Which Concrete Building Type Of Construction May Be Cast Larger
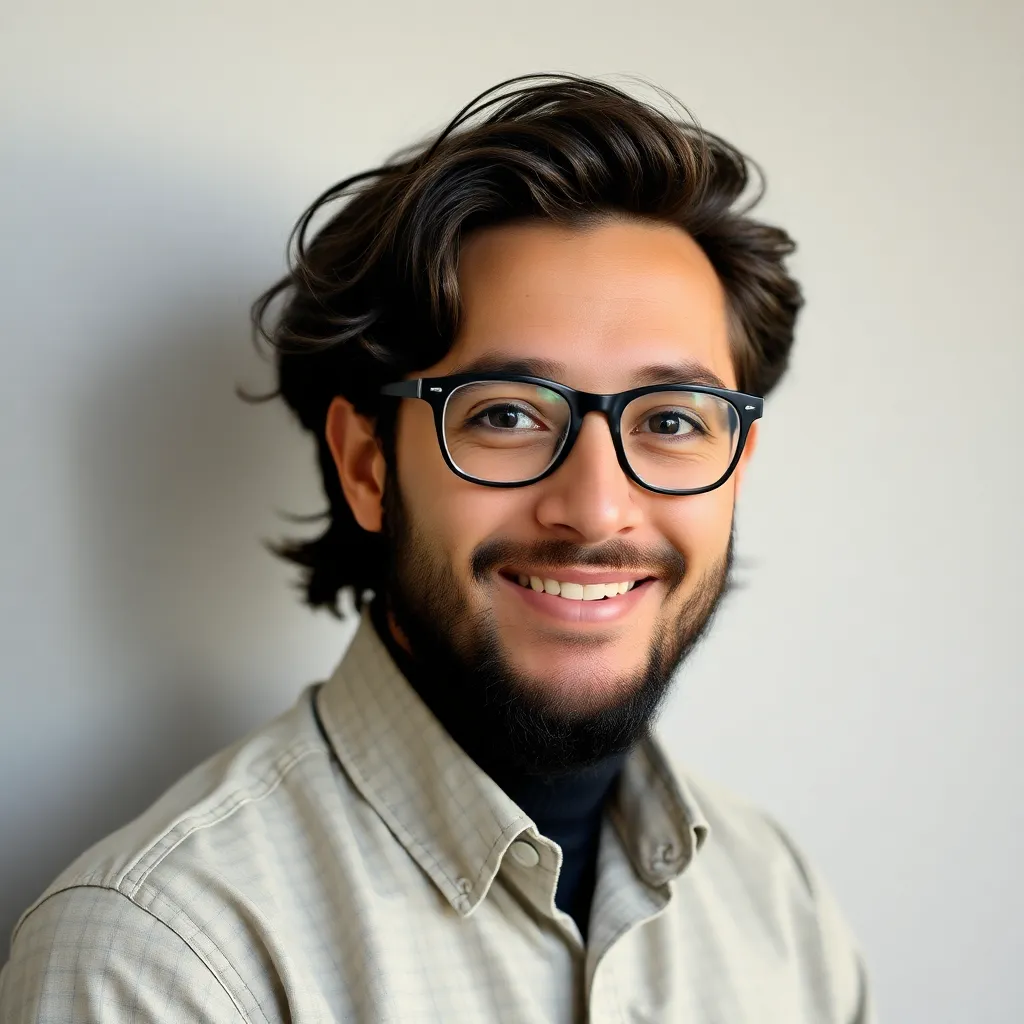
Breaking News Today
Apr 05, 2025 · 6 min read
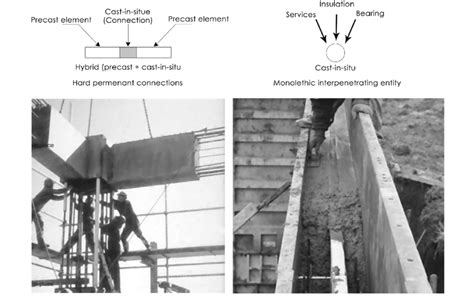
Table of Contents
Which Concrete Building Construction Type May Be Cast Larger?
Concrete, a versatile and robust material, allows for the construction of buildings of varying sizes and complexities. However, the size of a concrete structure that can be cast in a single pour, or in a series of carefully coordinated pours, depends significantly on several factors related to the chosen construction type. This article delves into the various concrete building construction types, analyzing their capabilities and limitations concerning the size of structures they can create. We'll explore the influencing factors, from material properties and formwork design to environmental considerations and the expertise of the construction team.
Understanding Concrete Construction Types
Several concrete construction types exist, each with its own advantages and disadvantages regarding scalability. The major types are:
1. Cast-in-Place Concrete (CIP)
CIP is the most common method, involving pouring and setting concrete directly on-site within a formwork system. This method offers significant design flexibility, allowing for intricate shapes and complex structures. However, it's significantly impacted by size limitations.
Factors Limiting CIP Cast Size:
- Formwork Complexity and Cost: Larger structures demand more extensive and complex formwork, leading to increased costs and logistical challenges. The formwork must be robust enough to withstand the immense pressure of the wet concrete and precise enough to maintain the structural integrity and desired aesthetic finish of the final structure.
- Concrete Placement and Consolidation: Placing and consolidating a large volume of concrete efficiently and effectively without void formation or segregation is crucial. Improper consolidation can lead to weakened sections and structural failure. This often necessitates specialized equipment and highly skilled labor, increasing costs and timelines.
