Total Productive Maintenance Is Best Described As
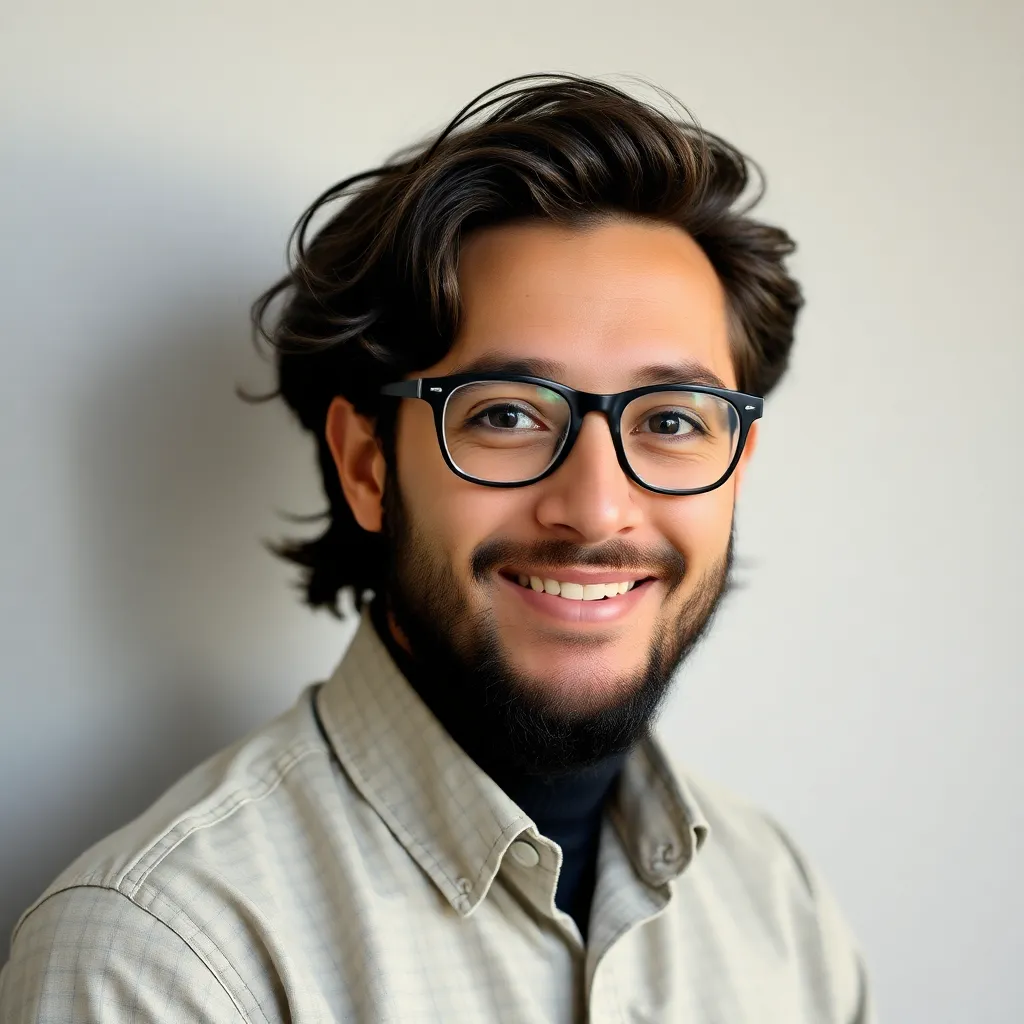
Breaking News Today
May 09, 2025 · 8 min read
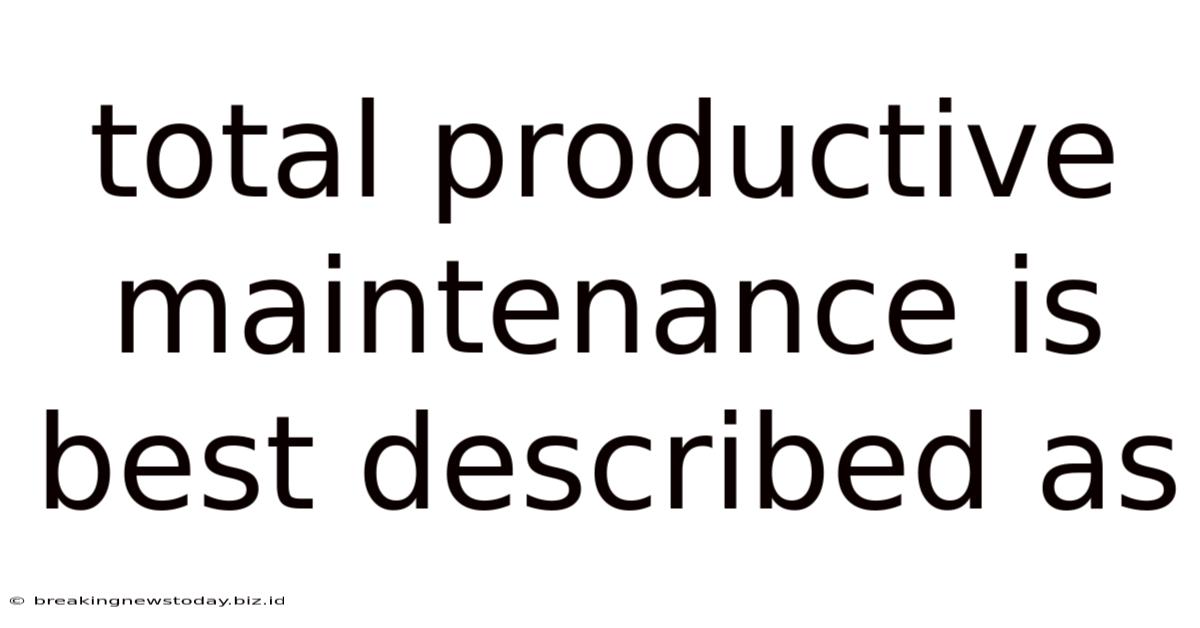
Table of Contents
Total Productive Maintenance (TPM): A Deep Dive into Maximizing Equipment Effectiveness
Total Productive Maintenance (TPM) is far more than just preventative maintenance; it's a philosophy, a holistic approach to maximizing the effectiveness of equipment and overall manufacturing processes. It’s about involving every employee in the continuous improvement of equipment reliability and performance, ultimately leading to increased productivity, reduced downtime, and significant cost savings. This in-depth article will explore TPM, its core principles, implementation strategies, and the substantial benefits it offers organizations.
Understanding the Core Principles of TPM
TPM's effectiveness hinges on its fundamental principles, which when implemented correctly, create a culture of proactive maintenance and continuous improvement within an organization. These core principles act as a framework, guiding the implementation and ensuring long-term success.
1. Autonomous Maintenance: Empowering the Workforce
Autonomous maintenance is a cornerstone of TPM. It empowers operators to perform basic maintenance tasks on their own equipment, fostering a sense of ownership and responsibility. This is not about replacing skilled technicians but equipping operators with the knowledge and tools to identify and address minor issues before they escalate into major problems. Training is crucial here, teaching operators how to perform routine inspections, lubricate equipment, and make minor repairs. This proactive approach significantly reduces downtime and frees up skilled technicians to focus on more complex tasks.
2. Planned Maintenance: Scheduled Preventative Measures
Planned maintenance, while a standard practice in many organizations, takes on a new significance within the TPM framework. It's not just about adhering to a schedule; it's about optimizing the maintenance schedule based on real-time data and predictive analytics. This involves meticulously tracking equipment performance, identifying potential failure points, and scheduling preventative maintenance before problems occur. This proactive approach minimizes unexpected downtime and maximizes equipment lifespan.
3. Focused Improvement: Continuous Optimization
Continuous improvement is the lifeblood of TPM. This principle emphasizes the importance of constantly striving to enhance equipment performance and processes. It involves using data-driven techniques like Kaizen (continuous improvement) events to identify areas for improvement, implement solutions, and monitor their effectiveness. This iterative process ensures that TPM is not a static program but a dynamic system constantly adapting to changing needs.
