The Different Gears In A Gear Head Multiplier
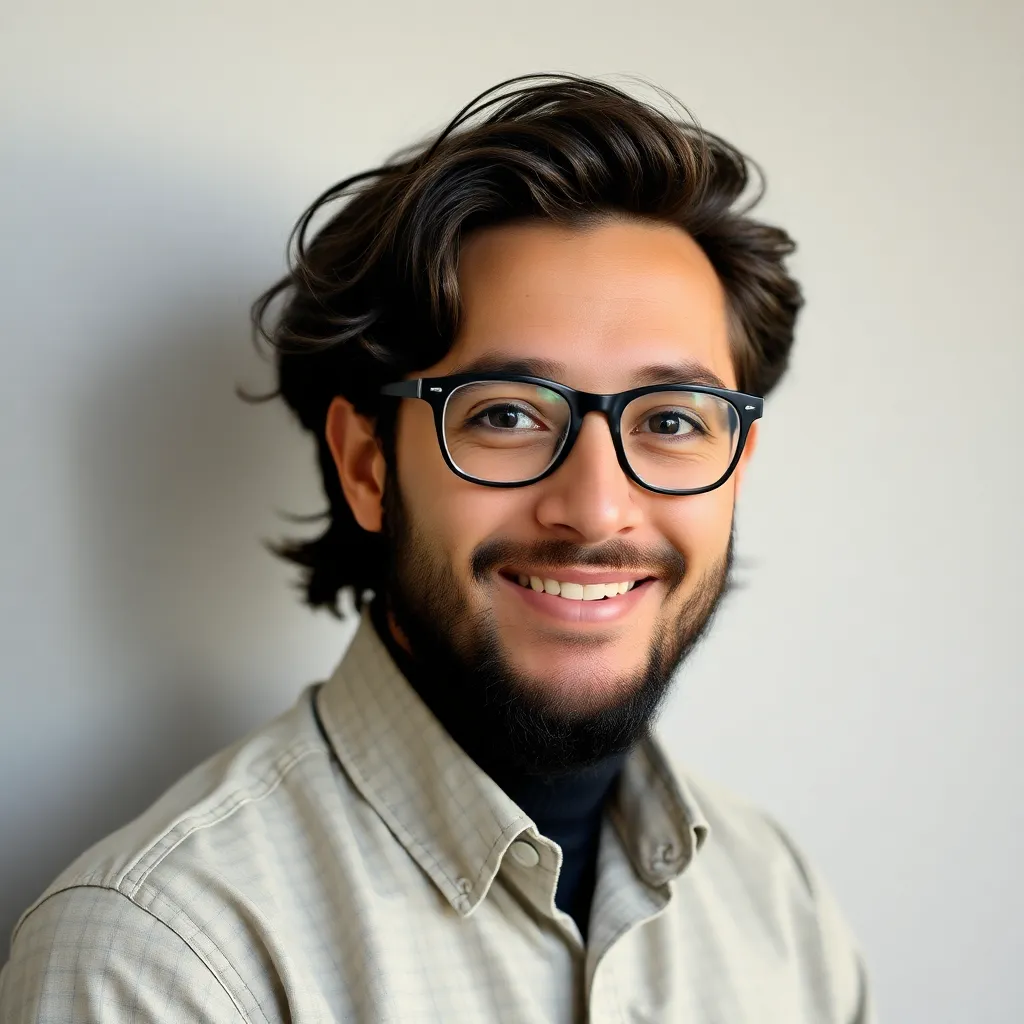
Breaking News Today
Apr 08, 2025 · 6 min read

Table of Contents
Decoding the Complexity: A Deep Dive into Gear Head Multiplier Gears
Gear head multipliers, also known as gearboxes, are ubiquitous in various mechanical systems, from industrial machinery to automotive applications. Their primary function is to increase or decrease the torque and speed of a rotating shaft. This intricate process relies on a precisely engineered system of gears, each playing a crucial role in achieving the desired output. This article delves deep into the different types of gears found within a gear head multiplier, explaining their functionalities, advantages, and disadvantages. Understanding these components is essential for engineers, technicians, and anyone interested in the mechanics of power transmission.
The Core Components: Types of Gears in a Gear Head Multiplier
Gear head multipliers utilize a variety of gear types, each selected based on factors like speed ratio, torque capacity, and space constraints. Let's explore some of the most common:
1. Spur Gears: The Workhorses
Spur gears are the most basic type, featuring straight teeth parallel to the axis of rotation. They are simple to manufacture and relatively inexpensive, making them ideal for applications requiring straightforward speed reduction or increase.
- Advantages: Simplicity, low cost, high efficiency at low speeds.
- Disadvantages: Noise at higher speeds, limited load capacity compared to other gear types, prone to vibration.
- Applications: Simple speed reduction systems, conveyor belts, low-speed industrial machinery.
2. Helical Gears: Smoother Operation
Helical gears feature teeth that are inclined at an angle to the axis of rotation. This angled design results in a smoother, quieter operation compared to spur gears, as the teeth engage gradually rather than abruptly. However, this also introduces an axial thrust that needs to be accommodated in the design.
- Advantages: Smoother operation, quieter than spur gears, higher load capacity.
- Disadvantages: Axial thrust, more complex manufacturing process, potential for increased wear if not properly lubricated.
- Applications: High-speed applications, power transmission systems where noise reduction is critical, automotive transmissions.
3. Herringbone Gears (Double Helical Gears): Powerhouses
Herringbone gears combine two helical gears mirrored on the same shaft, effectively canceling out the axial thrust. This results in a highly efficient and robust gear type capable of handling significant loads and speeds.
- Advantages: High load capacity, very smooth and quiet operation, no axial thrust.
