The Continuous Quality Improvement Process Is Designed To
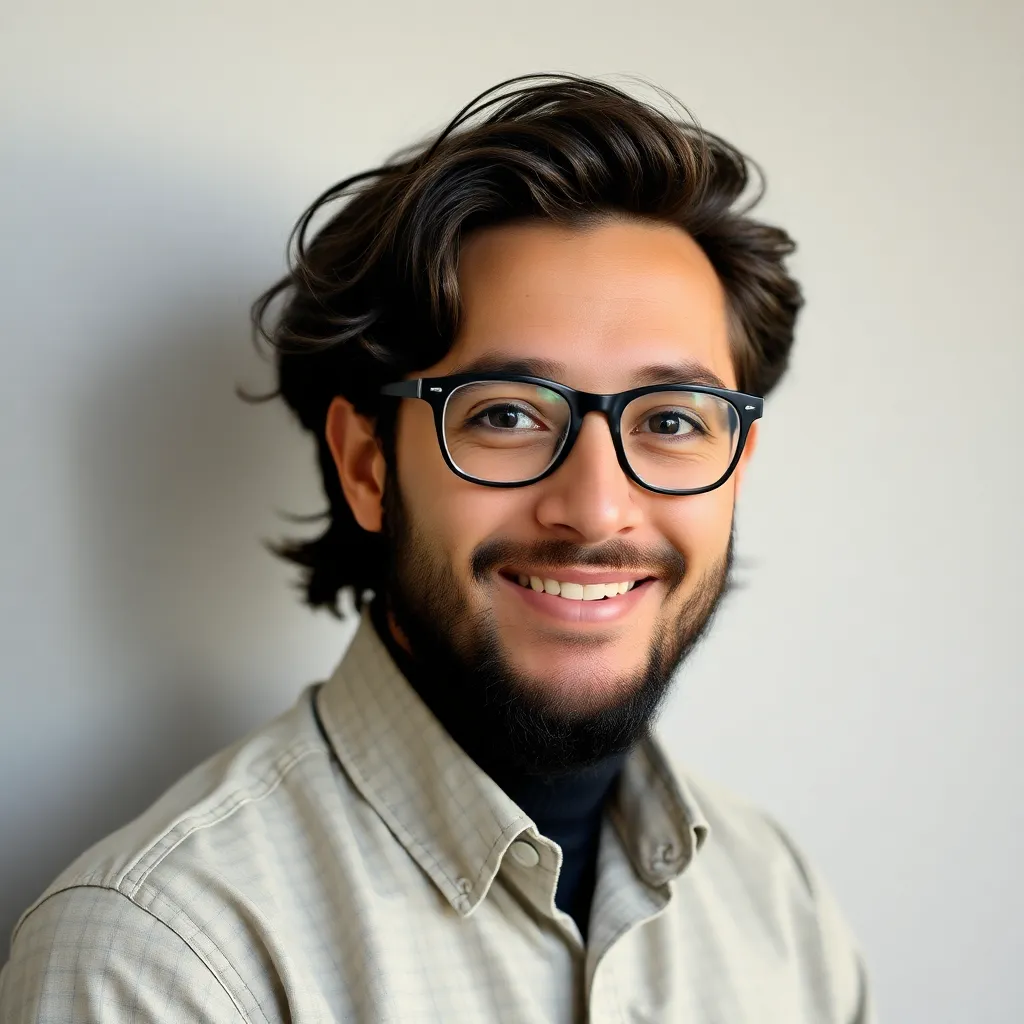
Breaking News Today
Apr 21, 2025 · 6 min read

Table of Contents
The Continuous Quality Improvement Process is Designed To… Drive Excellence
The pursuit of perfection is a journey, not a destination. In the dynamic landscape of today's businesses, maintaining a competitive edge requires a relentless commitment to improving every aspect of operations. This is where the Continuous Quality Improvement (CQI) process steps in, acting as a compass guiding organizations towards sustainable excellence. But what exactly is CQI designed to do? It's far more than just fixing problems; it's a proactive, holistic approach to achieving operational mastery.
