The Objective Of Inventory Management Is To
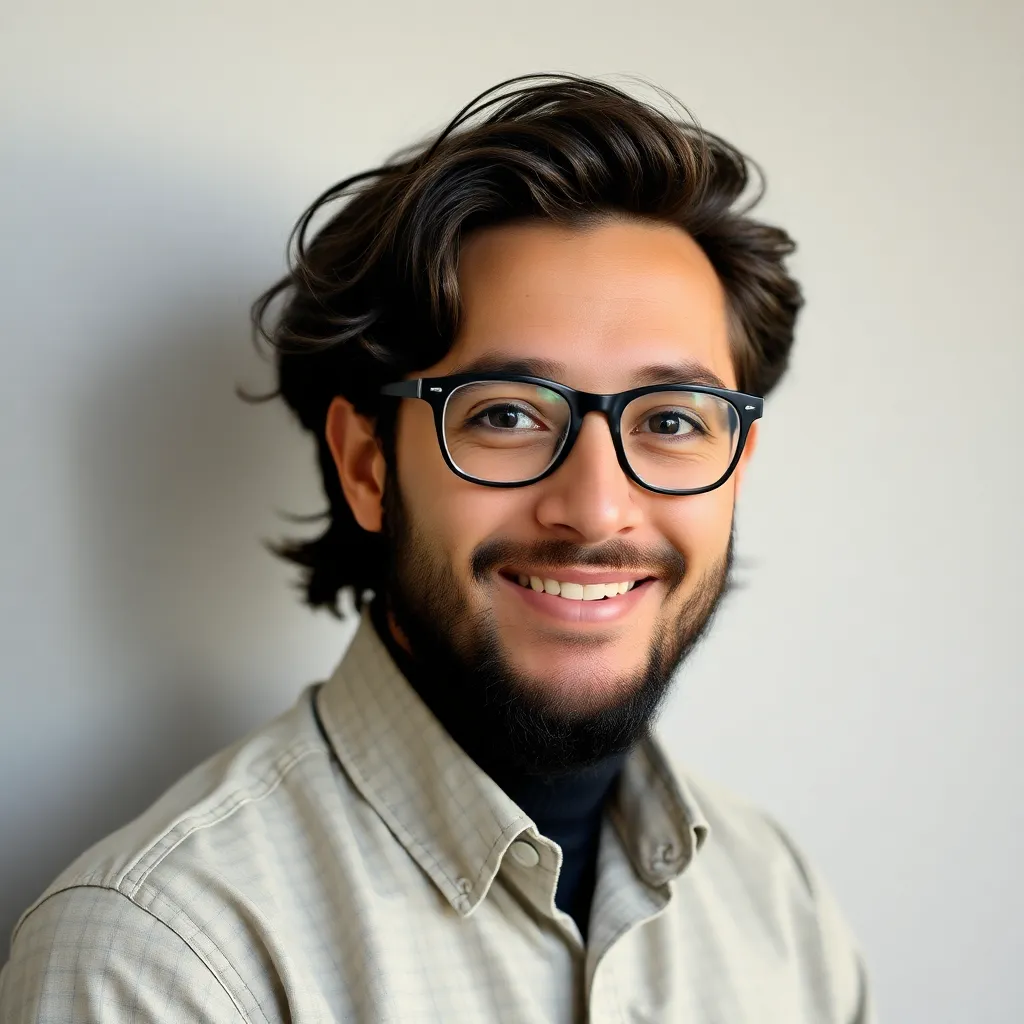
Breaking News Today
Mar 13, 2025 · 6 min read
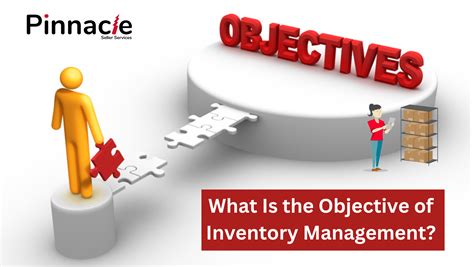
Table of Contents
The Objective of Inventory Management Is To… Strike a Delicate Balance
Inventory management: the very phrase conjures images of bustling warehouses, meticulous stocktaking, and the constant pressure to meet demand. But beneath the surface of these logistical operations lies a much more nuanced objective. It's not simply about having inventory; it's about strategically optimizing its presence to maximize profitability and minimize risk. The ultimate objective of inventory management is to strike a delicate balance between ensuring sufficient stock to meet customer demand and minimizing the costs associated with holding that stock. This intricate dance requires a multifaceted approach encompassing forecasting, storage, tracking, and control. Let's delve deeper into the core objectives and strategies that form the backbone of effective inventory management.
