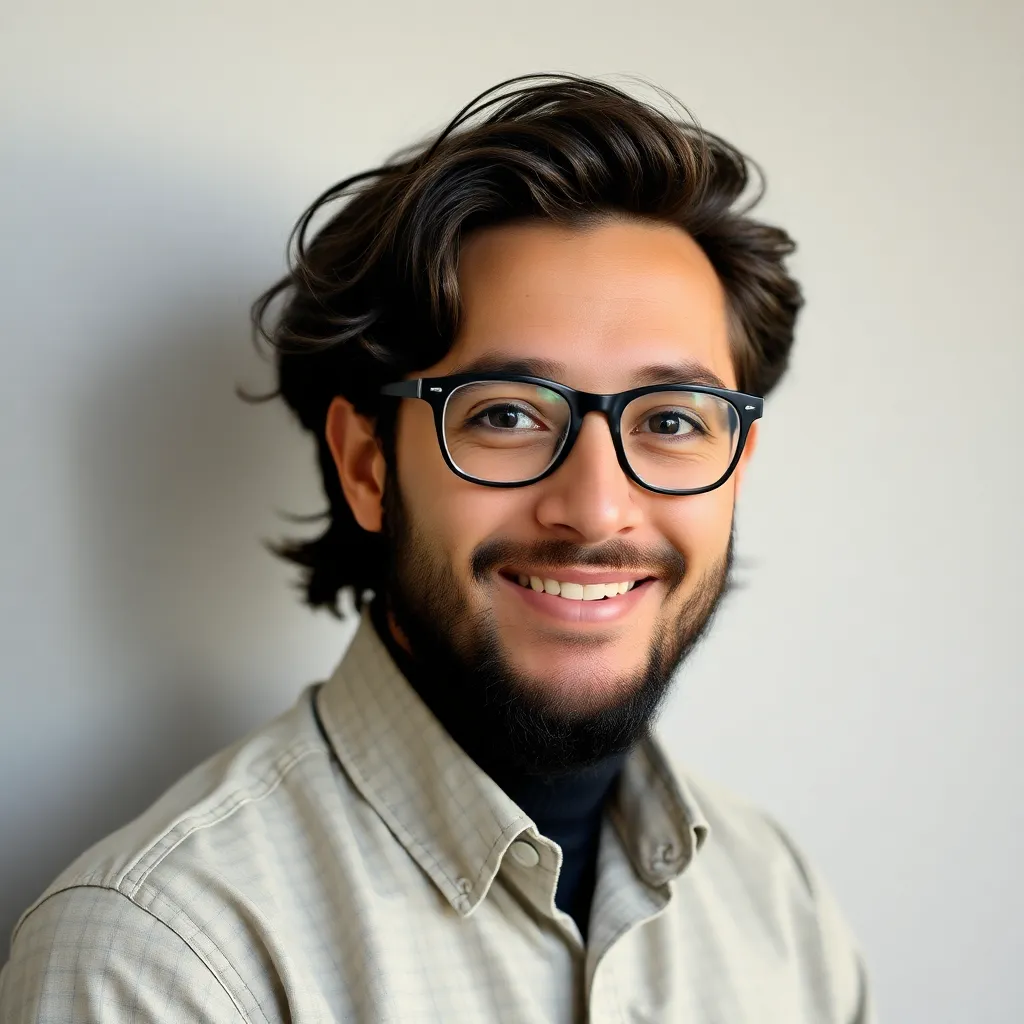
Breaking News Today
Apr 23, 2025 · 6 min read

Table of Contents
The Amount of Inspection Needed Depends on Risk and Complexity
The frequency and intensity of inspections are crucial aspects of ensuring quality, safety, and compliance across numerous industries. However, a blanket approach to inspection isn't efficient or cost-effective. Instead, a strategic approach tailored to the specific circumstances is vital. The amount of inspection needed depends fundamentally on two key factors: risk and complexity. Understanding these elements allows for the development of a robust, targeted inspection plan that maximizes effectiveness while minimizing unnecessary expenditure.
Understanding the Risk Factor
Risk assessment is the cornerstone of any effective inspection strategy. It involves identifying potential hazards, analyzing their likelihood of occurrence, and evaluating the potential severity of their consequences. This analysis should consider various factors, including:
1. Potential for Harm:
This encompasses the severity of potential consequences if a failure occurs. For example, a faulty component in a consumer product might lead to minor inconvenience, while a similar failure in a nuclear power plant could have catastrophic consequences. The higher the potential for harm, the more rigorous the inspection regime should be.
2. Likelihood of Failure:
This examines the probability of a component, system, or process failing. Several factors contribute to this assessment, such as the age and condition of the equipment, the environmental conditions, and the operating procedures. A system with a high likelihood of failure demands more frequent and thorough inspections.
3. Regulatory Requirements:
Compliance with legal and regulatory requirements is paramount. Specific industries and processes are subject to stringent regulations that dictate minimum inspection frequencies and standards. These requirements often vary depending on the level of risk associated with the activity. Ignoring regulatory requirements can lead to severe penalties and reputational damage. Understanding these regulations is an important part of determining the necessary inspection frequency and intensity.
4. Past Performance and History:
Analyzing past performance data, including historical inspection reports, maintenance logs, and incident records, provides valuable insights into the reliability of systems and processes. A history of failures or near-misses indicates a higher risk profile and necessitates more frequent and thorough inspections. Conversely, a consistent record of success might justify a less intense inspection schedule.
