The Pipe Schedule Table Method Is Limited To: Quizlet
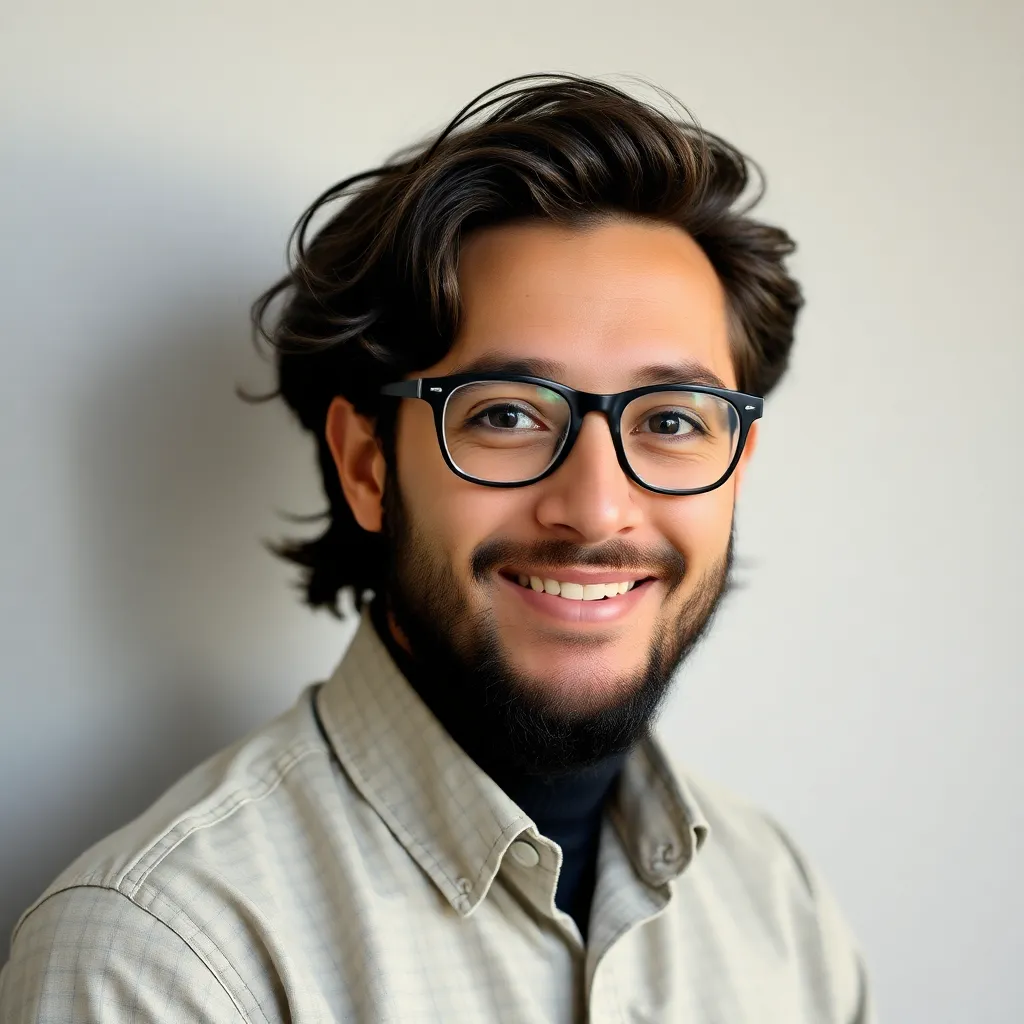
Breaking News Today
Mar 30, 2025 · 6 min read
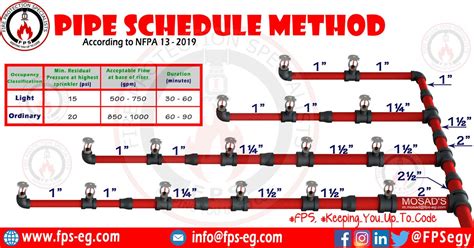
Table of Contents
The Pipe Schedule Table Method: Limitations and Beyond
The pipe schedule table method, a cornerstone of piping system design, provides a convenient way to quickly determine pipe dimensions and properties. However, relying solely on this method presents significant limitations. This article delves deep into these limitations, exploring the scenarios where the pipe schedule table method falls short and highlighting alternative methods and considerations for comprehensive pipe design.
