When Cpk Differs From Cp It Indicates The ________.
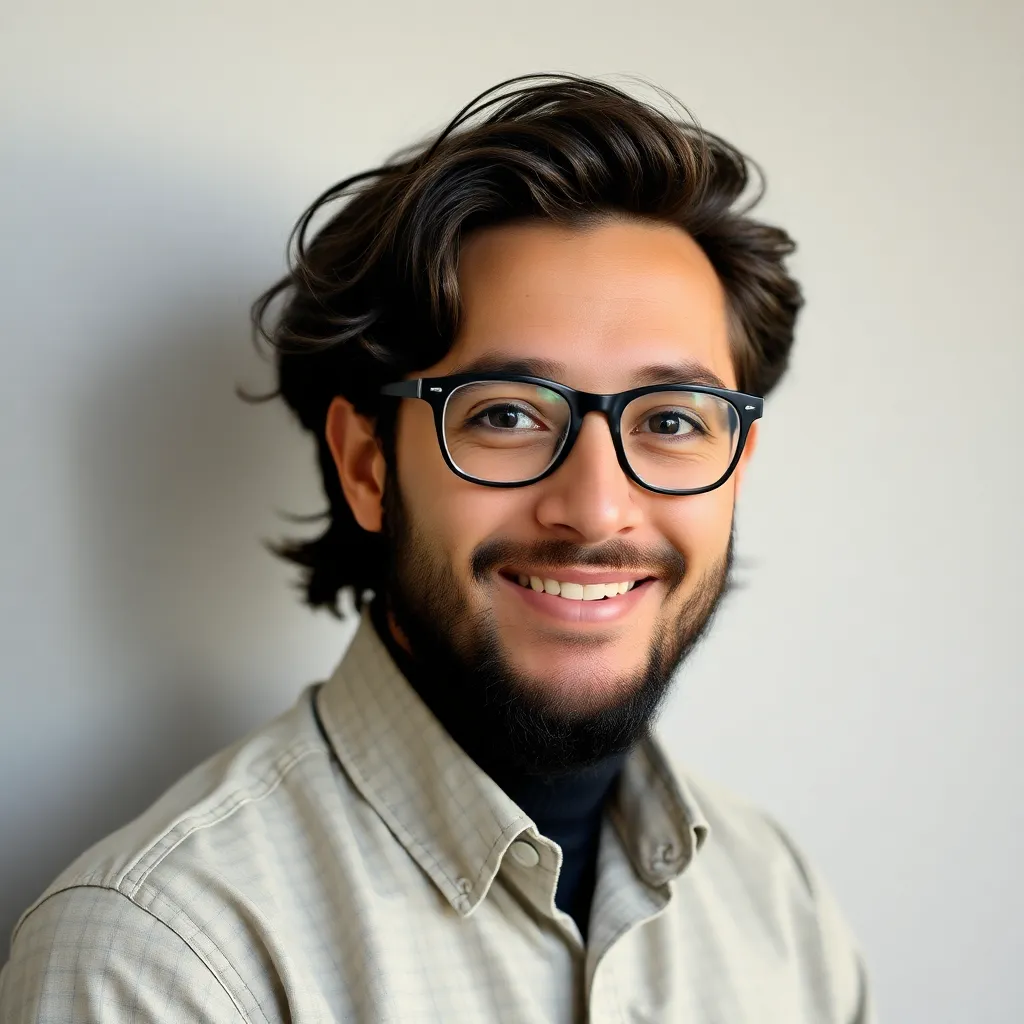
Breaking News Today
Mar 22, 2025 · 6 min read
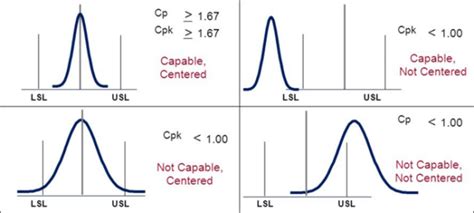
Table of Contents
When Cpk Differs From Cp: Understanding Process Capability and its Implications
Process capability analysis is crucial for any manufacturing or service-oriented business striving for consistent quality and efficiency. Two key metrics used in this analysis are Cp (Process Capability) and Cpk (Process Capability Index). While both assess the process's ability to meet specification limits, their differences highlight crucial aspects of process performance that can significantly impact product quality and customer satisfaction. When Cpk differs significantly from Cp, it indicates process centering issues. Let's delve deeper into understanding Cp, Cpk, and the implications of their disparity.
Understanding Cp: The Basic Process Capability
Cp, or the Process Capability index, is a simple measure that compares the process's natural variability to the tolerance range allowed by specifications. It essentially answers: "How much variation is present within the process relative to the allowable variation?"
- Formula: Cp = (USL - LSL) / 6σ
Where:
- USL = Upper Specification Limit
- LSL = Lower Specification Limit
- σ = Standard Deviation of the process
A higher Cp value indicates a more capable process. Generally, a Cp value of 1.0 or greater is considered acceptable, reflecting that the process spread is within the specification limits. Values above 1.0 indicate progressively better capability, with higher values demonstrating greater robustness. For instance, a Cp of 1.33 suggests that the process is capable of consistently producing outputs within the specified limits, with a margin for error.
Understanding Cpk: Incorporating Process Centering
Cpk, or the Process Capability Index, builds upon Cp by incorporating the concept of process centering. While Cp solely considers the process spread, Cpk assesses both the spread and the process mean's proximity to the target value. This addition is critical because a process might have a small spread (high Cp) but still produce outputs consistently outside the specification limits if the process mean is significantly shifted.
