The Goals Of Both Kanban And Mrp Include
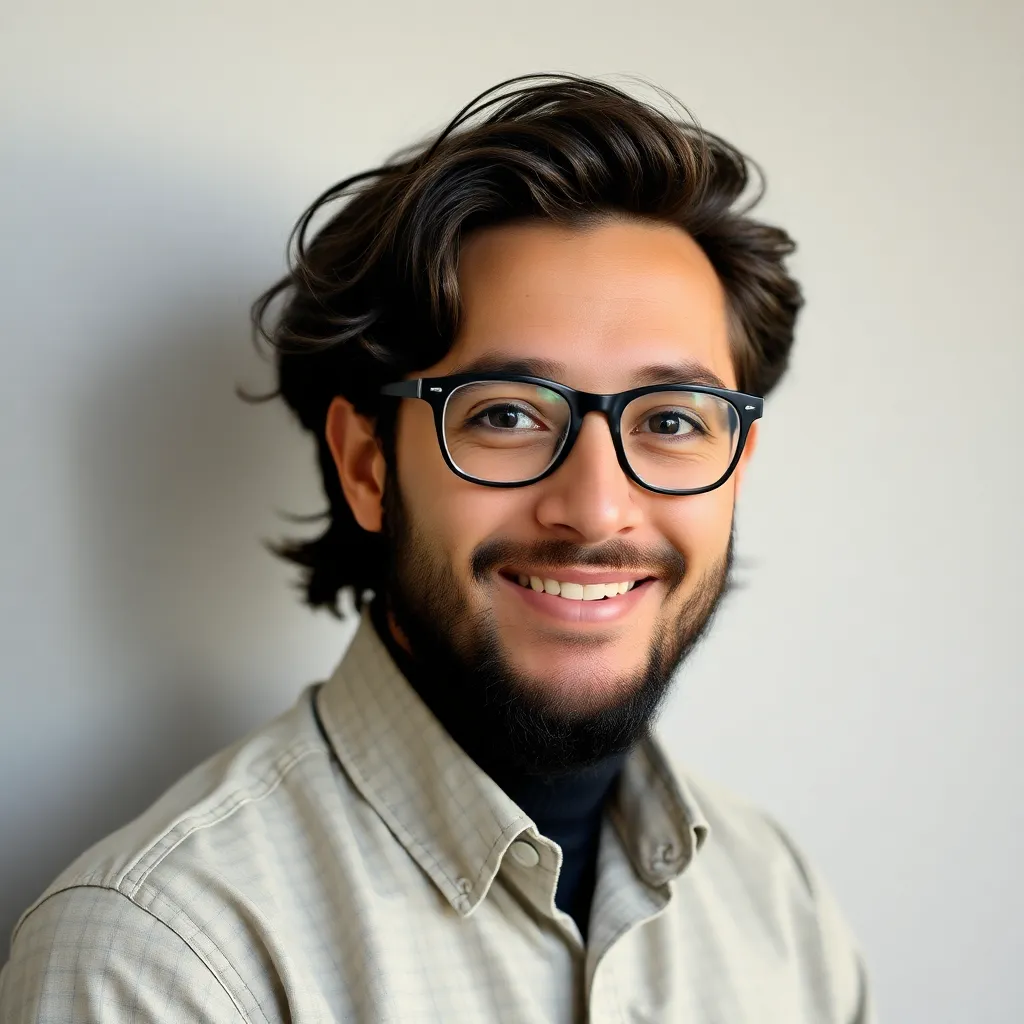
Breaking News Today
Apr 17, 2025 · 6 min read

Table of Contents
The Goals of Both Kanban and MRP: A Deep Dive into Inventory Management and Workflow Optimization
Both Kanban and Material Requirements Planning (MRP) are powerful inventory management and workflow optimization tools, but they achieve their goals in fundamentally different ways. Understanding their distinct approaches and shared objectives is crucial for businesses looking to improve efficiency and reduce waste. This article will delve into the core goals of both Kanban and MRP, highlighting their similarities and differences, and exploring scenarios where each system shines.
Shared Goals: Efficiency and Waste Reduction
Despite their contrasting methodologies, Kanban and MRP share some key objectives:
1. Optimizing Inventory Levels:
Both systems aim to maintain optimal inventory levels. Neither advocates for excessive stockpiles that tie up capital and risk obsolescence, nor for stockouts that halt production and disappoint customers. The difference lies in how they achieve this optimization. Kanban focuses on a just-in-time (JIT) approach, replenishing inventory only when needed, while MRP uses forecasting and planned orders to anticipate demand.
2. Improving Production Flow:
Both Kanban and MRP aim to streamline production processes, minimizing bottlenecks and delays. By visualizing workflow (Kanban) or precisely scheduling material delivery (MRP), both methods contribute to a smoother, more predictable production cycle. This leads to faster lead times and increased customer satisfaction.
3. Reducing Waste:
Both systems explicitly aim to reduce various forms of waste, although they target different types. Kanban focuses on minimizing waste associated with overproduction, inventory, waiting, transportation, motion, over-processing, and defects. MRP, while less directly focused on these lean principles, indirectly contributes to waste reduction by preventing stockouts and ensuring materials are available when needed, thereby minimizing wasted time and resources.
Kanban's Goals: Visualizing and Optimizing Workflow
Kanban, derived from the Japanese word for "signboard," is a visual system for managing workflow. Its core goals revolve around visualizing the flow of work, limiting work in progress (WIP), and continuously improving the process.