Understanding the Pipe Schedule Table Method
Before exploring the limitations, let's briefly revisit the fundamentals. The pipe schedule table method utilizes a standardized system to classify pipes based on their wall thickness. The schedule number, a numerical designation (e.g., Schedule 40, Schedule 80), correlates directly with the pipe's wall thickness for a given nominal pipe size (NPS). Thicker schedules imply higher pressure ratings and greater structural strength. These tables typically provide information including:
- Nominal Pipe Size (NPS): This is a nominal designation, not the exact outside diameter.
- Outside Diameter (OD): The actual outer diameter of the pipe.
- Wall Thickness (WT): The thickness of the pipe wall.
- Inside Diameter (ID): The inner diameter of the pipe.
- Weight per Foot: The weight of a one-foot length of the pipe.
The convenience lies in its simplicity. By knowing the desired pressure rating and nominal pipe size, one can quickly look up the appropriate schedule and obtain the necessary dimensions. However, this convenience masks several critical limitations.
Limitations of the Pipe Schedule Table Method: A Detailed Examination
The pipe schedule table method, despite its widespread use, is limited in several key aspects:
-
Limited Material Specifications: Schedule tables primarily focus on standard materials like carbon steel. They often lack comprehensive data for other materials like stainless steel, alloys, plastics, or composite pipes, each possessing unique properties influencing their suitability for specific applications. Specialized applications demanding specific material properties necessitate using more extensive material property databases and engineering calculations beyond the scope of standard schedule tables.
-
Pressure Rating Dependency on Material: The pressure rating associated with a particular schedule is heavily dependent on the material's yield strength and operating temperature. The tables often assume specific material properties and operating temperatures, which might not always align with real-world conditions. Variations in material composition, manufacturing processes, or operating temperatures can significantly alter the actual pressure rating, making reliance on schedule tables alone risky.
-
Temperature Effects: The pressure ratings provided in schedule tables are generally based on ambient or moderate temperatures. Elevated temperatures can significantly reduce the material's yield strength, impacting the pipe's pressure-bearing capacity. High-temperature applications require detailed stress analysis and potentially the use of specialized high-temperature alloys or designs not explicitly covered in the standard schedule tables. Neglecting temperature effects can lead to significant safety risks.
-
Corrosion Allowance: Schedule tables don't inherently account for corrosion allowance. Over time, pipe walls can corrode, reducing their thickness and potentially compromising structural integrity and pressure ratings. Designing for long-term service requires incorporating a corrosion allowance into the wall thickness calculation, a factor not directly addressed in standard schedule tables. This necessitates more detailed calculations and considerations beyond simple table lookup.
-
Ignoring Specific Application Requirements: The schedule tables only provide generic data. They do not account for the unique demands of specific applications like those involving vibration, cyclic loading, seismic activity, or unusual environmental conditions. Extreme environments or highly demanding operating conditions require far more sophisticated design considerations and may require specialized pipe designs or materials not represented in the schedule tables.
-
Lack of Information on Other Relevant Properties: Beyond dimensions and pressure ratings, many other pipe properties are crucial for complete design, including:
- Roughness: Affects fluid flow characteristics and pressure drop calculations.
- Thermal Expansion Coefficient: Important for thermal stress analysis.
- Fatigue Strength: Critical for applications involving cyclic loading.
- Flexibility and Bendability: Relevant for pipeline routing and installation. Standard schedule tables typically don't provide extensive data on these, necessitating further research into specific material properties.
