Two Technicians Are Discussing Retrofitting Cfc-12 Systems
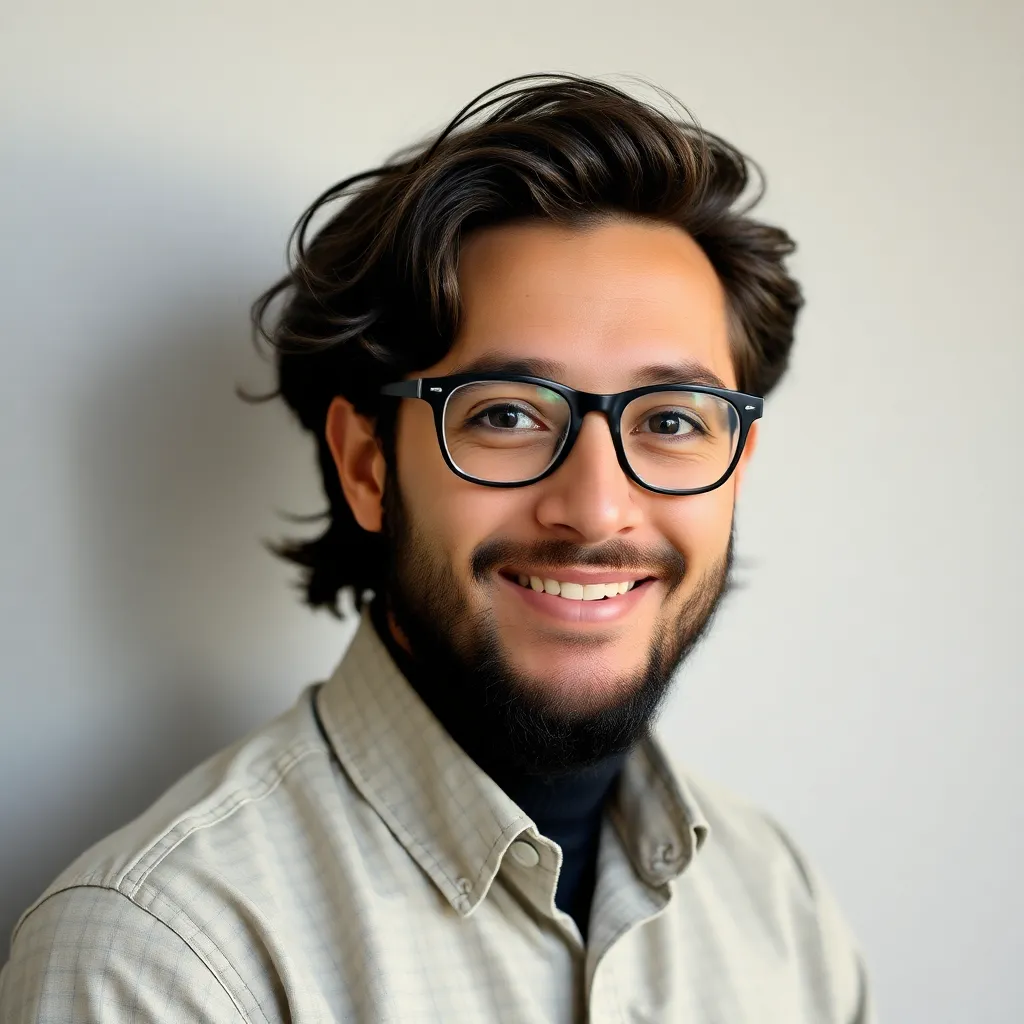
Breaking News Today
May 10, 2025 · 6 min read
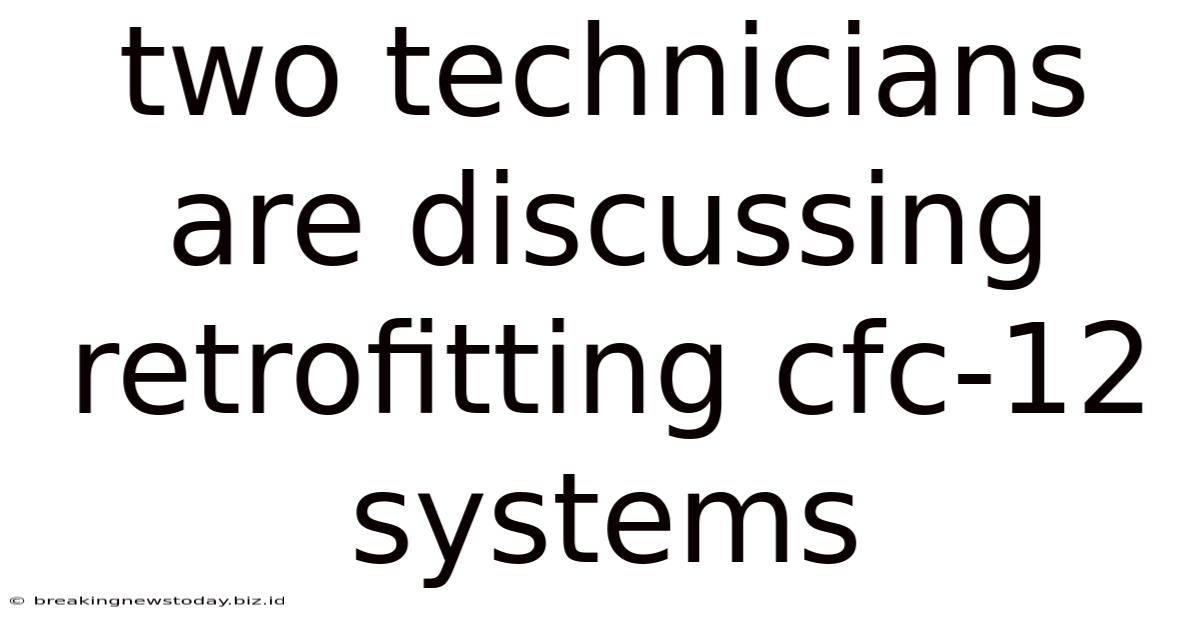
Table of Contents
Retrofitting CFC-12 Systems: A Technician's Roundtable
The phase-out of chlorofluorocarbons (CFCs), specifically CFC-12, has been a landmark event in environmental protection. However, numerous refrigeration systems still utilize this ozone-depleting substance, necessitating retrofitting to environmentally friendly alternatives. This article delves into a discussion between two experienced refrigeration technicians, Mark and David, as they navigate the complexities of CFC-12 system retrofitting.
The Challenges of CFC-12 Retrofitting
Mark: David, we've got another CFC-12 system on our hands. This older supermarket chiller is still running on R-12, and the client's understandably worried about the environmental impact and potential future maintenance headaches.
David: It's a common problem, Mark. These older systems present unique challenges. Simply replacing the refrigerant isn't enough. We need a comprehensive approach. The biggest hurdle is compatibility. R-12 has specific properties – its pressure-temperature relationship, oil compatibility, and lubrication characteristics – that aren't easily replicated. Finding a suitable drop-in replacement is tricky.
Mark: Precisely. A direct replacement might seem appealing, but often, it’s a band-aid solution. We've seen situations where seemingly compatible refrigerants lead to premature component failure due to differences in operating pressures and lubrication. The system's efficiency can also plummet.
