Which Is The Best Definition Of Quality Circles
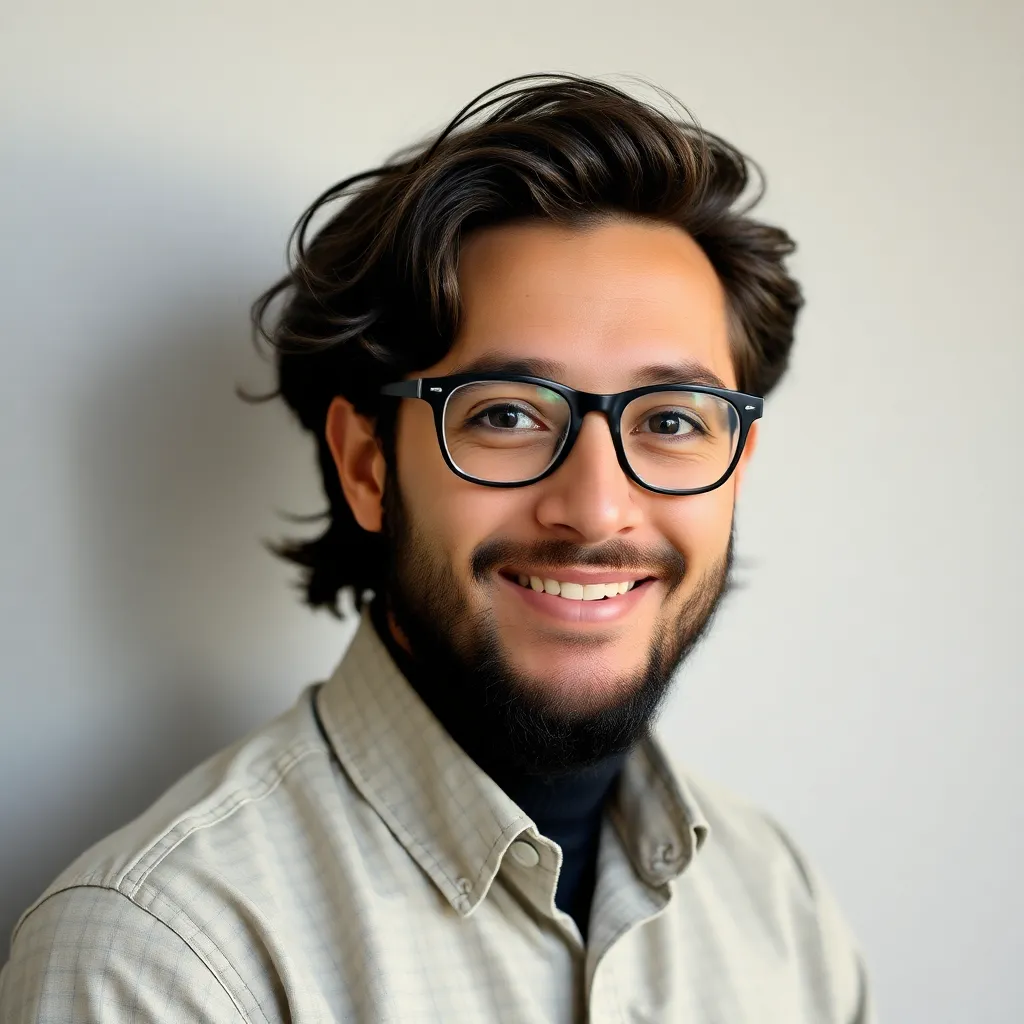
Breaking News Today
May 09, 2025 · 6 min read
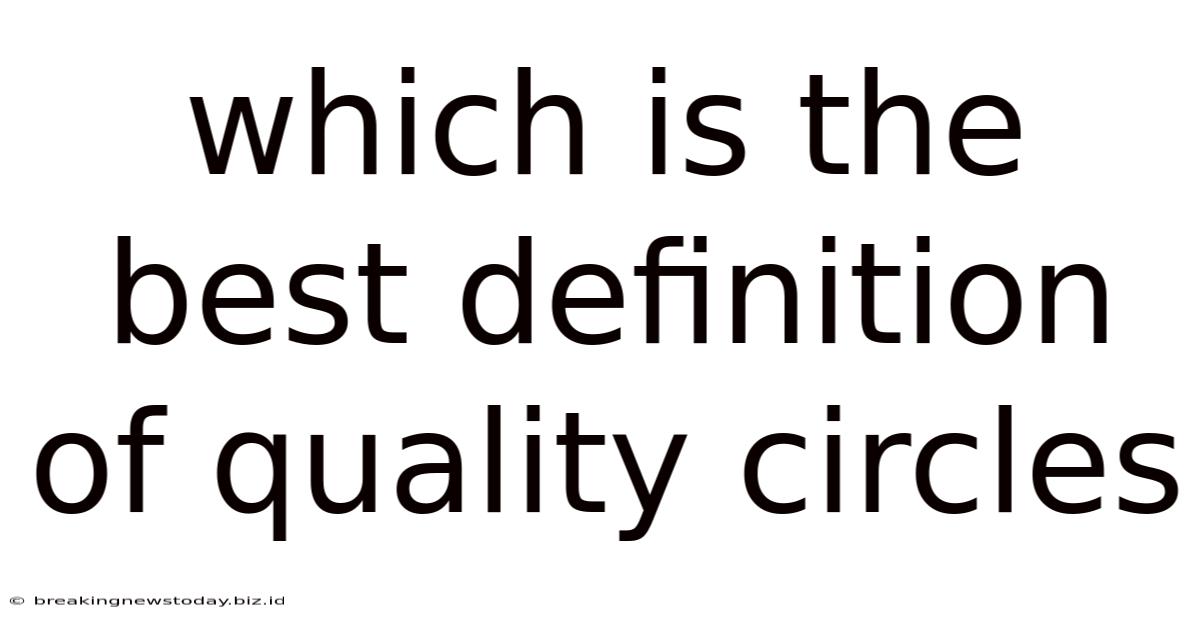
Table of Contents
Which is the Best Definition of Quality Circles? Unpacking the Concept and its Modern Applications
The term "quality circle" (QC) has been around for decades, yet its precise definition remains surprisingly fluid. While the core concept revolves around employee participation in improving workplace quality, the nuances of implementation, scope, and impact vary considerably across organizations and industries. This article delves deep into understanding quality circles, examining various definitions, exploring their evolution, and highlighting their continued relevance in today's dynamic business landscape. We’ll unpack the best definition, considering factors like employee empowerment, problem-solving techniques, and measurable results.
What are Quality Circles? A Multifaceted Definition
A simple definition of a quality circle might be: a small group of employees who voluntarily meet regularly to identify, analyze, and solve work-related problems. However, this succinct explanation lacks the richness and depth necessary to fully grasp the concept. A more comprehensive definition needs to encompass several key elements:
-
Voluntary Participation: Membership is not mandatory; employees choose to participate based on their interest and commitment to improvement. This voluntary nature fosters a sense of ownership and dedication.
-
Small Group Dynamics: The optimal size generally ranges from 5 to 12 members, allowing for effective communication and collaboration. Larger groups can become unwieldy and less productive.
-
Structured Problem-Solving: QCs utilize structured problem-solving methodologies, such as the Plan-Do-Check-Act (PDCA) cycle, to systematically address workplace issues.