-
Limited Applicability to Non-Circular Pipes: The schedule table method primarily focuses on circular pipes. Non-circular pipes (e.g., rectangular, oval) require different design approaches and calculations based on their specific geometries and loading conditions.
-
No Consideration for Fittings and Valves: The schedule tables apply to pipe sections only. Fittings (elbows, tees, reducers) and valves introduce additional stress concentrations and pressure drops, which are not directly addressed within the scope of the schedule table method. These components demand careful consideration and may even require special designs or higher schedule ratings to mitigate potential failure points.
-
Oversimplification of Complex Systems: Real-world piping systems often involve complex geometries, varying pressures, multiple fluids, and diverse operating conditions. The schedule table approach, by its very nature, oversimplifies these complexities and could lead to underdesign or overdesign if applied without careful consideration of the entire system.
Beyond the Pipe Schedule Table: Alternative Approaches
Given the limitations discussed above, relying solely on the pipe schedule table is often insufficient for comprehensive and robust piping system design. Engineers utilize several alternative methods and tools to ensure safe and reliable systems:
-
Detailed Engineering Calculations: For complex scenarios or critical applications, detailed engineering calculations based on fundamental fluid mechanics principles, stress analysis, and material properties are necessary. Software packages specifically designed for piping system design aid in these complex calculations, accounting for numerous factors often overlooked in the schedule table approach.
-
Finite Element Analysis (FEA): FEA is a powerful computational technique for simulating stress and strain distribution within complex pipe geometries and under various loading conditions. This approach provides a much more refined and accurate assessment of structural integrity compared to simply looking up values in a table.
-
Specialized Design Codes and Standards: Codes such as ASME B31.1 (Power Piping) and ASME B31.3 (Process Piping) provide comprehensive guidelines for piping system design, including detailed calculations, material selection criteria, and specific requirements for different applications. These codes transcend the limitations of simple schedule tables, addressing a wider array of considerations for complex and critical piping systems.
-
Material Property Databases: Comprehensive databases provide accurate material properties, accounting for temperature effects, corrosion rates, and other critical parameters. These databases provide the necessary input data for more advanced design calculations, surpassing the limited material scope inherent in schedule tables.
-
Software and Simulation Tools: Specialized software packages facilitate complex pipe design calculations, handling the complexities of fluid flow, pressure drop, stress analysis, and thermal effects. These tools significantly enhance the accuracy and efficiency of piping system design, addressing limitations of the simplified table-based approach.
Conclusion: A Balanced Approach to Pipe Design
The pipe schedule table method serves as a valuable initial tool for quick estimation and preliminary design. However, its inherent limitations necessitate a more comprehensive approach for critical applications. A balanced strategy combines the simplicity of the schedule table with more rigorous calculations, advanced simulation tools, and adherence to relevant design codes to ensure the design of robust, safe, and reliable piping systems. Over-reliance on the schedule table method, without thorough understanding of its shortcomings and the use of appropriate alternative methods, can lead to inadequate designs with potential safety and economic consequences. Therefore, a holistic approach employing multiple methods and techniques, guided by relevant codes and standards, remains crucial for successful and safe piping system design.
Latest Posts
Latest Posts
-
Many Jacks Use Hydraulic Power True False
Apr 01, 2025
-
Job Specifications Are Often Referred To As
Apr 01, 2025
-
Which Of The Following Is An Example Of Indexing
Apr 01, 2025
-
King Uses The Check And Promissory Note Metaphors To
Apr 01, 2025
-
Poor Maintenance Of Home Poor Personal Care
Apr 01, 2025
Related Post
Thank you for visiting our website which covers about The Pipe Schedule Table Method Is Limited To: Quizlet . We hope the information provided has been useful to you. Feel free to contact us if you have any questions or need further assistance. See you next time and don't miss to bookmark.