Three Issues Are At The Core Of Operations Management
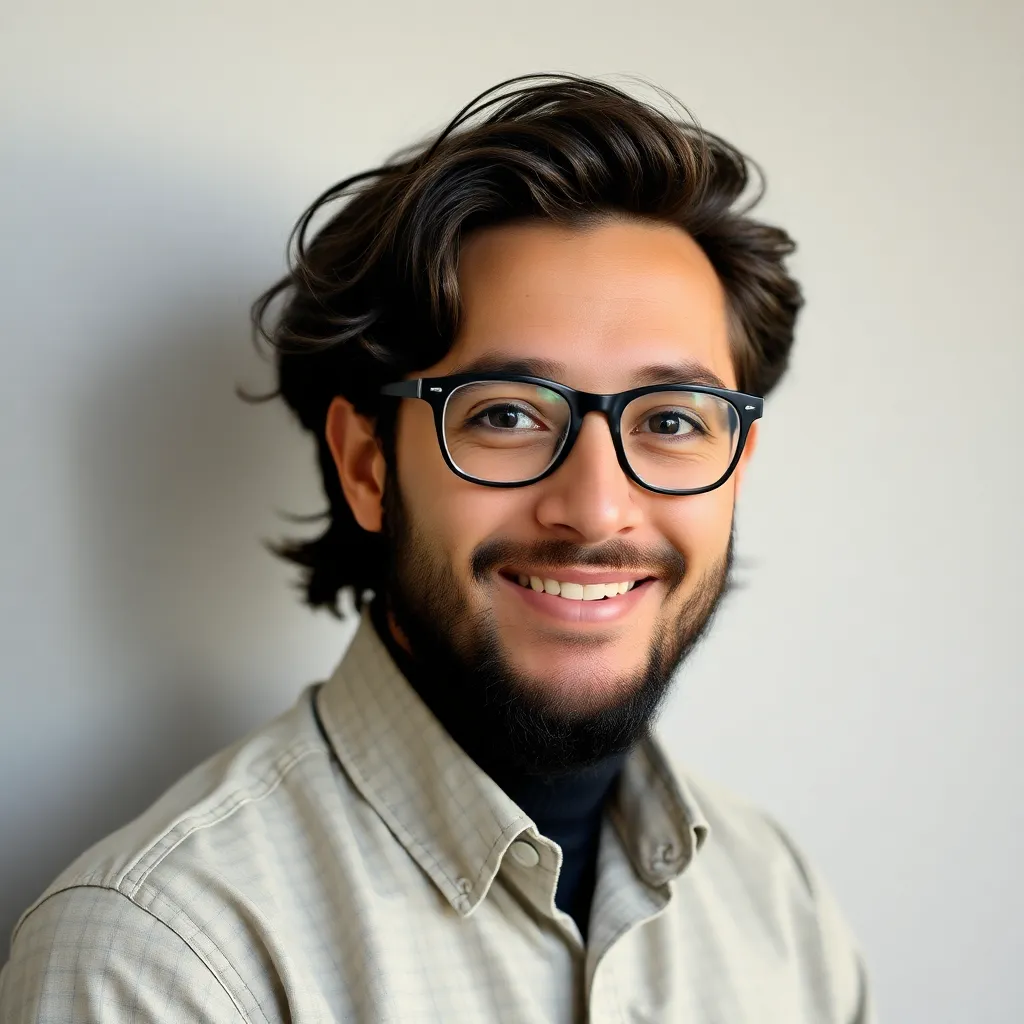
Breaking News Today
Apr 17, 2025 · 7 min read

Table of Contents
Three Core Issues in Operations Management: Efficiency, Effectiveness, and Agility
Operations management is the backbone of any successful organization, encompassing the planning, organizing, and controlling of resources to produce goods or services efficiently and effectively. While the specifics of operations management vary across industries, three core issues consistently challenge organizations: efficiency, effectiveness, and agility. Mastering these three elements is crucial for achieving sustainable competitive advantage and long-term success. This article delves deep into each of these core issues, exploring their interrelationships and providing strategies for improvement.
