Welding Cable Must Be Spliced ____ The Electrode Holder.
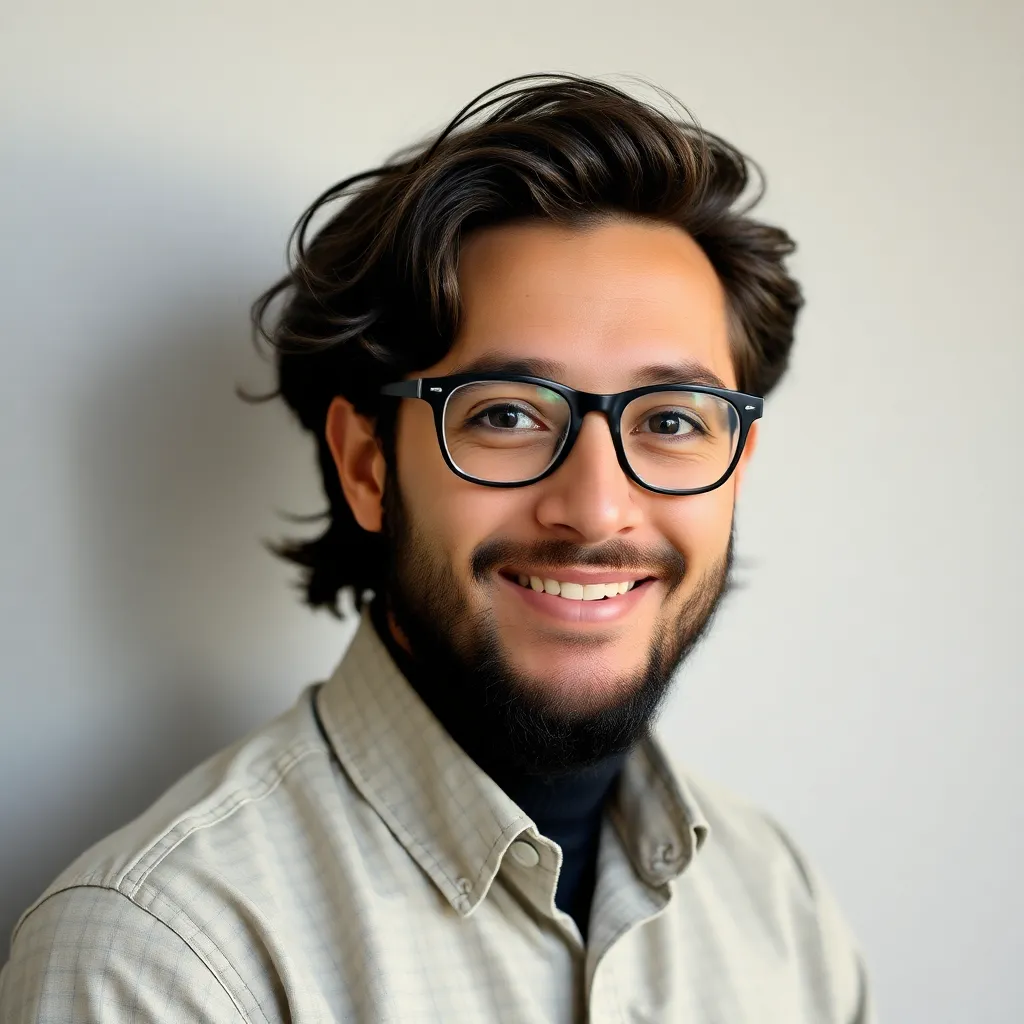
Breaking News Today
May 11, 2025 · 6 min read
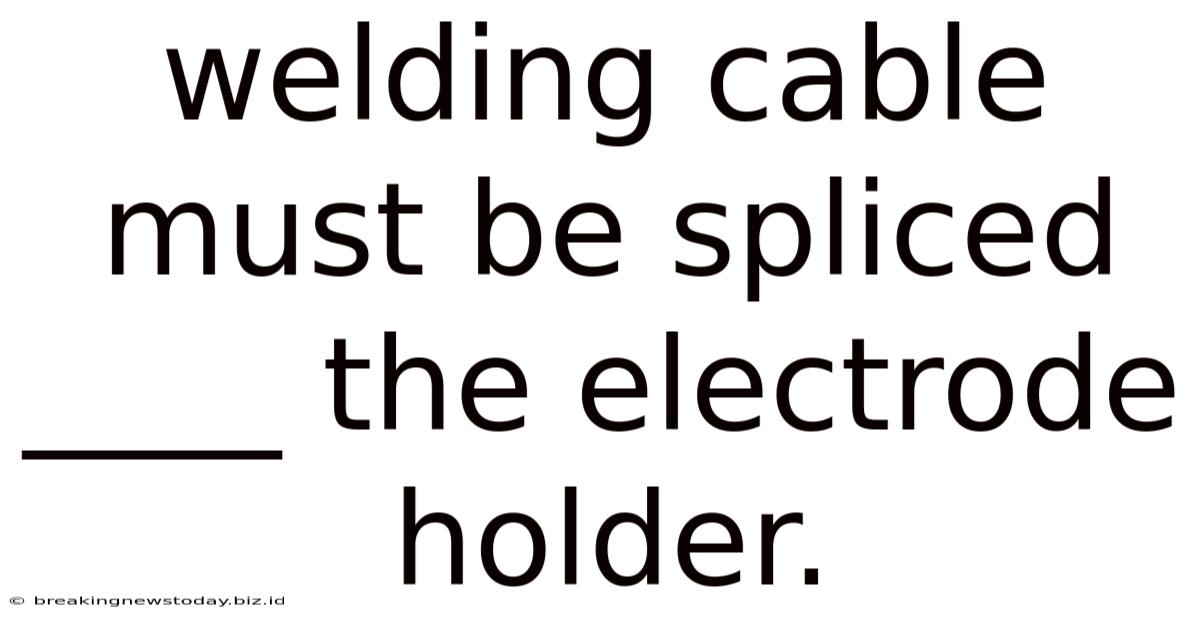
Table of Contents
Welding Cable: Splicing Techniques and Best Practices Near the Electrode Holder
Welding, a fundamental process in various industries, relies heavily on the efficient and safe transmission of electrical current. This transmission is achieved through welding cables, robust conductors that carry substantial amperage from the power source to the electrode holder and workpiece. A critical aspect of maintaining the integrity and functionality of this system involves understanding how and where to splice welding cables, particularly in the vicinity of the electrode holder. This article delves into the intricacies of splicing welding cables near the electrode holder, focusing on best practices, safety precautions, and the potential consequences of improper splicing.
Why Splicing Welding Cables is Necessary
Welding cables, despite their durability, are susceptible to wear and tear. Factors such as abrasion, excessive flexing, and exposure to harsh environments can damage the cable insulation and conductors, compromising its operational efficiency and creating safety hazards. Splicing becomes necessary when:
- Cable damage: Severe damage, such as cuts, significant abrasion, or exposed conductors, necessitates splicing to restore the cable's integrity.
- Cable extension: In certain scenarios, the existing cable length might be insufficient to reach the welding area. Splicing allows for extending the cable's reach.
- Cable replacement: If a section of the cable becomes irreparably damaged, splicing allows for the replacement of only the affected segment rather than the entire cable.
