When Is A Pneumatic Drill Commonly Used
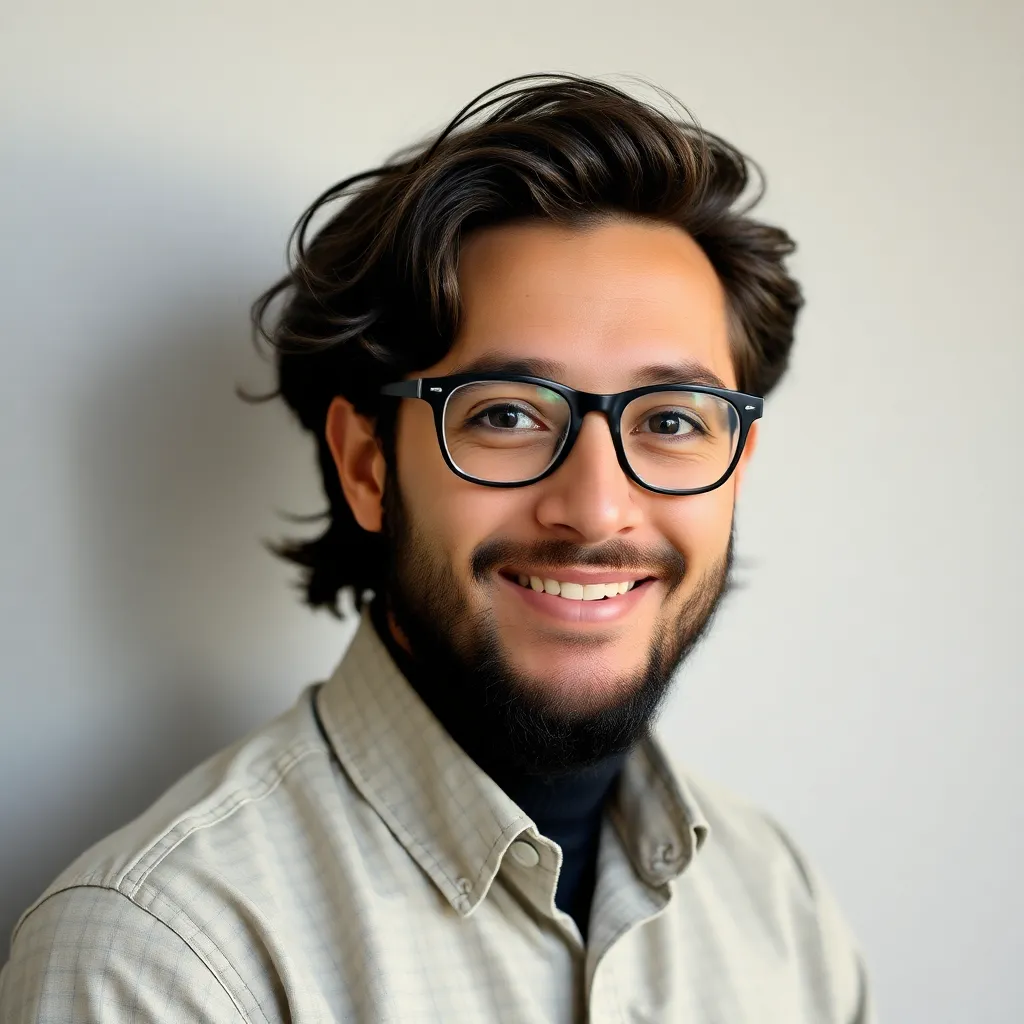
Breaking News Today
Apr 22, 2025 · 6 min read

Table of Contents
When is a Pneumatic Drill Commonly Used? A Comprehensive Guide
Pneumatic drills, also known as air drills, are powerful and versatile tools widely used across various industries. Their robust construction and ability to operate in demanding environments make them indispensable for numerous applications. But when exactly are these powerful tools most commonly employed? This comprehensive guide delves into the specific situations and industries where pneumatic drills shine, highlighting their advantages and why they remain a preferred choice over electric or cordless alternatives.
The Advantages of Pneumatic Drills: Why They Reign Supreme in Certain Applications
Before diving into specific applications, it's essential to understand why pneumatic drills are favored in certain scenarios. Their advantages often outweigh the limitations, making them the go-to choice for professionals in diverse fields.
Unmatched Power and Torque
High Power-to-Weight Ratio: Pneumatic drills boast an exceptional power-to-weight ratio. This means they deliver significant drilling power without being excessively bulky or heavy, making them easier to handle, especially during prolonged use in awkward positions or overhead work.
High Torque Output: The compressed air system provides exceptional torque, enabling them to effectively handle tough materials and challenging drilling tasks that would overwhelm electric or cordless drills. This is particularly crucial in applications requiring forceful penetration through dense materials like concrete, steel, or rock.
Durability and Reliability in Harsh Conditions
Robust Construction: Pneumatic drills are typically constructed with durable materials designed to withstand the rigors of heavy-duty use. They are less susceptible to damage from dust, debris, and moisture, which can severely impact the lifespan of electric drills.
Resistance to Extreme Temperatures: Unlike electric drills that can overheat during extended use or in hot environments, pneumatic drills maintain their operational efficiency even under extreme temperatures. This makes them suitable for outdoor projects in various climates.
Enhanced Safety Features
Reduced Risk of Electric Shock: The absence of electrical components significantly reduces the risk of electric shock, especially in damp or wet conditions. This is a critical safety advantage in environments where water or moisture is present.
