To Reduce The Risk Of Lead Exposure Employers Should
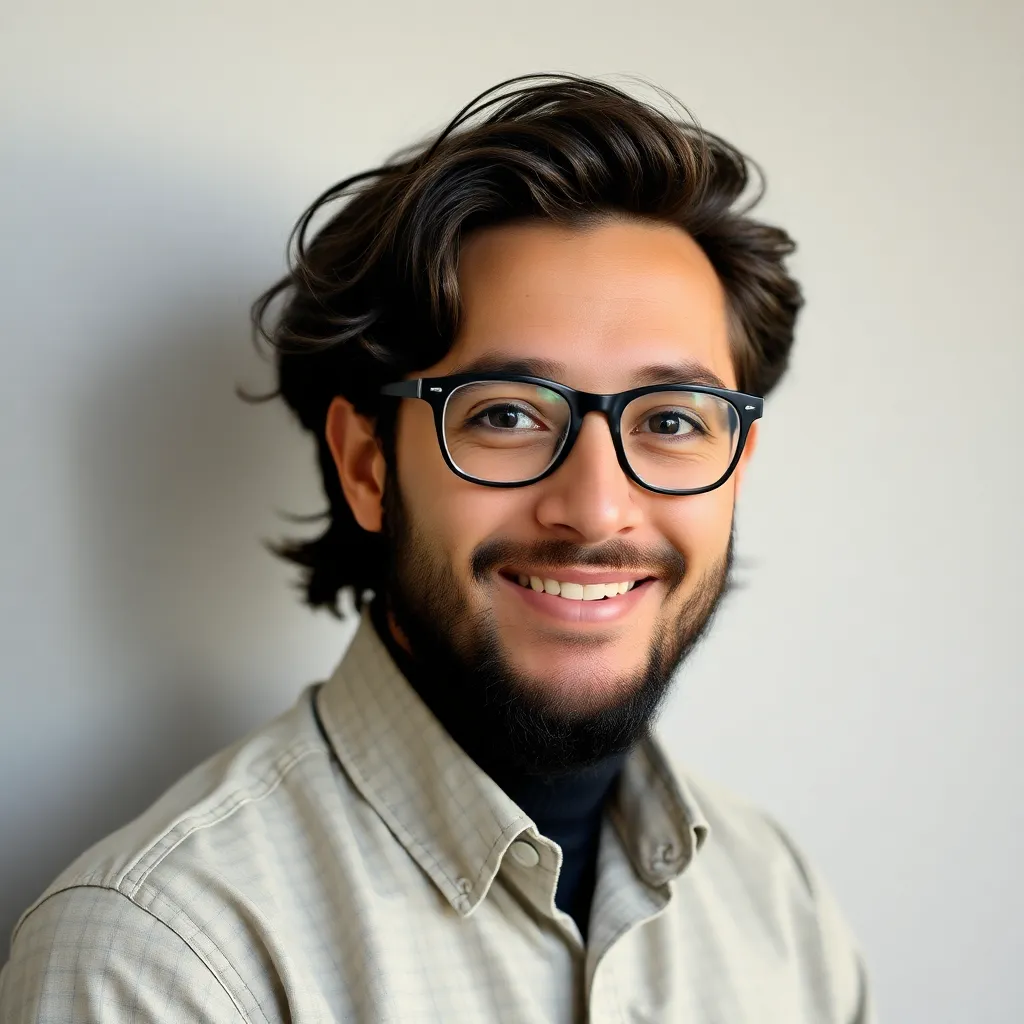
Breaking News Today
May 09, 2025 · 6 min read
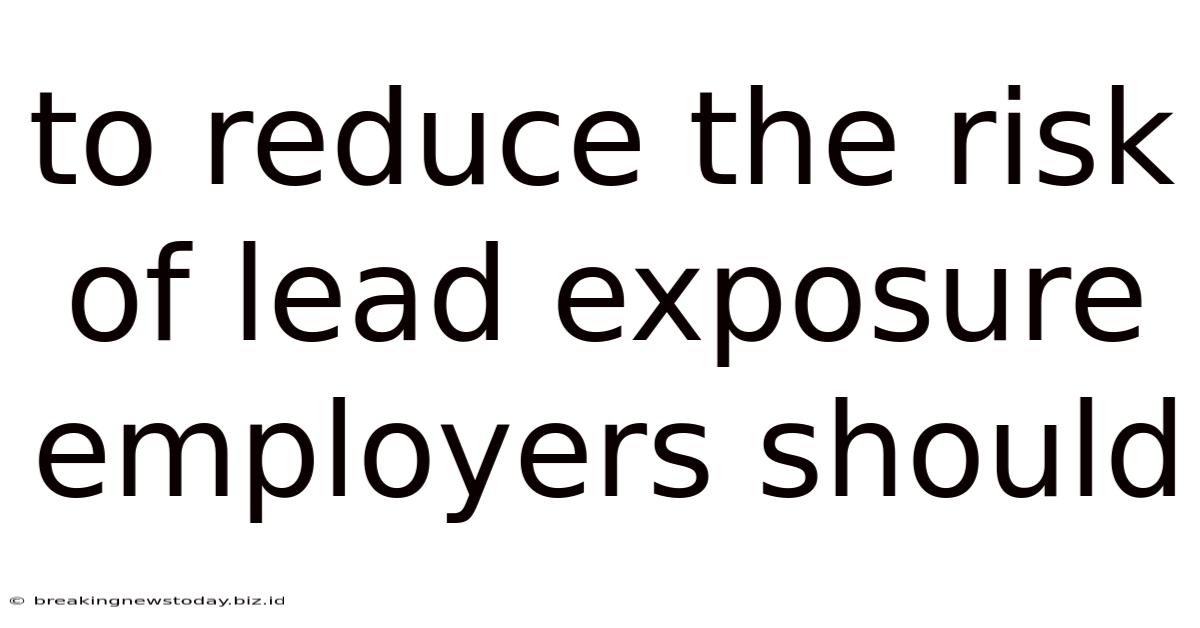
Table of Contents
To Reduce the Risk of Lead Exposure, Employers Should…
Lead poisoning is a serious health concern, and its impact extends far beyond the individual worker. Exposure to lead can result in significant health problems, decreased productivity, and increased healthcare costs for both employees and employers. Therefore, proactively mitigating lead exposure in the workplace is not just a moral obligation but also a sound business strategy. This comprehensive guide will outline crucial steps employers should take to reduce the risk of lead exposure and create a safer, healthier work environment.
Understanding Lead Exposure Risks
Before diving into preventative measures, understanding the sources and risks of lead exposure is paramount. Lead is a naturally occurring heavy metal that's been used in various industries for centuries. However, its toxicity is well-documented, making workplace safety a critical concern.
Common Sources of Lead Exposure in the Workplace:
- Construction and Demolition: Lead-based paint is a significant source in older buildings. Demolition and renovation projects release lead dust and particles into the air.
- Manufacturing: Certain manufacturing processes, such as battery manufacturing, smelting, and metalworking, use lead and generate lead dust or fumes.
- Automotive Repair: Working on older vehicles can expose mechanics to lead from batteries, paint, and other components.
- Recycling: Processing scrap metal and other materials can expose workers to lead contamination.
- Printing: Some printing processes used to involve lead-based inks and type. While less common now, some older facilities may still use them.
- Mining: Lead mining and processing are inherently hazardous, exposing workers to high levels of lead dust and fumes.
Health Effects of Lead Exposure:
Lead exposure can negatively impact various bodily systems. The severity of effects depends on the level and duration of exposure. Some common health consequences include:
