The Standard For Machine Room Safety Is
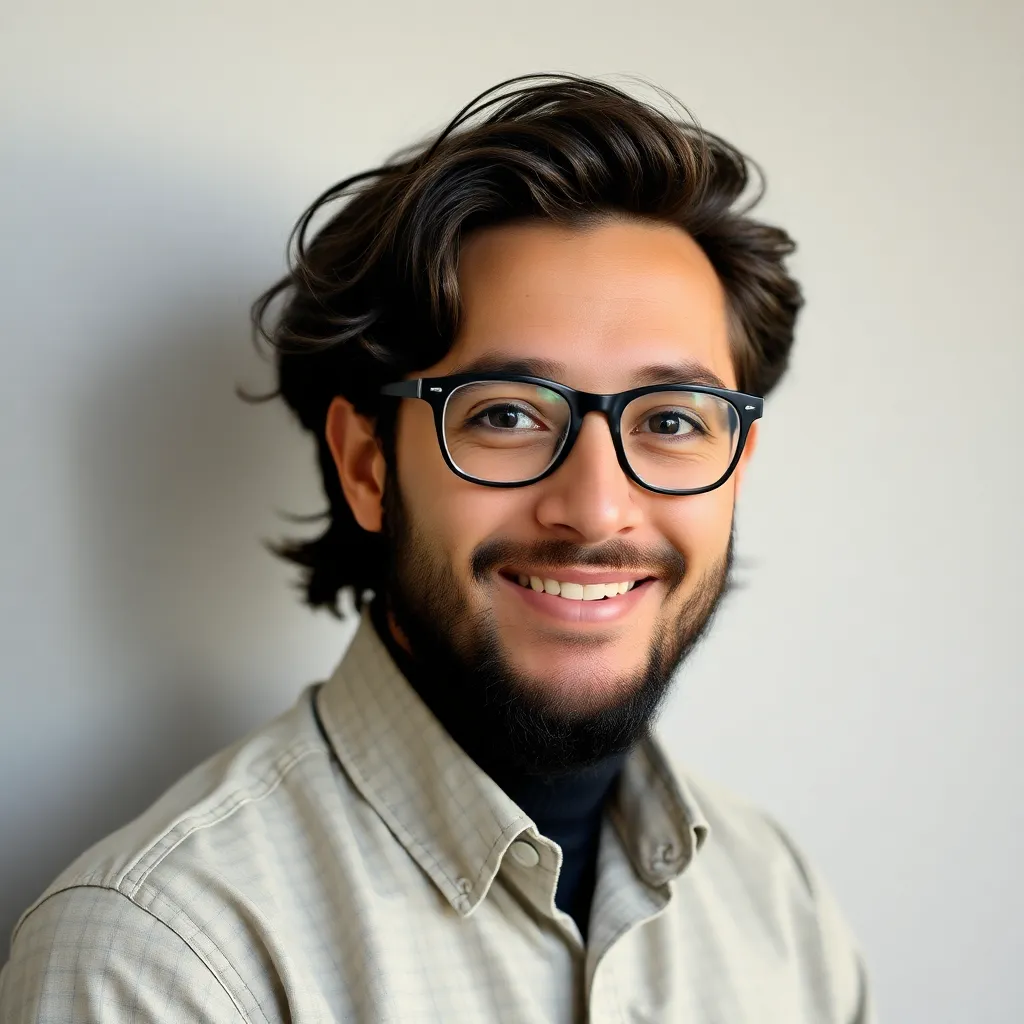
Breaking News Today
Apr 09, 2025 · 7 min read

Table of Contents
The Standard for Machine Room Safety Is… A Multifaceted Approach
Machine rooms, the beating hearts of many critical systems, house complex and potentially dangerous equipment. From servers humming with data to powerful generators ensuring uninterrupted power, these spaces demand stringent safety measures. The "standard" for machine room safety isn't a single document but rather a comprehensive approach built upon various regulations, best practices, and common sense. This article delves into the multifaceted aspects of ensuring a safe machine room environment, exploring key considerations for design, operation, and maintenance.
I. Understanding the Risks: Identifying Potential Hazards
Before diving into safety standards, understanding the potential hazards within a machine room is paramount. These hazards vary depending on the specific equipment housed, but common threats include:
1. Electrical Hazards:
- High Voltage: Machine rooms often contain high-voltage equipment, posing a risk of electric shock, burns, and even fatalities. Improper grounding, damaged insulation, and accidental contact are major concerns.
