The Rotating Windings Of A Dc Motor.
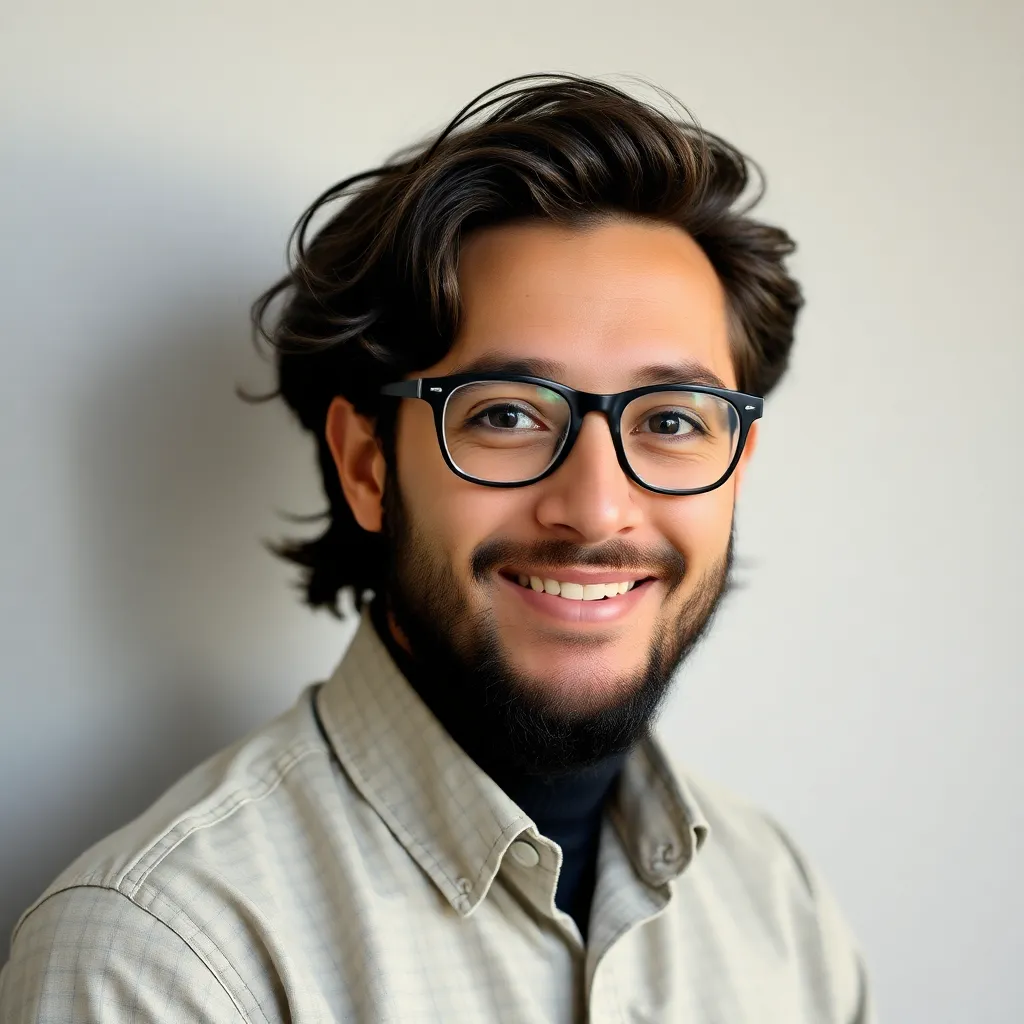
Breaking News Today
Apr 12, 2025 · 6 min read

Table of Contents
The Rotating Windings of a DC Motor: A Deep Dive into Construction, Operation, and Significance
The humble DC motor, a workhorse of countless applications, relies on a sophisticated interplay of magnetic fields and electrical currents to achieve its rotary motion. Central to this process are the rotating windings, also known as the armature windings. Understanding their construction, operation, and significance is crucial to grasping the intricacies of DC motor functionality and its various types. This comprehensive guide delves deep into the world of DC motor rotating windings, covering everything from their basic structure to advanced design considerations.
Understanding the Basics: Armature and its Windings
The rotating part of a DC motor is called the armature. Embedded within the armature are the rotating windings, coils of insulated copper wire carefully arranged to interact with the magnetic field produced by the stator (the stationary part). These windings are the heart of the motor, responsible for converting electrical energy into mechanical energy. The specific configuration of these windings profoundly impacts the motor's performance characteristics, including torque, speed, and efficiency.
Types of Armature Windings: Lap and Wave Windings
Two primary types of armature windings dominate DC motor design: lap windings and wave windings. The choice between them depends on factors like the desired voltage, current, and overall motor characteristics.
Lap Windings:
- Characteristics: In lap windings, the start and finish of each coil are connected to adjacent commutator segments. This arrangement leads to a relatively low voltage but high current output. The number of parallel paths is equal to the number of poles in the motor.
- Advantages: High starting torque, robust construction, better suited for high-current applications.
- Disadvantages: Lower voltage output compared to wave windings.
Wave Windings:
- Characteristics: Wave windings feature a series connection of coils, resulting in a higher voltage and lower current output. The number of parallel paths is usually two, regardless of the number of poles.
- Advantages: Higher voltage output, more efficient for high-speed applications.
