What Items Make Up A Basic Semiautomatic Welding System
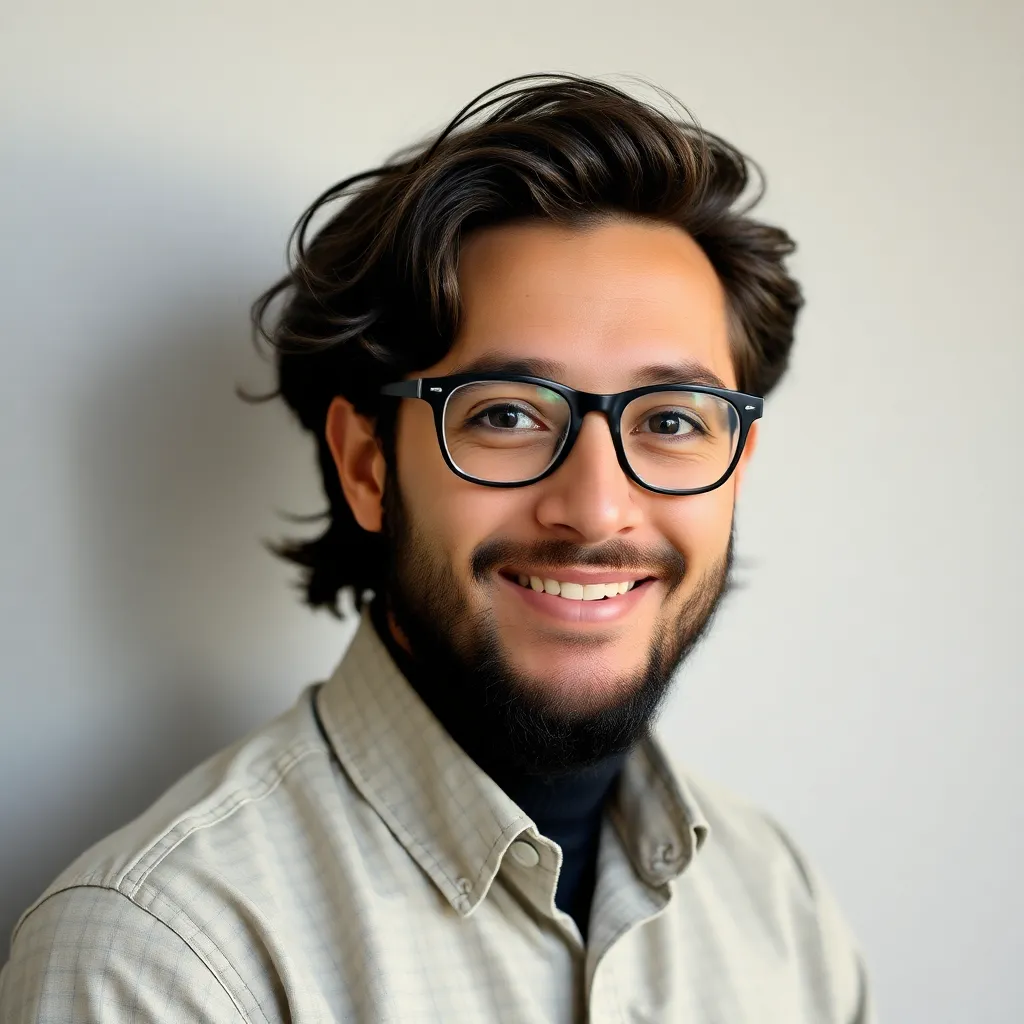
Breaking News Today
Apr 19, 2025 · 7 min read

Table of Contents
What Items Make Up a Basic Semiautomatic Welding System?
A semiautomatic welding system offers a significant upgrade from manual welding, providing increased speed, consistency, and ease of use. Understanding the components of such a system is crucial for both novice and experienced welders. This comprehensive guide breaks down the essential elements of a basic semiautomatic welding system, explaining their function and importance in achieving high-quality welds.
