What Are The Equipment Requirements For Windshields And Side Windows
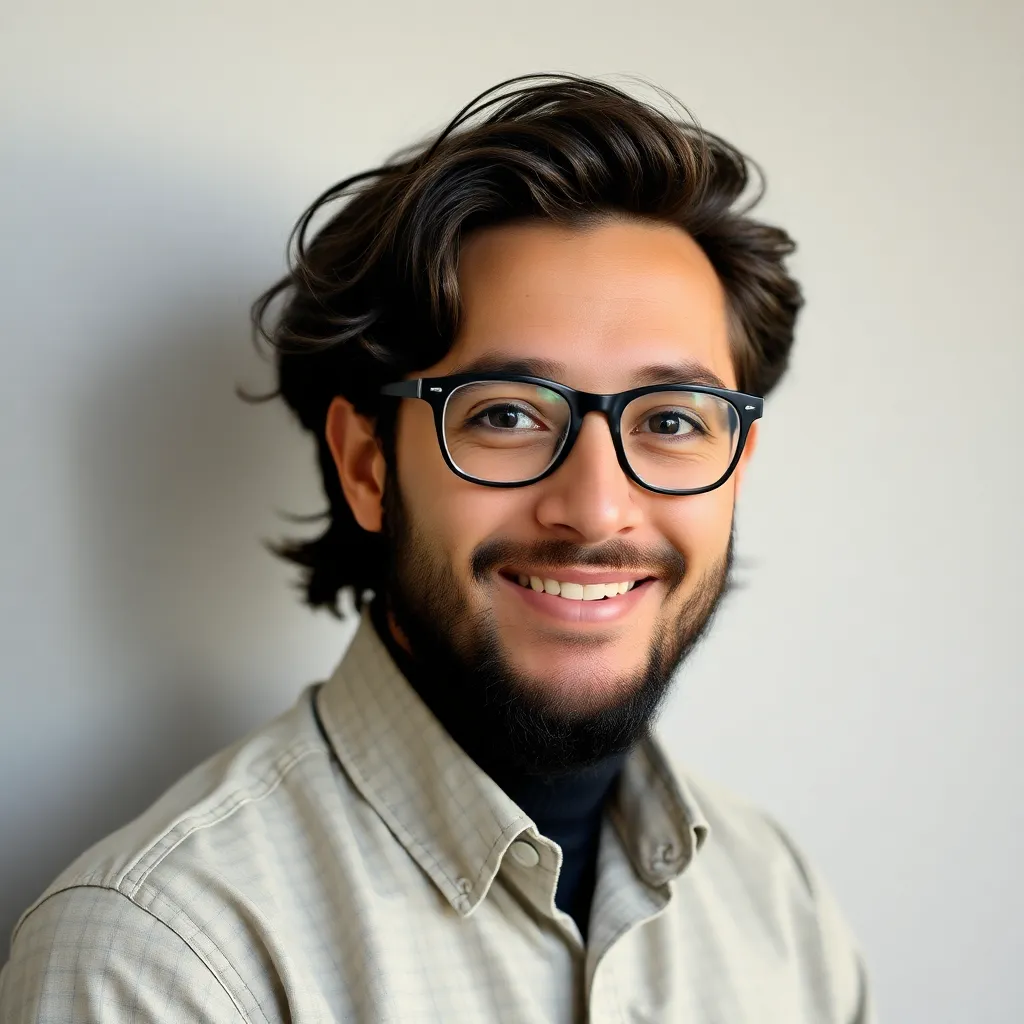
Breaking News Today
May 12, 2025 · 6 min read
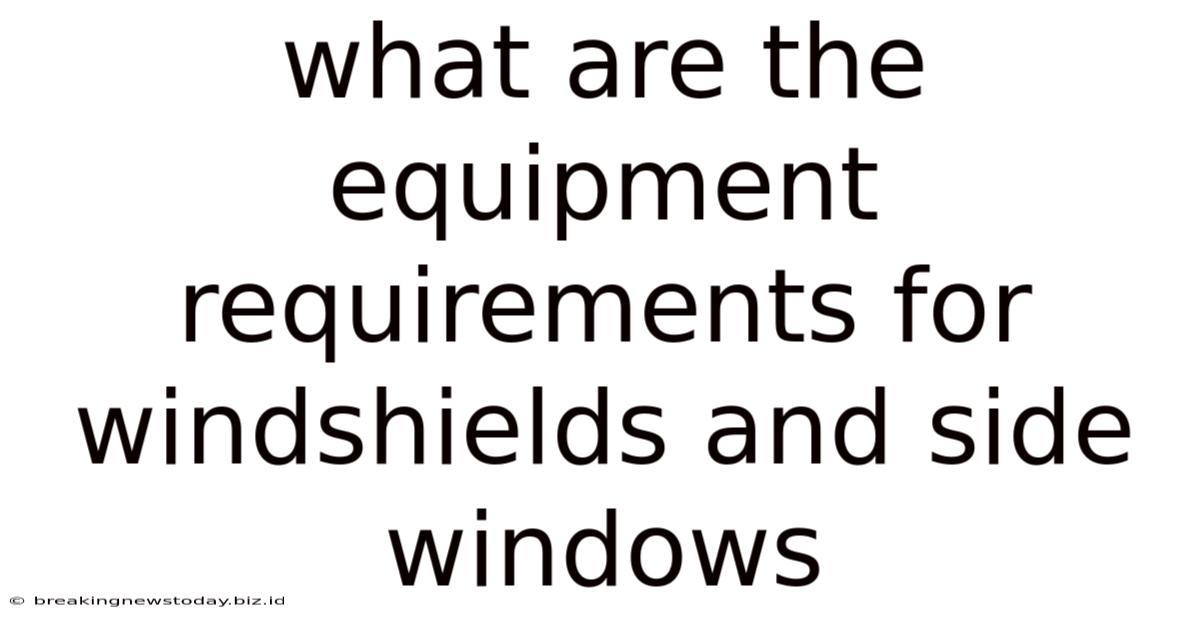
Table of Contents
What are the Equipment Requirements for Windshields and Side Windows?
The automotive glass industry is a complex one, involving stringent safety regulations and precise manufacturing processes. Understanding the equipment requirements for producing windshields and side windows – from initial raw material handling to final quality control – is crucial for anyone involved in this field, whether as a manufacturer, supplier, or even a consumer seeking to understand the quality behind the glass protecting them. This comprehensive guide delves into the diverse equipment needed at each stage, emphasizing safety and precision throughout.
I. Raw Material Handling and Preparation
Before any glass shaping or processing begins, the raw materials need careful handling and preparation. This stage significantly impacts the final product's quality and consistency.
A. Raw Material Storage and Transportation
Storage: Float glass, the primary raw material, requires careful storage to prevent damage or contamination. This typically involves climate-controlled warehouses with specialized racking systems designed to minimize stress on the large glass sheets. Proper stacking and protection from environmental factors like humidity and temperature fluctuations are vital.
Transportation: Specialized transport vehicles equipped with shock absorbers and secure fastening mechanisms are needed to ensure the safe transit of the fragile glass sheets from the manufacturing plant to the processing facility. This minimizes the risk of breakage during transport, reducing waste and ensuring the availability of high-quality raw materials.
B. Glass Cutting and Sizing
Precision cutting is crucial for efficient material utilization and the creation of accurately sized glass blanks for windshields and side windows. This step typically uses:
- Computer-controlled glass cutters: These high-precision machines utilize diamond-tipped blades or laser cutting systems to accurately cut the glass sheets to the precise dimensions required for each vehicle model. The software controlling these cutters often integrates CAD (Computer-Aided Design) data for automated cutting processes.
- CNC (Computer Numerical Control) Routers: These machines enable highly precise cutting, shaping, and drilling of complex contours, particularly beneficial for curved windshields. They often employ various cutting tools, depending on the material hardness and desired finish.
C. Cleaning and Surface Preparation
Cleanliness is paramount in glass processing. Contamination on the glass surface can significantly affect the adhesion of subsequent layers like interlayers and coatings. This process employs:
- Automated cleaning systems: These utilize a series of wash and rinse cycles with specialized detergents to remove dust, debris, and other contaminants from the glass surface. Ultrasonic cleaning might be incorporated for particularly challenging cleaning tasks.
- Inspection systems: Automated vision systems inspect the cleaned glass sheets for any remaining defects or imperfections before proceeding to the next stage. These systems provide real-time feedback, ensuring only flawless glass is used in further processing.
II. Windshield and Side Window Laminating
Laminating is a critical process in windshield manufacturing, combining layers of glass with a polyvinyl butyral (PVB) interlayer. This crucial step enhances safety and provides strength. The equipment required includes:
A. Laminating Autoclaves
Autoclaves: These high-pressure, high-temperature chambers are essential for bonding the glass sheets and PVB interlayer. Precise control over temperature and pressure is vital to ensure consistent curing and adhesion. The size and capacity of the autoclave depend on the volume and size of the windshields being laminated.
Vacuum Systems: Effective vacuum systems are crucial for removing air bubbles from between the glass and PVB layers. This ensures a flawless, optically clear laminated structure and avoids compromising safety. These systems often incorporate advanced pressure monitoring and control technologies.