The Core Goals of Continuous Quality Improvement
CQI isn't a one-size-fits-all solution; its application is tailored to the specific needs of an organization. However, several core goals consistently underpin its implementation:
1. Enhance Customer Satisfaction:
At the heart of any successful business lies the customer. CQI is fundamentally designed to boost customer satisfaction by consistently delivering high-quality products and services that meet or exceed expectations. This involves actively soliciting customer feedback, analyzing their needs, and translating this understanding into tangible improvements across the organization. By focusing on the customer journey, CQI ensures that every interaction, from initial contact to post-purchase support, contributes to a positive and memorable experience. This improved experience directly translates into increased customer loyalty and advocacy.
2. Optimize Processes and Efficiency:
CQI strives to streamline workflows and eliminate waste. Through meticulous process mapping and analysis, inefficient steps and bottlenecks are identified and removed. This leads to improved productivity, reduced operational costs, and faster turnaround times. By focusing on eliminating non-value-added activities, CQI frees up resources that can be redirected towards enhancing product quality, improving customer service, or driving innovation. This efficiency improvement is key to maintaining a competitive advantage in today's fast-paced market.
3. Minimize Errors and Defects:
Reducing errors and defects is a cornerstone of CQI. By systematically identifying the root causes of problems, the CQI process empowers organizations to implement preventative measures to avoid recurrence. This proactive approach to quality control reduces rework, scrap, and associated costs. Moreover, minimizing defects directly translates to higher levels of customer satisfaction and enhanced brand reputation. This reduction in defects also impacts employee morale, as it leads to a more streamlined and efficient work environment.
4. Foster a Culture of Continuous Improvement:
CQI isn't simply a set of tools and techniques; it’s a fundamental shift in organizational culture. It fosters a mindset where every employee feels empowered to identify opportunities for improvement and actively contribute to the process. This collaborative approach cultivates a sense of ownership and accountability, leading to greater engagement and innovation across all levels of the organization. A strong culture of continuous improvement is essential for sustainable success.
5. Increase Profitability and Competitiveness:
The cumulative effects of enhancing customer satisfaction, optimizing processes, minimizing errors, and fostering a culture of improvement directly contribute to increased profitability and a stronger competitive position. By reducing waste, improving efficiency, and delivering higher-quality products and services, CQI allows organizations to maximize their return on investment while outperforming their competitors. This improved bottom line is a crucial indicator of the success of the CQI process.
Key Principles of Continuous Quality Improvement
Several underlying principles guide the effective implementation of CQI:
1. Customer Focus:
Placing the customer at the center of all decisions is paramount. Understanding their needs, preferences, and expectations is crucial for delivering products and services that meet or exceed their requirements.
2. Process Approach:
CQI emphasizes a systematic approach to identifying, analyzing, and improving processes. Process mapping, flowcharts, and other visual tools help visualize the workflow and identify areas for improvement.
3. Data-Driven Decision Making:
Decisions within the CQI process are based on objective data and evidence. Collecting, analyzing, and interpreting data is essential for making informed decisions and tracking progress.
4. Management Commitment:
Top-level management support and commitment are essential for creating a culture of continuous improvement. Leaders must champion the CQI initiative and provide the necessary resources and support.
5. Continuous Improvement:
The CQI process is iterative and ongoing. It’s not a one-time project but a continuous cycle of improvement, adaptation, and refinement.
Methods and Tools Used in CQI
Several methods and tools facilitate the CQI process:
1. Plan-Do-Check-Act (PDCA) Cycle:
This cyclical approach provides a structured framework for implementing improvements. The PDCA cycle involves planning changes, implementing them, checking the results, and acting on the findings.
