The Reorder Point For An Item Is Calculated Based On
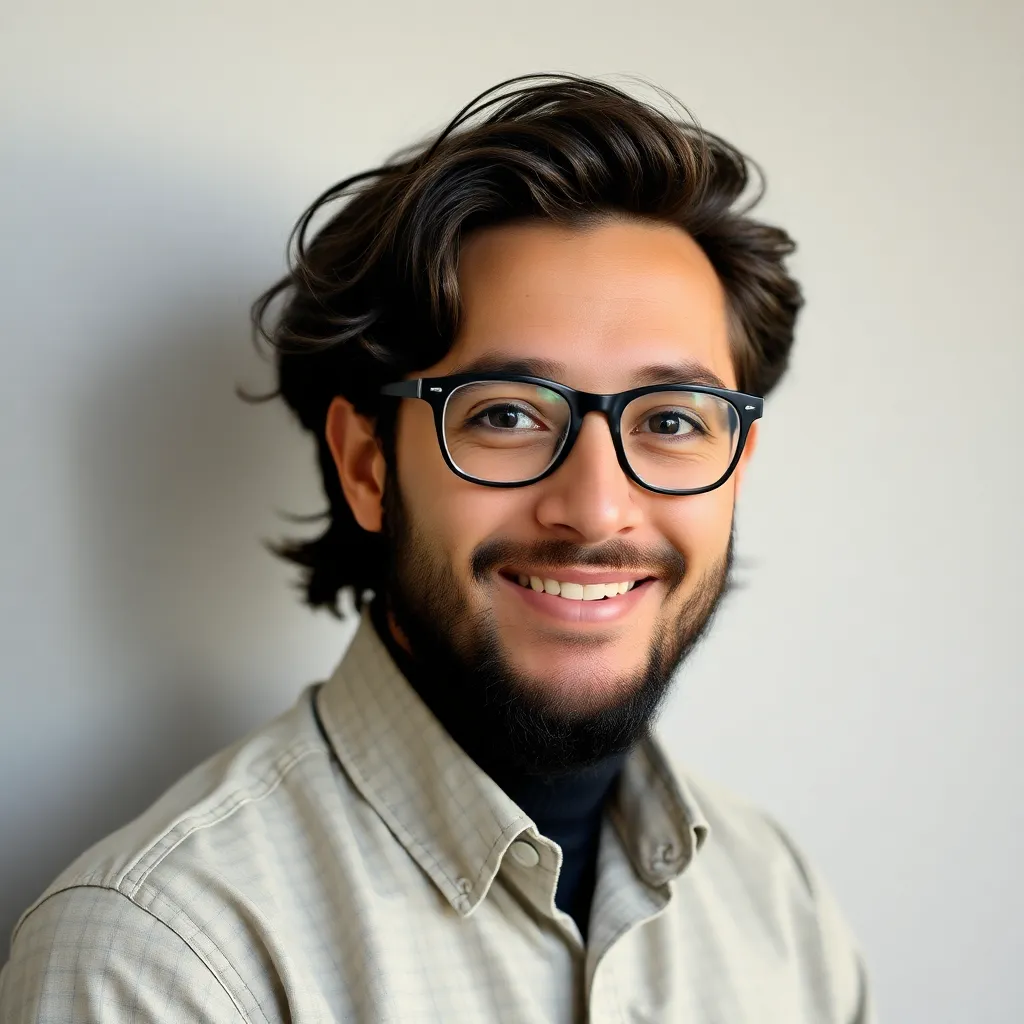
Breaking News Today
Apr 12, 2025 · 5 min read

Table of Contents
The Reorder Point: Calculating When to Replenish Inventory
Inventory management is the backbone of any successful business, regardless of size or industry. Efficient inventory control ensures smooth operations, minimizes stockouts, and maximizes profitability. A crucial element of this process is determining the reorder point (ROP). Understanding how to calculate the reorder point is vital for optimizing inventory levels and avoiding costly consequences. This comprehensive guide delves into the intricacies of reorder point calculation, exploring various factors, formulas, and scenarios to help you master this essential aspect of inventory management.
What is the Reorder Point (ROP)?
The reorder point is the inventory level at which a new order should be placed to replenish stock. It's the point where your existing inventory is low enough that you risk running out before your next order arrives. Accurately determining your reorder point prevents stockouts, which can lead to lost sales, dissatisfied customers, and damaged business reputation. Conversely, setting the reorder point too high leads to excess inventory, tying up capital and increasing storage costs.
Factors Affecting Reorder Point Calculation
Several factors influence the calculation of the reorder point. Ignoring these factors can lead to inaccurate calculations and suboptimal inventory management. Let's examine the key elements:
1. Lead Time Demand
This is perhaps the most critical factor. Lead time demand refers to the amount of inventory consumed during the time it takes to receive a new order. It's calculated by multiplying the average daily demand by the lead time.
-
Average Daily Demand: This represents the average number of units sold or used per day. It's calculated by analyzing historical sales data over a specified period. Consider seasonality and trends when calculating this average. A simple calculation could be Total Units Sold / Number of Days.