- Disadvantages: Lower starting torque compared to lap windings, more complex construction.
The Role of the Commutator: Rectifying the Current
The commutator, a crucial component integral to the armature, is a cylindrical assembly composed of copper segments insulated from each other. It plays a pivotal role in rectifying the alternating current (AC) induced in the rotating windings into a unidirectional current, ensuring continuous rotation.
Commutation Process Explained:
As the armature rotates within the magnetic field, the current flowing through the windings changes direction due to Faraday's law of electromagnetic induction. The commutator, in conjunction with the brushes (stationary carbon contacts), ensures that the current always flows in the same direction through the external circuit, preventing the motor from reversing direction with each half-cycle. This process of changing the direction of current in the coils is known as commutation. Proper commutation is essential for smooth and efficient motor operation; poor commutation can lead to sparking, overheating, and reduced motor lifespan.
Construction of Rotating Windings: A Detailed Look
The construction of rotating windings involves meticulous precision and careful consideration of several factors:
-
Coil Design: Individual coils are formed by winding insulated copper wire around formers. The number of turns per coil affects the motor's voltage and torque characteristics. Precise winding techniques are crucial to maintain consistent coil geometry and minimize inductance.
-
Coil Placement: The coils are strategically placed within the armature slots, ensuring proper distribution of magnetic flux and minimizing cogging (irregular torque fluctuations). Careful placement is vital for efficient operation and reduced vibrations.
-
Insulation: High-quality insulation is paramount to prevent short circuits and ensure the safety of the motor. Various insulation materials, such as enamel coatings, mica, and fiberglass, are used depending on the operating voltage and temperature requirements.
-
Slot Design: Armature slots are carefully designed to optimize the placement and cooling of the windings. Slot shape and size influence factors like the magnetic field distribution, efficiency, and heat dissipation.
Advanced Design Considerations: Improving Performance
Modern DC motor designs incorporate advanced techniques to enhance performance and efficiency:
-
Concentrated Windings: This technique involves placing coils directly in the armature slots, resulting in a more concentrated magnetic field and improved torque production.
-
Distributed Windings: In contrast, distributed windings spread the coils over multiple slots, resulting in a smoother torque and reduced cogging.
-
Skewed Windings: To further mitigate cogging and reduce noise, the armature slots are sometimes skewed. This arrangement reduces the abrupt changes in magnetic flux, leading to a quieter and smoother operation.
-
Fractional-Slot Concentrated Windings (FSCW): This advanced technique combines the advantages of both concentrated and distributed windings, optimizing both torque production and cogging reduction.
Impact of Winding Design on Motor Characteristics
The design of the rotating windings directly impacts several key motor characteristics:
-
Torque: The number of turns in the windings, the current flowing through them, and the magnetic field strength all directly influence the motor's torque output.
-
Speed: The motor's speed is determined by the voltage applied, the magnetic field strength, and the back EMF (electromotive force) generated by the rotating windings.
-
Efficiency: The efficiency of the motor is affected by factors such as copper losses in the windings, iron losses in the armature core, and mechanical losses in the bearings. Efficient winding design minimizes these losses.
-
Heat Dissipation: Proper winding design and insulation are crucial for efficient heat dissipation to prevent overheating and extend the motor's lifespan. Effective cooling mechanisms are usually incorporated into the armature design.
Troubleshooting Common Issues with Rotating Windings
Several issues can arise with DC motor rotating windings, some of which are:
-
Open Circuits: A break in the winding insulation can lead to an open circuit, preventing current flow and causing motor failure.
-
Short Circuits: A short circuit between windings or between a winding and the armature core can result in overheating and damage to the motor.
-
Ground Faults: A fault to ground can cause current leakage, leading to reduced efficiency and potential safety hazards.
-
Winding Deformations: Mechanical stress or vibrations can cause deformation in the windings, affecting the magnetic field and motor performance. This could be due to improper installation, overloading, or mechanical wear.
Regular inspection, proper maintenance, and adherence to operational limits can help prevent many of these issues.
Conclusion: The Unsung Hero of DC Motor Operation
The rotating windings of a DC motor, often overlooked, are the pivotal components responsible for converting electrical energy into mechanical work. Their intricate design and operation are essential for the smooth and efficient functioning of the motor. Understanding the nuances of winding types, construction techniques, and their impact on motor characteristics is crucial for engineers, technicians, and anyone seeking a deeper understanding of DC motor technology. From the fundamental lap and wave windings to the advanced designs employed in modern motors, the continuous improvement and optimization of armature windings are driving the development of ever more efficient and robust DC motor technologies. The continued refinement of these components will undoubtedly play a significant role in the future of electric power applications.
Latest Posts
Latest Posts
-
Examples Of Programmed And Nonprogrammed Decision Making
Apr 18, 2025
-
Whose Responsibility Is It To Report A Privacy Violation
Apr 18, 2025
-
Exercise 12 Review Sheet Art Labeling Activity 1
Apr 18, 2025
-
Which Statement Is True About Genetics And Environment
Apr 18, 2025
-
Classical And Operant Conditioning Are Forms Of Blank Learning
Apr 18, 2025
Related Post
Thank you for visiting our website which covers about The Rotating Windings Of A Dc Motor. . We hope the information provided has been useful to you. Feel free to contact us if you have any questions or need further assistance. See you next time and don't miss to bookmark.