- Disadvantages: Complex manufacturing process, high cost.
- Applications: Heavy-duty industrial machinery, large power transmission systems, wind turbines.
4. Bevel Gears: Changing Directions
Bevel gears are used to transmit power between intersecting shafts. They are commonly found in applications where a change in direction of rotation is required. Several types of bevel gears exist, each with its own characteristics:
-
Straight Bevel Gears: Similar to spur gears, but with teeth cut on a cone shape. They are simple but less efficient at higher speeds.
-
Spiral Bevel Gears: Similar to helical gears, but with curved teeth. They provide smoother, quieter operation than straight bevel gears.
-
Hypoid Bevel Gears: Similar to spiral bevel gears but with shafts that are offset. They allow for greater speed ratios and are commonly used in automotive differentials.
-
Advantages (Bevel Gears): Power transmission between intersecting shafts.
-
Disadvantages (Bevel Gears): More complex design and manufacturing than spur gears, potential for higher wear if not properly aligned.
-
Applications (Bevel Gears): Automotive differentials, robotic arms, machine tool applications requiring changes in rotational direction.
5. Worm Gears: High Reduction Ratios
Worm gears consist of a worm (a screw-like gear) and a worm wheel (a gear with teeth engaging the worm). They offer high speed reduction ratios in a compact package, often achieving ratios of 100:1 or more. However, they are generally less efficient than other gear types due to sliding friction between the worm and the worm wheel.
- Advantages: High reduction ratios, self-locking capability (in many cases, the worm wheel cannot drive the worm), compact design.
- Disadvantages: Lower efficiency than other gear types, significant heat generation, potential for wear if not properly lubricated.
- Applications: Jacks, conveyors, lifting mechanisms, applications requiring self-locking functionality.
6. Planetary Gears: Efficient Power Distribution
Planetary gears are a unique system consisting of a sun gear, planet gears, a planet carrier, and a ring gear. They offer high torque capacity and efficiency, often used in applications requiring complex speed ratios and power distribution.
- Advantages: High torque capacity, high efficiency, compact design, ability to achieve complex speed ratios.
- Disadvantages: Complex design and manufacturing, higher cost compared to simpler gear types.
- Applications: Automotive transmissions, wind turbines, robotics, industrial machinery requiring high torque and complex speed changes.
Selecting the Right Gears for Your Gear Head Multiplier
Choosing the appropriate gear types for your gear head multiplier is crucial for optimal performance and longevity. The selection process involves considering several factors:
- Speed Ratio: The desired ratio between input and output speeds dictates the gear ratios required.
- Torque Requirements: The load to be driven determines the necessary torque capacity of the gears.
- Space Constraints: Physical limitations of the application influence the size and type of gears that can be used.
- Noise Levels: Applications requiring quiet operation necessitates the use of gears designed for low noise levels (e.g., helical or herringbone gears).
- Efficiency: High efficiency is important in applications where energy conservation is critical.
- Cost: The manufacturing cost of different gear types varies significantly, influencing the selection process.
- Maintenance: The ease of maintenance and lubrication should also be considered.
Gear Material Selection: A Critical Factor
The material used for the gears significantly impacts their performance, durability, and lifespan. Common gear materials include:
- Steel: A popular choice due to its high strength and durability. Various grades of steel are available, offering different properties for specific applications.
- Cast Iron: A cost-effective option for low-speed, low-load applications.
- Bronze: Used in applications requiring good wear resistance and compatibility with steel gears.
- Plastics: Used for low-load, low-speed applications where noise reduction and cost are important factors. However, plastic gears generally have lower load-bearing capacity and shorter lifespans compared to metallic gears.
Advanced Considerations: Gear Design and Manufacturing
Optimizing gear design and manufacturing processes is paramount in achieving a high-performance gear head multiplier. This includes factors such as:
- Gear Tooth Profile: The shape of the gear teeth significantly impacts the meshing efficiency, load-carrying capacity, and noise levels. Involute profiles are commonly used for their ability to maintain constant velocity ratios.
- Gear Module: The gear module defines the size of the gears and influences their strength and load capacity.
- Backlash: The clearance between meshing gears. Proper backlash is crucial for smooth operation and to prevent gear binding.
- Lubrication: Adequate lubrication is essential for reducing friction, wear, and noise. The choice of lubricant depends on factors such as speed, load, and operating temperature.
- Heat Dissipation: Effective heat dissipation is critical in high-speed, high-load applications to prevent overheating and gear damage.
Conclusion: Mastering the Mechanics of Gear Head Multipliers
Gear head multipliers are complex systems relying on a precise arrangement of different gear types. Understanding the functionalities and characteristics of each gear type is crucial for selecting the optimal configuration for a given application. By carefully considering factors such as speed ratio, torque capacity, space constraints, noise levels, efficiency, cost, and maintenance, engineers and technicians can design and implement robust and reliable gear head multipliers that meet specific performance requirements. Continued advancements in gear materials, design techniques, and manufacturing processes promise even greater efficiency, durability, and performance in future gear head multiplier applications.
Latest Posts
Latest Posts
-
When Does Ashrae Standard 15 2013 Requires That Each Machinery Room
Apr 18, 2025
-
Retro Reflective Trim Is Recommended On All High Visibility Clothing
Apr 18, 2025
-
Consider Your Current Uses Of Tap Water
Apr 18, 2025
-
Which Of The Following Answer Options Are Your Employers Responsibility
Apr 18, 2025
-
As The Only Lifeguard Performing Cpr On A 7
Apr 18, 2025
Related Post
Thank you for visiting our website which covers about The Different Gears In A Gear Head Multiplier . We hope the information provided has been useful to you. Feel free to contact us if you have any questions or need further assistance. See you next time and don't miss to bookmark.