1. Meeting Customer Demand: The Foundation of Success
At its core, inventory management exists to support the customer. Without sufficient stock to meet orders, a business risks losing sales, damaging its reputation, and ultimately hindering its growth. This involves:
1.1 Accurate Demand Forecasting: Predicting the Future
Predicting future demand is arguably the most crucial aspect of successful inventory management. This isn't about gazing into a crystal ball; rather, it's about leveraging data analysis and forecasting techniques to estimate future sales volumes. Factors to consider include:
- Historical sales data: Analyzing past sales trends provides a valuable baseline for forecasting future demand. Seasonal variations, promotional periods, and economic factors should all be considered.
- Market trends: Keeping an eye on broader market trends, such as changes in consumer preferences or the emergence of new competitors, is essential for accurate forecasting.
- External factors: External factors like economic downturns, supply chain disruptions, or even weather patterns can significantly impact demand. Building these considerations into forecasts is crucial.
- Sales promotions and marketing campaigns: Planned sales promotions and marketing campaigns can dramatically influence demand, requiring adjustments to inventory levels.
1.2 Maintaining Optimal Stock Levels: Avoiding Shortages and Excess
Once demand is forecasted, the next step is to determine optimal stock levels. This involves finding the sweet spot between having enough inventory to meet anticipated demand and avoiding excess stock that ties up capital and incurs storage costs. Techniques like:
- Economic Order Quantity (EOQ): This classic model calculates the optimal order size to minimize total inventory costs, considering ordering costs and holding costs.
- Reorder Point (ROP): This determines the inventory level at which a new order should be placed to avoid stockouts, taking into account lead time and demand variability.
- Safety Stock: Maintaining a safety stock buffer helps mitigate unexpected demand spikes or supply chain disruptions, ensuring continuous customer fulfillment.
2. Minimizing Costs: The Balancing Act
While ensuring sufficient stock is paramount, effective inventory management must also focus on minimizing the costs associated with holding that inventory. These costs can be substantial and significantly impact profitability.
2.1 Holding Costs: The Hidden Expenses
Holding costs encompass all expenses incurred from storing and maintaining inventory. These include:
- Storage costs: Rent, utilities, and insurance for warehouse space.
- Insurance costs: Protecting inventory against damage, theft, or obsolescence.
- Obsolescence costs: The loss of value due to technological advancements, changing consumer preferences, or product expiration.
- Taxes: Property taxes or other taxes levied on inventory.
- Capital costs: The cost of tying up capital in inventory that could be used for other investments.
- Spoilage and waste: The cost of damaged, spoiled, or unusable inventory.
- Handling costs: Costs related to moving inventory within the warehouse or between locations.
2.2 Ordering Costs: The Price of Replenishment
Ordering costs involve all expenses related to placing and receiving new inventory orders. These include:
- Processing costs: The administrative costs associated with placing an order.
- Shipping costs: The cost of transporting inventory from suppliers to the warehouse.
- Receiving costs: Costs associated with inspecting and processing incoming inventory.
- Quality control costs: Checking for quality issues upon receipt of inventory.
2.3 Minimizing Waste: A Key Cost Reduction Strategy
Minimizing waste in the inventory management process is crucial for reducing costs and maximizing efficiency. This involves:
- Effective forecasting: Reducing inaccurate forecasting minimizes excess inventory and related costs.
- Efficient storage: Optimizing warehouse space and using appropriate storage solutions reduces handling costs and storage space expenses.
- Regular stocktaking: Accurate stocktaking helps to identify and address potential problems like damaged or obsolete goods early on.
