When Surface Preservation Of The Ship Is Required
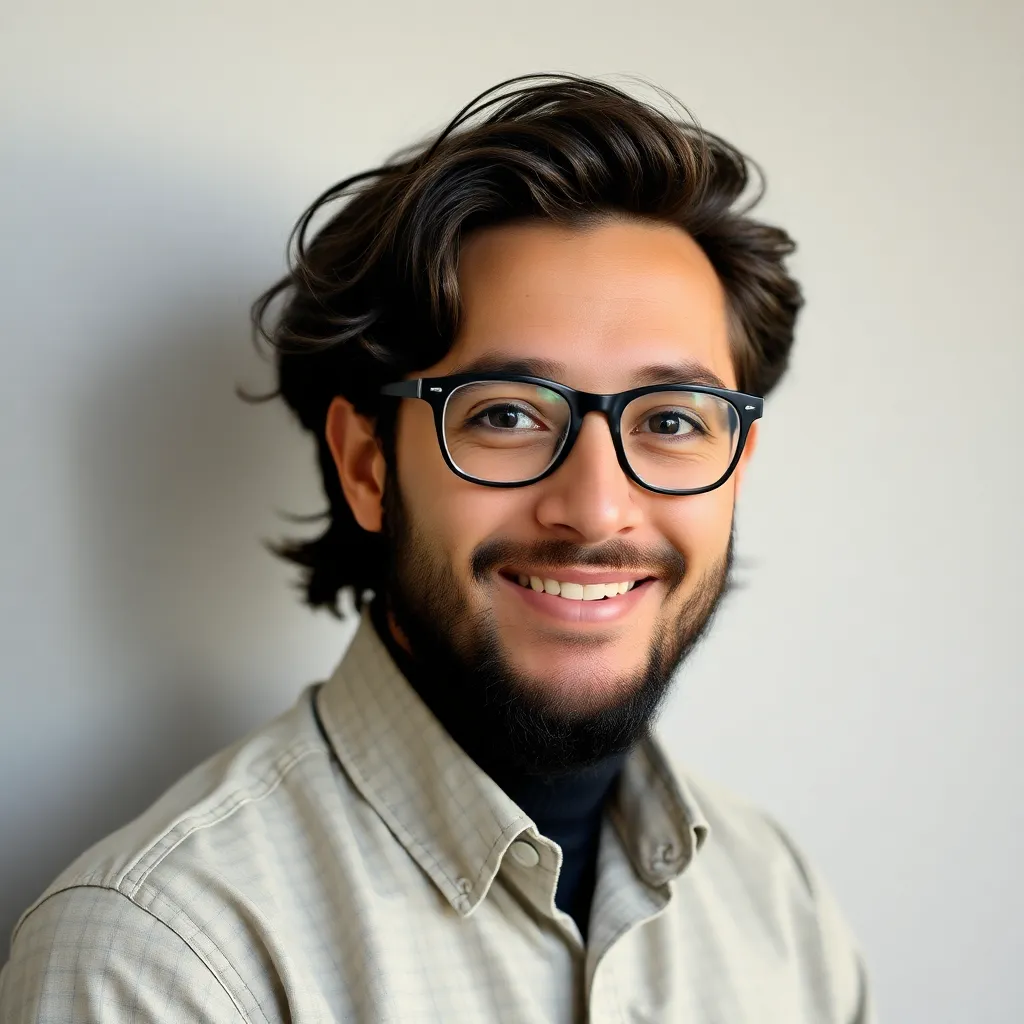
Breaking News Today
Apr 09, 2025 · 5 min read

Table of Contents
When Surface Preservation of a Ship is Required: A Comprehensive Guide
Maintaining a ship's hull and superstructure is crucial for its operational efficiency, longevity, and safety. Surface preservation, encompassing a range of protective measures, isn't just about aesthetics; it's a fundamental aspect of ship maintenance that directly impacts performance and cost-effectiveness. This comprehensive guide delves into the crucial instances where surface preservation becomes absolutely necessary, exploring the underlying reasons and the varied techniques employed.
Understanding the Importance of Ship Surface Preservation
Before diving into specific scenarios, it's essential to grasp the broader significance of ship surface preservation. The harsh marine environment relentlessly attacks a vessel's surfaces. Factors like:
- Corrosion: Saltwater, humidity, and oxygen create an ideal breeding ground for corrosion, particularly affecting steel hulls and metallic components. Corrosion weakens structural integrity, leading to potential failures and safety hazards.
- Biofouling: Marine organisms like barnacles, algae, and mussels readily attach to underwater surfaces, increasing drag, reducing speed, and impacting fuel efficiency. This biofouling also creates ideal habitats for corrosion.
- UV Degradation: Prolonged exposure to sunlight's ultraviolet (UV) rays degrades paint and other surface coatings, leading to fading, cracking, and ultimately, loss of protective properties.
- Abrasion: Contact with docks, other vessels, or debris can cause physical damage to the ship's surfaces, exposing underlying metal to the elements.
These factors contribute to significant operational and financial costs. Neglecting surface preservation translates to:
- Increased Fuel Consumption: Biofouling significantly increases drag, necessitating more fuel to maintain speed.
- Reduced Operational Efficiency: Corrosion and damage can lead to malfunctions in various systems and require costly repairs.
- Higher Maintenance Costs: Addressing extensive damage is considerably more expensive than implementing preventative measures.