David: And let's not forget the potential for leaks. Older systems often have deteriorated seals and components, increasing the likelihood of refrigerant leaks during the conversion process. Finding and repairing these leaks is critical before introducing a new refrigerant. We need to perform a thorough leak detection and repair before even thinking about the conversion process. This often requires specialized equipment and techniques.
Assessing the System: A Critical First Step
Mark: Absolutely. Before we even consider which refrigerant to use, a detailed system assessment is mandatory. This involves meticulously documenting the existing system's components, including the compressor, condenser, evaporator, and expansion device. We need to check for any signs of wear and tear, corrosion, or leaks. Pressure testing is also essential.
David: I always use a combination of electronic leak detectors and pressure testing with nitrogen. Nitrogen is inert, so it won't damage the system, and it helps pinpoint the exact location of any leaks. We then need to assess the condition of the compressor oil. R-12 systems traditionally use mineral oil, which isn't compatible with many modern refrigerants.
Mark: That's a key point. The oil needs to be compatible with the chosen replacement refrigerant. Using incompatible oils can lead to sludge formation, compressor damage, and even system failure. In many cases, a complete oil change is necessary.
Choosing the Right Refrigerant: A Balancing Act
David: Selecting the right replacement refrigerant is a critical decision. There isn't a single perfect solution; the choice depends on various factors, including the system's design, capacity, and the specific application.