1. Efficiency: Maximizing Output with Minimal Input
Efficiency in operations management centers on optimizing resource utilization to maximize output while minimizing input. This involves meticulously examining every stage of the production process to identify and eliminate waste. The goal is to produce more with less – less time, less material, less energy, and less cost. A highly efficient operation translates directly into increased profitability and competitive pricing.
Key Aspects of Operational Efficiency:
-
Lean Manufacturing Principles: Lean manufacturing, pioneered by Toyota, focuses on eliminating waste in all forms – from excess inventory (muda) to unnecessary movements (muri) and overburdening employees (mura). Implementing techniques like Just-in-Time (JIT) inventory management, Kaizen (continuous improvement), and 5S (sort, set in order, shine, standardize, sustain) are crucial for enhancing efficiency. Lean is not merely about cost cutting; it's about optimizing the entire value stream.
-
Process Optimization: Analyzing and streamlining workflows is critical. This involves identifying bottlenecks, redundancies, and inefficiencies in the production process. Techniques like process mapping, value stream mapping, and Six Sigma help pinpoint areas for improvement. Automation and technology play a vital role in process optimization, allowing for faster processing times, reduced errors, and improved consistency.
-
Supply Chain Management: Efficient operations depend heavily on a well-managed supply chain. This includes optimizing supplier relationships, managing inventory levels, and ensuring timely delivery of materials. Effective supply chain management minimizes disruptions, reduces lead times, and ensures the smooth flow of materials throughout the production process. Strong supplier relationships are paramount for efficiency.
-
Resource Allocation: Efficiently allocating resources – labor, capital, materials, and technology – is crucial. This requires accurate forecasting, demand planning, and capacity planning to ensure that the right resources are available at the right time and in the right quantities. Under-allocation leads to bottlenecks, while over-allocation leads to wasted resources.
-
Technology Integration: Implementing appropriate technologies, such as Enterprise Resource Planning (ERP) systems, can significantly enhance efficiency by integrating various aspects of the business, improving communication, and providing real-time data for informed decision-making. Data analytics also plays a critical role in identifying areas for improvement and optimizing resource allocation.
2. Effectiveness: Meeting Customer Needs and Achieving Organizational Goals
While efficiency focuses on how things are done, effectiveness focuses on what is done. An effective operation consistently delivers products or services that meet or exceed customer expectations and contribute to the overall goals of the organization. Effectiveness is about doing the right things, while efficiency is about doing things right. A highly effective operation leads to increased customer satisfaction, brand loyalty, and market share.
Key Aspects of Operational Effectiveness:
-
Customer Focus: Understanding customer needs and preferences is paramount. Market research, customer feedback, and data analytics help organizations tailor their products and services to meet specific customer demands. A customer-centric approach drives operational effectiveness.
-
Quality Management: Delivering high-quality products or services is essential for effectiveness. Implementing quality management systems, such as ISO 9001, helps organizations establish standards, monitor performance, and continuously improve quality. Quality is not just a goal; it's a competitive advantage.
-
Product and Service Design: Effective operations begin with designing products and services that meet customer needs and are feasible to produce. This involves considering factors such as functionality, usability, cost, and manufacturability. Careful design significantly impacts downstream operations.
-
Strategic Alignment: Operational effectiveness is intimately tied to the organization's overall strategy. Operations must be aligned with the company's mission, vision, and goals. Misalignment leads to wasted resources and missed opportunities.
-
Innovation and Continuous Improvement: Continuously innovating and improving products, services, and processes is crucial for maintaining effectiveness. This requires a culture of learning, experimentation, and adaptation to changing market demands. Embracing change is a key driver of effectiveness.
-
Performance Measurement: Regularly monitoring and measuring operational performance against key metrics is crucial for identifying areas for improvement and ensuring effectiveness. This requires establishing clear Key Performance Indicators (KPIs) and using data-driven insights to make informed decisions. Metrics should be relevant, measurable, achievable, relevant, and time-bound (SMART).