- Safety Hazards: Structural weakening due to corrosion poses serious safety risks to the crew and the vessel itself.
- Environmental Concerns: Loss of paint and coatings can pollute the marine environment.
Specific Scenarios Demanding Surface Preservation
Now, let's explore specific situations where surface preservation becomes not just advisable, but critically necessary:
1. Before Launching a New Vessel
Before a newly constructed vessel is launched, meticulous surface preservation is paramount. This involves:
- Primer Application: Applying a high-quality primer creates an effective barrier against corrosion and improves the adhesion of subsequent coatings.
- Anti-Fouling Paint: A specialized anti-fouling paint is applied to the underwater hull to prevent biofouling. The choice of paint depends on factors like the vessel's type, operational area, and environmental regulations.
- Topcoat Application: Topcoats provide further protection against UV degradation, abrasion, and weathering. The selection of topcoat depends on aesthetic requirements and desired properties.
Proper surface preservation at this stage sets the foundation for the vessel's long-term protection.
2. During Dry-Docking and Hull Cleaning
Dry-docking provides the ideal opportunity for thorough hull inspection and surface preservation. During this period:
- Hull Cleaning: All marine growth and loose paint are removed to expose the bare metal. This allows for a proper assessment of any corrosion or damage.
- Repairing Damage: Any identified corrosion or damage is repaired, ensuring structural integrity. This may involve welding, grinding, or other repair techniques.
- Re-coating: Once repairs are complete, the hull is primed and recoated with anti-fouling and topcoat paints.
3. After Damage or Collision
Any accident resulting in damage to the vessel's surface necessitates immediate surface preservation. This includes:
- Emergency Repairs: Temporary repairs are conducted to prevent further damage and water ingress.
- Thorough Inspection: A detailed inspection assesses the extent of damage, identifying areas requiring repair and recoating.
- Permanent Repairs and Recoating: Permanent repairs are carried out, followed by application of appropriate primers and coatings to restore the protective barrier.
4. Regular Scheduled Maintenance
Routine maintenance, based on the vessel's operational profile and environmental conditions, is crucial for preventing deterioration. This includes:
- Regular Inspections: Visual inspections and non-destructive testing (NDT) techniques identify potential issues early on.
- Touch-ups and Minor Repairs: Addressing small areas of damage or deterioration before they become larger problems.
- Re-coating Cycles: Depending on the type of coating and the vessel's operational profile, recoating might be necessary every few years.
5. Changes in Operational Area
If a vessel operates in a significantly different environment (e.g., moving from temperate waters to tropical waters), its surface preservation needs may change. This might require:
- Different Anti-Fouling Paints: Tropical waters often necessitate more aggressive anti-fouling paints to combat rapid biofouling.
- Additional Protective Coatings: Exposure to harsher UV radiation or increased salinity could necessitate additional layers of protection.
6. Regulatory Compliance
Various international and national maritime regulations dictate minimum standards for ship surface preservation. Compliance is crucial to avoid penalties and ensure operational legality. These regulations often address:
- Anti-fouling Paint Regulations: Regulations restrict the use of certain biocides in anti-fouling paints to minimize environmental impact.
- Hull Condition Standards: Regular inspections and maintenance are mandated to ensure the structural integrity and safety of the vessel.
Different Types of Surface Preservation Techniques
The specific techniques employed for surface preservation vary depending on the material, the extent of damage, and environmental factors. Some common techniques include:
- Protective Coatings: Paints, varnishes, and specialized coatings form a barrier against corrosion, biofouling, and UV degradation. Choosing the right coating system is crucial for optimal performance.
- Corrosion Inhibitors: These chemicals are incorporated into coatings or applied directly to metallic surfaces to slow down or prevent corrosion.
- Zinc-Based Coatings: Zinc-rich primers provide cathodic protection, sacrificing themselves to prevent corrosion of the underlying steel.
- Protective Wraps: For sensitive areas or during temporary storage, protective wraps provide an additional layer of protection.
- Specialized Coatings: Specialized coatings, such as polyurethane or epoxy coatings, offer enhanced durability and resistance to specific environmental conditions.
- Non-Destructive Testing (NDT): Techniques like ultrasonic testing, magnetic particle inspection, and radiographic testing assess the condition of the ship's structure without causing damage.
Conclusion
Surface preservation of a ship is an ongoing process that's vital for its operational life, safety, and economic viability. Ignoring the need for appropriate maintenance leads to significant costs, safety risks, and environmental concerns. The specific scenarios highlighted in this article underscore the critical moments when surface preservation becomes non-negotiable. Understanding these instances and employing the appropriate techniques is essential for maintaining a vessel's integrity and ensuring its long-term operational success. Regular inspection, proactive maintenance, and adherence to regulatory standards form the cornerstone of effective ship surface preservation strategies.
Latest Posts
Latest Posts
-
Three Components Of The Highway Transportation System
Apr 17, 2025
-
What Is A Major Tourist Attraction In Nicaragua
Apr 17, 2025
-
Match The Type Of Fault With Its Description
Apr 17, 2025
-
Its Contagious And Represents The Greatest Risk For Occupational Exposure
Apr 17, 2025
-
Rn Critical Alterations In Gas Exchange Assessment
Apr 17, 2025
Related Post
Thank you for visiting our website which covers about When Surface Preservation Of The Ship Is Required . We hope the information provided has been useful to you. Feel free to contact us if you have any questions or need further assistance. See you next time and don't miss to bookmark.