The Formula To Determine The Materials To Be Purchased Is
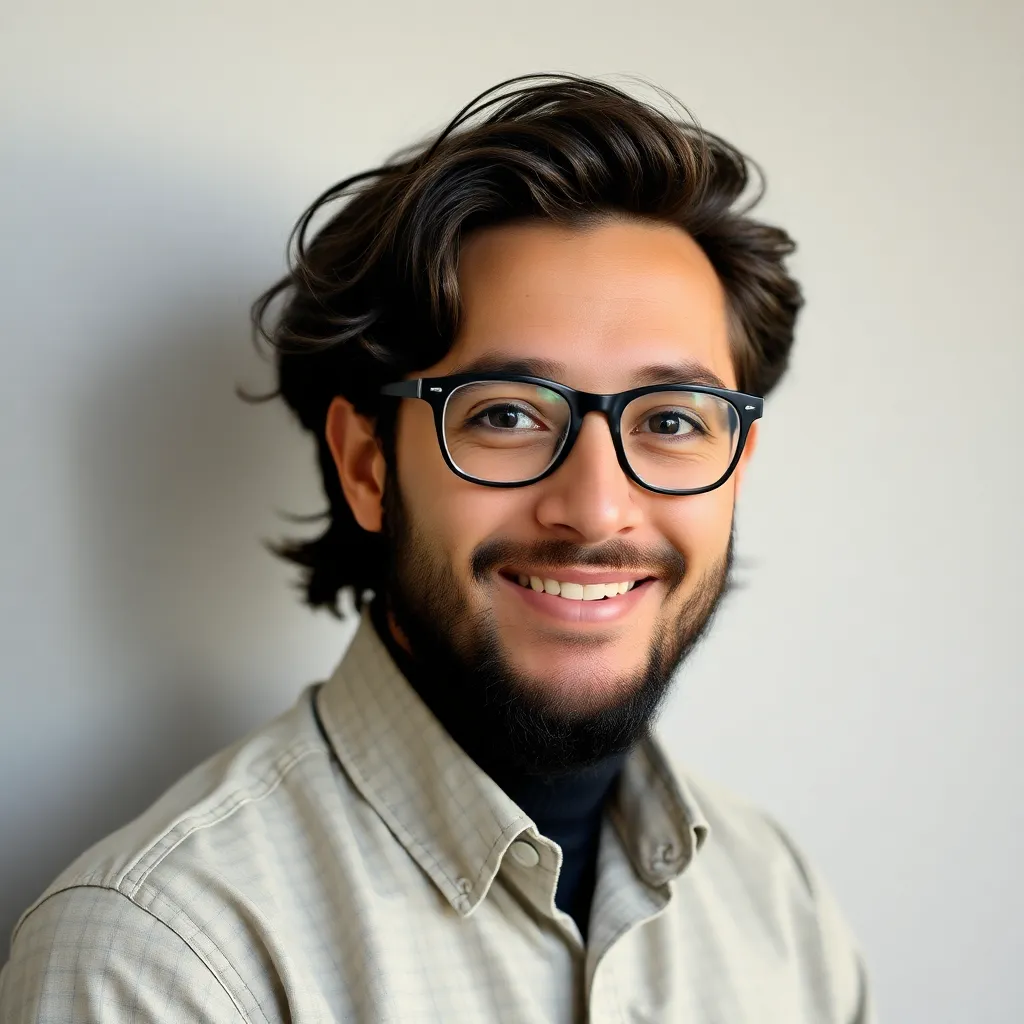
Breaking News Today
Mar 30, 2025 · 6 min read
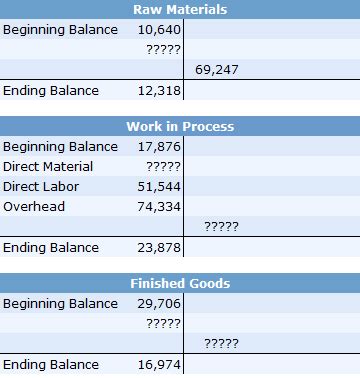
Table of Contents
The Formula to Determine Materials to Purchase: A Comprehensive Guide
Determining the right quantity of materials to purchase is crucial for any business, from small startups to large corporations. Overstocking ties up capital and increases storage costs, while understocking can lead to production delays, lost sales, and dissatisfied customers. There's no single magic formula, but rather a combination of techniques and calculations that need to be tailored to your specific business needs and industry. This comprehensive guide will explore the key factors and methods involved in accurately determining material purchasing requirements.