-
Focus on Quality Improvement: The primary goal is to enhance the quality of products, services, or processes. This can encompass efficiency, cost reduction, safety improvements, and customer satisfaction.
-
Employee Empowerment: QCs empower employees by giving them a voice in improving their work environment. This participation enhances morale, job satisfaction, and a sense of belonging.
-
Management Support: Successful QCs require strong management support, providing resources, training, and recognition for the group's achievements. Without this backing, QCs are unlikely to thrive.
Considering these elements, a more robust definition emerges: Quality circles are small, voluntary groups of employees who meet regularly to identify, analyze, and solve work-related problems using structured problem-solving methodologies, with the goal of improving the quality of products, services, processes, and the overall work environment, supported by management.
The Evolution of Quality Circles: From Japan to Global Adoption
The origins of quality circles can be traced back to post-World War II Japan, where companies like Toyota sought ways to enhance productivity and quality in the face of fierce global competition. The Japanese approach, often referred to as jishu kanri (self-control), emphasized employee involvement and continuous improvement. This philosophy provided the foundation for the widespread adoption of quality circles.
While the initial implementation focused primarily on manufacturing, quality circles rapidly expanded into diverse sectors, including service industries, healthcare, and education. The success stories from early adopters fueled global interest, leading to its widespread adoption throughout the 1970s and 1980s.
