The Least Efficient Type Of Transformer Is The
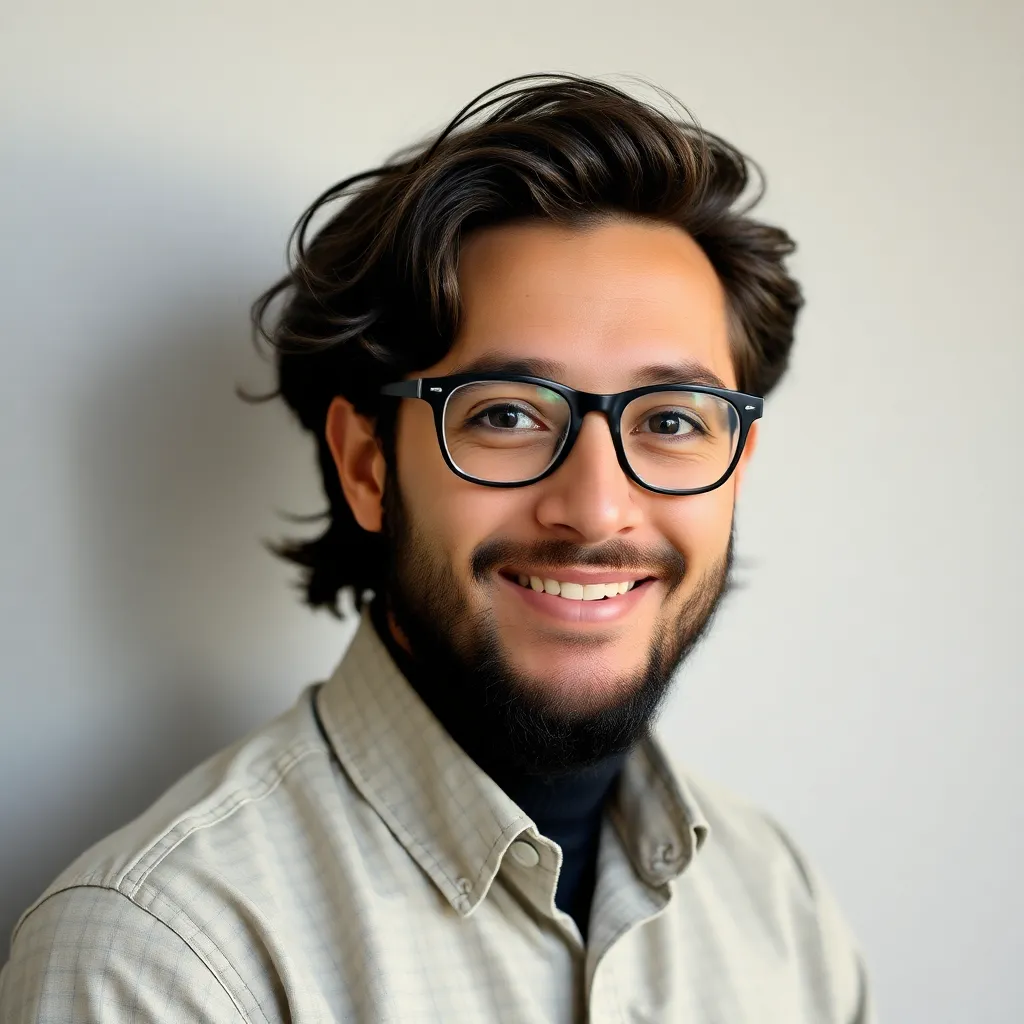
Breaking News Today
Apr 19, 2025 · 5 min read

Table of Contents
The Least Efficient Type of Transformer Is the… (It's Complicated!)
Transformers, those ubiquitous devices humming quietly in electrical substations and powering our homes, aren't all created equal. While incredibly efficient in general, certain designs and operating conditions lead to significantly lower efficiency than others. Pinpointing the single least efficient type is difficult, as efficiency depends on a complex interplay of factors. However, we can examine several transformer types and their inherent weaknesses to understand which are generally considered less efficient and why. The answer isn't a single definitive model, but rather a range of factors contributing to lower performance.
Understanding Transformer Efficiency
Before delving into specific inefficient types, let's establish the key factors impacting transformer efficiency. Efficiency, often expressed as a percentage, represents the ratio of output power to input power. Losses, therefore, represent the difference between input and output power. These losses are broadly categorized into:
1. Core Losses (Iron Losses):
- Hysteresis Losses: These are caused by the continuous magnetization and demagnetization of the transformer core as the AC current changes direction. The energy required to overcome this molecular friction is lost as heat. Materials with lower hysteresis coefficients, like grain-oriented silicon steel, minimize this loss.
- Eddy Current Losses: These are due to circulating currents induced within the core material by the changing magnetic flux. These currents generate heat, reducing efficiency. Laminating the core (creating thin sheets insulated from each other) significantly reduces eddy current losses.