B. Laminate Inspection and Quality Control
Post-lamination, rigorous inspection is essential to identify any defects. This stage utilizes:
- Automated optical inspection systems: These systems scan the laminated glass for defects like air bubbles, scratches, and delamination. Advanced imaging techniques allow for high-resolution detection of even minute imperfections.
- Strength testing equipment: Specialized machines test the laminated glass's strength and impact resistance to ensure it meets safety standards. This step includes impact tests and stress tests simulating real-world driving conditions.
III. Side Window Manufacturing
Side windows typically undergo a different process compared to windshields. They often require less complex shaping and usually aren't laminated but may incorporate coatings.
A. Heat Bending or Forming
For curved side windows, sophisticated heating and forming equipment is necessary.
- Heat bending furnaces: These furnaces precisely control the temperature profile to carefully bend the glass sheets to the required curvature. Precise temperature control is crucial to prevent cracking or distortion during the bending process.
- Forming molds: These molds determine the exact shape of the curved side windows. They are precisely engineered and often made from heat-resistant materials.
B. Coating Application
Many side windows incorporate coatings for improved performance characteristics such as UV protection, heat reduction, or acoustic insulation. This often involves:
- Coating applicators: These machines precisely apply thin layers of coatings to the glass surface using methods like spraying, dipping, or curtain coating. Precise control over coating thickness and uniformity is crucial for performance.
- Curing ovens: After coating application, curing ovens ensure proper adhesion and hardening of the coating. The process often involves carefully controlled temperature and humidity levels.
IV. Cutting, Edge Finishing, and Drilling
Regardless of whether it's for windshields or side windows, the final stage often involves precise cutting, edge finishing, and drilling for fittings. This involves:
A. Precise Cutting and Shaping
Advanced CNC cutting machines, similar to those used in raw material preparation, are employed to achieve high precision for final trimming and shaping. This is particularly crucial for ensuring a perfect fit in the vehicle's frame.
B. Edge Finishing and Grinding
Sharp edges are unacceptable for safety reasons. This process relies on:
- Edge grinding machines: These machines smooth and round the edges of the glass, eliminating sharp corners and making them safe to handle. Precise control over grinding depth and surface finish is needed.
- Polishing machines: After grinding, polishing machines further refine the edges, creating a smooth and aesthetically pleasing finish.
C. Drilling for Fittings
Precisely placed holes are needed for mounting hardware.
- CNC drilling machines: These machines use diamond-tipped drill bits to create accurate holes for attaching the glass to the vehicle. High precision is essential to avoid any misalignment or damage to the glass.
V. Quality Control and Inspection
Throughout the entire manufacturing process, robust quality control is paramount. This involves multiple inspections at various stages:
- Visual Inspection: Manual and automated visual inspections detect surface flaws and imperfections. This is critical for ensuring that only flawless glass components are used in vehicles.
- Dimensional Inspection: Measurements ensure adherence to precise specifications, verifying that each component is correctly sized and shaped for a perfect fit.
- Strength and Durability Testing: Rigorous testing ensures the glass meets or exceeds safety standards regarding impact resistance, stress endurance, and overall durability.
VI. Packaging and Shipping
The final stage involves carefully packaging the finished windshields and side windows for safe transport to automotive manufacturers or distributors. This requires:
- Protective Packaging: Specialized packaging materials, including cushioning, protective films, and sturdy containers, are used to safeguard the glass from damage during shipping and handling.
- Labeled and Tracked Shipping: Clear labeling and efficient tracking systems are employed to monitor the transportation process, ensuring timely and safe delivery to the destination.
This detailed overview highlights the diverse and sophisticated equipment involved in the manufacturing of windshields and side windows. Each step demands precision, accuracy, and strict adherence to safety regulations, resulting in high-quality automotive glass crucial for vehicle safety and performance. The continual advancements in technology will undoubtedly further refine these processes and enhance the capabilities of the equipment used in this critical industry.
Latest Posts
Latest Posts
-
A Partial Bath Includes Washing A Residents
May 12, 2025
-
Which Of The Following Describes A Net Lease
May 12, 2025
-
Nurse Logic 2 0 Knowledge And Clinical Judgment
May 12, 2025
-
Panic Disorder Is Characterized By All Of The Following Except
May 12, 2025
-
Positive Individual Traits Can Be Taught A True B False
May 12, 2025
Related Post
Thank you for visiting our website which covers about What Are The Equipment Requirements For Windshields And Side Windows . We hope the information provided has been useful to you. Feel free to contact us if you have any questions or need further assistance. See you next time and don't miss to bookmark.