- First-In, First-Out (FIFO) and Last-In, First-Out (LIFO): Implementing appropriate inventory management methods such as FIFO and LIFO helps reduce spoilage and waste. FIFO ensures that older items are used first, minimizing obsolescence.
- Implementing a robust quality control system: This prevents the acceptance of faulty items that would later lead to costly returns or disposal.
3. Enhancing Efficiency and Productivity: Streamlining Operations
Effective inventory management isn't just about minimizing costs; it also plays a vital role in enhancing efficiency and productivity across the entire supply chain. This includes:
3.1 Streamlined Processes: Minimizing Bottlenecks
Streamlining inventory processes involves identifying and eliminating bottlenecks that hinder efficiency. This could involve:
- Automating tasks: Automating tasks such as order placement, stock tracking, and reporting reduces manual workload and errors.
- Improving communication: Effective communication between different departments (e.g., purchasing, warehouse, sales) ensures smooth inventory flow.
- Optimizing warehouse layout: Designing a warehouse layout that minimizes movement of goods saves time and resources.
- Employing barcoding and RFID technologies: Implementing these technologies enhances tracking and reduces manual counting and errors.
3.2 Improved Inventory Visibility: Real-time Tracking
Real-time inventory visibility allows businesses to track inventory levels across all locations, providing crucial data for informed decision-making. This enhances:
- Accurate forecasting: Real-time data enables more accurate demand forecasting, leading to optimized stock levels.
- Proactive problem-solving: Early identification of potential problems, such as stockouts or excess inventory, allows for prompt corrective action.
- Faster order fulfillment: Accurate inventory information leads to quicker order processing and fulfillment.
4. Maintaining Inventory Accuracy: The Foundation of Control
Maintaining accurate inventory records is essential for the effectiveness of the entire inventory management system. This involves:
4.1 Regular Stocktaking: Ensuring Accuracy
Regular physical stocktaking, coupled with periodic cycle counts, helps to identify discrepancies between physical inventory and recorded levels.
4.2 Implementing Inventory Management Software: Automating Processes
Investing in inventory management software automates many tasks, reducing manual effort and errors, and providing real-time inventory visibility.
4.3 Implementing Robust Inventory Control Systems: Minimizing Losses
Robust inventory control systems encompass all the processes and procedures used to track, manage, and control inventory. This includes setting reorder points, implementing safety stock levels, and regular stocktaking.
5. Adaptability and Flexibility: Navigating Change
The business environment is constantly evolving. Therefore, an effective inventory management strategy must be adaptable and flexible enough to respond to changes in demand, supply chain disruptions, and other unforeseen circumstances. This requires:
- Regular review and adjustment: The inventory management strategy should be regularly reviewed and adjusted to reflect changes in business conditions.
- Contingency planning: Businesses should have contingency plans in place to handle unexpected disruptions to the supply chain or sudden spikes in demand.
- Data-driven decision making: Data analysis should guide decision-making, allowing for a more agile and responsive inventory management strategy.
Conclusion: The Holistic Approach to Inventory Management
The objective of inventory management is not a single, isolated goal, but a holistic approach encompassing multiple interwoven objectives. It's about striking a delicate balance between meeting customer demands, minimizing costs, enhancing efficiency, and maintaining accuracy. By implementing the strategies outlined above, businesses can optimize their inventory management processes, leading to improved profitability, reduced risk, and a stronger competitive position. It's a continuous journey of refinement, adaptation, and a constant pursuit of that perfect equilibrium between supply and demand.
Latest Posts
Latest Posts
-
When The First Referee Tells The Scorer
Mar 13, 2025
-
A 19 Year Old Female Has Just Been Extricated
Mar 13, 2025
-
Nurse Logic Knowledge And Clinical Judgment Advanced
Mar 13, 2025
-
New York State Notary Public Exam Study Guide
Mar 13, 2025
-
Mario Traerte La Camara Digital Que Le Regalo Gema
Mar 13, 2025
Related Post
Thank you for visiting our website which covers about The Objective Of Inventory Management Is To . We hope the information provided has been useful to you. Feel free to contact us if you have any questions or need further assistance. See you next time and don't miss to bookmark.