- Arcing and Flash Fires: Faulty wiring or equipment can lead to arcing, producing intense heat and potentially igniting nearby combustible materials.
- Electromagnetic Interference (EMI): The operation of certain equipment can generate EMI, potentially interfering with other systems or creating health risks.
2. Mechanical Hazards:
- Moving Parts: Fans, pumps, and generators possess moving parts capable of causing serious injuries if contacted. Guards and safety interlocks are critical.
- Rotating Equipment: Centrifugal force from rotating components can create dangerous projectiles if a malfunction occurs.
- Pinch Points: Areas where moving parts come close together can pinch fingers or limbs, leading to crushing injuries.
3. Environmental Hazards:
- Heat: Concentrated heat generated by equipment can create an uncomfortable and even dangerous work environment. Proper ventilation is essential.
- Noise: The operation of many machines generates significant noise, potentially causing hearing loss if not mitigated.
- Fire: Combustible materials, faulty wiring, and overheating equipment present a significant fire risk.
- Chemical Hazards: Some machine rooms may contain chemicals used for cooling or cleaning, requiring appropriate handling and storage procedures.
II. Regulatory Compliance: The Foundation of Machine Room Safety
Numerous regulations and standards guide machine room safety practices. Compliance is crucial to minimizing risks and avoiding legal penalties. Key regulations often include (note: specific regulations vary by location and should be researched for your area):
- National Electrical Code (NEC): This code dictates safe practices for electrical installations and wiring, crucial for preventing electrical hazards in machine rooms.
- Occupational Safety and Health Administration (OSHA): OSHA guidelines cover various aspects of workplace safety, including machine guarding, lockout/tagout procedures, and personal protective equipment (PPE) requirements for machine room personnel.
- Local Fire Codes: These codes specify fire prevention and suppression measures, including the type and placement of fire extinguishers, fire suppression systems, and emergency exits.
- International Standards (IEC): International standards, like those from the International Electrotechnical Commission (IEC), provide globally recognized safety guidelines for electrical equipment and systems.
- Manufacturer's Instructions: Adhering to manufacturer's guidelines for specific equipment is crucial, as they often contain specific safety recommendations and maintenance procedures.
III. Design Considerations: Building a Safe Machine Room Environment
Safe machine room design begins at the planning stage. Key considerations include:
1. Layout and Access:
- Clear Aisles and Pathways: Adequate space must be provided for movement and access to equipment for maintenance and repairs.
- Emergency Exits: Clearly marked and easily accessible emergency exits are essential for swift evacuation in case of an emergency.
- Proper Lighting: Sufficient lighting prevents accidents caused by poor visibility. Emergency lighting is also needed for power outages.
- Signage: Clear signage indicating hazards, emergency procedures, and safety instructions is critical.
2. Environmental Controls:
- Ventilation: Effective ventilation removes heat, fumes, and moisture, preventing overheating and potential health hazards. This often involves HVAC systems designed for the specific heat load of the equipment.
- Temperature Control: Maintaining optimal temperature prevents equipment malfunction and ensures a comfortable work environment.
- Fire Suppression: Appropriate fire suppression systems, such as sprinklers or fire suppression agents, should be installed based on the type of equipment and potential fire hazards.
- Noise Reduction: Implementing noise-reducing measures such as sound-dampening materials or enclosures can minimize noise pollution.
3. Electrical Safety:
- Grounding and Bonding: Proper grounding and bonding of all electrical equipment is essential to prevent electrical shocks and arcing.
- Overcurrent Protection: Circuit breakers and fuses must be appropriately sized and installed to protect against overloads and short circuits.
- Isolation and Lockout/Tagout (LOTO): Procedures for isolating equipment from power sources before maintenance or repair are crucial to prevent accidental energization and electrical shocks. LOTO is a fundamental safety procedure.
- Cable Management: Organized and properly secured cabling prevents tripping hazards and minimizes the risk of damage to wires.
4. Mechanical Safety:
- Guarding: Moving parts of machinery must be properly guarded to prevent accidental contact.
- Interlocks: Safety interlocks should prevent operation of machinery unless guards are in place.
- Emergency Stops: Easily accessible emergency stop buttons or switches should be provided for immediate shutdown of equipment.