- Formula: Cpk = min[(USL - μ) / 3σ, (μ - LSL) / 3σ]
Where:
- μ = Process Mean
Cpk accounts for the potential offset of the process mean from the target, providing a more realistic picture of process capability. A Cpk value of 1.0 or greater is generally considered acceptable, suggesting that the process is both centered and capable of consistently meeting specification limits.
When Cpk Differs Significantly From Cp: The Implications of Process Incentering
The difference between Cp and Cpk reveals crucial insights about process performance. When Cpk is significantly lower than Cp, it unequivocally points to poor process centering. This implies that the process mean is not centered within the specification limits, even if the process variation is relatively low.
Let's visualize this:
Imagine a scenario where Cp = 1.5, indicating a capable process with low variation. However, the process mean is shifted towards one of the specification limits, resulting in a Cpk of only 0.8. This means although the process variation is low, a significant proportion of the output falls outside the acceptable range due to poor centering. This highlights the critical role of process centering in ensuring consistent product quality.
The consequences of a significant difference between Cp and Cpk can include:
- Increased defect rates: A process that is not centered will inevitably produce a higher percentage of defective items, leading to increased scrap, rework, and customer dissatisfaction.
- Higher production costs: Dealing with defects, rework, and customer complaints leads to increased production costs, potentially impacting profitability.
- Reputational damage: Consistently supplying substandard products can severely damage a company's reputation, leading to loss of market share and decreased customer loyalty.
- Missed opportunities: Inability to consistently meet specifications may limit opportunities for growth and expansion.
Investigating the Root Causes of Process Incentering
When Cpk is significantly lower than Cp, a thorough investigation into the root causes is essential. Possible causes include:
- Machine Miscalibration: Improper calibration of machines or equipment can lead to systematic biases, causing the process mean to drift from the target.
- Raw Material Variation: Inconsistent quality of raw materials can affect the final product, leading to process incentering.
- Operator Error: Human error during the production process can introduce variation and shift the process mean.
- Environmental Factors: Changes in temperature, humidity, or other environmental factors can also influence process performance.
- Process Design Flaws: Inadequate process design or lack of proper controls can contribute to incentering issues.
Corrective Actions for Process Incentering
Addressing process incentering requires a systematic approach involving various corrective actions, such as:
- Machine Recalibration: Regular calibration of machines and equipment ensures accuracy and minimizes systematic errors.
- Improved Raw Material Control: Implementing stricter quality control measures for raw materials can help to minimize variability.
- Operator Training: Providing adequate training to operators enhances their skills and minimizes human errors.
- Environmental Control: Maintaining a stable and controlled environment can help minimize environmental influences on the process.
- Process Optimization: Analyzing the process thoroughly to identify and address any design flaws or control deficiencies.
- Statistical Process Control (SPC): Implementing SPC techniques enables the continuous monitoring of process parameters and early detection of deviations from the target.
- Control Charts: Regularly reviewing control charts such as X-bar and R charts or X-bar and S charts allows for identification of shifts in the process mean and variances before they escalate into major problems.
The Importance of Continuous Improvement
Improving process capability is an ongoing process. Regular monitoring of Cp and Cpk values, coupled with investigation of any significant differences between them, is crucial for ensuring consistent product quality and continuous improvement. By proactively addressing process incentering issues, businesses can enhance efficiency, reduce costs, and improve customer satisfaction.
Examples and Case Studies
Consider a company manufacturing precision parts. Their Cp value is 1.4, indicating a relatively capable process with low variation. However, their Cpk is only 0.9, revealing that the process mean is shifted, resulting in a significant number of parts falling outside the specification limits. This indicates the need for immediate corrective actions, such as recalibration of the machines or adjustments to the process parameters to shift the mean towards the target.
Another scenario might involve a food processing plant. They might find that their Cp is consistently high, indicating low variability in their process. However, a low Cpk could be due to problems with ingredient consistency or slight variations in the machinery leading to a shifted mean. Addressing these issues might involve better supplier relationships, more regular maintenance checks, or adjustments to the process parameters.
These examples demonstrate that focusing only on Cp can be misleading. A low Cpk, even with a high Cp, suggests a problem with process centering that needs immediate attention.
Conclusion: Cp and Cpk: A Powerful Duo for Process Improvement
The difference between Cp and Cpk provides a powerful diagnostic tool for understanding and improving process capability. While Cp provides a measure of process variability, Cpk incorporates process centering, offering a more comprehensive assessment of process performance. A significant difference between these two indices strongly suggests process incentering issues that require immediate attention. By understanding the implications of this difference and implementing appropriate corrective actions, businesses can effectively improve process performance, reduce defects, enhance efficiency, and ultimately, increase customer satisfaction. Continuous monitoring and improvement remain crucial to maintaining a robust and capable production process.
Latest Posts
Latest Posts
-
Which Of The Following Is True About Protein
Mar 22, 2025
-
Mi Hermano Y Yo Llegamos A La Casa De Padres
Mar 22, 2025
-
An Example Of A Subjective Symptom Would Be
Mar 22, 2025
-
Fire Department Line Personnel Are Responsible For
Mar 22, 2025
-
Compare Group Selection To Single Tree Selection
Mar 22, 2025
Related Post
Thank you for visiting our website which covers about When Cpk Differs From Cp It Indicates The ________. . We hope the information provided has been useful to you. Feel free to contact us if you have any questions or need further assistance. See you next time and don't miss to bookmark.