- Neurological effects: Lead can damage the nervous system, leading to cognitive impairment, reduced concentration, memory loss, and even seizures. These effects are particularly severe in children and developing fetuses.
- Reproductive effects: Lead exposure can impact fertility in both men and women, and can cause birth defects.
- Cardiovascular effects: Lead can increase blood pressure and the risk of heart disease.
- Renal effects: Lead can damage the kidneys, leading to kidney failure in severe cases.
- Gastrointestinal effects: Lead exposure can cause abdominal pain, nausea, and vomiting.
- Hematological effects: Lead can interfere with the production of red blood cells, leading to anemia.
Implementing a Comprehensive Lead Exposure Prevention Program
A robust lead exposure prevention program is crucial for protecting workers and avoiding legal liabilities. This program must be multifaceted and include:
1. Engineering Controls: The First Line of Defense
Engineering controls are the most effective way to reduce lead exposure. These involve modifying the work environment to minimize lead presence or worker exposure:
- Substitution: Replace lead-containing materials with safer alternatives whenever possible. This is the most effective method of reducing risk.
- Enclosure: Enclose processes that generate lead dust or fumes, using local exhaust ventilation (LEV) systems to capture and remove contaminants.
- Isolation: Isolate lead-containing materials or processes from workers using barriers or physical separation.
- Wet methods: Using water to suppress dust generation during processes like grinding or cutting.
- Improved ventilation: Ensure adequate ventilation in work areas to dilute and remove airborne lead particles. This may involve increasing airflow or installing ventilation systems.
2. Administrative Controls: Managing Work Practices
Administrative controls focus on changing how work is performed to reduce exposure:
- Work Rotation: Rotating workers through different tasks to minimize exposure duration.