The Critical Zone: Near the Electrode Holder
Splicing welding cables near the electrode holder requires extra care and precision. This area experiences higher current densities and substantial mechanical stress due to the continuous movement and flexing of the cable during welding operations. Improper splicing in this critical zone can lead to several serious issues:
- Increased Resistance: A poorly executed splice can introduce additional resistance, leading to voltage drops, reduced welding performance, and increased heat generation within the splice itself, potentially causing melting or fire.
- Arc Blow: Inconsistent current flow due to a faulty splice can exacerbate arc blow, disrupting the welding arc and compromising weld quality.
- Safety Hazards: A poorly made splice can lead to loose connections, sparking, and even short circuits, creating serious fire and electrical shock hazards for the welder.
Splicing Methods: A Comparative Analysis
Several splicing methods exist for welding cables, each with its strengths and limitations. The choice of method should always prioritize safety, durability, and compatibility with the cable's amperage rating. Here are some commonly used methods:
1. Compression Connectors
Compression connectors utilize a crimping tool to securely connect two cable ends. These connectors offer a reliable, efficient, and relatively fast splicing method when used correctly. Key advantages include ease of use, relatively low cost, and excellent electrical conductivity when properly crimped. However, improper crimping can lead to poor electrical contact, increasing resistance and posing safety risks. Careful selection of the correct connector size and type, and use of a high-quality crimping tool, are crucial.
