The Cost Of Direct Materials Are Classified As
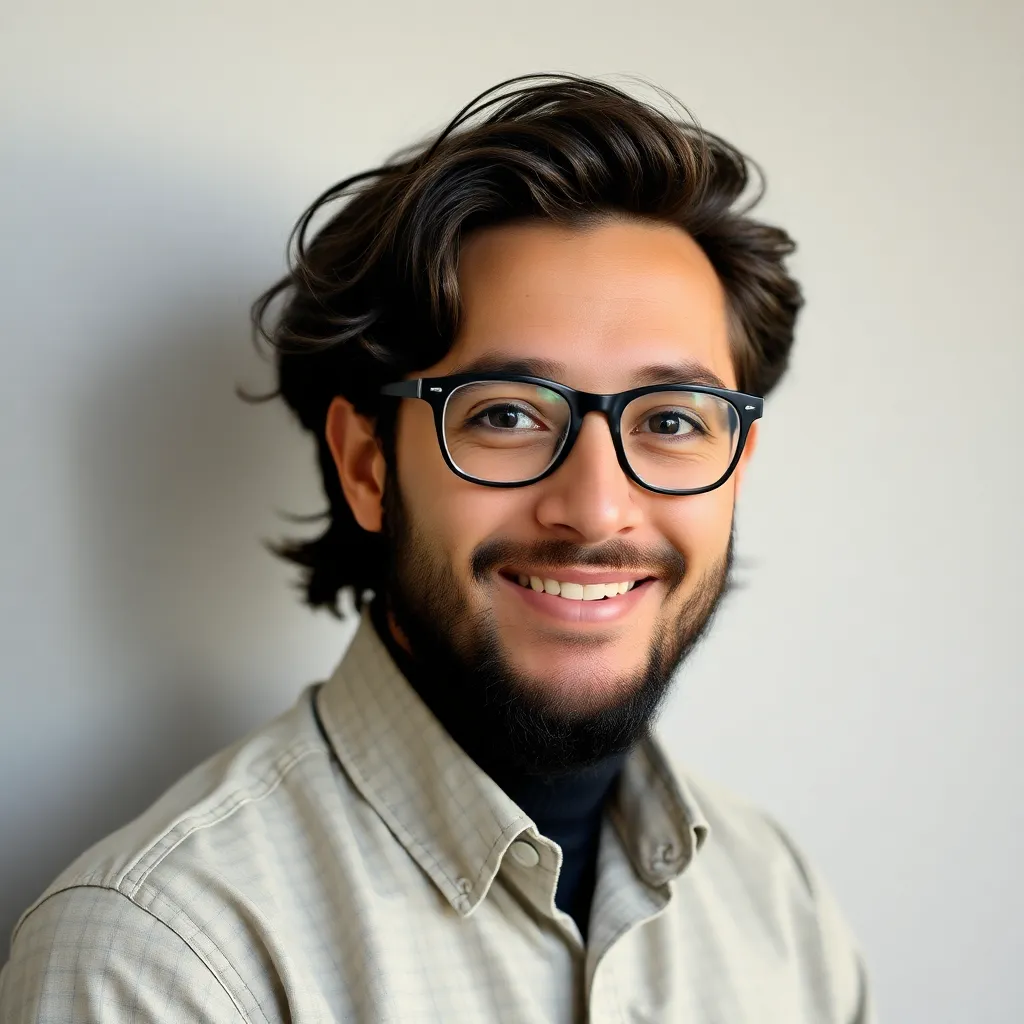
Breaking News Today
Apr 06, 2025 · 6 min read

Table of Contents
The Cost of Direct Materials: A Comprehensive Classification Guide
Direct materials are the lifeblood of any manufacturing or production process. Understanding their cost and how it's classified is crucial for accurate budgeting, efficient production, and informed decision-making. This comprehensive guide delves deep into the classification of direct material costs, providing a detailed breakdown for businesses of all sizes. We'll explore different costing methods, considerations for accurate accounting, and the impact of fluctuating material prices.
What are Direct Materials?
Before diving into classification, let's define direct materials. These are the raw materials that are directly used in the production process and become an integral part of the finished product. They're easily traceable and directly attributable to the manufactured goods. Examples include:
- Manufacturing: Wood for furniture, steel for automobiles, fabric for clothing, silicon for computer chips.
- Food Production: Flour for bread, beef for burgers, sugar for candy.
- Construction: Cement, bricks, lumber, steel rebar.
It's essential to distinguish direct materials from indirect materials. Indirect materials are those used in the production process but are not directly traceable to a specific product. These often include small components, lubricants, cleaning supplies, and general maintenance items. The cost of indirect materials is usually included in manufacturing overhead.
Key Classifications of Direct Material Costs
The cost of direct materials isn't simply a single figure. It's composed of several elements, which need careful consideration for accurate accounting and cost control. We'll break down the key classifications:
1. Purchase Price
This is the most straightforward component – the actual amount paid to acquire the raw materials. This includes the cost of the materials themselves, plus any applicable taxes, freight charges, and import duties directly related to their acquisition. For example, the purchase price of lumber includes not only the cost of the wood itself but also transportation charges from the lumberyard to the manufacturing facility. Careful record-keeping is vital to accurately track these costs.