The Core Components: A Semiautomatic Welding System Breakdown
A basic semiautomatic welding system, typically used for Gas Metal Arc Welding (GMAW), also known as MIG welding, comprises several key components working in concert. These can be broadly categorized into:
1. The Power Source: The Heart of the System
The power source is the brain of the operation, supplying the electrical energy needed to create the arc. This is a crucial component, determining the welding process's capabilities and quality. Different power sources offer varying characteristics, affecting the welder's control and the quality of the final weld.
-
Constant Voltage (CV) Power Sources: These are the most common type for semiautomatic welding. They maintain a consistent voltage, allowing the welding current to adjust based on the arc length and wire feed speed. This offers good control and arc stability, especially beneficial for welding different thicknesses of metal.
-
Constant Current (CC) Power Sources: Less common in semiautomatic welding, constant current power sources maintain a constant current regardless of arc length. While simpler in design, they offer less control and arc stability compared to CV power sources.
-
Synergic Power Sources: These sophisticated power sources automatically adjust welding parameters based on the selected wire type, diameter, and material thickness. This simplifies the welding process, especially for beginners, by reducing the need for manual adjustments.
Key Considerations for Power Source Selection:
- Welding Current Range: This determines the thickness of materials you can weld.
- Duty Cycle: This indicates the percentage of time the power source can operate at its maximum current output before overheating. A higher duty cycle is essential for prolonged welding tasks.
- Voltage Output: This impacts the arc characteristics and penetration depth.
- Features: Look for features such as voltage adjustment, wire feed speed control, and pre/post-flow gas control.
2. The Wire Feeder: Precise and Reliable Wire Delivery
The wire feeder is the mechanism that precisely feeds the welding wire from the spool to the contact tip. Its accuracy directly impacts the quality and consistency of the weld. A malfunctioning wire feeder can result in inconsistent welds, interruptions, and even safety hazards.
-
Motor-Driven Feeders: Most semiautomatic systems utilize motor-driven feeders, offering precise control over wire feed speed. These are generally more reliable and consistent than gravity-fed systems.
-
Drive Rollers: These rollers grip and feed the welding wire, ensuring a steady supply to the contact tip. The condition of the drive rollers is critical; worn or damaged rollers can lead to inconsistent wire feeding.
-
Wire Feed Speed Control: This is a crucial adjustment allowing the welder to control the amount of filler metal deposited. Proper wire feed speed is essential for achieving the desired weld penetration and bead shape.
Key Considerations for Wire Feeder Selection:
- Wire Feed Speed Range: This should be adjustable to accommodate different wire diameters and welding applications.
- Drive Rollers: Ensure the rollers are suitable for the wire diameter being used.
- Durability: A robust wire feeder is vital for consistent performance.
3. The Welding Gun (Torch): Delivering the Arc
The welding gun is the tool that delivers the welding wire to the weld pool and conducts the welding current. It's the interface between the welder and the welding process. The gun's design and quality significantly influence the welding experience and the weld's final appearance.
-
Contact Tip: This is the component at the end of the gun through which the welding wire passes. It wears down over time and needs to be replaced regularly to maintain consistent arc characteristics.
-
Gas Nozzle: This directs the shielding gas around the welding arc, protecting it from atmospheric contamination. The gas nozzle size is usually matched to the contact tip size.
-
Trigger: This controls the flow of current and wire feed. Different designs offer varying levels of comfort and control.
-
Cable Assembly: The cable assembly connects the gun to the power source and wire feeder, transmitting the electrical current and signals.
Key Considerations for Welding Gun Selection:
- Ergonomics: Comfort and ease of use are crucial for reducing fatigue during extended welding sessions.
- Durability: The gun should withstand the rigors of welding.
- Replaceable Parts: The availability of replacement parts such as contact tips and gas nozzles is essential.
4. Shielding Gas: Protecting the Weld
Shielding gas is crucial for preventing atmospheric contamination of the weld pool. This prevents oxidation and porosity, ensuring the weld's strength and quality. The type of gas used depends on the welding application and the materials being joined.