Improved Control and Precision: The responsiveness of pneumatic drills often allows for more precise control and better feedback during operation. This precision is beneficial in intricate drilling tasks requiring accuracy.
Industries and Applications Where Pneumatic Drills Excel
Now, let's explore the diverse industries and specific applications where pneumatic drills prove their worth.
Construction and Demolition
This is arguably the most prominent application of pneumatic drills. Their immense power makes them essential for:
- Breaking Concrete: Demolition work frequently involves breaking through concrete structures. Pneumatic drills, equipped with appropriate bits, effectively handle this demanding task.
- Drilling Holes in Masonry: Whether it's for anchoring, installing fixtures, or creating conduits, pneumatic drills effortlessly penetrate brick, stone, and concrete blocks.
- Road Repair and Construction: Creating holes for road markings, utility installations, or anchoring structures on highways and roads often utilizes the power of pneumatic drills.
- Foundation Work: Drilling pilot holes for anchors and support structures during foundation construction benefits from the strength and speed of pneumatic drills.
Mining and Quarrying
The harsh and demanding environment of mining and quarrying necessitates robust equipment, making pneumatic drills an ideal choice for:
- Drilling Blast Holes: Creating precise holes for explosives during rock blasting requires the powerful torque and penetration capabilities of pneumatic drills.
- Extraction of Minerals: Drilling into rock formations to extract valuable minerals often relies on the dependable performance of pneumatic drills.
- Tunnel Boring: In tunnel construction, pneumatic drills contribute to breaking through rock and soil, facilitating the advancement of the tunnel.
Automotive and Manufacturing
While not as prevalent as in construction, pneumatic drills find specific applications in automotive and manufacturing industries:
- Drilling Metal: In metal fabrication, pneumatic drills efficiently create holes in various metal sheets and components.
- Assembly Line Work: Some assembly line processes benefit from the speed and power of pneumatic drills for fastening and drilling tasks.
- Automotive Repair: Certain automotive repair tasks involving drilling and removal of components can be facilitated by pneumatic drills.
Shipbuilding and Repair
The scale and demanding nature of shipbuilding necessitate reliable power tools. Pneumatic drills contribute significantly to:
- Drilling Steel Plates: The robust construction of pneumatic drills makes them suitable for piercing through thick steel plates during shipbuilding.
- Repair and Maintenance: Maintaining and repairing large vessels often involves drilling through metal and other materials; pneumatic drills are often the most efficient option.
Other Applications
Besides these major industries, pneumatic drills find applications in various other fields:
- Plumbing: Drilling holes in pipes and walls for installing fixtures.
- HVAC: Creating holes for ductwork and other components.
- Aerospace: Certain aerospace applications require the precision and power of pneumatic drills.
- Woodworking (Specialized Applications): Although less common than electric or cordless drills, specialized pneumatic drills exist for specific heavy-duty woodworking tasks.
Selecting the Right Pneumatic Drill: Key Considerations
Choosing the appropriate pneumatic drill depends on the specific application and the materials being worked with. Key factors to consider include:
- Chuck Size: This determines the size of drill bits that can be used.
- Speed and Torque: Higher speed is suitable for lighter materials, while higher torque is needed for denser materials.
- Air Pressure Requirements: The operating air pressure affects the drill's power and performance.
- Weight and Ergonomics: A lighter weight drill is easier to handle for prolonged use.
- Durability and Build Quality: Investing in a robust drill ensures longevity.
Pneumatic Drills vs. Electric and Cordless Drills: A Comparison
While electric and cordless drills have their own advantages, pneumatic drills offer unique benefits in certain scenarios:
Feature | Pneumatic Drill | Electric Drill | Cordless Drill |
---|---|---|---|
Power | Very High | High | Moderate to High |
Torque | Very High | High | Moderate to High |
Weight | Moderate | Moderate to High | Moderate to Light |
Durability | Very High | Moderate to High | Moderate |
Maintenance | Moderate | Low | Low |
Cost | Moderate to High | Low to Moderate | Moderate to High |
Cord/Hose | Requires Air Hose | Requires Power Cord | Cordless |
Suitable for | Heavy-Duty tasks, harsh environments | General use, indoor projects | General use, light-duty projects |
Conclusion: The Enduring Power of Pneumatic Drills
Pneumatic drills remain indispensable tools in numerous industries due to their unmatched power, durability, and suitability for demanding environments. While electric and cordless drills have their place, pneumatic drills excel in applications requiring high torque, robust construction, and resistance to harsh conditions. Understanding the specific advantages and applications of pneumatic drills allows professionals to choose the right tool for the job, ensuring efficiency, safety, and successful project completion. By considering the factors highlighted in this guide, you can confidently select and utilize a pneumatic drill for your specific needs.
Latest Posts
Latest Posts
-
Did You Get It Practica De Gramatica
Apr 22, 2025
-
Is Expert Knowledge About The Practical Aspects Of Life
Apr 22, 2025
-
The Third Step Of Mbo Reminds Us That
Apr 22, 2025
-
The Smell Of A Cockroach Infestation Is Often Described As
Apr 22, 2025
-
The Open Web Design Of Truss Joints
Apr 22, 2025
Related Post
Thank you for visiting our website which covers about When Is A Pneumatic Drill Commonly Used . We hope the information provided has been useful to you. Feel free to contact us if you have any questions or need further assistance. See you next time and don't miss to bookmark.