2. Freight-In Costs
These are the transportation expenses incurred in getting the direct materials from the supplier to the production facility. As mentioned, these are usually included as part of the overall cost of the materials, directly adding to the purchase price. However, separate tracking can provide insights into supply chain efficiency and potential cost-saving opportunities. Analyzing freight costs can help businesses identify more cost-effective transportation methods or supplier locations.
3. Inspection Costs
Once materials arrive, inspection is necessary to ensure they meet quality standards. Costs associated with this inspection, including labor costs for inspectors and any equipment used, are directly attributable to the materials and form part of their overall cost. High inspection costs can signal potential quality issues with suppliers, necessitating proactive measures. This could involve renegotiating contracts, changing suppliers, or implementing stricter quality control checks at the source.
4. Receiving and Handling Costs
The process of receiving and handling materials before they're put into production also involves costs. These include labor costs for warehouse personnel, storage costs, and any equipment used in handling the materials. These costs are often minimal, but accumulating these costs over time can significantly impact the total cost of materials. Effective warehouse management and efficient handling procedures can mitigate these costs.
5. Preparation Costs
Before use in production, some direct materials may require additional preparation, such as cleaning, cutting, or mixing. Labor costs associated with this preparation, as well as any materials consumed during preparation (e.g., cleaning solvents), are classified as part of the direct material cost. Efficient preparation processes can significantly impact overall productivity and material costs. This emphasizes the importance of process optimization and employee training.
6. Shrinkage and Spoilage
Not all materials make it into the finished product. Shrinkage (a reduction in quantity due to processing) and spoilage (materials rendered unusable due to damage or defect) represent a loss of material and therefore a direct material cost. Tracking and minimizing shrinkage and spoilage is crucial for cost control. Analyzing the causes of these losses can help identify areas for improvement in processes, storage, and handling.
7. Obsolescence Costs
Materials can become obsolete due to technological advancements, changes in design, or simply slow demand. The cost of obsolete materials is a direct material cost that needs to be accounted for. Strategies for minimizing obsolescence costs include careful forecasting of material needs, effective inventory management, and flexible production planning.
Accounting for Direct Material Costs
Accurate accounting for direct material costs is essential for various financial reports and decision-making processes. Several methods are commonly used:
1. First-In, First-Out (FIFO)
This method assumes that the oldest materials are used first. This is beneficial for accurate costing when dealing with materials with a short shelf life or that are subject to price fluctuations.
2. Last-In, First-Out (LIFO)
This method assumes the newest materials are used first. This can be advantageous during periods of inflation, as it results in a higher cost of goods sold and lower net income, which can reduce tax liability.
3. Weighted-Average Cost
This method calculates the average cost of materials over a period, simplifying the costing process but potentially obscuring the impact of price fluctuations.
The choice of method depends on various factors, including industry practices, company policies, and tax regulations. Consistency in the chosen method is vital for reliable financial reporting.
Impact of Fluctuating Material Prices
Material prices are rarely static. Fluctuations can significantly impact the profitability of a business. Effective strategies to manage these fluctuations include:
- Long-term contracts with suppliers: Securing stable pricing for a certain volume of materials over a defined period.
- Hedging: Using financial instruments to mitigate the risk of price changes.
- Diversification of suppliers: Reducing reliance on a single supplier to minimize vulnerability to price increases from a single source.
- Inventory management: Optimizing inventory levels to balance supply needs with cost considerations.
- Continuous monitoring of market prices: Staying informed about market trends and potential price movements.
Conclusion
Understanding the cost of direct materials and its various classifications is essential for any business involved in manufacturing or production. Accurate accounting, efficient material management, and proactive strategies for managing price fluctuations are crucial for profitability and sustained success. By carefully considering the different components of direct material costs, businesses can gain valuable insights into their production processes, improve efficiency, and make informed decisions to optimize profitability. The detailed tracking and analysis of these costs are not merely accounting exercises; they are powerful tools for improving operational efficiency and overall business performance. Remember, consistent and accurate tracking allows for better forecasting, improved budgeting, and stronger decision-making, ultimately leading to a more robust and competitive business.
Latest Posts
Latest Posts
-
Which Statement Correctly Describes The Cells Produced By Meiosis
Apr 07, 2025
-
Skills Module 3 0 Iv Therapy And Peripheral Access Posttest
Apr 07, 2025
-
The Answer To A Division Problem Is The
Apr 07, 2025
-
If You Cause Damage To An Unattended Vehicle You Should
Apr 07, 2025
-
Match Each Question Type To The Correct Example
Apr 07, 2025
Related Post
Thank you for visiting our website which covers about The Cost Of Direct Materials Are Classified As . We hope the information provided has been useful to you. Feel free to contact us if you have any questions or need further assistance. See you next time and don't miss to bookmark.