However, the enthusiasm wasn't always sustained. Many early QC implementations failed due to insufficient management support, lack of proper training, and a resistance to change within the organizational culture. This led to a period of reevaluation and adaptation, resulting in more refined approaches and a greater emphasis on integration with existing quality management systems.
Key Differences and Variations in QC Approaches
While the core principles remain consistent, various approaches and interpretations of quality circles exist. Some key differences include:
-
Focus and Scope: Some QCs focus narrowly on specific departmental problems, while others adopt a broader, organization-wide perspective.
-
Methodology: While the PDCA cycle is common, other problem-solving techniques, such as brainstorming, root cause analysis, and statistical process control, may be integrated.
-
Level of Management Involvement: The degree of management involvement varies; some organizations favor a highly participatory approach, while others prefer a more supervisory role.
-
Formalization and Structure: The level of formality and structure also differs. Some organizations establish formal QC programs with clear guidelines and procedures, while others adopt a more informal, flexible approach.
Best Practices for Successful Quality Circles
The success of a quality circle hinges on several crucial factors:
-
Strong Management Commitment: Management must actively support QCs by providing resources, training, and recognition. This includes allocating time for meetings, providing necessary tools and data, and celebrating successes.
-
Employee Training: Members need training in problem-solving techniques, data analysis, and effective communication. This ensures they have the skills and knowledge to effectively contribute to the group's work.
-
Clear Objectives and Goals: The QC should define clear, measurable, achievable, relevant, and time-bound (SMART) goals. This provides direction and helps track progress.
-
Effective Facilitation: A skilled facilitator guides the group's discussions, ensuring that meetings remain focused and productive. They help manage conflicts, encourage participation, and keep the group on track.
-
Regular Communication and Feedback: Regular communication is vital to keep management informed of progress, challenges, and successes. Feedback from management and other stakeholders helps refine the QC's approach.
-
Recognition and Rewards: Recognizing and rewarding the group's achievements boosts morale and motivates continued participation. This can take various forms, from simple acknowledgement to more substantial incentives.
Quality Circles in the Modern Workplace: Adapting to Change
While the fundamental principles of quality circles remain relevant, their application needs to adapt to the evolving demands of the modern workplace. This includes:
-
Integration with Technology: Utilizing technology for data analysis, communication, and collaboration can significantly enhance the effectiveness of QCs. Tools like project management software and online communication platforms can streamline processes and improve efficiency.
-
Focus on Innovation: In addition to problem-solving, QCs can play a vital role in driving innovation by fostering a culture of creativity and continuous improvement. This involves encouraging members to explore new ideas and propose innovative solutions.
-
Emphasis on Customer Focus: Modern QCs should prioritize customer feedback and strive to improve products and services that directly impact customer satisfaction. Gathering customer insights and incorporating them into the problem-solving process is crucial.
-
Cross-functional Collaboration: QCs can benefit from involving members from different departments and functions. This fosters a broader perspective and facilitates the implementation of cross-departmental solutions.
-
Continuous Learning and Development: Promoting a culture of continuous learning and development within the QC ensures that members remain updated with the latest best practices and techniques. This may involve regular training sessions, workshops, or participation in professional development programs.
Conclusion: Redefining Quality Circles for the 21st Century
The best definition of quality circles is not static; it evolves with the changing landscape of the workplace. While the core principles of voluntary participation, structured problem-solving, and management support remain essential, modern QCs need to embrace technology, innovation, and customer focus. By adapting to these changes, quality circles can continue to play a vital role in improving workplace quality, driving organizational excellence, and fostering a culture of employee empowerment and continuous improvement. The key to success lies in a commitment to best practices, ongoing adaptation, and a genuine desire to leverage the collective intelligence and expertise of the workforce. In essence, the “best” definition is the one that most effectively empowers employees to contribute meaningfully to their organization's success.
Latest Posts
Latest Posts
-
Setting Up An Effective Nonroutine Meeting Begins With
May 09, 2025
-
Mobile Device Management Should Be Able To
May 09, 2025
-
Match The Type Of Stressor With Its Description
May 09, 2025
-
There Can Be No Bacterial Infection Without The Presence Of
May 09, 2025
-
Which Of These Is Not A Fossil Fuel
May 09, 2025
Related Post
Thank you for visiting our website which covers about Which Is The Best Definition Of Quality Circles . We hope the information provided has been useful to you. Feel free to contact us if you have any questions or need further assistance. See you next time and don't miss to bookmark.