4. Early Equipment Management: Proactive Design and Procurement
Early equipment management involves incorporating maintenance considerations into the very design and procurement phases of equipment. This means selecting equipment that is inherently reliable, easy to maintain, and well-suited to the specific production needs. Careful consideration of factors like durability, accessibility, and modularity ensures that equipment is designed for optimal maintainability from the outset, minimizing future maintenance challenges.
5. Education and Training: Empowering the Team
TPM’s success hinges on the commitment and involvement of every employee. Comprehensive training programs are essential to equip operators and maintenance personnel with the necessary skills and knowledge to perform their roles effectively. This includes training on autonomous maintenance procedures, safety protocols, and the use of maintenance management systems. Continuous training and development help maintain high levels of competency and foster a culture of continuous improvement.
6. Preventive Maintenance: Reducing Downtime
Preventive maintenance under TPM is far more sophisticated than simply following a schedule. It involves sophisticated data analysis and predictive modeling to anticipate potential equipment failures before they occur. By implementing this proactive approach, companies minimize unexpected downtime and maximize equipment uptime. This goes beyond basic lubrication and inspection; it involves understanding the equipment's performance patterns and employing predictive maintenance techniques to preempt potential issues.
7. Quality Maintenance: Ensuring High Standards
Quality maintenance is a critical principle of TPM. It establishes stringent standards for all maintenance activities, ensuring that work is performed correctly and efficiently. This principle goes hand-in-hand with proper documentation and a focus on error prevention. This helps to build a strong foundation of reliable equipment and reduces the risk of costly mistakes during maintenance operations.
Implementing TPM: A Step-by-Step Guide
Implementing TPM is a journey, not a destination. It requires a structured approach, commitment from all levels of the organization, and a willingness to adapt and improve continuously.
1. Building a Strong Foundation: Defining Goals and Objectives
Begin by clearly defining the goals and objectives of your TPM implementation. What are you hoping to achieve? Reduced downtime? Increased productivity? Improved product quality? Setting clear goals provides direction and helps to measure the success of your program. This also includes identifying key performance indicators (KPIs) to track progress and ensure accountability.
2. Securing Executive Sponsorship: Gaining Leadership Support
TPM requires strong leadership support. Executive sponsorship is essential to ensure that resources are allocated, that the initiative has the necessary backing, and that it's integrated into the overall business strategy. This sponsorship helps to overcome resistance to change and ensures that the program receives the attention and support it requires.
3. Forming a TPM Team: Establishing Cross-Functional Collaboration
Assemble a cross-functional TPM team comprising representatives from different departments, including operations, maintenance, engineering, and quality control. This diverse team brings a range of perspectives and ensures that the program addresses the needs of all stakeholders. The team's role is to develop and implement the TPM strategy, and to monitor and evaluate its effectiveness.
4. Developing a Training Program: Empowering the Workforce
Invest in a comprehensive training program to equip your workforce with the necessary skills and knowledge to participate effectively in TPM. This includes training on autonomous maintenance, planned maintenance, and continuous improvement techniques. Training is not a one-time event but an ongoing process to ensure that employees are equipped with the latest knowledge and skills.
5. Selecting Pilot Equipment: Starting Small and Scaling Up
Start with a pilot project involving a few key pieces of equipment. This allows you to test and refine your approach before rolling it out across the entire organization. Choosing equipment that is critical to production or has a history of frequent downtime is a good starting point. This phased implementation helps minimize disruptions while gaining valuable experience.
6. Implementing Autonomous Maintenance: Empowering Operators
Begin empowering operators by providing them with the training and tools needed to perform basic maintenance tasks. This requires clear procedures, regular training sessions, and support from maintenance personnel. Gradually increase the level of responsibility assigned to operators as their proficiency improves.