- Heat of Hydration: The chemical reaction during concrete setting releases heat. In massive concrete pours, this heat can build up, causing excessive thermal stresses and potentially leading to cracking and weakening. This necessitates careful consideration of concrete mix design, cooling techniques, and controlled pouring procedures.
- Settlement and Shrinkage: As the concrete cures and dries, it undergoes shrinkage, potentially leading to cracking in large structures. Controlling this shrinkage requires careful mix design, proper curing techniques, and controlled construction sequencing.
- Construction Time and Logistics: The time required to construct and strip the formwork for large CIP structures is significantly longer. This needs meticulous planning and coordination, including efficient material delivery, labor management, and site logistics.
2. Precast Concrete
Precast concrete involves manufacturing concrete elements off-site in a controlled environment, then transporting and assembling them on-site. This method allows for larger elements to be produced, as the limitations of on-site pouring are reduced.
Advantages in Larger Structures:
- Controlled Environment: Production in a factory setting offers precise control over concrete mix design, curing processes, and quality assurance. This minimizes the risk of defects and ensures consistent quality.
- Faster Construction Time: Precast elements can be assembled much faster than equivalent CIP structures, speeding up overall construction.
- Larger Element Sizes: Precast elements can be significantly larger than those typically achievable with CIP, enabling the construction of larger structures with fewer individual components.
- Improved Quality Control: Factory production allows for better quality control and reduces the potential for on-site errors.
Limitations:
- Transportation and Handling: Transporting large precast elements can be complex and costly, requiring specialized equipment and careful planning.
- On-site Assembly: Precision is essential during on-site assembly to ensure proper alignment and structural integrity. Any inaccuracies can compromise the structural performance of the finished building.
- Design Limitations: While precast offers flexibility, it might not be suitable for every design. Intricate shapes and complex configurations might be more challenging to achieve with precast than with CIP.
3. Tilt-Up Concrete
Tilt-up construction involves casting concrete panels directly on-site, then tilting them into their final upright position. This method is cost-effective for certain building types, but it's inherently limited in the size of panels it can handle safely.
Size Limitations:
- Panel Weight and Handling: The weight of the panels increases exponentially with size, making transport and tilting increasingly difficult and requiring specialized equipment.
- Strength of the Panel: The larger the panel, the greater the potential for cracking or structural failure during handling and tilting. Reinforcement design is critical.
- Crane Capacity: The crane used must have sufficient capacity to lift and maneuver these panels, placing limits on feasible panel size.
Factors Influencing Cast Size Regardless of Construction Type
Several factors influence the maximum cast size, irrespective of the chosen concrete construction type:
- Concrete Mix Design: The properties of the concrete mix, including strength, workability, and slump, directly affect the maximum cast size. Higher-strength concrete is generally preferred for larger pours, but its workability might be reduced, requiring specialized techniques.
- Reinforcement Design: Appropriate reinforcement is essential to manage stresses and prevent cracking in large concrete structures. This involves detailed analysis and careful planning.
- Formwork Design and Material: The formwork must be strong and rigid enough to withstand the pressure of the wet concrete, and the materials used must be suitable for the specific job. Larger pours require more robust formwork, adding to costs.
- Environmental Conditions: Temperature, humidity, and wind can all influence the curing process and the strength development of concrete. Extreme temperatures can cause rapid drying and cracking, requiring careful control of environmental factors.
- Curing Methods: Adequate curing is critical for the strength and durability of concrete. Large pours often need specialized curing techniques like insulation and moisture retention to maintain optimal conditions.
- Construction Expertise and Planning: Successful large concrete pours require experienced professionals with detailed plans, meticulous coordination, and effective communication.
Which Construction Type Can Cast Larger?
While both CIP and precast offer possibilities for large-scale concrete construction, precast generally allows for casting larger individual elements than CIP. The controlled environment and ability to manufacture large sections off-site significantly reduce many of the constraints associated with on-site pouring. However, the overall size of the finished structure depends on the ability to assemble these precast elements efficiently and safely. Highly skilled teams and specialized lifting equipment become critical for larger projects.
Furthermore, while tilt-up is a suitable and economical method for some buildings, it’s inherently limited by panel size. The maximum panel size will be significantly smaller than that achievable using precast techniques.
Conclusion
The maximum cast size for concrete structures depends on a complex interplay of factors, including the chosen construction method, concrete mix design, formwork, reinforcement, environmental conditions, and construction expertise. While precast concrete generally offers the potential for larger individual elements, the overall project size also depends on the practicalities of transportation, assembly, and other on-site logistical considerations. Thorough planning, expert execution, and careful attention to detail are essential for successfully constructing any large-scale concrete structure, regardless of the chosen methodology. Understanding these factors allows for informed decision-making and contributes to the safe and efficient construction of robust and durable concrete buildings.
Latest Posts
Latest Posts
-
Which Of The Following Improves Overall Network Performance
Apr 06, 2025
-
What Is The First Guideline For Doing Research With People
Apr 06, 2025
-
An Arbitrator Is Different Than A Mediator Because An Arbitrator
Apr 06, 2025
-
Why Were Northerners Upset About The Dred Scott Decision
Apr 06, 2025
-
Relational Issues Are Inextricably Bound To Content Issues
Apr 06, 2025
Related Post
Thank you for visiting our website which covers about Which Concrete Building Type Of Construction May Be Cast Larger . We hope the information provided has been useful to you. Feel free to contact us if you have any questions or need further assistance. See you next time and don't miss to bookmark.