3. Agility: Responding Quickly to Change and Uncertainty
In today's dynamic business environment, agility is no longer a desirable trait; it's a necessity. Agility in operations management refers to the ability to quickly adapt to changing market conditions, customer demands, and unexpected disruptions. This involves flexibility, responsiveness, and the ability to quickly adjust operations to meet new challenges. Agile operations are resilient and capable of thriving in uncertainty.
Key Aspects of Operational Agility:
-
Flexible Manufacturing Systems: Implementing flexible manufacturing systems allows organizations to quickly adapt to changes in product demand and design. This involves using modular production lines, adaptable equipment, and skilled workers capable of performing multiple tasks. Flexibility is key to handling fluctuating demand.
-
Supply Chain Resilience: Building a resilient supply chain is crucial for agility. This involves diversifying suppliers, establishing robust inventory management systems, and developing contingency plans to mitigate disruptions. A resilient supply chain can withstand shocks and maintain operations during crises.
-
Information Technology Infrastructure: A robust IT infrastructure is essential for agility. This involves implementing real-time data analytics, cloud-based systems, and advanced communication technologies to facilitate quick decision-making and coordination. Data-driven insights are crucial for rapid response.
-
Collaborative Partnerships: Building strong relationships with suppliers, customers, and other stakeholders enhances agility. Collaboration enables faster information sharing, quicker problem-solving, and greater responsiveness to market changes. Collaboration fosters agility and innovation.
-
Decentralized Decision-Making: Empowering employees to make decisions at lower levels of the organization speeds up response times and enhances agility. This requires clear communication channels, delegated authority, and a culture of empowerment. Decentralization fosters faster responses to unexpected events.
-
Continuous Learning and Adaptation: Cultivating a culture of continuous learning and adaptation is paramount for agility. This involves investing in employee training, monitoring industry trends, and embracing new technologies to maintain a competitive edge. Continuous improvement is crucial for agility in a changing environment.
The Interplay of Efficiency, Effectiveness, and Agility
These three core issues are not mutually exclusive; they are interdependent and mutually reinforcing. For example, improving efficiency can free up resources that can be invested in improving effectiveness, such as enhancing product quality or expanding customer service. Similarly, achieving effectiveness can generate the financial resources necessary to invest in technology and infrastructure that improve agility. An agile operation can adapt quickly to market changes, optimizing efficiency and effectiveness along the way.
The challenge for operations managers lies in balancing these three core issues. Striving for maximum efficiency without considering effectiveness can lead to the production of low-quality products that don't meet customer needs. Focusing solely on effectiveness without considering efficiency can lead to high costs and reduced profitability. Prioritizing agility without considering efficiency and effectiveness can lead to chaotic and unsustainable operations. The optimal approach involves a holistic strategy that integrates all three core issues.
Conclusion: A Holistic Approach to Operations Management
Mastering efficiency, effectiveness, and agility is crucial for achieving sustainable competitive advantage in today's dynamic business environment. Operations managers need to develop a holistic approach that integrates these three core issues, creating a synergistic relationship that drives overall organizational success. By implementing the strategies discussed in this article, organizations can build robust, efficient, effective, and agile operations capable of thriving in the face of challenges and opportunities. Continuous monitoring, evaluation, and adaptation are key to maintaining operational excellence and securing a strong competitive position in the market.
Latest Posts
Latest Posts
-
According To Prohibited Personnel Practices Employees Who Are Subjected
Apr 19, 2025
-
What Is The Final Electron Acceptor In The Etc
Apr 19, 2025
-
Luisa 1 Of 1 Muchas Presiones Este Ano
Apr 19, 2025
-
Calibration Of Dental X Ray Equipment Should Be Performed By A
Apr 19, 2025
-
What Is Not True About Booking Official Flights
Apr 19, 2025
Related Post
Thank you for visiting our website which covers about Three Issues Are At The Core Of Operations Management . We hope the information provided has been useful to you. Feel free to contact us if you have any questions or need further assistance. See you next time and don't miss to bookmark.