7. Developing a Planned Maintenance System: Optimizing Maintenance Schedules
Implement a robust planned maintenance system that utilizes data analysis and predictive maintenance techniques. This involves tracking equipment performance, analyzing maintenance data, and scheduling preventative maintenance based on predicted failure rates. This proactive approach minimizes downtime and maximizes equipment uptime.
8. Focusing on Continuous Improvement: Driving Organizational Learning
TPM is a continuous improvement journey. Regularly conduct Kaizen events to identify areas for improvement, implement solutions, and measure their effectiveness. This requires a culture of open communication, collaboration, and a commitment to continuous learning. The cycle of identifying issues, testing solutions, and implementing changes based on data is key.
Measuring the Success of TPM Implementation
Monitoring and measuring the effectiveness of TPM is essential to demonstrate its value and to identify areas for improvement. Key performance indicators (KPIs) can track various aspects of the program’s success. Some vital KPIs include:
- Overall Equipment Effectiveness (OEE): A widely used metric that measures the combined impact of availability, performance, and quality on production equipment.
- Mean Time Between Failures (MTBF): Measures the average time between equipment failures, indicating improved reliability.
- Mean Time To Repair (MTTR): Indicates the average time required to repair failed equipment, showing improvements in maintenance efficiency.
- Downtime Reduction: Measures the decrease in unplanned downtime, a direct indicator of TPM effectiveness.
- Maintenance Costs: Tracks changes in maintenance expenses, highlighting cost savings achieved through TPM.
- Employee Engagement and Satisfaction: Measures the level of employee involvement and satisfaction with TPM implementation.
By regularly monitoring these KPIs, organizations can track progress, identify areas for improvement, and demonstrate the positive impact of TPM on their bottom line.
The Benefits of TPM: A Holistic Approach to Manufacturing Excellence
Implementing TPM offers a multitude of benefits that extend beyond simply improving equipment maintenance. It fosters a culture of continuous improvement, enhancing operational efficiency, and contributing significantly to the overall success of the organization.
-
Increased Equipment Uptime: By addressing potential issues proactively and empowering operators to perform basic maintenance, TPM significantly reduces downtime, leading to increased production output and meeting higher production demands.
-
Reduced Maintenance Costs: Preventative maintenance, along with reduced emergency repairs, translates into significant cost savings over time.
-
Improved Product Quality: Well-maintained equipment produces higher quality products with fewer defects, resulting in enhanced customer satisfaction and reduced waste.
-
Enhanced Safety: A proactive approach to maintenance reduces the risks associated with equipment malfunction, improving workplace safety for all employees.
-
Increased Employee Engagement: TPM empowers employees by giving them ownership and responsibility for equipment maintenance, fostering a sense of pride and accomplishment.
-
Improved Workplace Culture: TPM promotes teamwork, communication, and continuous improvement, building a stronger and more collaborative work environment.
-
Enhanced Competitive Advantage: TPM's focus on maximizing equipment effectiveness provides a significant competitive advantage in today's demanding marketplace.
In conclusion, Total Productive Maintenance is not merely a maintenance program but a holistic approach that transforms the way organizations manage their equipment and processes. By focusing on proactive maintenance, employee empowerment, and continuous improvement, TPM delivers significant benefits in terms of increased productivity, reduced costs, and enhanced competitiveness. It requires commitment, planning, and ongoing effort, but the rewards are substantial and long-lasting, creating a truly more efficient and productive environment.
Latest Posts
Latest Posts
-
What Does The Arrow Mean In A Food Chain
May 09, 2025
-
Which Is Not An Example Of An Abiotic Factor
May 09, 2025
-
Scraping Of Material From The Body For Microscopic Examination
May 09, 2025
-
How Should Hard Intake Hose Be Cleaned After Use
May 09, 2025
-
Which Question Below Represents A Crm Reporting Technology Example
May 09, 2025
Related Post
Thank you for visiting our website which covers about Total Productive Maintenance Is Best Described As . We hope the information provided has been useful to you. Feel free to contact us if you have any questions or need further assistance. See you next time and don't miss to bookmark.