2. Six Sigma:
A data-driven methodology that focuses on minimizing variation and defects in processes. Six Sigma uses statistical tools and techniques to identify and eliminate root causes of problems.
3. Lean Manufacturing:
A philosophy focused on eliminating waste and maximizing value for the customer. Lean principles emphasize efficiency, continuous flow, and waste reduction.
4. Kaizen:
A Japanese term that means "continuous improvement." Kaizen promotes small, incremental improvements that, when implemented consistently, can lead to significant change.
5. 5S Methodology:
A workplace organization method that focuses on maintaining a clean, orderly, and efficient work environment. The five S's represent Sort, Set in Order, Shine, Standardize, and Sustain.
6. Root Cause Analysis:
Techniques such as the "5 Whys" and fishbone diagrams are used to identify the root causes of problems and implement corrective actions.
Implementing Continuous Quality Improvement: A Step-by-Step Guide
Implementing CQI requires a strategic approach. Here's a step-by-step guide:
-
Define Objectives: Clearly articulate the goals of the CQI initiative. What specific areas need improvement? What metrics will be used to measure success?
-
Assess Current State: Conduct a thorough assessment of current processes, identifying strengths, weaknesses, and areas for improvement. Utilize tools such as process mapping and data analysis.
-
Identify Improvement Opportunities: Based on the assessment, identify specific areas where improvements can be made. Prioritize opportunities based on their potential impact and feasibility.
-
Develop and Implement Solutions: Develop and implement solutions to address the identified improvement opportunities. Utilize appropriate tools and methodologies, such as PDCA, Six Sigma, or Lean.
-
Monitor and Measure Results: Track progress and measure the effectiveness of implemented solutions. Use key performance indicators (KPIs) to monitor changes and ensure that objectives are being met.
-
Review and Adjust: Regularly review the CQI process and make adjustments as needed. The process should be iterative and adaptive, constantly evolving to meet changing needs.
Overcoming Challenges in Continuous Quality Improvement
Implementing CQI isn't without its challenges:
-
Resistance to change: Employees may resist changes to established processes or procedures. Effective communication and training are crucial to overcome this resistance.
-
Lack of resources: Implementing CQI may require significant investment in training, technology, and other resources. Securing necessary funding and support is vital.
-
Lack of management commitment: Without strong leadership support, the CQI initiative is unlikely to succeed. Management must actively champion the process and provide the necessary resources.
-
Measuring progress: Accurately measuring progress and demonstrating the ROI of CQI can be challenging. Clear KPIs and data-driven tracking are essential.
Conclusion: The Ongoing Pursuit of Excellence
The Continuous Quality Improvement process is designed to drive excellence by fostering a culture of continuous learning and improvement. It's a journey that requires commitment, collaboration, and a relentless pursuit of perfection. By focusing on customer satisfaction, process optimization, and a data-driven approach, organizations can leverage CQI to achieve sustainable competitive advantage and long-term success. The benefits are multifaceted, impacting profitability, employee morale, and ultimately, the overall success and sustainability of the business. It’s not simply about fixing what's broken; it's about proactively shaping a future defined by excellence. The ongoing nature of CQI ensures that organizations remain agile, adaptable, and constantly striving for improvement in a continuously evolving marketplace.
Latest Posts
Latest Posts
-
Signed The Charter Of 1732 Which Created Ga
Apr 21, 2025
-
An Insurance Applicant Must Be Informed Of An Investigation
Apr 21, 2025
-
What Goods Are Available To All Without Direct Payment
Apr 21, 2025
-
Which Of The Following Is Part Of A Shotgun Shell
Apr 21, 2025
-
Before The Industrial Revolution Living Standards In The World
Apr 21, 2025
Related Post
Thank you for visiting our website which covers about The Continuous Quality Improvement Process Is Designed To . We hope the information provided has been useful to you. Feel free to contact us if you have any questions or need further assistance. See you next time and don't miss to bookmark.