5. Environmental Factors:
Environmental conditions can significantly influence the risk of failure. Harsh environments characterized by extreme temperatures, humidity, or corrosive substances accelerate the degradation of materials and increase the likelihood of equipment failure. Inspections in such environments should be more frequent and comprehensive.
Decoding Complexity: A Multifaceted Consideration
Complexity, the second crucial factor, refers to the intricacy and interconnectedness of the system or process being inspected. This involves evaluating:
1. System Interdependencies:
In many systems, components are interconnected, and the failure of one component can trigger a cascade of failures in other parts of the system. The greater the interdependencies, the more complex the inspection process becomes. A comprehensive understanding of these relationships is crucial to identify potential vulnerabilities and ensure thorough inspection coverage.
2. Technological Advancement:
Advanced technologies and complex systems present unique challenges for inspection. Inspecting sophisticated electronics, software systems, or advanced manufacturing processes requires specialized expertise and advanced inspection techniques. The level of technical sophistication dictates the complexity of the inspection process and the required expertise.
3. Process Variability:
Process variability refers to the inherent fluctuations and variations in a process or system. Higher variability often necessitates more frequent inspections to detect deviations from established norms and ensure consistent quality. This is especially critical in manufacturing processes where even slight variations can impact product quality or safety.
4. Geographic Dispersion:
Inspecting systems or processes spread across multiple locations introduces additional challenges. Coordinating inspections, ensuring consistent standards across different sites, and managing logistics add to the complexity of the inspection process. A well-defined inspection plan is crucial to manage this complexity effectively.
5. Data Management and Analysis:
The sheer volume of data generated by inspections in complex systems can be overwhelming. Effective data management, analysis, and reporting are critical to extracting valuable insights, identifying trends, and making informed decisions about future inspections. Investing in appropriate software and training is vital for managing the complexity of data analysis in large-scale inspection programs.
The Interplay of Risk and Complexity: Tailoring Inspection Strategies
The optimal inspection strategy isn't a one-size-fits-all solution; it requires a delicate balance between the level of risk and the degree of complexity. Consider these scenarios:
Scenario 1: High Risk, Low Complexity:
Imagine a simple but critical safety system, such as a pressure relief valve in a small chemical plant. The risk of failure is high (potential for explosion), but the system itself is relatively simple to inspect. The inspection strategy would emphasize frequent, thorough inspections focused on the critical components, perhaps daily or weekly checks.
Scenario 2: Low Risk, High Complexity:
Consider a complex software system with numerous interconnected modules. The risk of individual component failure might be low, but the potential cascading failures could have significant consequences. The inspection strategy would focus on rigorous testing and validation of the system's functionality and integration, perhaps through simulations or rigorous testing protocols. Frequency might be less, but the depth of analysis would be significant.
Scenario 3: High Risk, High Complexity:
This scenario presents the greatest challenge, such as inspecting a nuclear power plant. Both the risk of failure (catastrophic consequences) and the complexity of the system are very high. The inspection strategy would necessitate a multi-layered approach, involving regular inspections of individual components, system-level testing, and comprehensive risk assessments. Specialized personnel and advanced inspection technologies would be essential.
Scenario 4: Low Risk, Low Complexity:
This is the least demanding scenario, perhaps the periodic inspection of simple hand tools in a small workshop. Inspections could be infrequent and less thorough, perhaps focusing on visual checks for damage or wear.
Implementing a Practical Inspection Strategy
Developing an effective inspection plan requires a structured approach:
-
Risk Assessment: Conduct a thorough risk assessment identifying potential hazards, likelihood of failure, and potential consequences.
-
Complexity Analysis: Analyze the complexity of the system or process, considering interdependencies, technology, variability, and other factors.
-
Inspection Method Selection: Choose appropriate inspection methods based on the risk and complexity assessment. This could involve visual inspections, non-destructive testing (NDT), or specialized testing methodologies.
-
Inspection Frequency Determination: Establish a schedule for inspections based on the identified risk levels and the complexity of the system. High-risk, high-complexity systems will require more frequent inspections.
-
Documentation and Reporting: Maintain detailed records of all inspections, including findings, corrective actions, and follow-up actions. This documentation is crucial for continuous improvement and demonstrating compliance.
-
Continuous Improvement: Regularly review and update the inspection plan based on inspection findings, new technologies, and changes in regulations or risk profiles.
By carefully considering the interplay between risk and complexity, organizations can develop tailored inspection strategies that are both effective and efficient. This approach ensures that resources are focused where they are most needed, maximizing the benefits of inspection programs while minimizing unnecessary costs and disruptions. A well-defined, risk-based inspection strategy is essential for ensuring safety, quality, and compliance across all industries.
Latest Posts
Latest Posts
-
Which Medication Is Responsible For Neonatal Hypoglycemia
Apr 23, 2025
-
Are You Smarter Than A 1st Grader Questions
Apr 23, 2025
-
A Social Problem Is Defined As A Condition That
Apr 23, 2025
-
Producer Commissions May Not Be Paid To
Apr 23, 2025
-
Which Of The Following Patients Is In Decompensated Shock
Apr 23, 2025
Related Post
Thank you for visiting our website which covers about The Amount Of Inspection Needed Depends On __________ And __________. . We hope the information provided has been useful to you. Feel free to contact us if you have any questions or need further assistance. See you next time and don't miss to bookmark.