Mark: We often consider HFCs, like R-134a, or blends like R-407C. R-134a has been widely used as a replacement for R-12, but it often requires some system modifications, especially regarding the expansion device. The pressure-temperature characteristics are different, which necessitates adjustments.
David: R-407C is another option, and although it's a blend, it typically requires less modification. However, its performance might not be identical to R-12, and we might need to adjust superheat and subcooling settings to optimize efficiency. We always need to refer to the manufacturer's guidelines for retrofitting specific refrigerants.
Mark: The key is thorough research. We need to evaluate the performance characteristics of different refrigerants and compare them to the original R-12 system. This includes factors like capacity, efficiency, and operating pressures. Some might require minor modifications, while others might require more extensive alterations, like changing the expansion valve. It's a balancing act between cost and performance.
Modifications and Adaptations: A Delicate Process
David: Retrofit isn't always a simple swap. Sometimes, we need to make modifications to the system to ensure compatibility with the new refrigerant. This can include replacing the expansion valve, adjusting the metering device, or even upgrading the compressor, depending on the chosen refrigerant.
Mark: Exactly. For instance, if we're using R-134a, we'll often need to replace the expansion valve with one that’s designed to operate at R-134a's pressure and temperature. A slightly larger expansion valve might be necessary to compensate for potential pressure drops. This requires precision and care to avoid introducing any leaks or damaging the system.
David: Sometimes, we might need to replace the compressor entirely, especially if the old compressor isn't compatible with the new refrigerant or its oil. Modern compressors are designed for efficiency and environmental impact in mind. This could represent a substantial financial investment for the client, but often improves long term efficiency and saves on energy costs.
The Importance of Proper Training and Certification
Mark: I can't stress enough the importance of proper training and certification for this type of work. Retrofitting CFC-12 systems involves working with refrigerants and handling high-pressure components – it requires specialized knowledge and skills.
David: Absolutely. Technicians must be properly trained to handle refrigerants safely and efficiently, complying with all relevant environmental regulations. Certification ensures technicians are equipped to handle the technical aspects of the retrofit process and understand the environmental considerations. Ignoring this is hazardous for both the technicians and the environment.
Post-Retrofit Testing and System Optimization
Mark: After the retrofit, a thorough testing phase is crucial. We need to check for leaks, verify that the system is operating within the appropriate pressure and temperature ranges, and assess the overall system performance.
David: We should monitor system performance over several days or weeks to ensure it's running smoothly. We’ll check refrigerant pressures, temperatures, and capacity. Any discrepancies might indicate problems that need addressing.
Mark: Proper system optimization is also important. This involves fine-tuning the system's settings to maximize efficiency and minimize energy consumption. This might include adjusting the superheat and subcooling, and optimizing the refrigerant charge.
Conclusion: A Sustainable Solution
David: Retrofitting CFC-12 systems is a complex but necessary process. It requires a thorough understanding of refrigeration systems, refrigerant properties, and environmental regulations. While it’s more expensive than a simple refrigerant replacement, it’s a crucial step towards environmental responsibility and ensuring the long-term reliability of these older systems.
Mark: Precisely. By undertaking a professional and well-planned retrofit, we not only protect the ozone layer but also enhance the efficiency and longevity of these existing systems. Clients will reap the benefits in reduced energy consumption and long-term cost savings, all while contributing to a cleaner planet. The added investment upfront translates to a much better return over time.
This conversation highlights the intricacies involved in retrofitting CFC-12 systems. It’s a specialized process requiring expert knowledge, careful planning, and adherence to safety and environmental regulations. The result, however, is a sustainable solution that minimizes environmental impact while ensuring the continued functionality of essential refrigeration systems. The future of refrigeration lies in environmentally friendly practices, and retrofitting plays a vital role in this transition.
Latest Posts
Latest Posts
-
A Driver Be Cited For Drowsy Driving
May 10, 2025
-
Which Blood Vessel Carries Blood Into A Glomerulus
May 10, 2025
-
Sort These Items Into The Appropriate Bins
May 10, 2025
-
Chapter 10 Nutrition For Health Worksheet Answer Key
May 10, 2025
-
Quotes Of Mary Warren In The Crucible
May 10, 2025
Related Post
Thank you for visiting our website which covers about Two Technicians Are Discussing Retrofitting Cfc-12 Systems . We hope the information provided has been useful to you. Feel free to contact us if you have any questions or need further assistance. See you next time and don't miss to bookmark.