1. Visualizing Workflow:
This is the cornerstone of Kanban. By using a Kanban board (physical or digital), teams can see the status of every task or item in the process. This transparency allows for quicker identification of bottlenecks, delays, and potential problems. The visual nature makes it easier to understand the overall flow and identify areas for improvement.
2. Limiting Work in Progress (WIP):
Kanban emphasizes limiting the number of tasks in progress at any given time. This prevents multitasking and context switching, leading to increased focus and faster completion times. By focusing on completing fewer tasks at a time, the team can improve quality and reduce the risk of errors.
3. Continuous Improvement (Kaizen):
Kanban is not a static system. It encourages continuous improvement through regular review meetings (often called Kanban meetings) where the team identifies bottlenecks, discusses improvements, and adjusts the workflow as needed. This iterative approach allows teams to adapt to changing conditions and continuously optimize their processes.
4. Enhancing Collaboration and Communication:
The visual nature of Kanban fosters better communication and collaboration among team members. Everyone can see the status of tasks, identify dependencies, and quickly understand the overall progress. This shared understanding promotes teamwork and improves accountability.
5. Delivering Value Faster:
By optimizing workflow and reducing bottlenecks, Kanban helps deliver value to customers faster. The focus on limiting WIP and continuous improvement ensures that tasks are completed more efficiently, resulting in quicker turnaround times and improved customer satisfaction.
MRP's Goals: Planning and Scheduling Material Requirements
Material Requirements Planning (MRP) is a computer-based system used to manage inventory and plan production. Its goals are primarily focused on ensuring that the right materials are available at the right time to meet production demands.
1. Accurate Demand Forecasting:
MRP begins with forecasting future demand for finished goods. Accurate demand forecasting is crucial for the entire system's effectiveness. Inaccurate forecasting leads to either excess inventory or stockouts, undermining the system's core goals. Sophisticated MRP systems utilize various forecasting techniques to improve accuracy.
2. Determining Material Requirements:
Once demand is forecasted, MRP calculates the precise quantity and timing of raw materials, components, and sub-assemblies required to meet that demand. This "explosion" of the bill of materials (BOM) ensures that all necessary components are ordered and received in a timely manner.
3. Scheduling Production and Procurement:
MRP creates a production schedule and a procurement schedule. The production schedule outlines the manufacturing process, specifying which products to produce, when to produce them, and the required resources. The procurement schedule details when to order raw materials and components from suppliers.
4. Managing Inventory:
MRP helps manage inventory levels by identifying when materials are needed and ensuring that sufficient stock is available to meet production demands. It aims to minimize inventory holding costs while avoiding stockouts that can disrupt production. This often involves careful consideration of safety stock levels to account for unexpected delays or variations in demand.
5. Optimizing Production Capacity:
By considering production capacity constraints, MRP can help optimize resource utilization. It helps prevent over-scheduling and ensures that the production plan is realistic and achievable, leading to improved efficiency and reduced lead times.
6. Reducing Lead Times:
Through effective planning and scheduling, MRP can contribute to reduced lead times. By ensuring materials are readily available and production is efficiently sequenced, the overall time required to manufacture and deliver finished goods can be minimized.
Comparing Kanban and MRP: When to Use Which
While both aim for efficiency, Kanban and MRP excel in different contexts:
-
Kanban is ideal for: Projects with evolving requirements, knowledge work, software development, small to medium-sized teams, and situations needing quick adaptation to change. Its focus on visualizing workflow, limiting WIP, and continuous improvement makes it very effective in dynamic environments.
-
MRP is ideal for: Manufacturing environments with complex BOMs, high demand predictability, large-scale production, and a need for precise material planning and scheduling. Its strength lies in accurate forecasting and efficient planning of material procurement and production.
Synergies Between Kanban and MRP
Interestingly, Kanban and MRP aren't mutually exclusive. They can complement each other in some scenarios. For example, a manufacturing company might use MRP for overall production planning and material procurement but employ Kanban within individual production cells or work areas to manage the flow of work and reduce bottlenecks. This combined approach leverages the strengths of both systems, improving efficiency and reducing waste across the entire value chain.
Conclusion: Achieving Operational Excellence
Both Kanban and MRP represent valuable tools for achieving operational excellence. Kanban excels in visualizing workflow and optimizing processes, while MRP focuses on precisely planning material requirements and scheduling production. The choice between them depends on the specific needs and characteristics of the organization and the nature of its operations. Understanding the goals of each system is critical for selecting and implementing the appropriate methodology or a hybrid approach that maximizes efficiency and minimizes waste. By embracing a data-driven approach to inventory management and workflow optimization, businesses can significantly improve productivity, reduce costs, and enhance their competitiveness in today’s dynamic market.
Latest Posts
Latest Posts
-
Las Playas De Isla Del Sol Son Muy Limpias
Apr 19, 2025
-
The Purpose Of Examining A Clients Family Constellation Is To
Apr 19, 2025
-
Calculating Gross Earnings In The Payroll Process Is The
Apr 19, 2025
-
What Is One Of The Key Indicators Of Primates Adaptability
Apr 19, 2025
-
Most Flake Ice Machines Utilize This Type Of Evaporator
Apr 19, 2025
Related Post
Thank you for visiting our website which covers about The Goals Of Both Kanban And Mrp Include . We hope the information provided has been useful to you. Feel free to contact us if you have any questions or need further assistance. See you next time and don't miss to bookmark.