2. Winding Losses (Copper Losses):
- I²R Losses (Joule Heating): These are caused by the resistance of the copper windings. As current flows through the windings, heat is generated, proportional to the square of the current and the resistance. Using larger-gauge wire reduces resistance but increases cost and size.
3. Stray Losses:
- Leakage Flux Losses: Not all magnetic flux generated by the primary winding links the secondary winding. The "leakage flux" creates losses in the surrounding air and other components. Careful design and construction minimize leakage flux.
- Magnetostriction Losses: These losses arise from the physical expansion and contraction of the core material due to magnetization. This mechanical vibration generates heat and noise.
Contenders for the Least Efficient Title:
While no single transformer type is universally the "least efficient," certain designs and operating conditions significantly contribute to lower performance. Here are some prime contenders:
1. Transformers with Poor Core Material:
Transformers using low-quality or outdated core materials will inherently suffer from higher hysteresis and eddy current losses. Older transformers, especially those employing cores made from materials with high hysteresis and high resistivity, will demonstrate significantly lower efficiency than modern ones using high-grade silicon steel or amorphous metal alloys. Poor core material selection directly impacts efficiency.
2. Poorly Designed or Manufactured Transformers:
Manufacturing defects, such as poor winding insulation, loose laminations, or air gaps within the core, dramatically increase losses and reduce efficiency. Inconsistent winding density and imperfect core construction lead to increased leakage flux and higher losses. These issues are more likely to be found in low-cost, poorly engineered transformers.
3. Transformers Operating Outside their Rated Capacity:
Operating a transformer at significantly higher loads than its rated capacity causes excessive I²R losses in the windings. The increased current flow generates substantially more heat, reducing efficiency. Conversely, operating far below its rated capacity leads to higher losses relative to the lower output power, also reducing efficiency though to a lesser extent. Optimal operation within the rated power range is crucial for efficiency.
4. Transformers with High Leakage Inductance:
Transformers with high leakage inductance suffer from increased leakage flux, leading to greater losses. This can be a result of poor design or manufacturing imperfections. Minimizing leakage flux is a critical design consideration for achieving high efficiency.
5. Older, Unserviced Transformers:
Over time, transformer insulation degrades, windings may become loose, and core laminations can become oxidized or separated. These factors lead to increased losses and reduced efficiency. Regular inspection and maintenance, including cleaning and tightening connections, can significantly extend the lifespan and improve the performance of transformers. Neglecting maintenance contributes substantially to reduced efficiency.
6. Small, Low-Power Transformers:
While not inherently inefficient in terms of percentage losses, very small, low-power transformers often have proportionally higher losses because the manufacturing constraints limit the optimization possibilities. The surface area-to-volume ratio is higher in smaller transformers, leading to increased heat dissipation issues which affect efficiency.
Improving Transformer Efficiency:
Several design and manufacturing techniques aim to enhance transformer efficiency. These include:
- Using high-quality core materials: Employing materials with low hysteresis and eddy current losses, such as grain-oriented silicon steel or amorphous metal alloys, is crucial.
- Optimizing core design: Careful design minimizes leakage flux and reduces magnetostriction losses.
- Employing efficient winding techniques: Techniques like interleaving windings can reduce leakage inductance.
- Using larger gauge wire: Larger wire reduces I²R losses, though this increases cost and size.
- Improved insulation: High-quality insulation reduces partial discharge and minimizes winding losses.
- Advanced cooling techniques: Implementing effective cooling systems removes generated heat, maintaining optimal operating temperature and efficiency.
Conclusion:
Identifying the single "least efficient" transformer type is misleading. Efficiency is a function of design, materials, manufacturing quality, operating conditions, and age. Transformers with poor core materials, design flaws, excessive loading, or those that are poorly maintained exhibit considerably lower efficiency compared to well-designed and maintained units. Focusing on using high-quality components, optimizing designs to minimize losses, and adhering to proper operating parameters are paramount in ensuring optimal transformer efficiency. The key is understanding the interplay of factors and prioritizing design and manufacturing choices that minimize losses in all operating conditions.
Latest Posts
Latest Posts
-
Weekly Language Review Q1 2 Answer Key
Apr 19, 2025
-
The Are Bevel Gears Held By The Pinion Shaft
Apr 19, 2025
-
What Is The Minimum Amount Of Shrinkage For Curly Hair
Apr 19, 2025
-
Sugar Changed The World Part 4 Building Claims
Apr 19, 2025
-
End Of Semester Test Us History Semester A
Apr 19, 2025
Related Post
Thank you for visiting our website which covers about The Least Efficient Type Of Transformer Is The . We hope the information provided has been useful to you. Feel free to contact us if you have any questions or need further assistance. See you next time and don't miss to bookmark.