2. Solder Splices
Soldering provides a strong mechanical and electrical connection, but requires more skill and precision. Advantages include excellent conductivity and the ability to create a watertight seal. However, soldering needs a controlled environment and appropriate equipment, and improper execution can damage the cable insulation or the conductors. It's crucial to use a solder that is compatible with the cable material and insulation. Furthermore, the use of solder is often less desirable for high-amperage applications.
3. Welding Cable Connectors
These are specialized connectors designed for welding applications and typically utilize a clamping mechanism or screw terminals. They provide a secure connection and are often preferred for their ease of use and robust design. Advantages include ease of connection and disconnection, robust design, and typically high current carrying capacity. However, careful selection is needed based on the cable's amperage rating and type.
4. Braided Sleeve Connectors
Braided sleeve connectors offer excellent flexibility and current carrying capacity. The conductor ends are inserted into a braided copper sleeve, and then the sleeve is crimped or soldered to create a secure connection. Advantages include flexibility and high current-carrying capacity. However, this method requires more specialized tools and expertise compared to other methods.
Best Practices for Splicing Welding Cables Near the Electrode Holder
Regardless of the chosen splicing method, several crucial best practices should be followed to ensure safety, efficiency, and longevity:
- Proper Cable Selection: Choose welding cables with an ampacity rating that exceeds the welding machine's maximum output current. Consider the cable's insulation type and its resistance to heat, abrasion, and the welding environment.
- Use Appropriate Tools: Employ high-quality crimping tools, soldering irons, and other necessary tools specifically designed for welding cable splicing. Using inappropriate tools can lead to faulty connections and safety hazards.
- Clean Connection Points: Before splicing, ensure the cable ends are clean and free from dirt, grease, or corrosion. This is crucial for optimal electrical contact and minimizing resistance.
- Protect Splices: After splicing, thoroughly insulate the splice using heat-shrink tubing, electrical tape, or other suitable insulating materials. This is essential to protect the splice from damage, moisture, and accidental contact.
- Strain Relief: Implement strain relief mechanisms to prevent excessive stress and tension on the splice, which could lead to failure.
- Regular Inspection: Regularly inspect all cable splices for signs of damage, wear, or overheating. Replace or repair any damaged splices immediately to prevent potential hazards.
- Safety First: Always disconnect the power source before working on welding cables. Wear appropriate personal protective equipment (PPE), including safety glasses, gloves, and protective clothing.
- Proper Grounding: Ensure the welding machine and workpiece are properly grounded to prevent electrical shocks and minimize the risk of fire.
Consequences of Improper Splicing
Ignoring best practices and employing improper splicing techniques can lead to several serious consequences:
- Equipment damage: Faulty connections can damage the welding machine, electrode holder, and other equipment due to overheating and excessive current flow.
- Weld defects: Inconsistent current flow caused by poor splices can result in inconsistent welds, leading to reduced strength, porosity, and other defects.
- Injuries: Poorly insulated splices can cause electric shocks, burns, and fire hazards to the welder.
- Increased costs: Replacing damaged equipment and repairing faulty welds significantly increases production costs.
- Downtime: Repairing faulty splices or replacing damaged equipment leads to production downtime, affecting productivity and efficiency.
Conclusion
Splicing welding cables near the electrode holder is a critical task that demands precision, skill, and adherence to safety standards. Choosing the right splicing method, using appropriate tools, and following best practices are paramount to maintaining the integrity and safety of the welding system. Regular inspection and timely repairs are crucial for preventing accidents, ensuring consistent welding performance, and minimizing the risk of costly downtime. Neglecting these important aspects can have serious consequences, potentially leading to equipment damage, injuries, and increased operational costs. By prioritizing safety and employing correct splicing techniques, welders can ensure the reliable and safe operation of their equipment.
Latest Posts
Latest Posts
-
A Partial Bath Includes Washing A Residents
May 12, 2025
-
Which Of The Following Describes A Net Lease
May 12, 2025
-
Nurse Logic 2 0 Knowledge And Clinical Judgment
May 12, 2025
-
Panic Disorder Is Characterized By All Of The Following Except
May 12, 2025
-
Positive Individual Traits Can Be Taught A True B False
May 12, 2025
Related Post
Thank you for visiting our website which covers about Welding Cable Must Be Spliced ____ The Electrode Holder. . We hope the information provided has been useful to you. Feel free to contact us if you have any questions or need further assistance. See you next time and don't miss to bookmark.