Understanding the Core Components
Before diving into formulas, let's lay the groundwork by understanding the crucial components influencing material purchasing decisions:
1. Demand Forecasting: The Foundation of Your Plan
Accurate demand forecasting is the bedrock of effective material purchasing. This involves predicting the quantity of materials you'll need over a specific period, considering factors like:
-
Historical Sales Data: Analyzing past sales figures provides a baseline understanding of your typical demand. Consider seasonal variations, trends, and any significant events that impacted sales.
-
Market Trends: Researching industry trends, economic indicators, and competitor activities helps anticipate potential shifts in demand.
-
Sales Forecasts: Collaborate with your sales team to obtain their projections for future sales. This provides a forward-looking perspective on demand.
-
External Factors: Account for unpredictable events that could significantly impact demand, such as natural disasters, economic downturns, or changes in government regulations.
Several forecasting techniques exist, including:
-
Simple Moving Average: Averages sales data over a specific period. Simple, but may not capture trends effectively.
-
Weighted Moving Average: Assigns different weights to more recent data points, giving more importance to current trends.
-
Exponential Smoothing: A more sophisticated method that weighs recent data more heavily and considers trends.
-
Regression Analysis: Statistical method to identify relationships between sales and other variables, allowing for more accurate predictions.
2. Lead Time: The Time Gap to Account For
Lead time refers to the time elapsed between placing an order for materials and receiving the delivery. This includes order processing, manufacturing, shipping, and potential delays. Accurately estimating lead time is crucial to avoid stockouts. Consider factors such as:
-
Supplier Reliability: Some suppliers are more reliable than others in terms of on-time delivery.
-
Transportation Methods: Different shipping methods have varying transit times.
-
Potential Delays: Account for potential unforeseen delays due to weather, logistical issues, or other unexpected circumstances.
3. Safety Stock: A Buffer Against Uncertainty
Safety stock is an extra quantity of materials kept on hand to act as a buffer against unexpected fluctuations in demand or lead time. The amount of safety stock depends on the following:
-
Demand Variability: Higher demand variability requires higher safety stock.
-
Lead Time Variability: Longer and more variable lead times necessitate more safety stock.
-
Service Level: The desired probability of meeting customer demand without stockouts. A higher service level requires more safety stock.
4. Inventory Turnover: Monitoring Your Efficiency
Inventory turnover measures how efficiently you're using your inventory. A higher turnover rate indicates that you're selling your inventory quickly and efficiently, minimizing storage costs and the risk of obsolescence. It's calculated as:
Inventory Turnover = Cost of Goods Sold / Average Inventory
Monitoring inventory turnover helps you identify potential issues with overstocking or understocking.
Formulas for Determining Material Purchases
Now, let's explore the formulas used to determine the quantity of materials to purchase. The specific formula will depend on your chosen inventory management system.
1. Economic Order Quantity (EOQ) Model
The EOQ model is a classic inventory management technique aimed at minimizing the total inventory costs, which include ordering costs and holding costs. The formula is:
EOQ = √[(2DS)/H]
Where:
- D = Annual demand for the material
- S = Ordering cost per order
- H = Holding cost per unit per year
Limitations: The EOQ model assumes constant demand and lead time, which isn't always realistic. It also doesn't explicitly account for safety stock.