- Regular Inspections: Regular inspections of mechanical components for wear and tear, damage, and loose parts are essential for preventing accidents.
IV. Operational Procedures: Maintaining a Safe Working Environment
Safe operational procedures are as crucial as safe design. These procedures should cover:
1. Access Control:
- Restricted Access: Only authorized personnel should have access to the machine room.
- Identification and Training: All personnel entering the machine room should have proper identification and undergo appropriate safety training.
- Sign-in/Sign-out Log: Maintaining a log of individuals entering and exiting the machine room helps track who is inside at any given time.
2. Lockout/Tagout (LOTO) Procedures:
- Strict Adherence: LOTO procedures should be strictly followed before any maintenance or repair work is performed.
- Training and Competency: Personnel performing LOTO procedures should be properly trained and competent.
- Clear Procedures: Clear, concise, and well-understood LOTO procedures should be readily available.
3. Personal Protective Equipment (PPE):
- Appropriate PPE: Appropriate PPE, such as safety glasses, gloves, hearing protection, and safety shoes, should be used when necessary.
- PPE Availability: PPE should be readily available and in good condition.
- Training on PPE Use: Personnel should be trained on the proper use and care of PPE.
4. Emergency Procedures:
- Clear Procedures: Clearly defined emergency procedures for fire, electrical shock, or other emergencies should be in place.
- Emergency Contacts: Emergency contact information should be readily available.
- Regular Drills: Regular emergency drills should be conducted to ensure personnel are familiar with emergency procedures.
5. Regular Inspections and Maintenance:
- Preventative Maintenance: Regular preventative maintenance helps identify and address potential hazards before they cause incidents.
- Scheduled Inspections: Scheduled inspections should be conducted to identify and address any safety concerns.
- Documentation: Maintain detailed records of inspections and maintenance activities.
V. Ongoing Monitoring and Improvement: A Continuous Safety Journey
Machine room safety isn't a one-time event; it's an ongoing process that demands constant vigilance and improvement. Key elements of continuous improvement include:
1. Safety Audits and Inspections:
- Regular Audits: Regular safety audits conducted by qualified professionals can identify potential hazards and areas for improvement.
- Corrective Actions: Corrective actions should be implemented promptly to address identified hazards.
- Documentation: Maintain detailed records of audits, inspections, and corrective actions.
2. Employee Training and Education:
- Ongoing Training: Regular safety training and education should be provided to all machine room personnel.
- Hazard Awareness: Training should focus on hazard awareness, safe work practices, and emergency procedures.
- Feedback Mechanisms: Establish mechanisms for employees to report safety concerns without fear of reprisal.
3. Data Analysis and Reporting:
- Incident Reporting: Establish a system for promptly reporting and investigating safety incidents.
- Data Analysis: Analyze safety data to identify trends and areas for improvement.
- Performance Indicators: Track key performance indicators (KPIs) related to safety to monitor progress and effectiveness of safety initiatives.
4. Continuous Improvement Methodology:
- Plan-Do-Check-Act (PDCA): Utilize a continuous improvement methodology, such as PDCA, to systematically identify, address, and prevent safety incidents.
- Proactive Measures: Implement proactive measures to prevent future incidents.
- Adaptive Approach: Maintain a flexible and adaptive approach to safety management to address changing conditions and evolving technology.
In conclusion, the standard for machine room safety is not a singular metric but rather a commitment to a multifaceted approach. By combining regulatory compliance, careful design considerations, robust operational procedures, and continuous monitoring and improvement, organizations can create a safe and productive environment for their personnel and protect their valuable equipment. Remember that safety is not an expense but a crucial investment in the long-term success and sustainability of any operation.
Latest Posts
Latest Posts
-
In A Marketing Context A Market Refers To
Apr 17, 2025
-
Antidiuretic Hormone Provides A Means Of Controlling Water
Apr 17, 2025
-
Maxs Behavior And Self Presentation Is Relaxed And Informal
Apr 17, 2025
-
Why Did The Serfs Accepted Their Economic Hardships
Apr 17, 2025
-
When Should Rescuers Switch Positions During Cpr
Apr 17, 2025
Related Post
Thank you for visiting our website which covers about The Standard For Machine Room Safety Is . We hope the information provided has been useful to you. Feel free to contact us if you have any questions or need further assistance. See you next time and don't miss to bookmark.