-
Lead Time: This is the time it takes for an order to be placed and received. It includes order processing time, shipping time, and any potential delays. Accurate lead time estimation is crucial for effective ROP calculation.
Example: If your average daily demand is 10 units and your lead time is 5 days, the lead time demand is 10 units/day * 5 days = 50 units.
2. Safety Stock
Safety stock is the extra inventory held to buffer against unexpected fluctuations in demand or lead time. It acts as a cushion to prevent stockouts during periods of higher-than-anticipated demand or longer-than-expected lead times. The amount of safety stock depends on several factors including:
-
Demand Variability: Higher demand variability necessitates higher safety stock. This is often measured using standard deviation.
-
Lead Time Variability: Unpredictable lead times require greater safety stock to mitigate the risk of delays.
-
Service Level: The desired service level, or the probability of not experiencing a stockout, directly impacts the safety stock level. A higher service level requires more safety stock.
Calculating safety stock involves statistical methods, often employing the standard deviation of demand and lead time. More sophisticated methods consider the correlation between demand and lead time variability.
3. Reorder Point Formula
The basic reorder point formula is:
ROP = (Lead Time Demand) + Safety Stock
This formula combines the lead time demand and safety stock to arrive at the optimal reorder point. More advanced formulas incorporate statistical measures for demand and lead time variability, providing a more accurate and robust calculation.
Advanced Reorder Point Calculations
For more precise control, especially when dealing with products with high demand variability or unpredictable lead times, more complex calculations are necessary. These calculations often involve statistical analysis and probability theory.
Incorporating Standard Deviation
A more advanced formula considers the standard deviation of lead time demand:
ROP = (Average Lead Time Demand) + (Z-score * Standard Deviation of Lead Time Demand)
Where:
-
Z-score: This represents the desired service level. A higher Z-score corresponds to a higher service level (and thus, higher safety stock). You can find Z-scores corresponding to various service levels in a standard normal distribution table. For example, a 95% service level has a Z-score of approximately 1.65.
-
Standard Deviation of Lead Time Demand: This measures the variability of lead time demand. It reflects the uncertainty in predicting the exact amount of inventory needed during lead time.
This formula provides a more nuanced calculation, taking into account the inherent uncertainty in demand and lead time.
Considering Lead Time Variability
If lead time itself is variable, the calculation becomes even more complex. This often involves using a distribution that considers both demand and lead time variability simultaneously. Specialized inventory management software can simplify this process.
Practical Applications and Considerations
The accurate calculation of the reorder point is crucial for effective inventory management. However, several practical considerations must be kept in mind:
-
Regular Review and Adjustment: The reorder point is not a static number. Regularly review and adjust your ROP based on changes in demand, lead times, and other relevant factors. Seasonal fluctuations, marketing campaigns, and economic conditions can significantly influence demand.
-
Data Accuracy: The accuracy of your ROP calculation depends entirely on the accuracy of your input data. Maintain accurate records of sales, inventory levels, and lead times.
-
Inventory Management Software: For businesses with a large and diverse inventory, specialized inventory management software can automate the reorder point calculation, providing real-time insights and alerts.
-
Economic Order Quantity (EOQ): The reorder point calculation should be considered in conjunction with the Economic Order Quantity (EOQ). EOQ determines the optimal order size to minimize inventory costs. Combining ROP and EOQ provides a holistic approach to inventory optimization.
-
ABC Analysis: Categorizing inventory items based on their value and demand (ABC analysis) allows for focused attention on high-value items, ensuring precise ROP calculations for those items.
Conclusion
Calculating the reorder point is a fundamental aspect of inventory management. Understanding the factors that influence the ROP, employing appropriate formulas, and regularly reviewing and adjusting your calculations are crucial for optimizing inventory levels, minimizing costs, and ensuring business success. While the basic formula provides a starting point, incorporating standard deviation and considering lead time variability enhances accuracy and effectiveness, particularly for businesses dealing with high demand variability or unpredictable lead times. By mastering the reorder point calculation and integrating it with other inventory management techniques, businesses can achieve greater efficiency, reduce waste, and improve overall profitability. Remember to choose the method that best suits the complexity and needs of your business. Continuous monitoring and adaptation are key to achieving optimal inventory levels and maintaining a competitive edge in today’s dynamic market.
Latest Posts
Latest Posts
-
Tacts Are Easier To Teach Than Mands
Apr 18, 2025
-
Refraction Occurs When A Wave Changes Its
Apr 18, 2025
-
What Do Sound Energy And Thermal Energy Have In Common
Apr 18, 2025
-
In The Term Oste O Arthr O Pathy Which Part Is The Suffix
Apr 18, 2025
-
Everyone Should Exercise With The Same Frequency
Apr 18, 2025
Related Post
Thank you for visiting our website which covers about The Reorder Point For An Item Is Calculated Based On . We hope the information provided has been useful to you. Feel free to contact us if you have any questions or need further assistance. See you next time and don't miss to bookmark.