-
Common Gases: Common shielding gases include Argon, Carbon Dioxide (CO2), and mixtures of Argon and CO2. The choice depends on factors such as the material being welded and the desired weld characteristics.
-
Gas Flow Rate: The gas flow rate is adjustable, impacting the effectiveness of the shielding gas. Insufficient gas flow can lead to weld porosity, whereas excessive flow can increase costs and create turbulence.
-
Gas Cylinder and Regulator: A gas cylinder supplies the shielding gas, while a regulator controls the gas flow rate.
Key Considerations for Shielding Gas Selection:
- Material Compatibility: Select the shielding gas appropriate for the materials being welded.
- Cost: Different gases have different costs.
- Weld Quality: The shielding gas significantly impacts the weld's final quality.
5. Welding Wire: The Filler Metal
Welding wire is the filler material that is melted and deposited into the weld joint, joining the base materials. The wire's composition and diameter affect the weld's strength, appearance, and penetration.
-
Wire Composition: Welding wires are available in various compositions, each designed for specific applications and materials. Steel, stainless steel, aluminum, and other alloys each require a corresponding wire type.
-
Wire Diameter: Different wire diameters influence the welding current and deposition rate. Thinner wires are typically used for thinner materials, while thicker wires are suitable for thicker materials.
Key Considerations for Welding Wire Selection:
- Material Compatibility: Choose a wire compatible with the base materials being welded.
- Diameter: Select a diameter appropriate for the material thickness and welding current.
- Quality: High-quality welding wire ensures consistent and strong welds.
Expanding the System: Optional but Beneficial Additions
While the components above form the core of a basic semiautomatic welding system, several additional components can significantly enhance its capabilities and user experience:
-
Welding Cart: A welding cart provides mobility and storage for the power source, wire feeder, gas cylinder, and other accessories.
-
Ground Clamp: A reliable ground clamp ensures a secure electrical connection to the workpiece, crucial for proper current flow and weld quality.
-
Safety Equipment: Appropriate safety equipment, including a welding helmet with appropriate shade, gloves, and protective clothing, is paramount for safety during welding.
-
Wire Brush: A wire brush is used to clean the weld area before and after welding.
-
Chipping Hammer: A chipping hammer helps remove excess weld spatter.
Maintaining Your Semiautomatic Welding System
Regular maintenance is crucial for ensuring the longevity and performance of your semiautomatic welding system. This includes:
-
Regular Inspection: Regularly inspect all components for wear and tear, paying particular attention to the contact tip, gas nozzle, and drive rollers.
-
Cleaning: Clean the welding gun and wire feeder regularly to prevent clogging and malfunction.
-
Replacing Consumables: Replace consumables such as contact tips, gas nozzles, and welding wire as needed.
-
Calibration: Periodically calibrate the wire feeder to ensure accurate wire feed speed.
-
Professional Service: Consider professional servicing for more complex maintenance or repairs.
Conclusion: Mastering Your Semiautomatic Welding System
Understanding the individual components of a semiautomatic welding system and their interdependencies is essential for achieving high-quality, consistent welds. By selecting appropriate components and performing regular maintenance, you can maximize the performance and longevity of your system. Remember that safety should always be the top priority when working with any welding equipment. Proper training and adherence to safety guidelines are crucial for preventing accidents and injuries. With careful consideration of each component and a commitment to safety, you can confidently embark on your semiautomatic welding projects.
Latest Posts
Latest Posts
-
Which Statement About The Value Of X Is True
Apr 19, 2025
-
Weekly Language Review Q1 2 Answer Key
Apr 19, 2025
-
The Are Bevel Gears Held By The Pinion Shaft
Apr 19, 2025
-
What Is The Minimum Amount Of Shrinkage For Curly Hair
Apr 19, 2025
-
Sugar Changed The World Part 4 Building Claims
Apr 19, 2025
Related Post
Thank you for visiting our website which covers about What Items Make Up A Basic Semiautomatic Welding System . We hope the information provided has been useful to you. Feel free to contact us if you have any questions or need further assistance. See you next time and don't miss to bookmark.