2. Reorder Point (ROP) Calculation
The reorder point (ROP) determines the inventory level at which a new order should be placed. The basic formula is:
ROP = (Lead Time Demand) + Safety Stock
Where:
-
Lead Time Demand = Average daily demand x Lead time in days
-
Safety Stock = Z x σ x √Lead Time
- Z = Number of standard deviations corresponding to the desired service level (e.g., 1.65 for 95% service level)
- σ = Standard deviation of daily demand
Limitations: This formula assumes that demand and lead time follow a normal distribution.
3. Material Requirements Planning (MRP)
MRP is a more sophisticated inventory management system that considers the entire production process. It integrates various factors such as:
- Bill of Materials (BOM): A detailed list of all the components needed to manufacture a product.
- Master Production Schedule (MPS): A plan outlining the production quantities and schedules for finished goods.
- Inventory Records: Information on current inventory levels for all materials.
MRP systems use algorithms to calculate the net requirements for each material, taking into account lead times, safety stock, and existing inventory. This provides a more precise material purchasing plan.
Limitations: MRP systems require significant data input and maintenance, and their effectiveness depends on the accuracy of the underlying data.
4. Just-in-Time (JIT) Inventory Management
JIT aims to minimize inventory holding costs by receiving materials only when they are needed for production. This approach relies on close collaboration with suppliers and efficient logistics. While it doesn't have a specific formula, it requires meticulous planning and execution.
Limitations: JIT is highly sensitive to disruptions in supply chains. Even small delays can severely impact production.
Choosing the Right Approach
The best approach for determining materials to purchase depends on various factors, including:
- Type of Business: A small business might use simpler methods like EOQ or ROP, while larger companies may rely on MRP systems.
- Demand Variability: For products with highly variable demand, safety stock and more sophisticated forecasting techniques are crucial.
- Lead Time: Long lead times require more accurate forecasting and larger safety stock.
- Inventory Costs: Balancing ordering costs and holding costs is crucial in all methods.
- Technological Capabilities: The availability of software and systems for inventory management will influence the choice of method.
Beyond the Formulas: Practical Considerations
While formulas provide a framework, several practical considerations are essential for effective material purchasing:
-
Supplier Relationships: Building strong relationships with reliable suppliers is paramount. This ensures consistent quality, timely delivery, and potentially better pricing.
-
Quality Control: Implement rigorous quality control measures to ensure that the received materials meet the required specifications.
-
Inventory Management Software: Utilizing inventory management software can automate many of the processes involved in material purchasing, forecasting, and tracking.
-
Regular Review and Adjustment: The material purchasing plan should be reviewed and adjusted regularly to adapt to changing circumstances.
Conclusion
Determining the optimal quantity of materials to purchase is a multifaceted process that goes beyond simple formulas. By combining accurate demand forecasting, understanding lead times, incorporating safety stock, and selecting the appropriate inventory management system, businesses can effectively manage their inventory, minimize costs, and ensure smooth production processes. Remember that continuous monitoring, adaptation, and a focus on strong supplier relationships are key to long-term success in materials purchasing. The formulas are tools; your business acumen and strategic planning are the driving force behind efficient and profitable material management.
Latest Posts
Latest Posts
-
Netflix Launched In The 1990s Offering Customers
Apr 01, 2025
-
What Hypothesis Have The Grants Been Testing
Apr 01, 2025
-
Self Worth Accomplishment And Confidence Represent The
Apr 01, 2025
-
A Food Establishment That Serves Raw Oysters
Apr 01, 2025
-
Atls Test Questions And Answers 10th Edition
Apr 01, 2025
Related Post
Thank you for visiting our website which covers about The Formula To Determine The Materials To Be Purchased Is . We hope the information provided has been useful to you. Feel free to contact us if you have any questions or need further assistance. See you next time and don't miss to bookmark.