- Limited exposure time: Restricting the amount of time workers spend in areas with high lead concentrations.
- Scheduled breaks: Providing frequent breaks to allow workers to rest and reduce fatigue, which can increase vulnerability to lead exposure.
- Training and education: Providing comprehensive training to workers about the hazards of lead exposure, safe work practices, and emergency procedures. Training should be regularly updated.
- Medical surveillance: Implementing a program of regular medical monitoring for workers exposed to lead, including blood lead level testing. This allows for early detection of problems and appropriate intervention.
- Personal Protective Equipment (PPE): While PPE is not a substitute for engineering and administrative controls, it's a critical supplement.
3. Personal Protective Equipment (PPE): A Necessary Supplement
While engineering and administrative controls are the primary methods of preventing lead exposure, PPE provides an additional layer of protection:
- Respirators: Appropriate respirators, such as half-mask or full-face respirators with HEPA filters, should be provided and used when necessary to prevent inhalation of lead dust or fumes. Proper fit testing is crucial.
- Protective clothing: Providing workers with coveralls, gloves, and boots that can prevent skin contact with lead. Clothing should be laundered regularly and not worn outside of the work environment.
- Eye protection: Safety glasses or goggles should be worn to protect eyes from lead dust or splashes.
- Proper handwashing facilities: Provide readily accessible handwashing stations with soap and water, along with appropriate hand sanitizers, and enforce strict handwashing protocols before breaks, after work, and whenever contamination is suspected.
4. Environmental Monitoring and Clean-up
Regular monitoring of the work environment is essential to ensure the effectiveness of control measures:
- Air monitoring: Regularly monitor the air for lead levels using appropriate sampling and analytical methods. This helps identify areas with high concentrations of lead and inform preventative actions.
- Surface wipe sampling: Periodically test surfaces for lead contamination to identify areas needing cleaning or remediation.
- Soil testing: If lead is used outdoors, testing the soil for contamination is important, especially around work areas.
- Decontamination procedures: Establish clear procedures for cleaning up spills and removing lead-contaminated materials. This often involves specialized cleaning techniques and equipment.
5. Record Keeping and Documentation
Meticulous record-keeping is vital for demonstrating compliance with regulations and tracking the effectiveness of the lead exposure prevention program:
- Training records: Maintain records of all worker training on lead safety.
- Medical surveillance records: Keep records of all medical monitoring results for exposed workers.
- Environmental monitoring data: Document all air and surface sampling results.
- Incident reports: Keep detailed records of any incidents involving lead exposure.
- Emergency response plan: Develop and maintain a detailed emergency response plan for dealing with lead spills or exposures. Workers must be regularly trained on this plan.
6. Compliance with Regulations and Standards
Employers must adhere to all applicable occupational safety and health regulations related to lead exposure. These regulations vary by jurisdiction, but generally involve:
- OSHA (Occupational Safety and Health Administration) standards (USA): The OSHA standards outline specific requirements for lead exposure prevention in various industries.
- Equivalent regulations in other countries: Employers must be aware of and compliant with relevant regulations in their country or region.
Building a Culture of Safety: The Key to Long-Term Success
A successful lead exposure prevention program requires more than just implementing policies and procedures. It requires building a culture of safety where workers feel empowered to report hazards and participate actively in their own safety:
- Open communication: Encourage workers to report any concerns about lead exposure without fear of retribution.
- Employee involvement: Involve workers in the development and implementation of the lead exposure prevention program.
- Regular safety meetings: Hold regular safety meetings to discuss safety concerns, review procedures, and provide updates.
- Recognition and rewards: Recognize and reward workers for their commitment to safety.
By adopting a multi-pronged approach that incorporates engineering controls, administrative controls, PPE, environmental monitoring, record-keeping, regulatory compliance, and a strong safety culture, employers can significantly reduce the risk of lead exposure and create a healthier, safer work environment for their employees. Remember, preventing lead exposure is an ongoing process, requiring constant vigilance, adaptation, and commitment to worker well-being. The investment in a comprehensive program will yield substantial returns in terms of improved worker health, increased productivity, and reduced legal liability.
Latest Posts
Latest Posts
-
The Ability To Respond To A Stimulus
May 09, 2025
-
Bow Saw To Cut Intricate External Sapes
May 09, 2025
-
Why Do We Use Coaching To Develop Marines
May 09, 2025
-
Why Was The Hijra A Turning Point For Islam
May 09, 2025
-
The Things They Carried Chapter One Summary
May 09, 2025
Related Post
Thank you for visiting our website which covers about To Reduce The Risk Of Lead Exposure Employers Should . We hope the information provided has been useful to you. Feel free to contact us if you have any questions or need further assistance. See you next time and don't miss to bookmark.